Koa/Bear Claw sitka 00 12 fret short scale.
Posted: Sun Apr 05, 2020 11:29 pm
While locked up in social distancing I have been working on a commision. This will be a Martin (xbrace) style 00, 12 fret short scale guitar. It has been awhile since I have built an X-braced guitar but for the playing style and what this client is looking giving him a Martin sounding guitar is the right choice. Going back and forth a bit I assembled a kit from which to build.
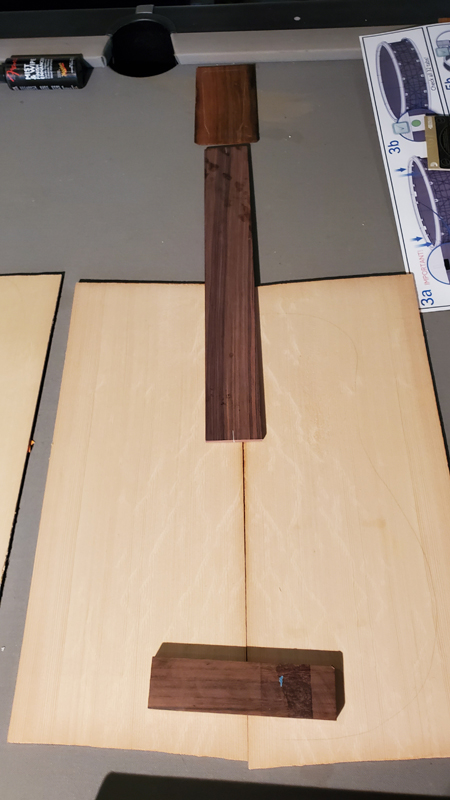
With some really figured and flamed Hawaiian Koa. I felt really guilty about the Koa as it was an auction item in the Seattle Lutherie Group auction that went way below cost.
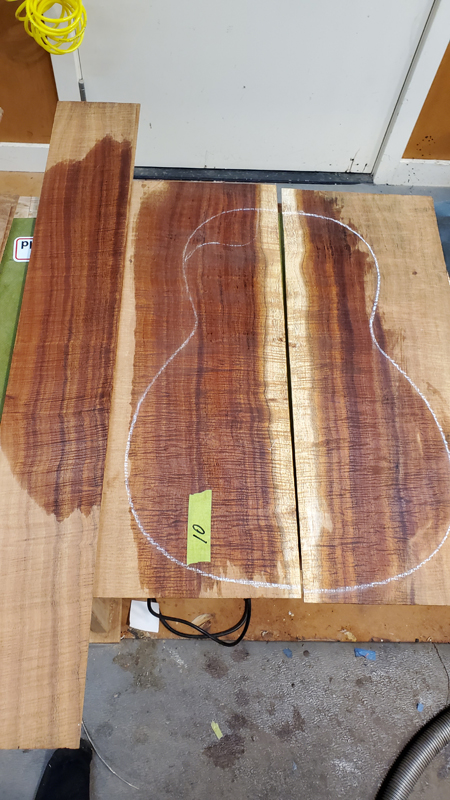
Unfortunately the sides were a bit too wild and their was a flaw in a dark figure line on a side that seperated when bending. Amazingly not on the venetian cutaway side but in the wide curve on the non cutaway side.
I did have a lot of Koa so I grabbed another set of sides that were a good color match. Still figured but not as much flame. Same back as the previous picture just different lighting.
So the second set of sides I thinned to just under .080" and I scraped the inside of the cut away to .070" from just past the waist through the cutaway bends to the end.
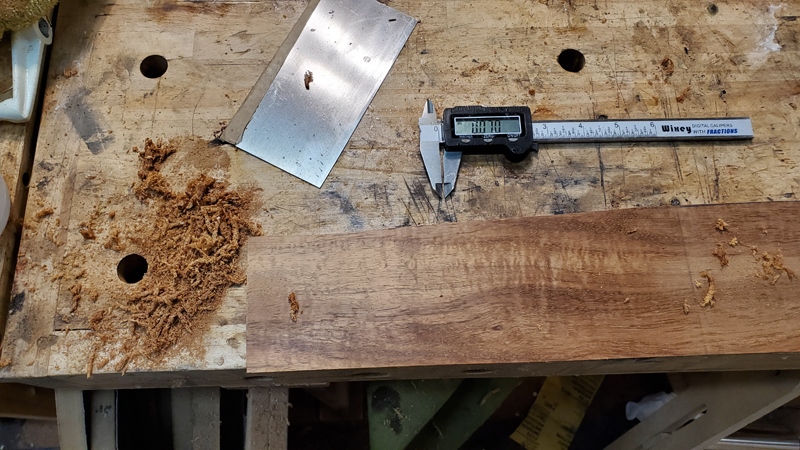
I sprayed them both with supersoft II, wrapped them and let them set under some weight (a big piece of ebony) overnight.
