First Concert Ukulele
Posted: Tue Oct 19, 2021 12:49 am
I am starting a spruce and tulipwood concert ukulele for a friend. It may be a little bit fancy for me as she is really in to having a shell rosette and purflings. I always thought tulipwood was poplar and rather plain. This wood is figured with good tonal properties. After helping someone on line with some plans, I was sent the set. Maybe some one recognizes this wood. (I have since learned that this is, DALBERGIA DECIPULARIS ORIGIN: SOUTH AMERICA. A true rosewood.
Tulipwood is an exotic wood native to the tropical region of South America, mainly Brazil. It is a hard and heavy wood, with a rather fine texture. The sapwood is a solid yellow color, while the heartwood color ranges from a pink to a darker red, with a straw colored background. Tulipwood is excellent for wood turning, as well as knife handles, furniture, and cabinets. It is a lustrous wood, has excellent polishing qualities, and glues well.
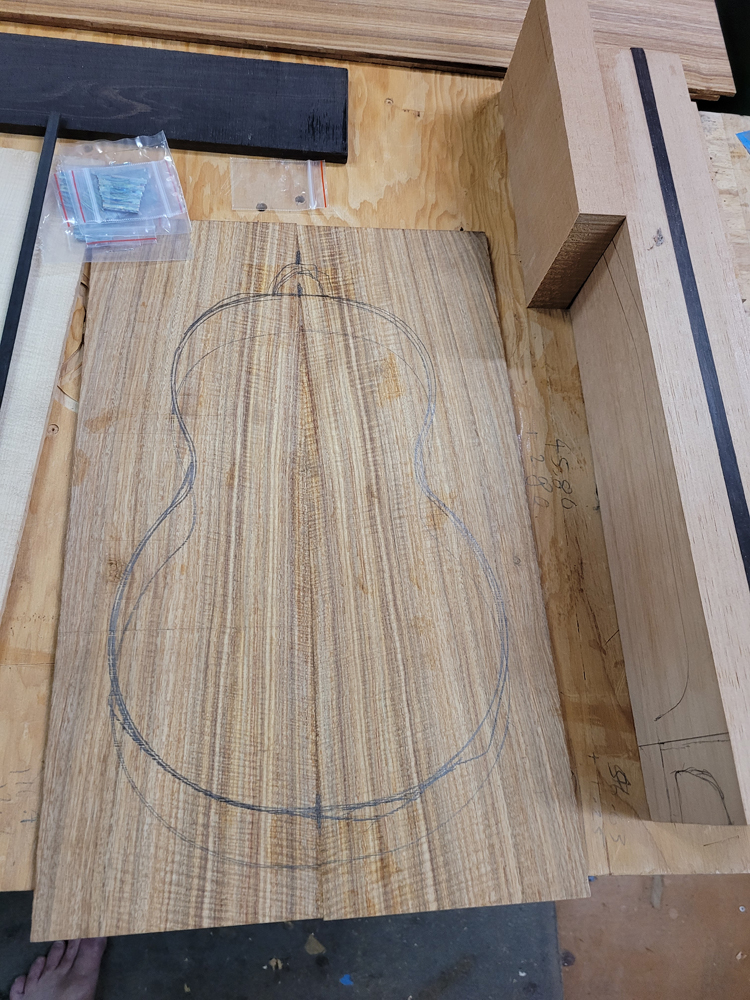
I have never made a concert before, I once bought a complete set of Martin Ukulele forms at an auction so I was some what ready. I got a mold from John Hall modified it and combined it with a work board for a Spanish neck joint. In the background you will see I have a second mold that I will use if I ever do a bolt on.
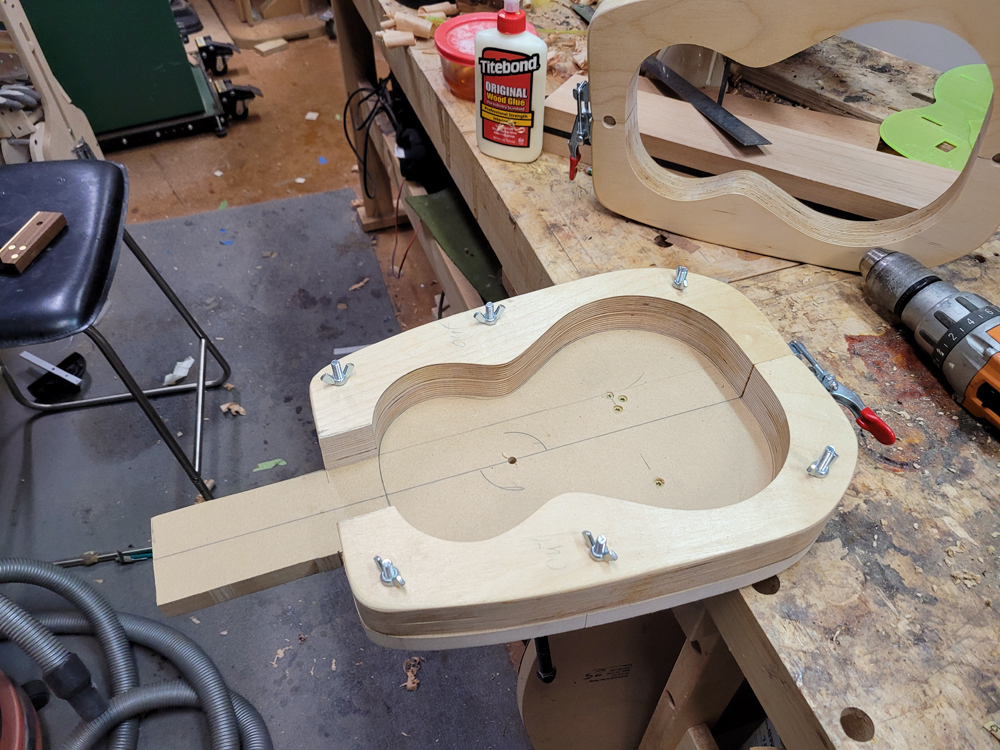
I used an old record plane to joint the plates. I used my guitar plate jointing jig to clamp the plates together but it really was too big.
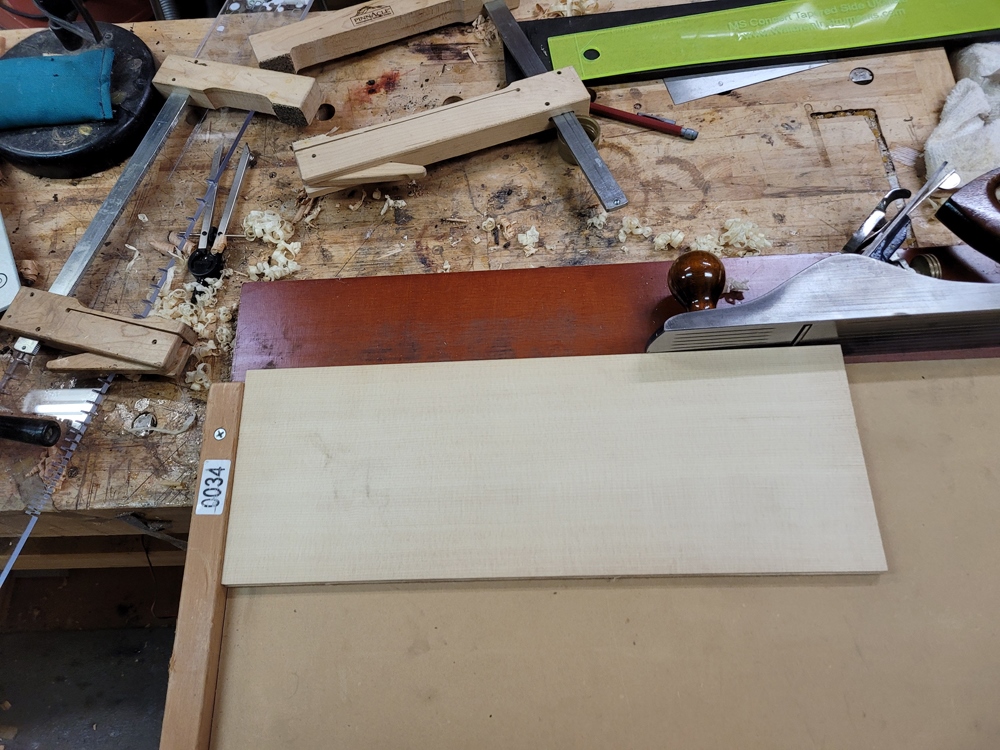
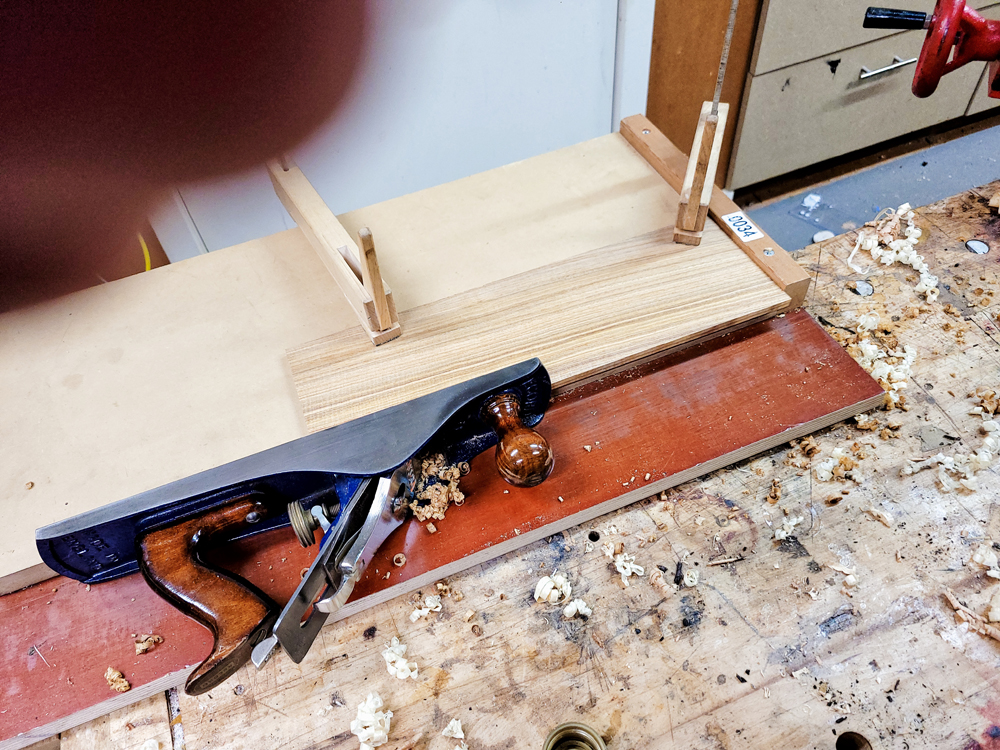
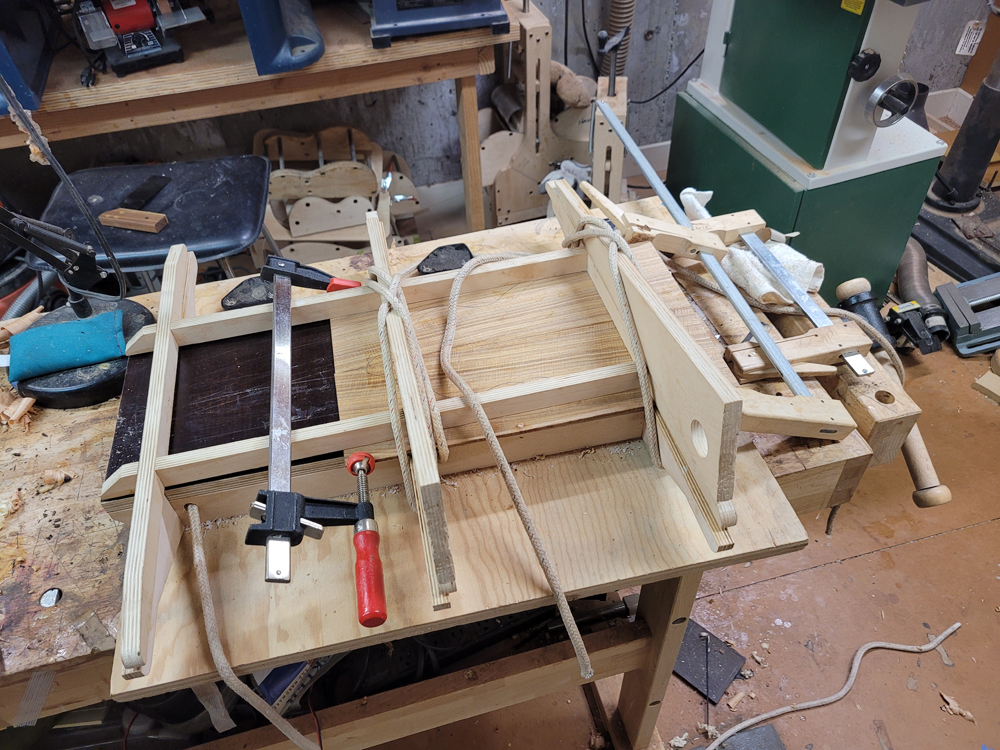
Here is most of the tonewood I will use. A couple of years ago I accidently rift sawed large mahogany neck blank. I also had a nice plate of ebony, so I used two rift saw mahogany pieces and the ebony to mack a neck blank. I will need some thin wings for the head stock to get enough width.
