With the sides bent I used titebond to glue on the tail and neck block. The tail block is straight forward with the sides trimmed to size on the bandsaw and the belt sander.
I have always struggled clamping clamping the heel block to the cutaway sides. This time it finally hit me that there is no need to glue both sides on at once.
So I first glued the cutaway aligned and glued on the cutaway side.
After a couple of hours I glued on the non cutaway side.
Before profiling the sides I used the square top side to evenly place the sides in the molds and then marking a couple of lines to help me realign the sides in the mold after the top and bottom are profiled.
Starting on the back sides I used a plane to remove most of the excess. The sides were profiled but tall. I marked the sides down a few millimeters and used a plane to take them down to the lines.
Then I used a 10' radius board to clean up the sides to the 10' profiles.
Leaving the rims on the 10' radius board I used a 32' radius board for the top profile.
In the picture above notice that I do most of the sanding on the lower bout. I lower the lower bout to create the correct angle for the neck angle. Most builders profiled the entire top and work on the upper bout to create the correct angle. I instead get most of the angle by dropping the lower bout.
I any case I profile the rims until an unbrace top held on the rims show that I have the right angle.
First is too low needs more work
After a bit more work the 3 mm bit shows me I am close.
Once the top is braced I play with the profile more to make the fit perfect.
On the CAD front I figured out how to profile the wings with the trapezoid block shape.
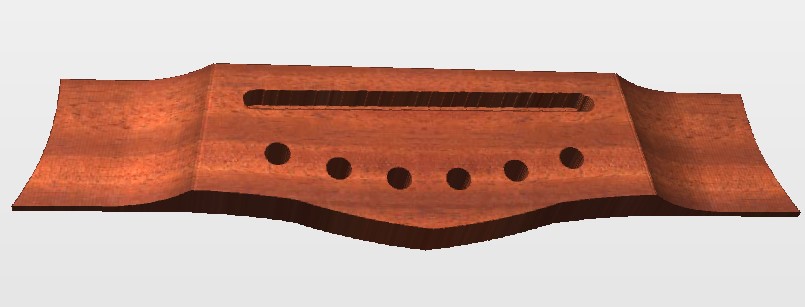