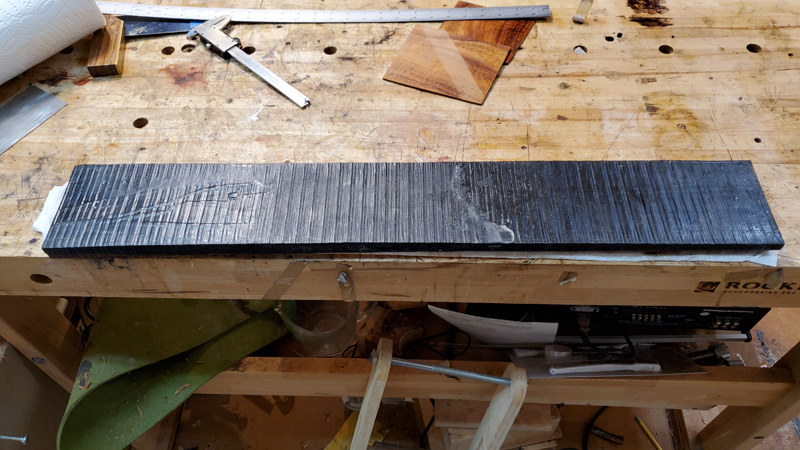
No problem with these bends in my fox style bender. While bending the cutaway I heat the bottom side of the cutaway area with a heat gun. I really took my time screwing in that last tight bend. I also used my stainless spring steel slats as my soft steel ones seem to ebonise koa. I learned that on my set of broken sides. It can be sanded out but I could also avoid it using stainless. I really need to take care removing the cutaway side as the spring steel can blow it up. (happened to a friend of mine once).
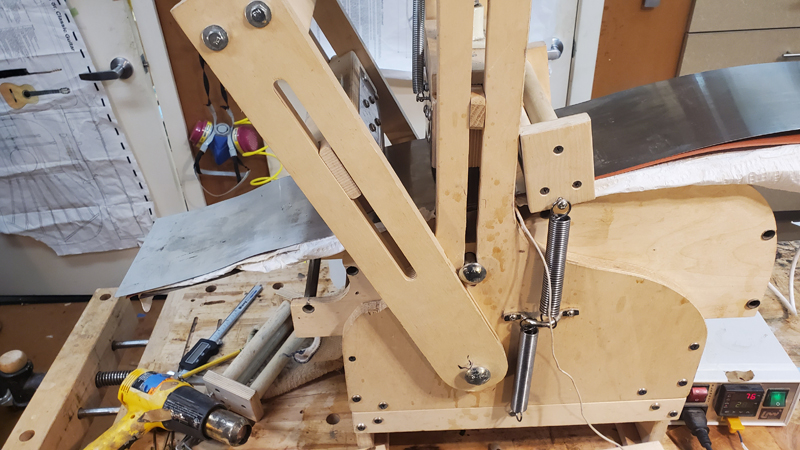
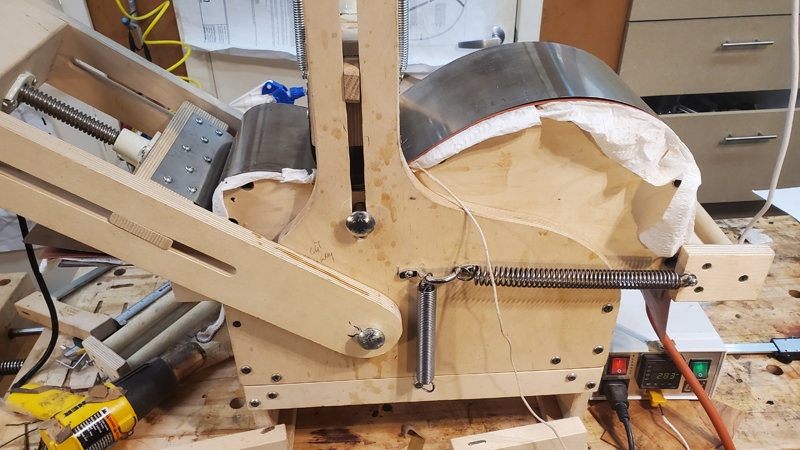