I used my bandsaw to profile the top and the back.
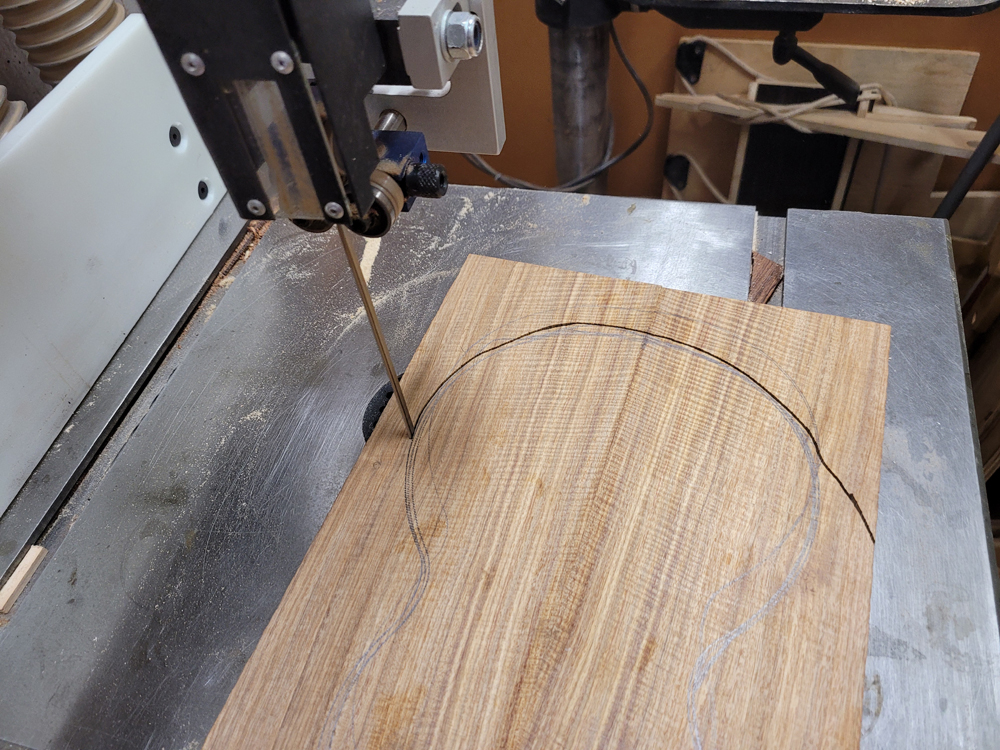
I installed a Paua Abalone rosette with black fiber purflings. I used my bishop cochren router base to to cut a 1/16" + 1 mm channel. I carefully set the diameter of the rosette using a set of calipers. I am using a 1/16" bit. I cut to the inside line, make the diameter 1 mm larger and cut for the purfling. I use a bit of the shell to set the depth.
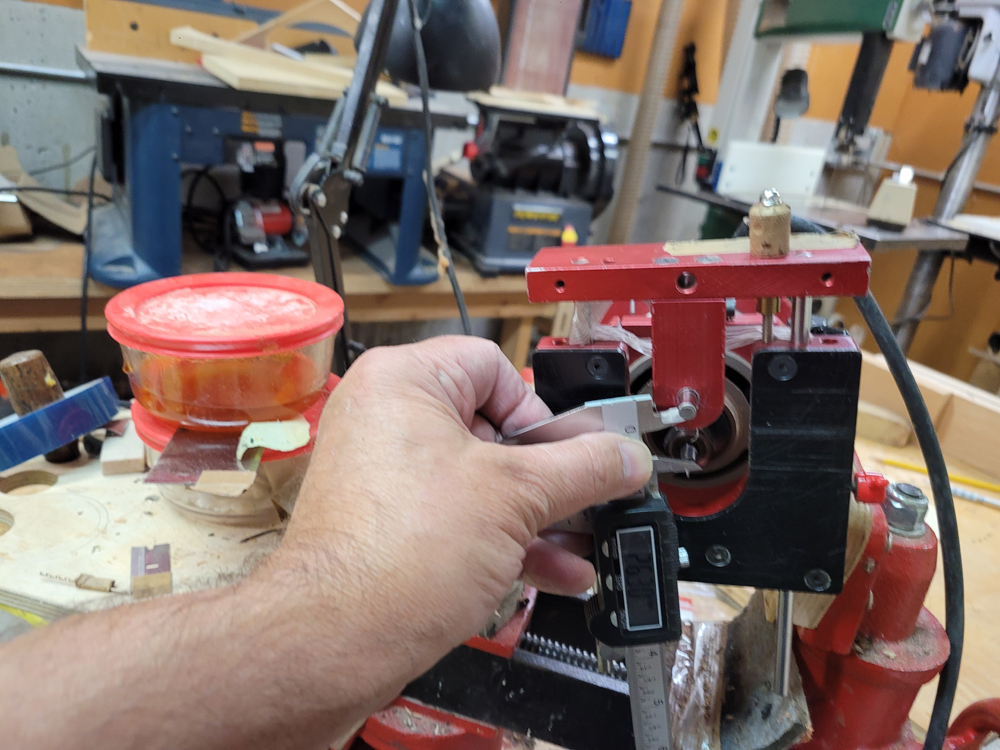
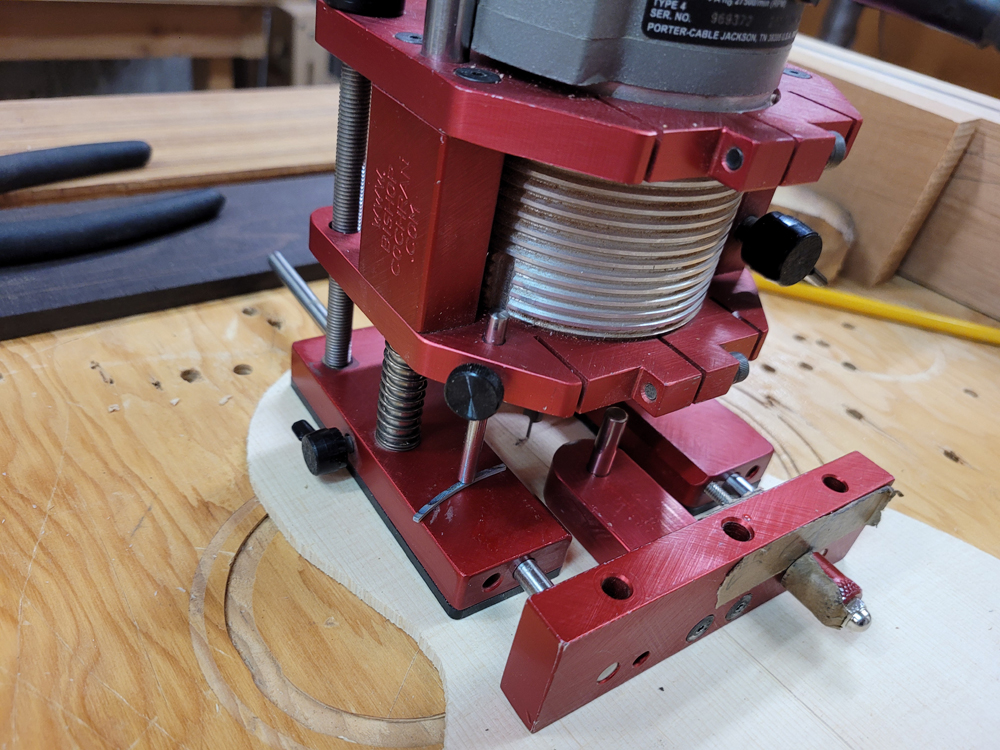
Once routed I tested it and ultimately made it a smidge wider to deal with swelling from the glue.
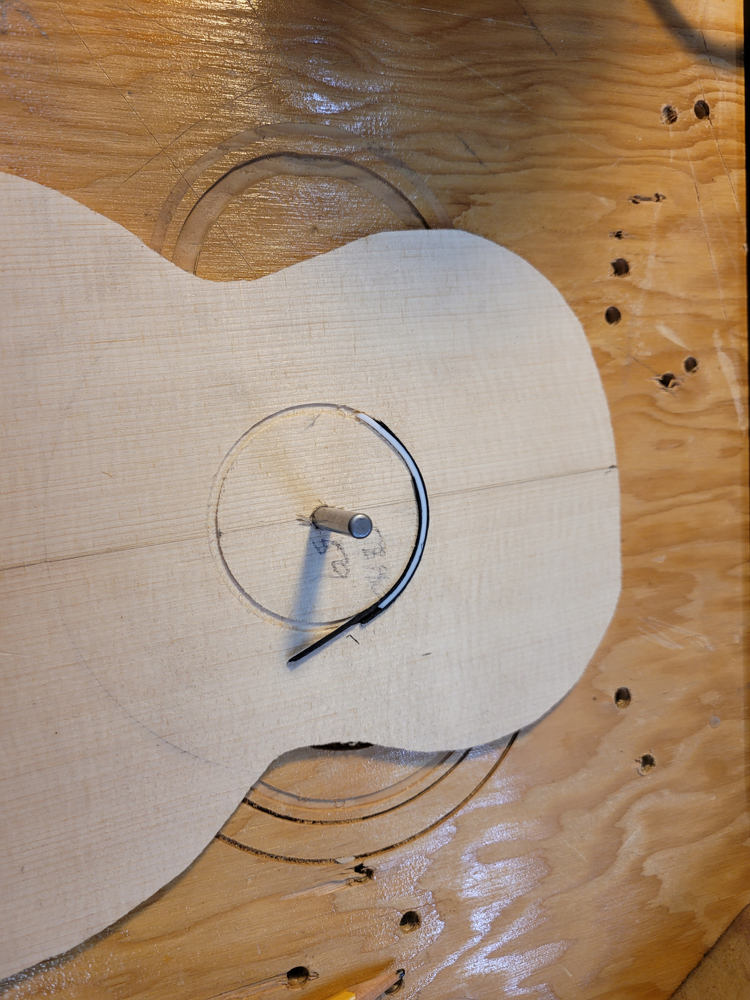
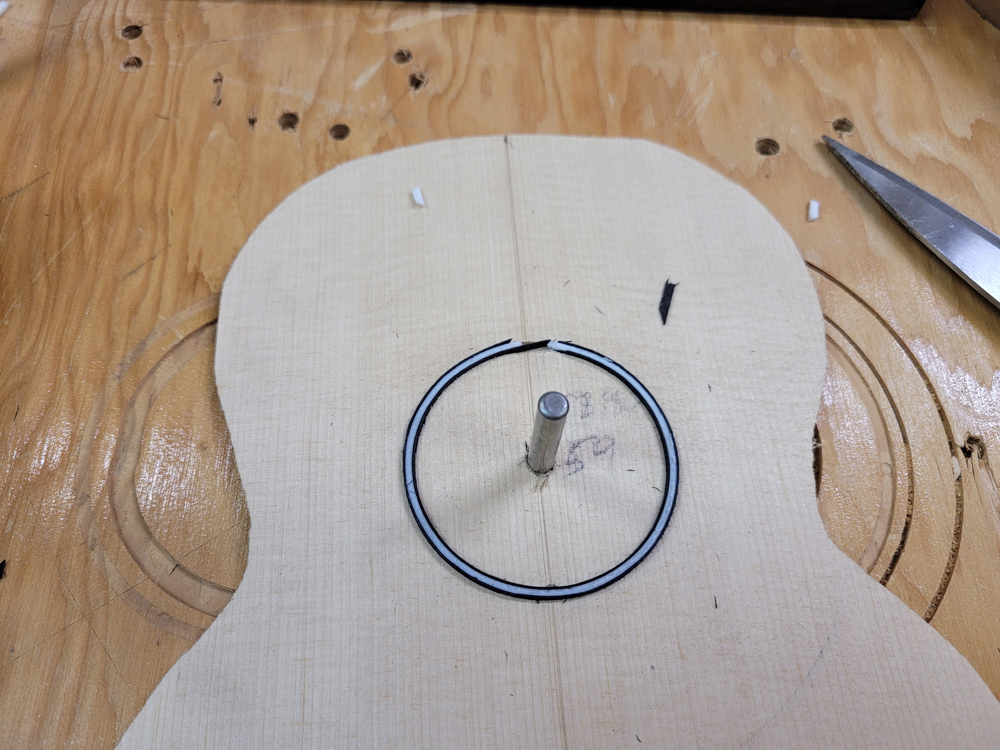
Once the glue set I leveled the fiber strips and cleaned out (well sort of cleaned out) the channel
