So for the first time to do this, I made an experimental guitar, not for a customer. But it turns out quite nice.
Spruce/Sapele/Maple/Mahogany and Ebony. Home made Full-Round Rosette/Armbevel/Soundports and a Florentine cutaway.
For more details, specs and pictures look Here
Finally I recorded some Sounds
But the Armbevel is something you might like to see here, so:
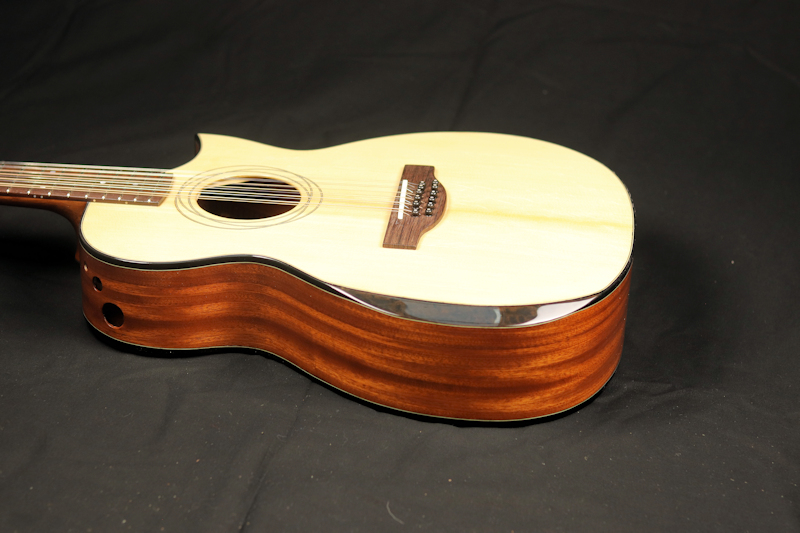

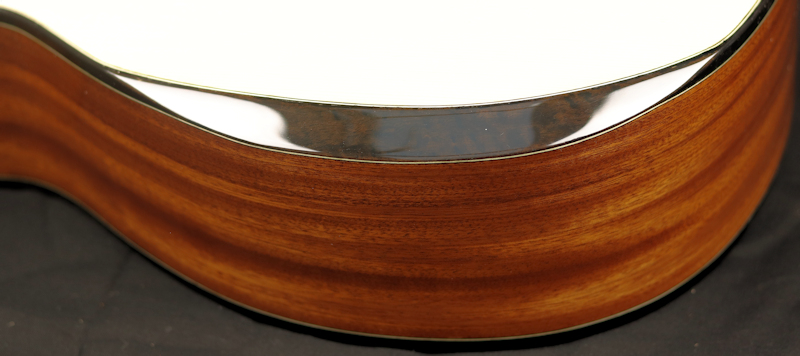