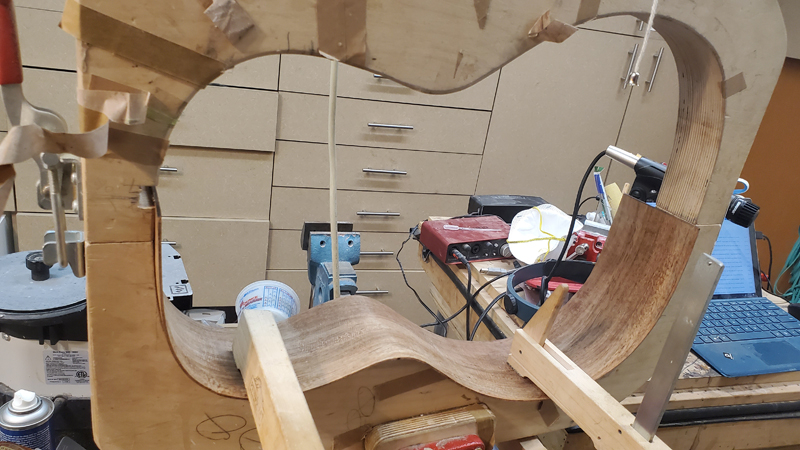
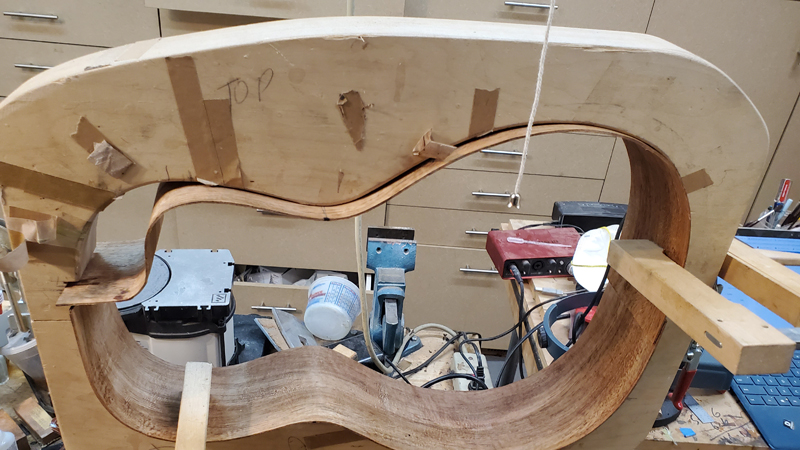
To get the heel block just right I put poster board under the guitar sides in the mold (not shown) and I traced out the pattern for the heel block. I glued that to chunk of mahogany and cut it out on the bandsaw.
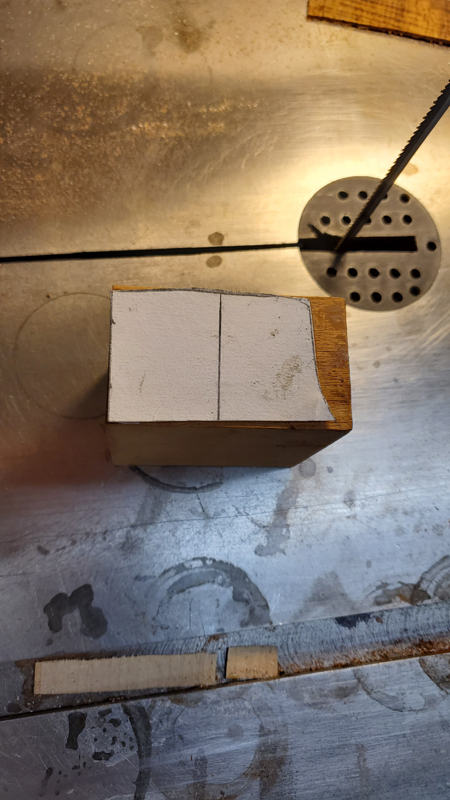
I used to try and glue in the heel block in one go. Now I glue first to the non cutaway side and then glue the cutaway side to the block. To assure alignment I set a couple of clamps while the sides are in the mold to hold it in position. I then remove the clamped block and side from the mold to make sure I can really clamp it.