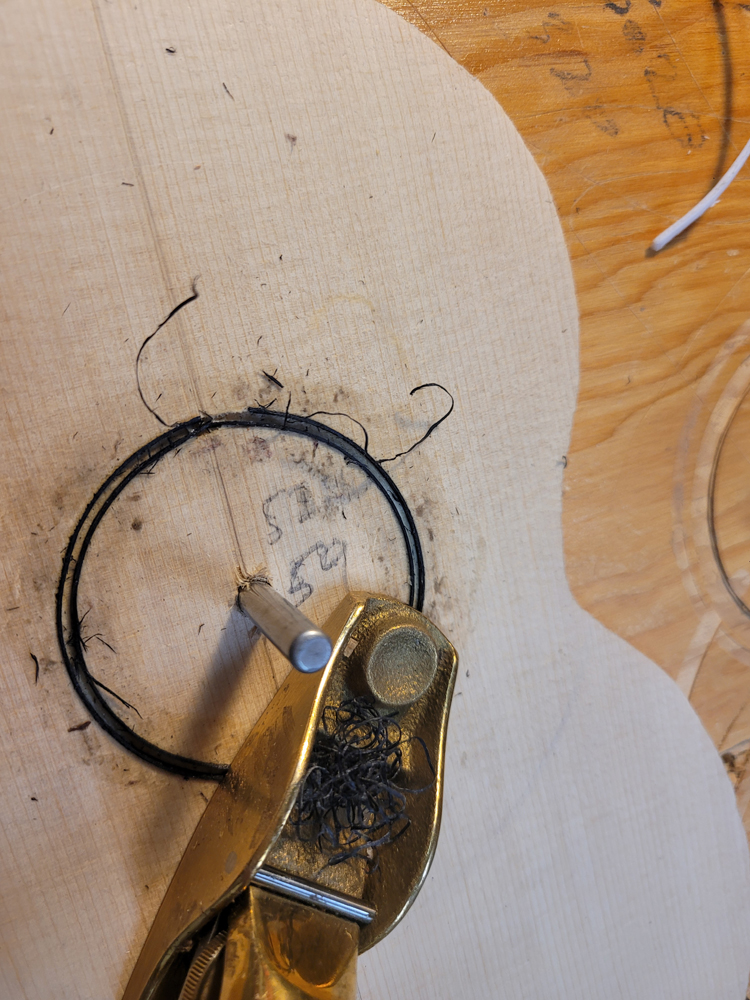
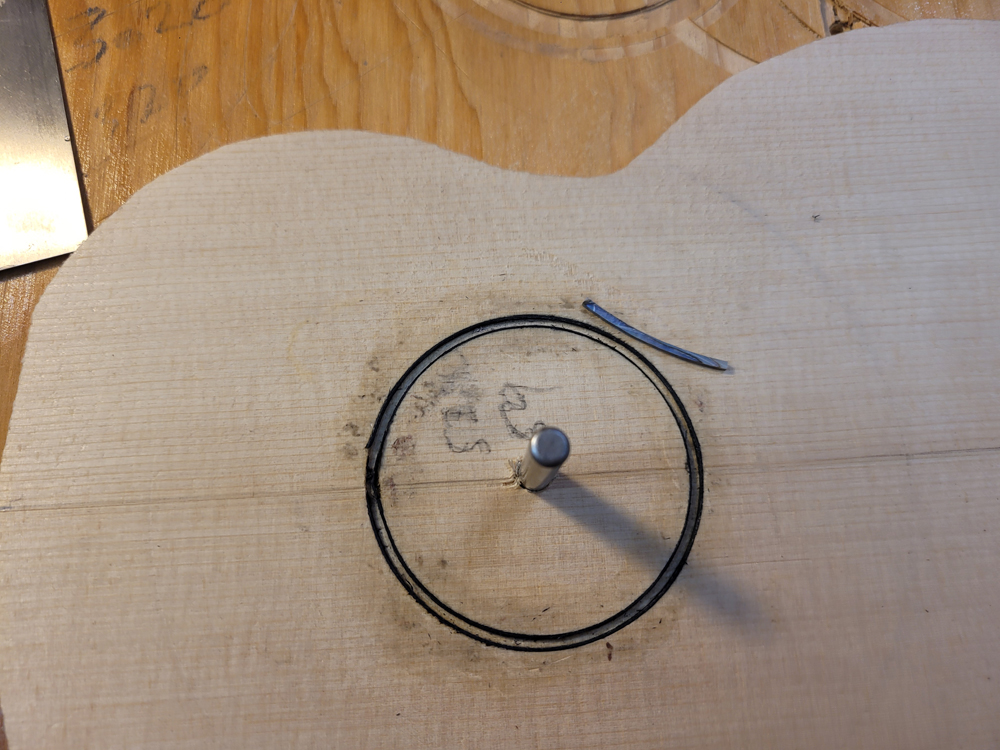
Then I just worked my way around breaking the abolone into the channel. I would start at one end jam as much as I could along the channel until the strip broke. I would use that pointy tool to push in the piece and once in, push back tight against the previous piece and repeat. I used thin CA to set the shell as I went. The spruce was sealed with the purfling and the glue I used to install the purfling.
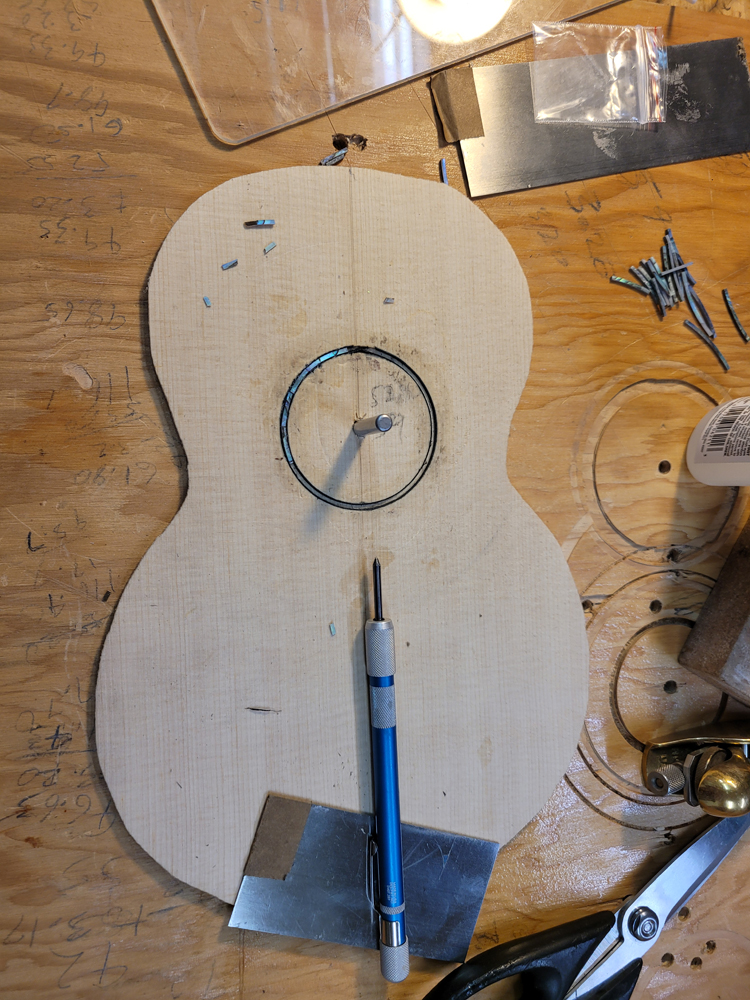
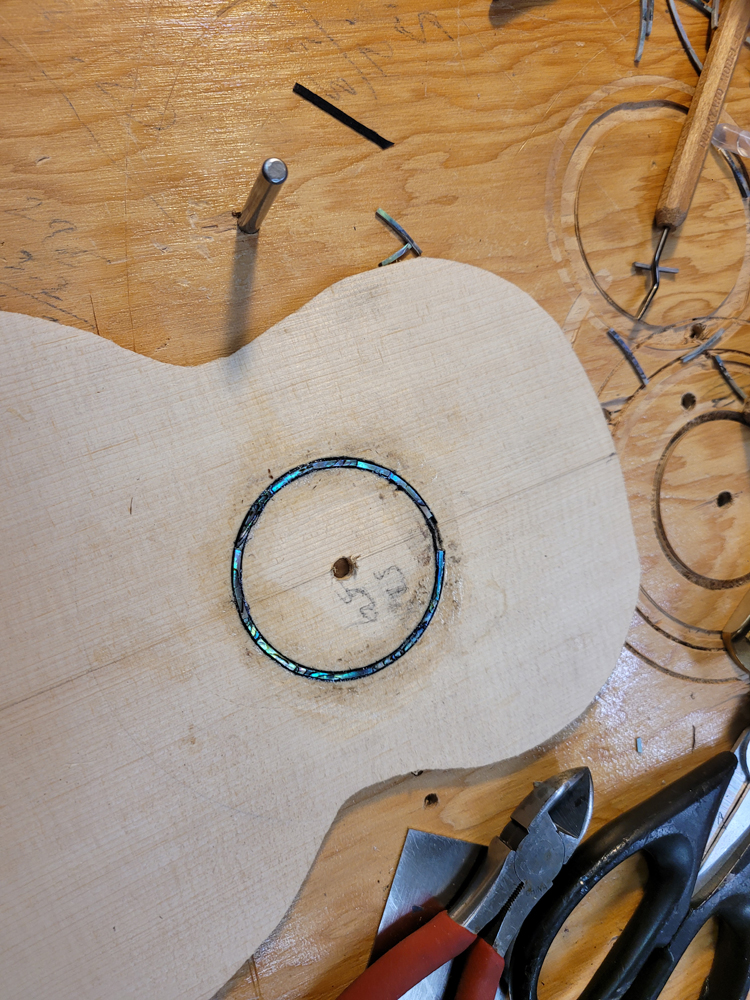
Level sanded.
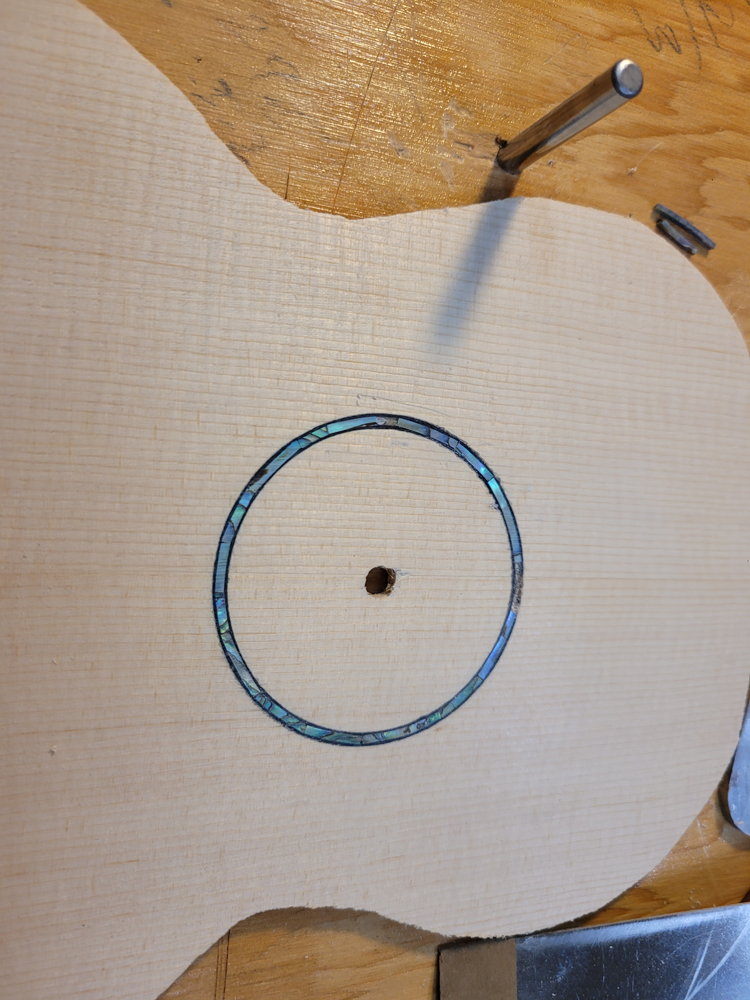
I used the same bit to cut out the sound hole. I set the bit depth a little more than my final top thickness. I sanded the back of the top until the sound hole dropped out.