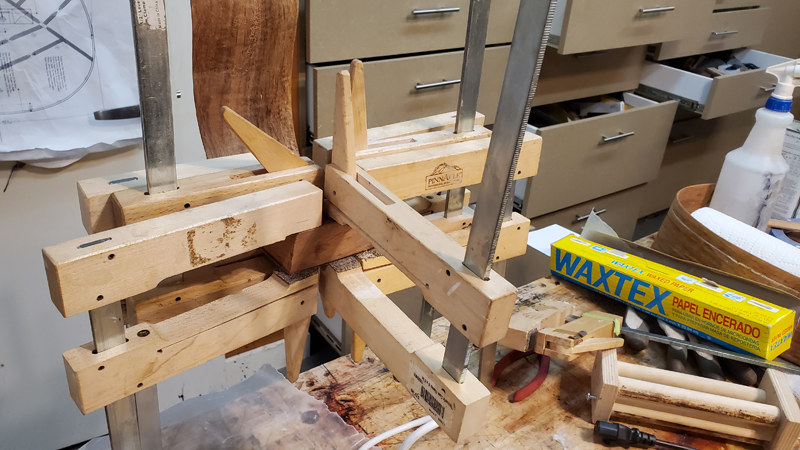
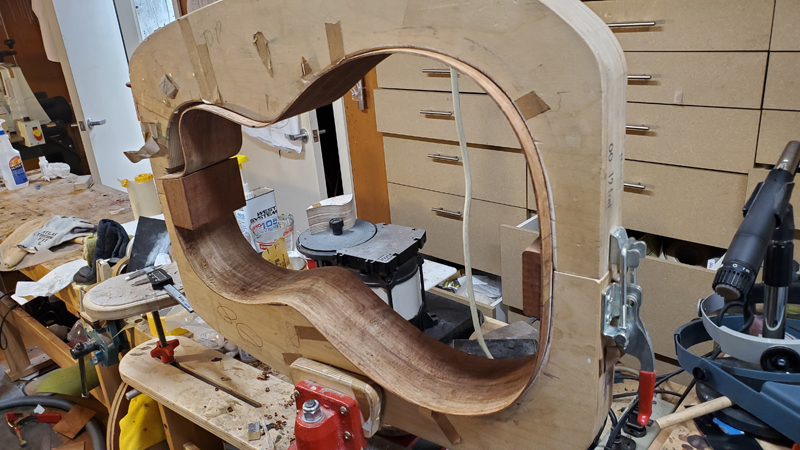
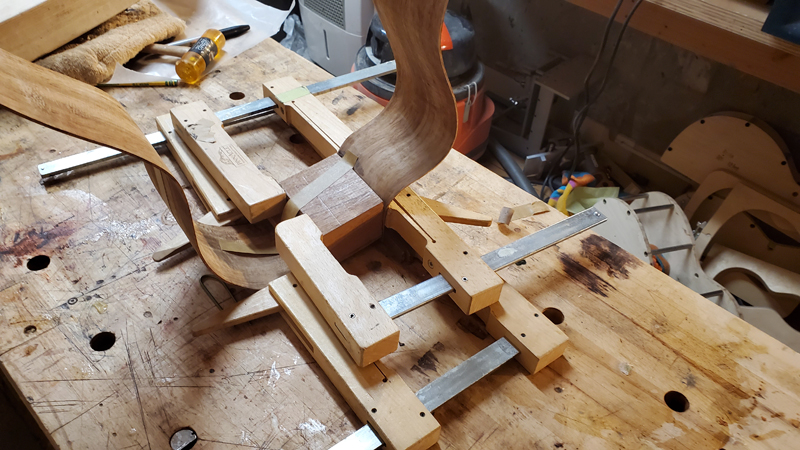
I also glued on the tail block, a cut and slight shaped piece of mahogany.
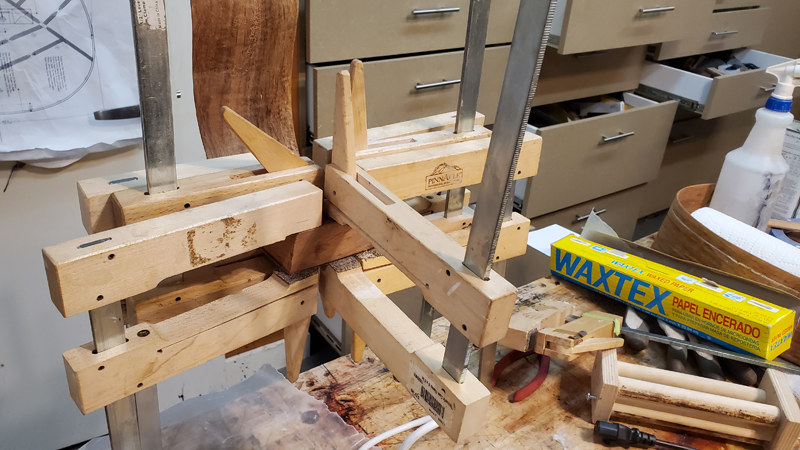
I radiused the back to 15' and the lower bout of the top to 30'. First the back. My side templates are really close to the correct shape for both sides. They are close enough that I cut the sides pretty close, leaving just enough extra to safely put the radius on the heel block without making the guitar too thin.
You can see in the first picture before doing any sanding the rims fit tightly on the radius dish
I do a combination of sanding and planing. I mark the top of the rims and the blocks with pencil. I sand for a bit, turn the sides over and plane where the pencil mark was sanded off. I repeat this unto the heel block is completely sanded\ planed to the correct radius.
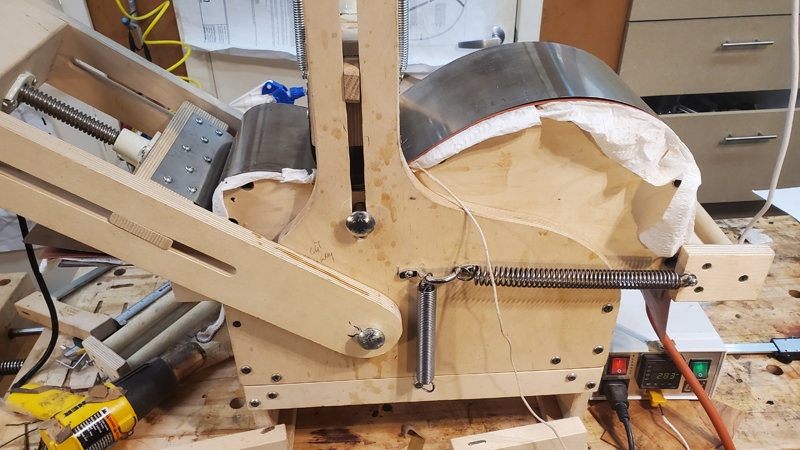

When the back was radiused I turned it over and put tape on the blocks. The tape is to stop me from sanding the back on the top's radius dish. This was a procedure I had to learn multiple times.
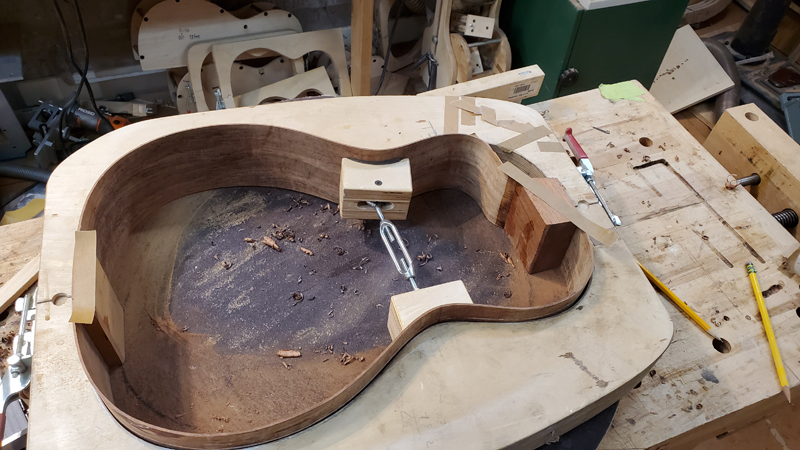
I leave the dish back side down in the 15' radius dish and radius the top firstI radius the lower bout to just past the middle of the waist with a 30' and then use a flat disk to clean up the upper bout.
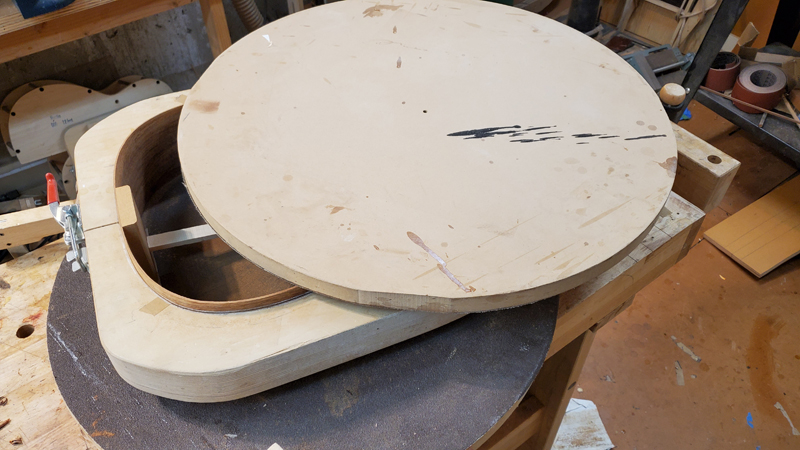
I went ahead and installed some kerfed linings on the back side. Pretty straight forward. I do remove a bit from each of the kerfed blocks around the cutaway so that they do not run into each other on the tight bends.