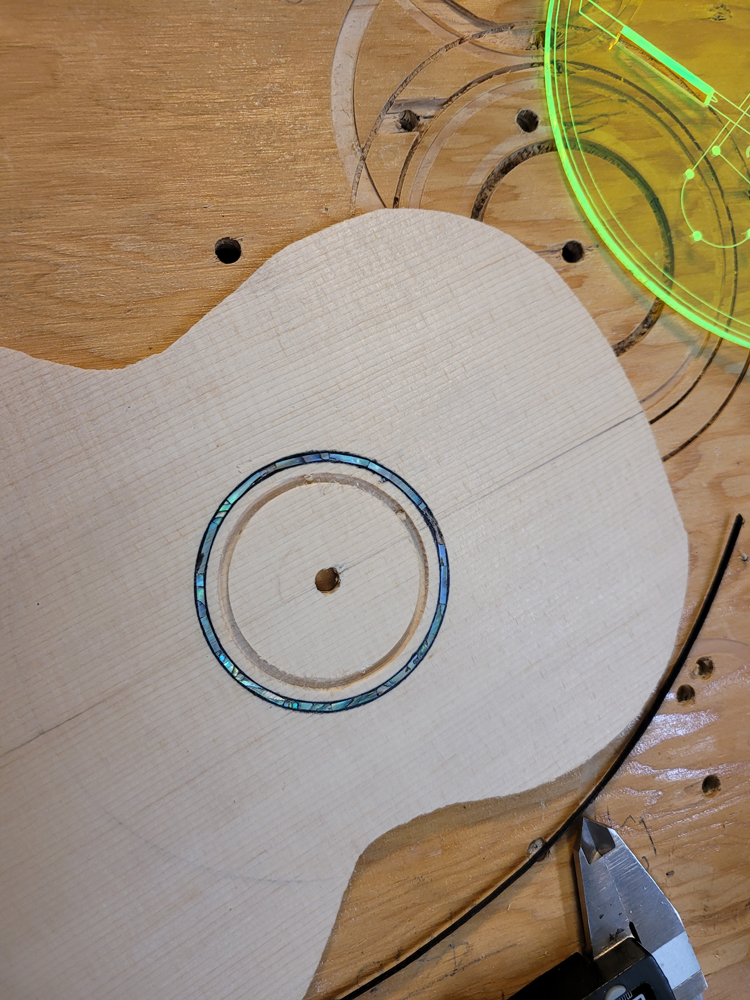
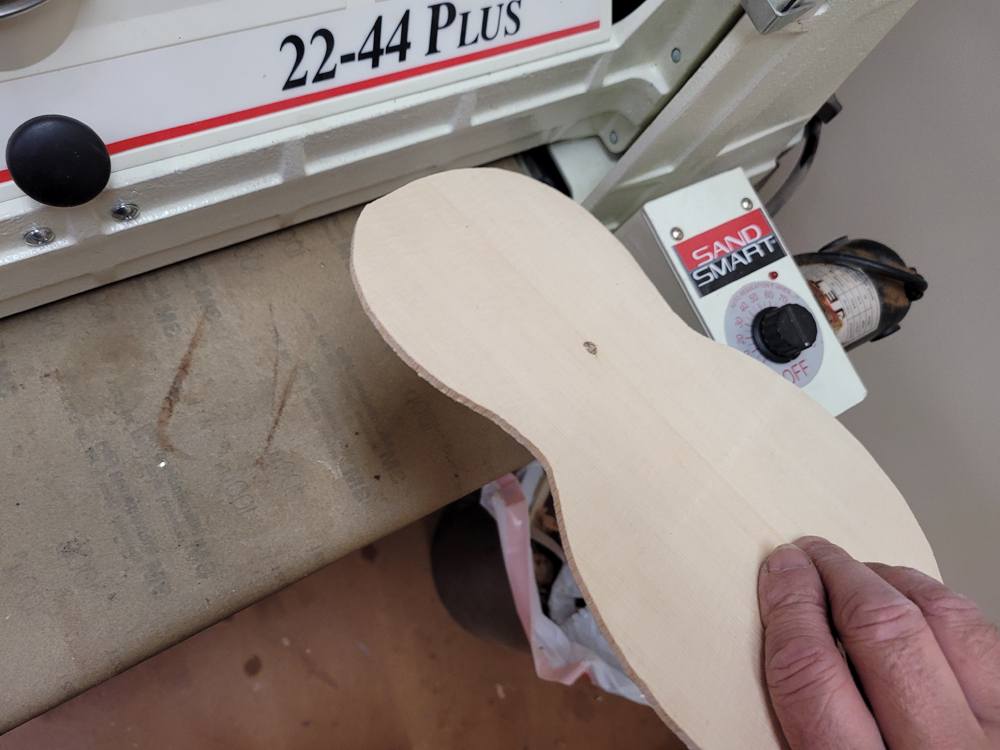
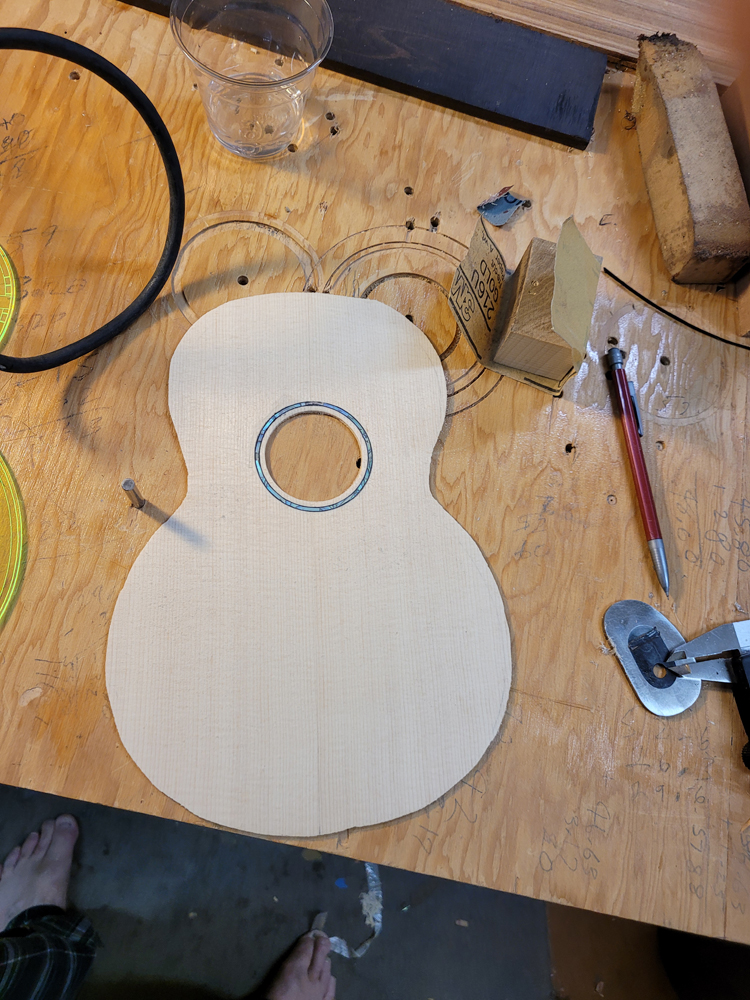
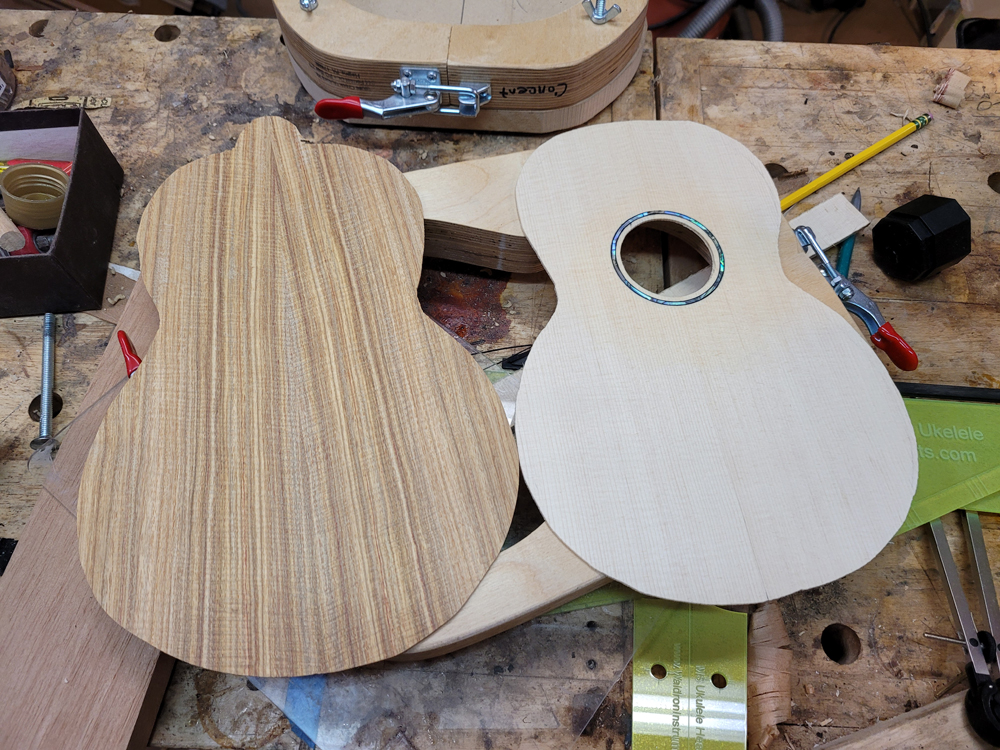
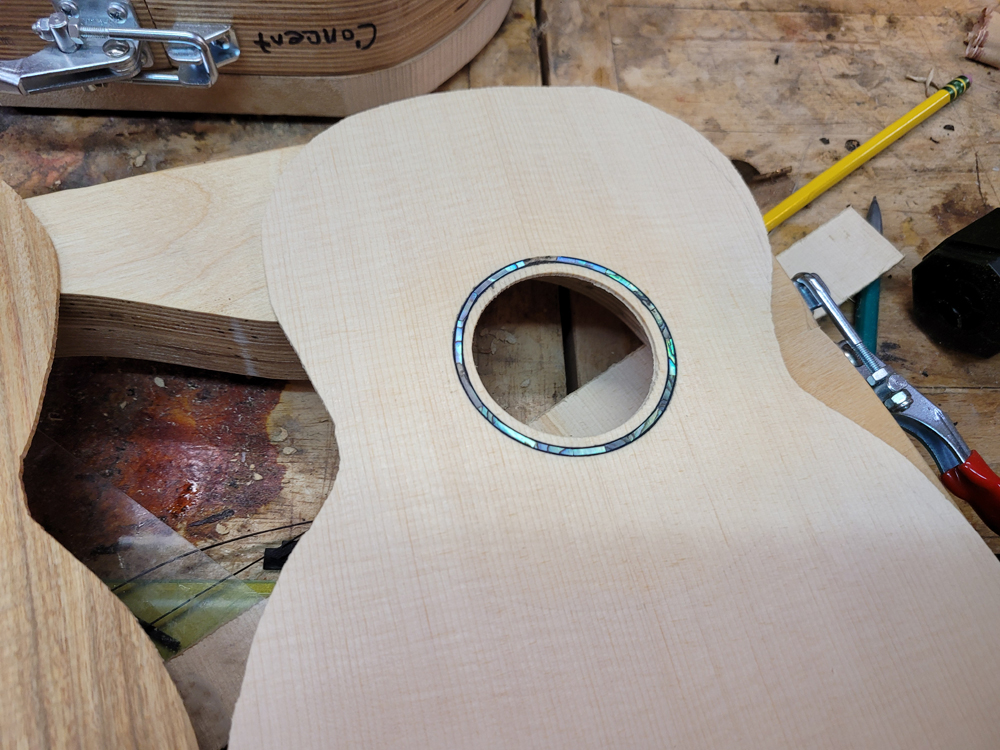
Tulipwood is an exotic wood native to the tropical region of South America, mainly Brazil. It is a hard and heavy wood, with a rather fine texture. The sapwood is a solid yellow color, while the heartwood color ranges from a pink to a darker red, with a straw colored background. Tulipwood is excellent for wood turning, as well as knife handles, furniture, and cabinets. It is a lustrous wood, has excellent polishing qualities, and glues well.
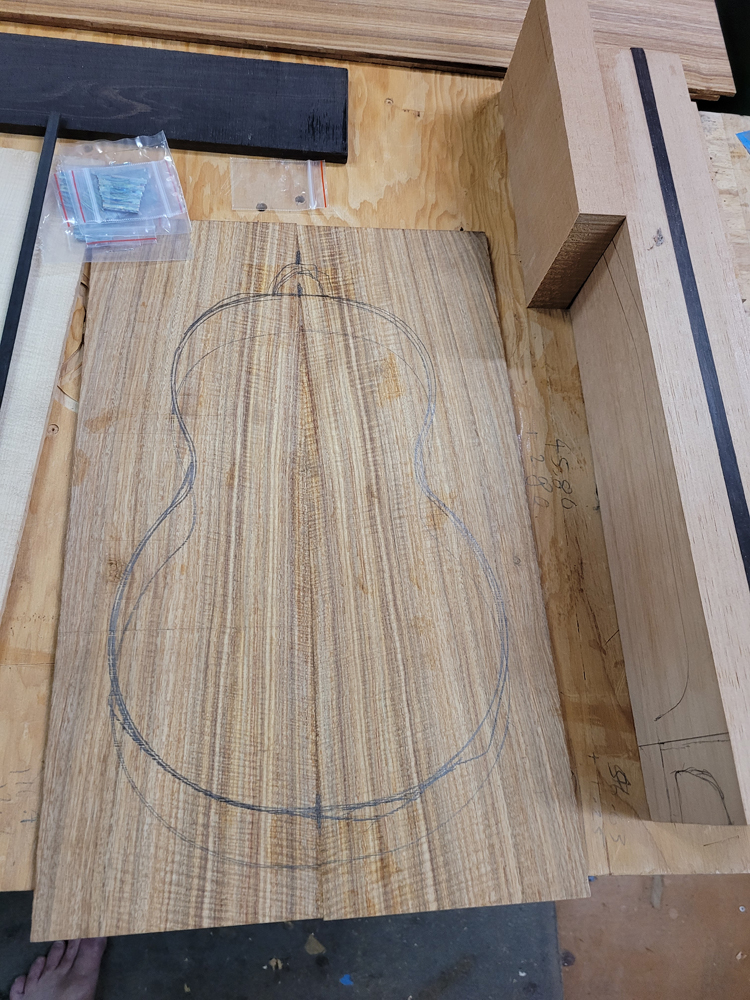
I have never made a concert before, I once bought a complete set of Martin Ukulele forms at an auction so I was some what ready. I got a mold from John Hall modified it and combined it with a work board for a Spanish neck joint. In the background you will see I have a second mold that I will use if I ever do a bolt on.
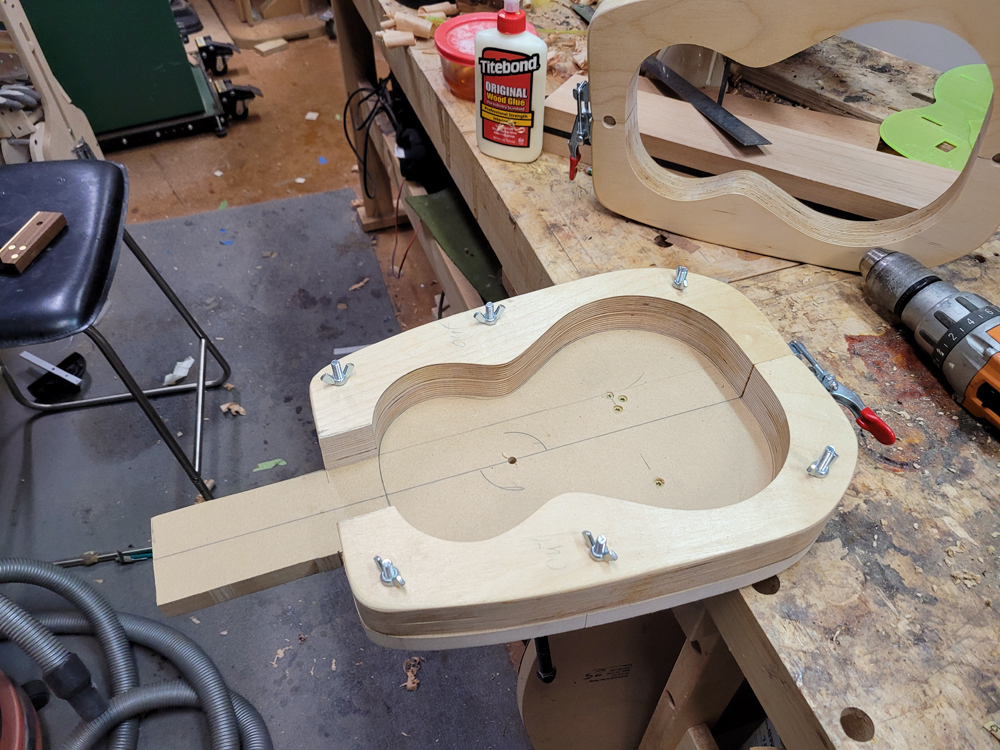
I used an old record plane to joint the plates. I used my guitar plate jointing jig to clamp the plates together but it really was too big.
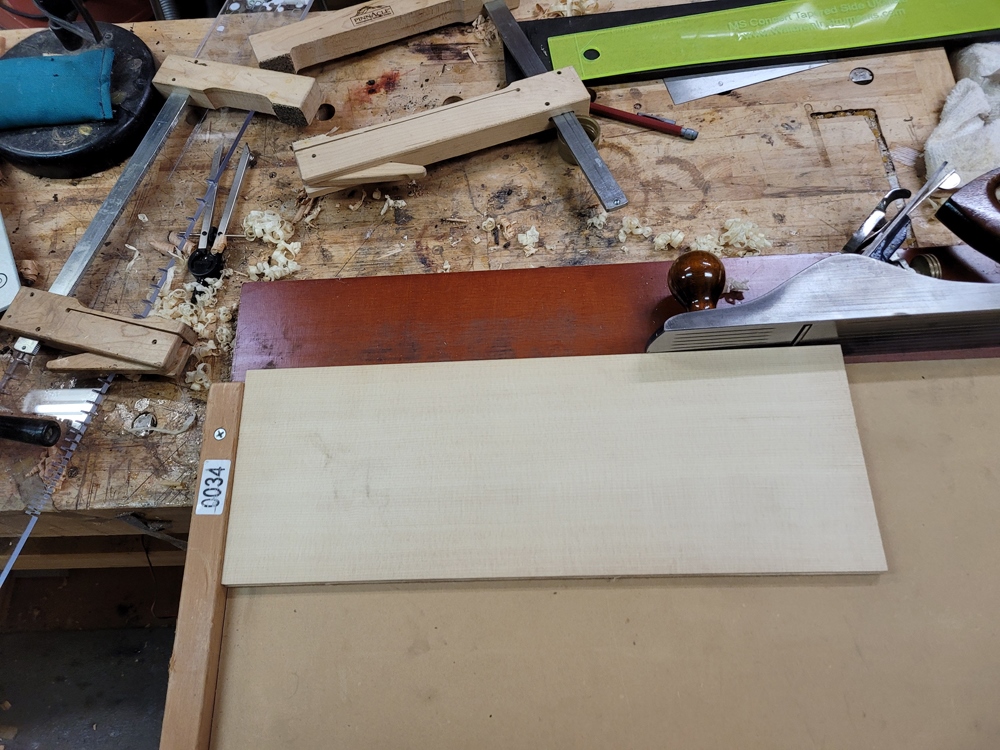
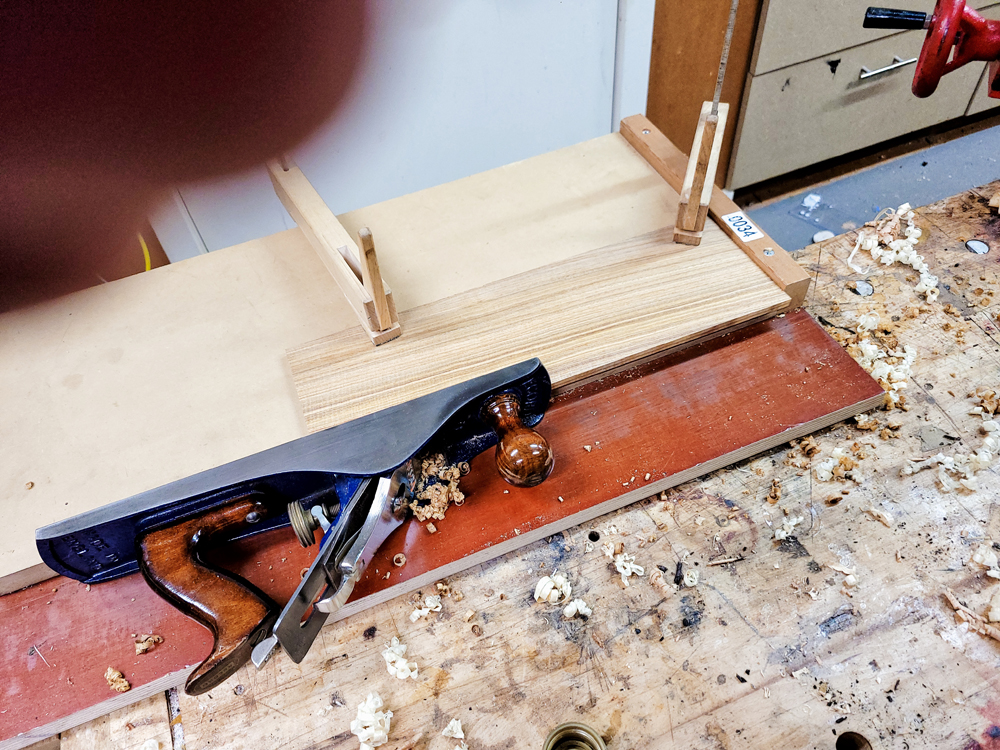
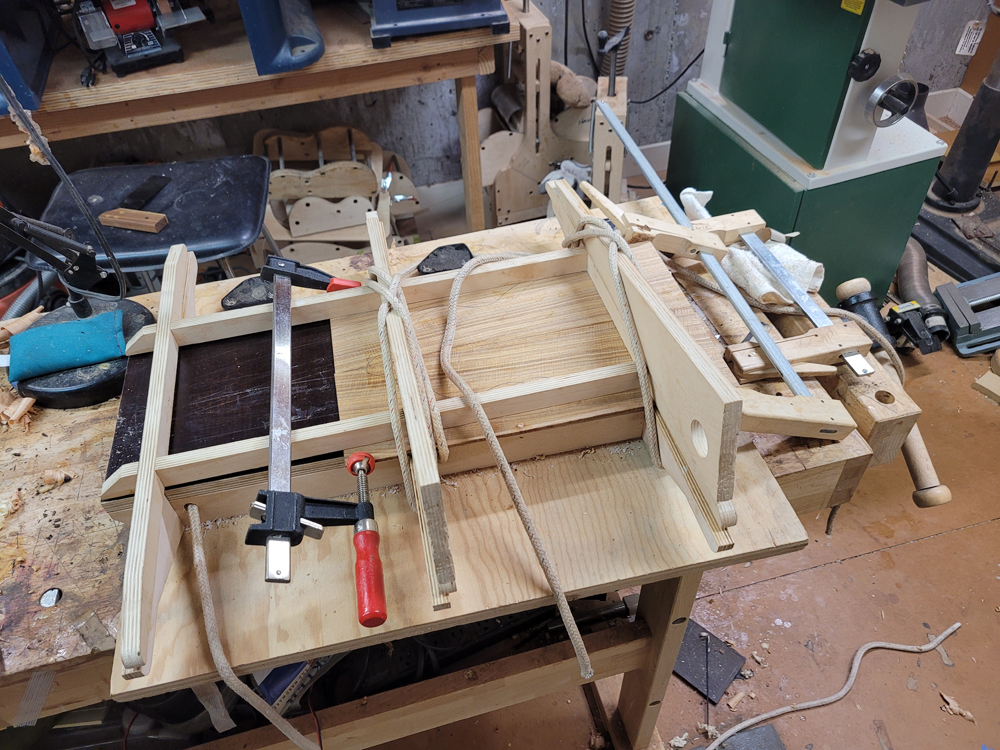
Here is most of the tonewood I will use. A couple of years ago I accidently rift sawed large mahogany neck blank. I also had a nice plate of ebony, so I used two rift saw mahogany pieces and the ebony to mack a neck blank. I will need some thin wings for the head stock to get enough width.
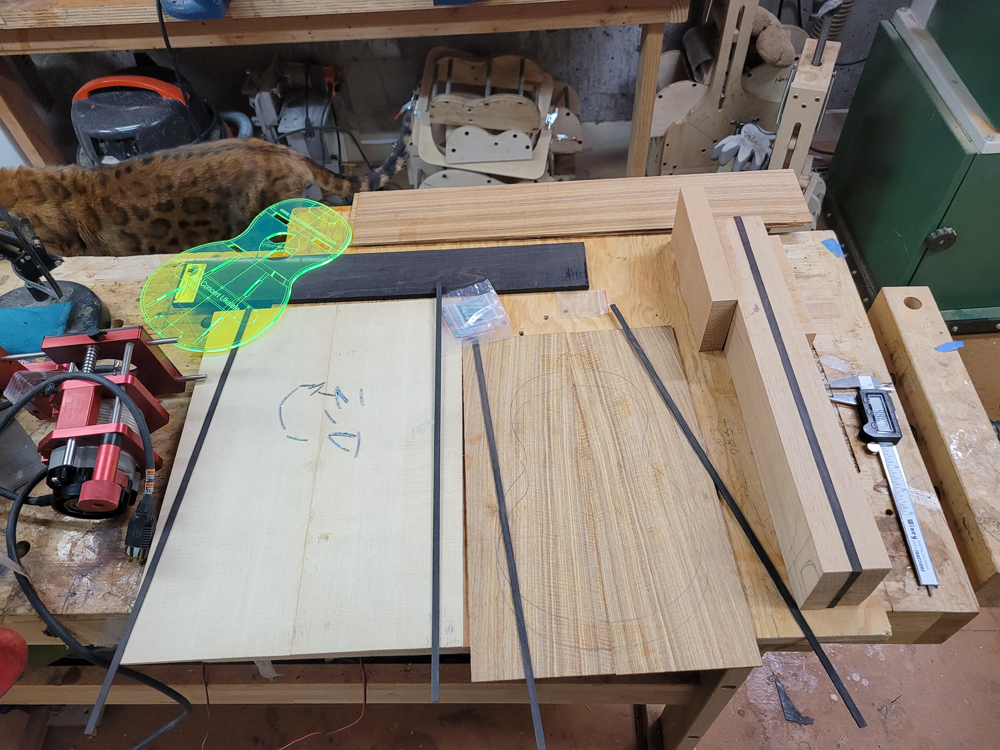
I used my bandsaw to profile the top and the back.
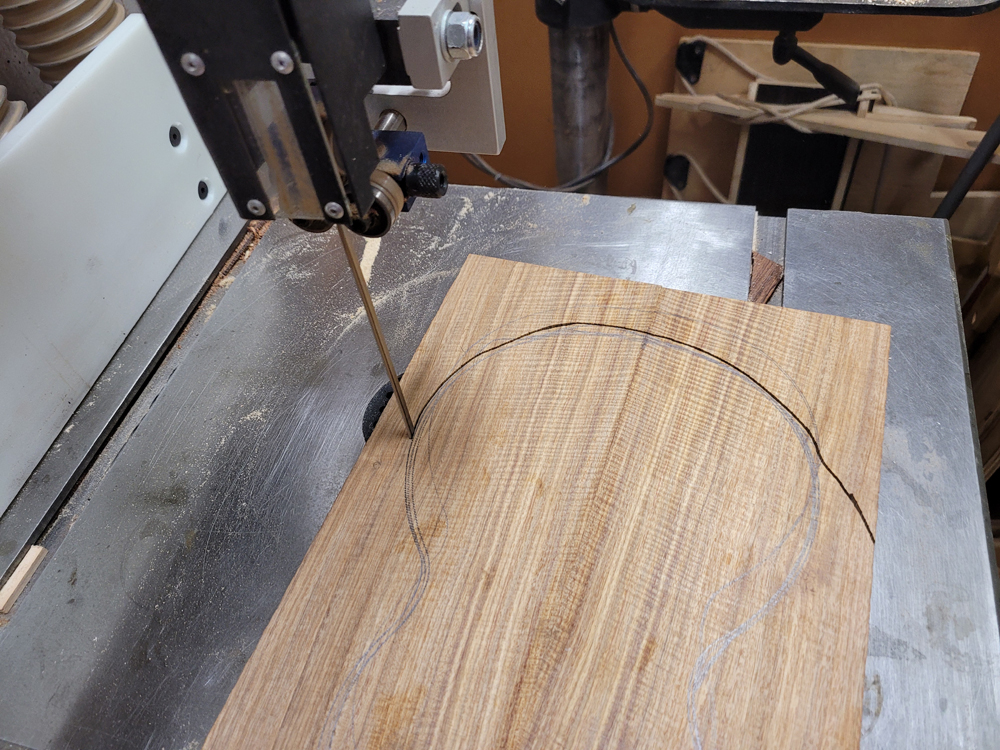
I installed a Paua Abalone rosette with black fiber purflings. I used my bishop cochren router base to to cut a 1/16" + 1 mm channel. I carefully set the diameter of the rosette using a set of calipers. I am using a 1/16" bit. I cut to the inside line, make the diameter 1 mm larger and cut for the purfling. I use a bit of the shell to set the depth.
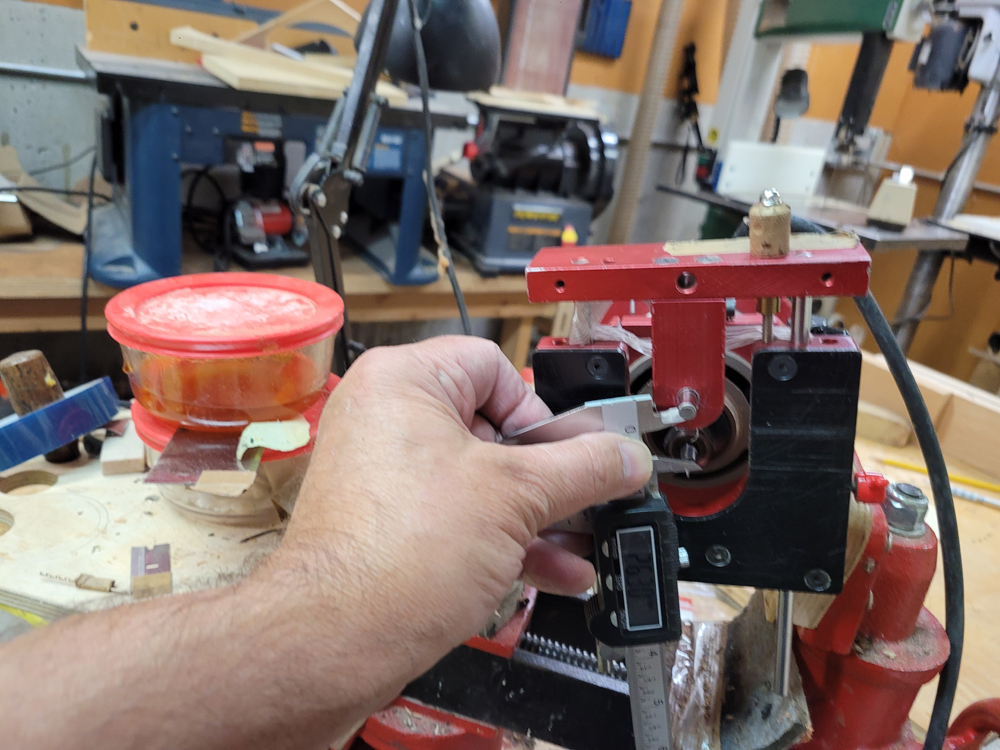
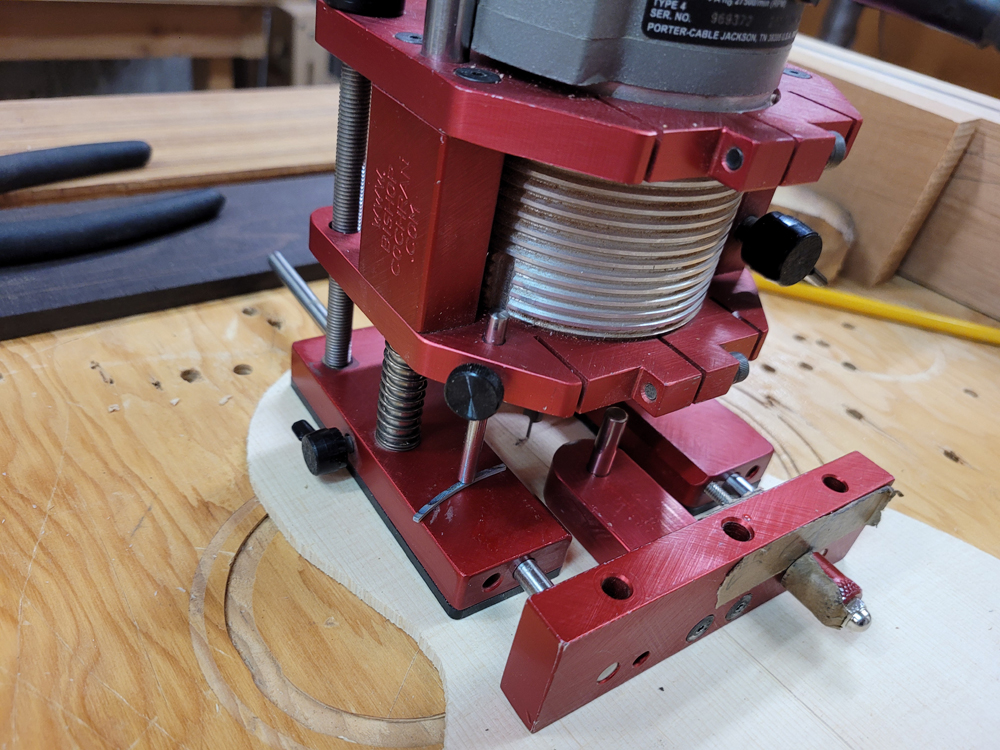
Once routed I tested it and ultimately made it a smidge wider to deal with swelling from the glue.
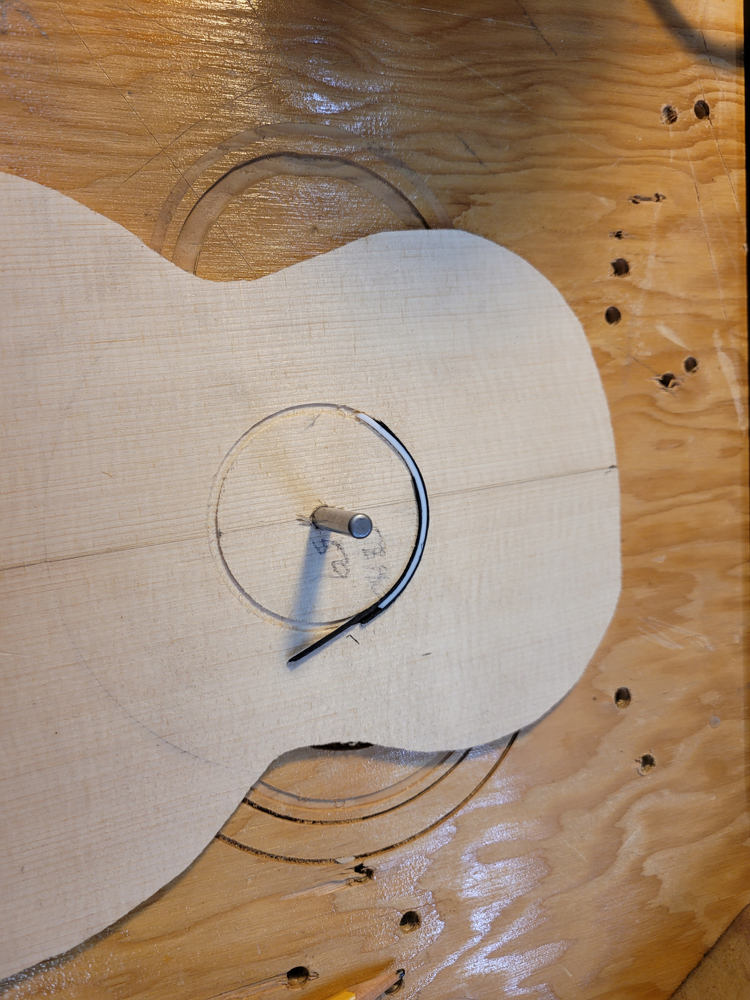
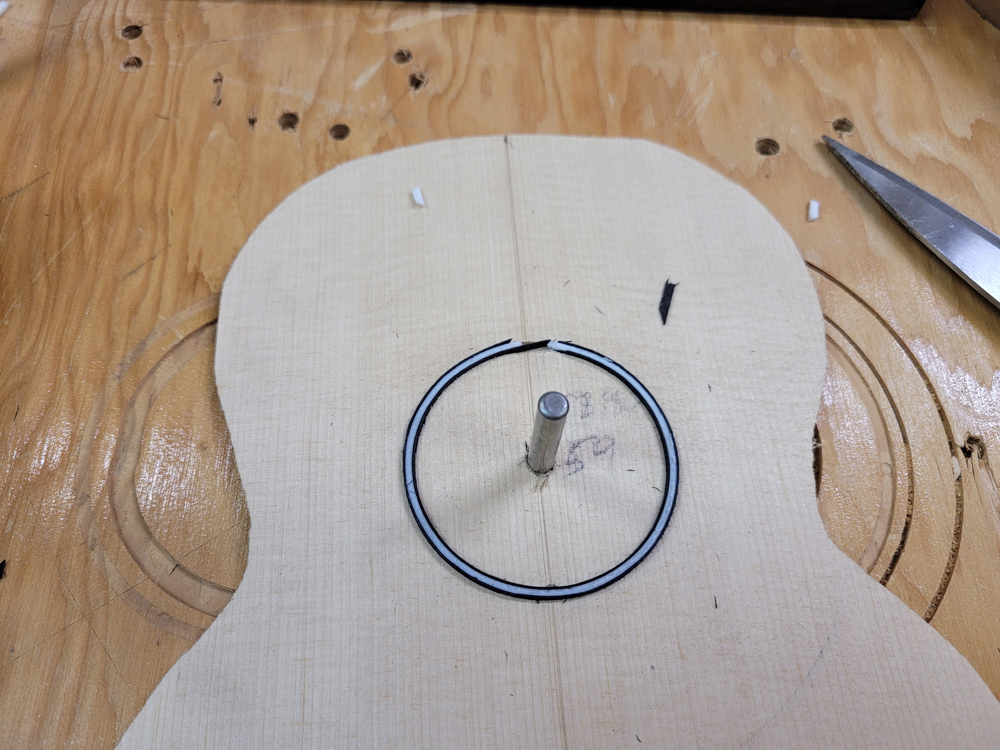
Once the glue set I leveled the fiber strips and cleaned out (well sort of cleaned out) the channel
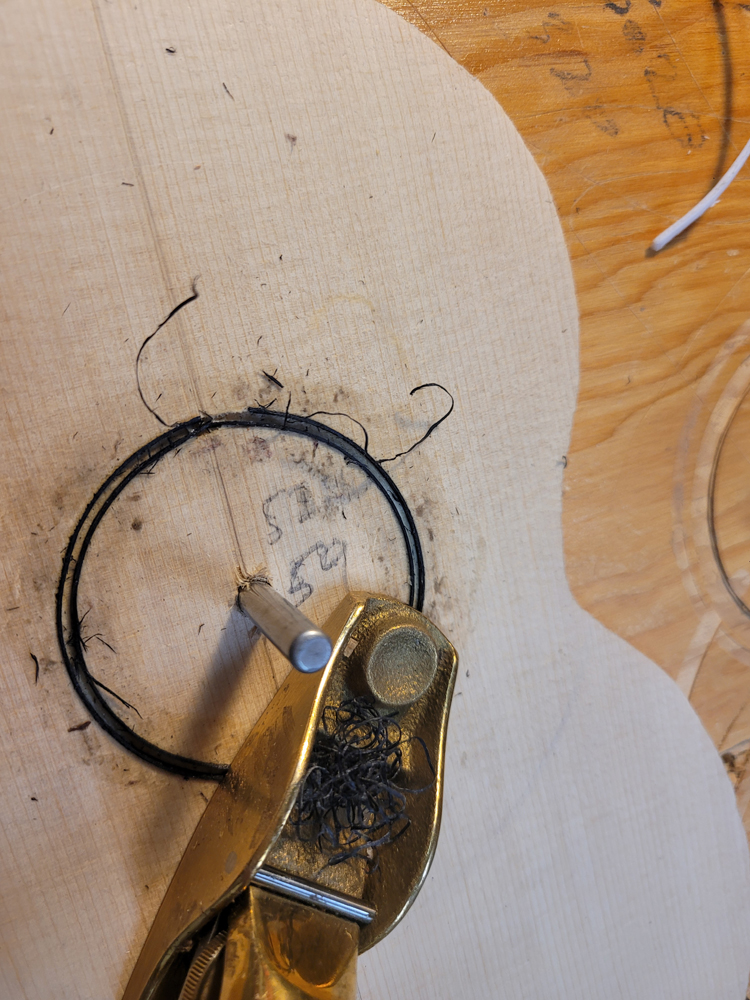
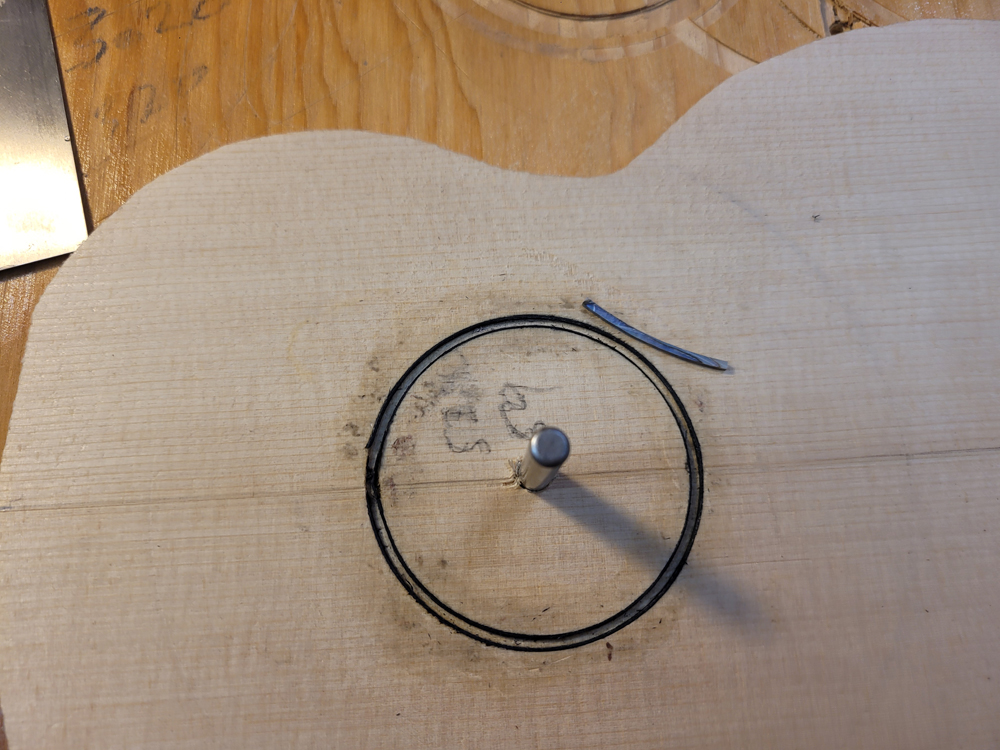
Then I just worked my way around breaking the abolone into the channel. I would start at one end jam as much as I could along the channel until the strip broke. I would use that pointy tool to push in the piece and once in, push back tight against the previous piece and repeat. I used thin CA to set the shell as I went. The spruce was sealed with the purfling and the glue I used to install the purfling.
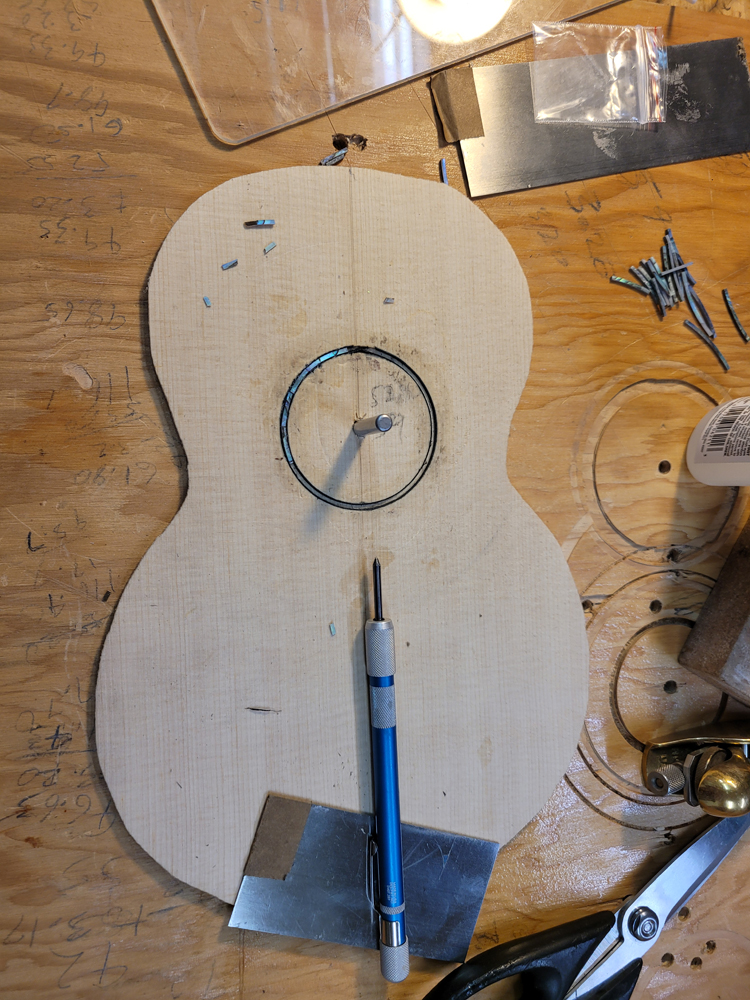
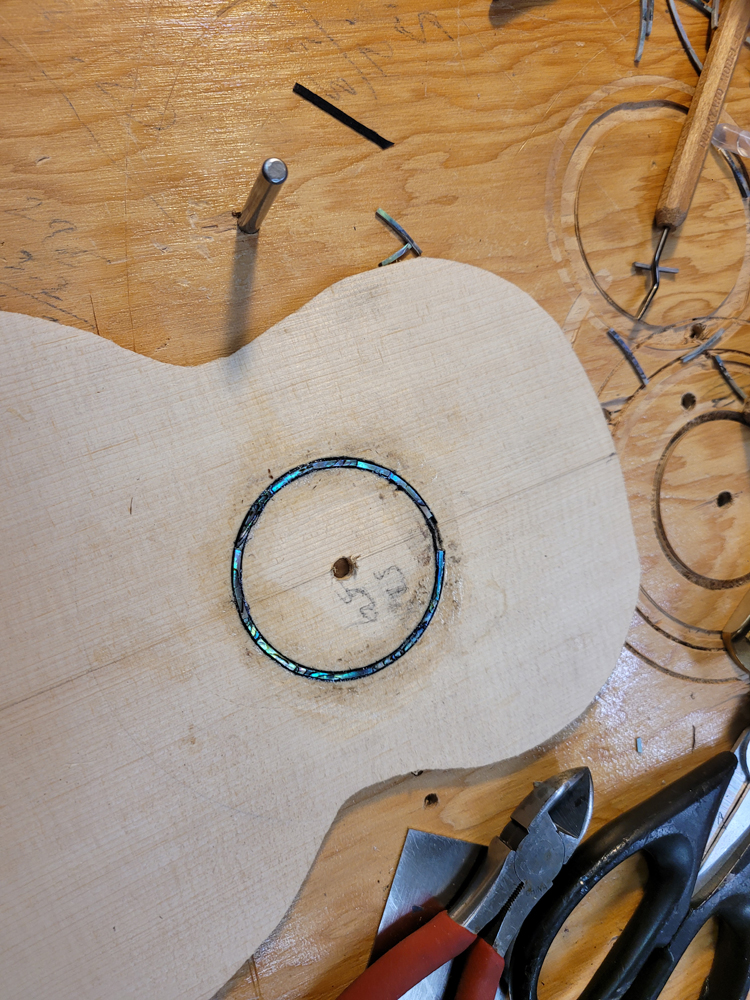
Level sanded.
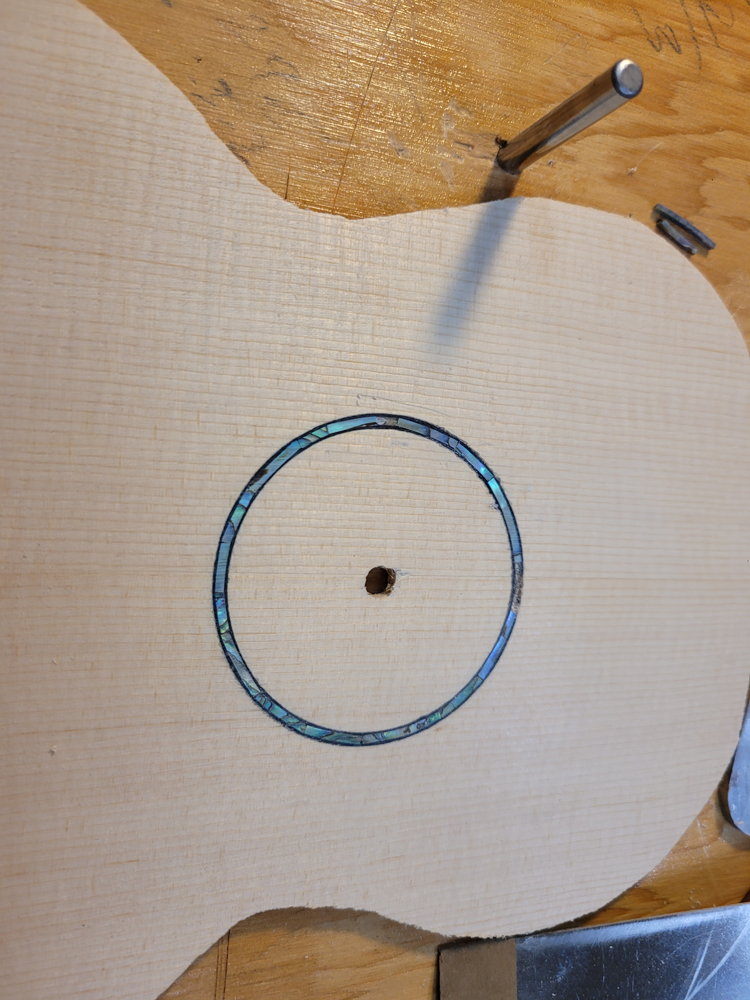
I used the same bit to cut out the sound hole. I set the bit depth a little more than my final top thickness. I sanded the back of the top until the sound hole dropped out.
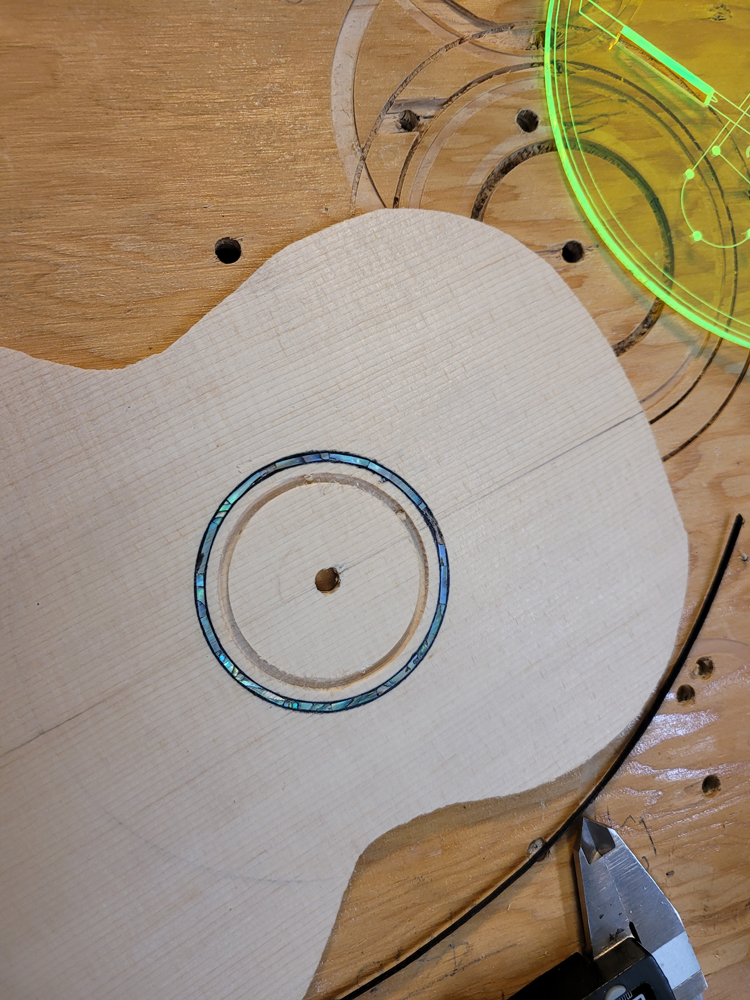
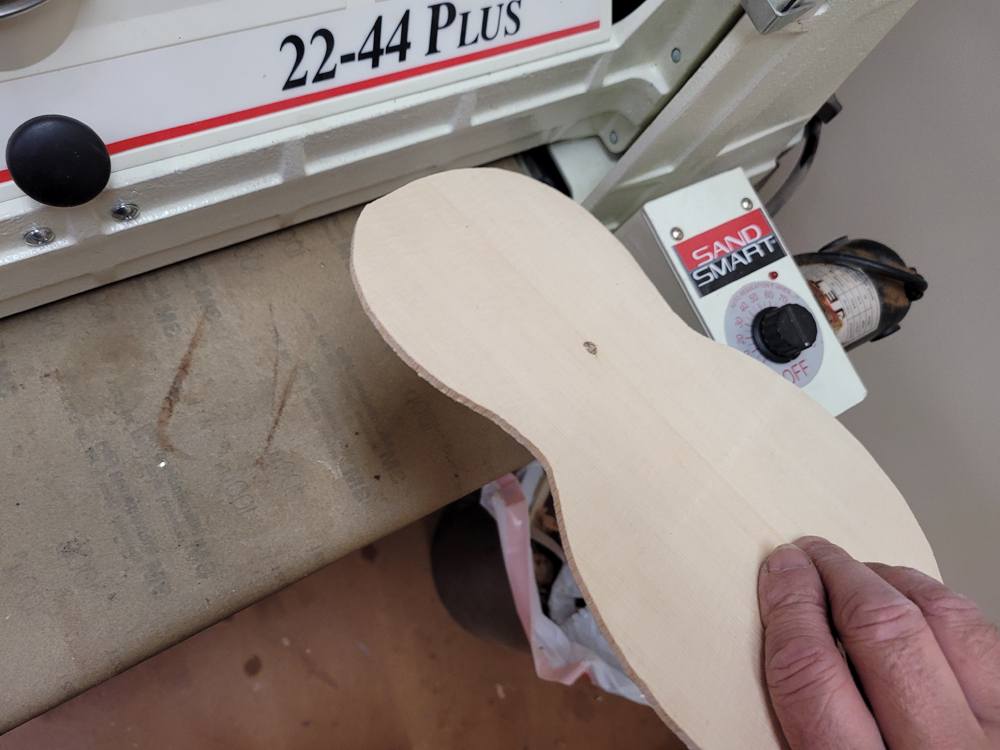
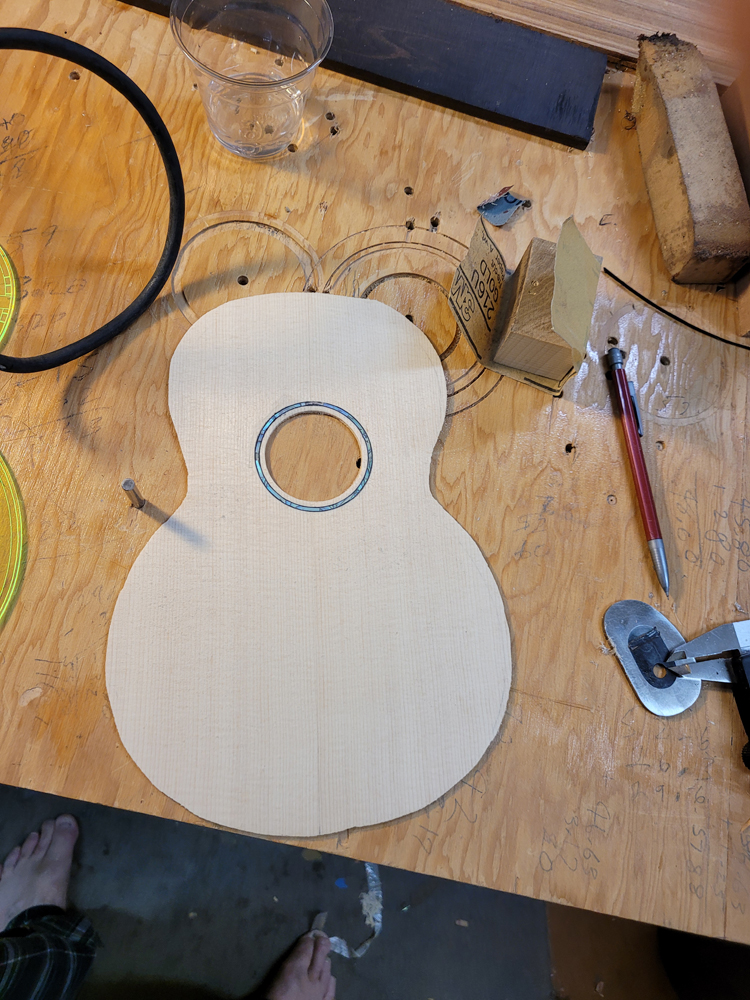
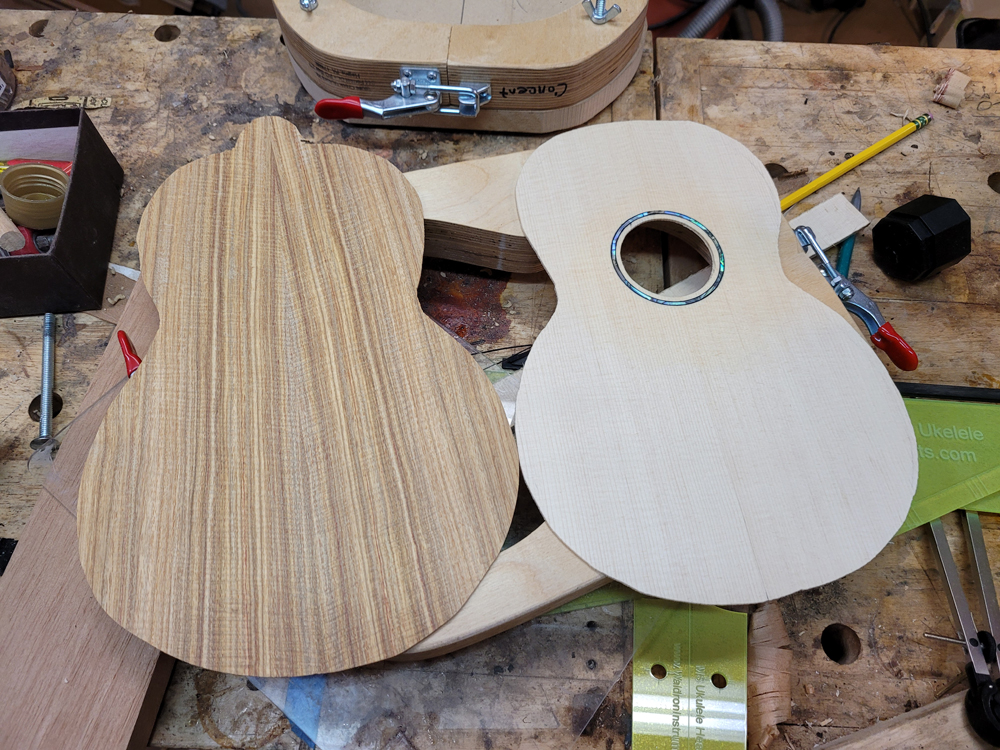
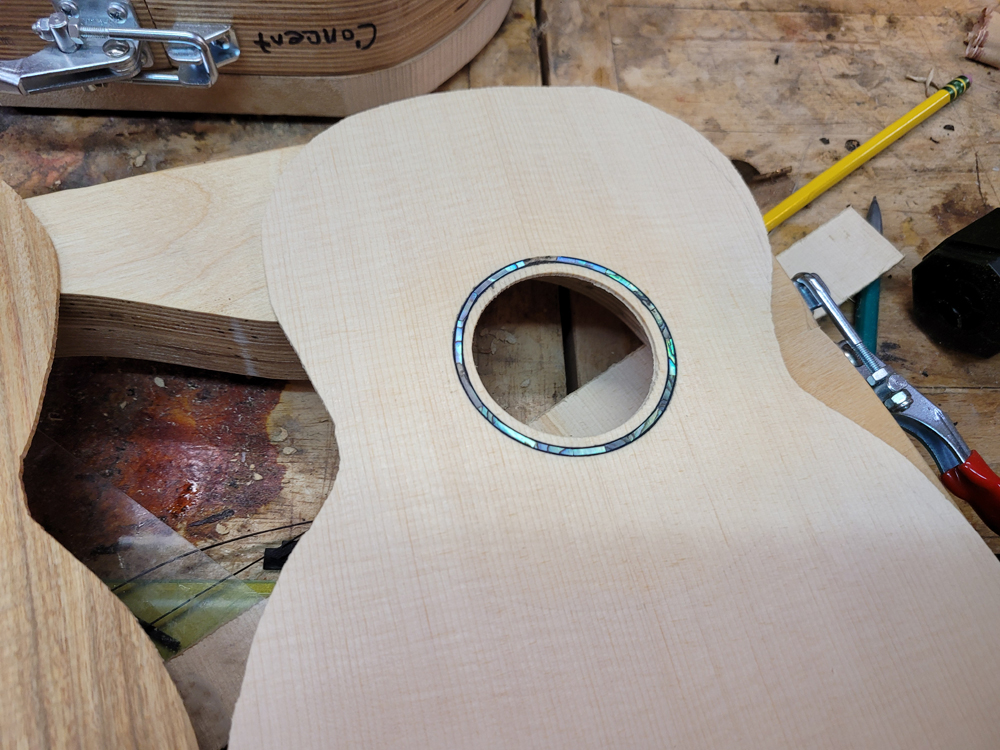