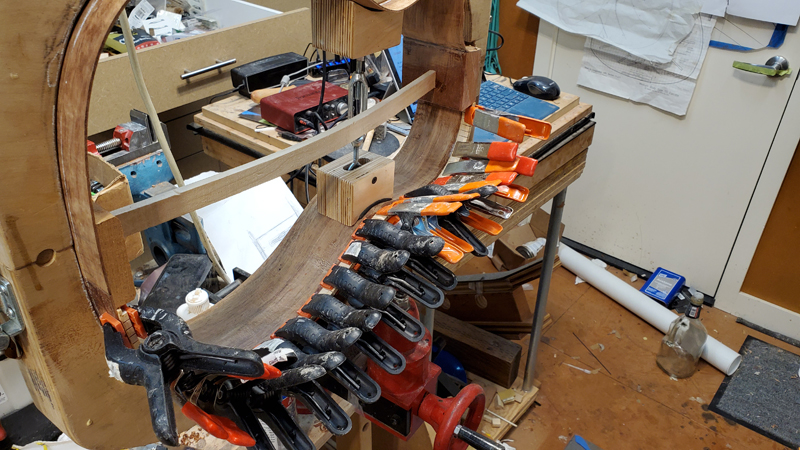
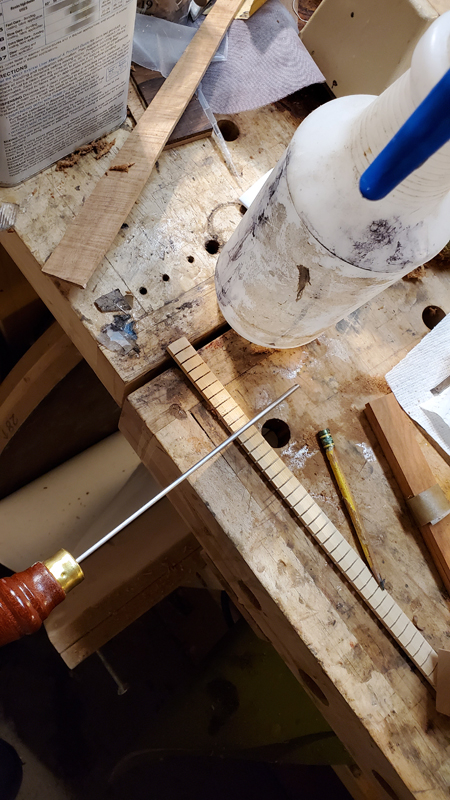
I took it back to the 15' dish and cleaned the kerfed linings up. I will do the top linings after I have a top and I can make sure the rims are profiled for the correct neck angle.
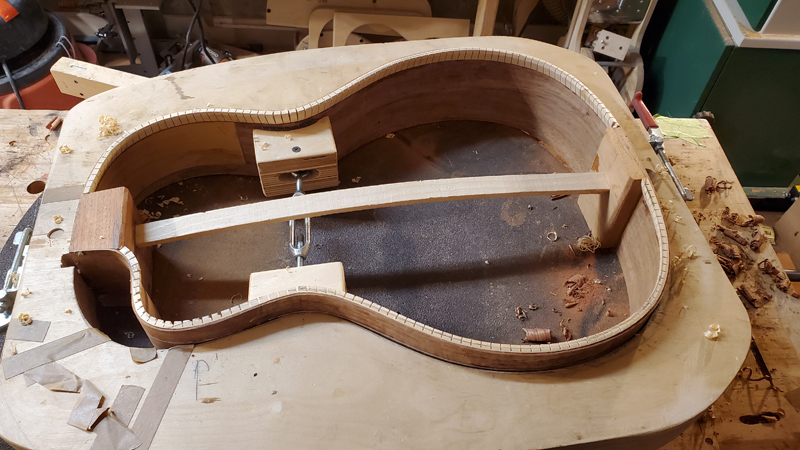
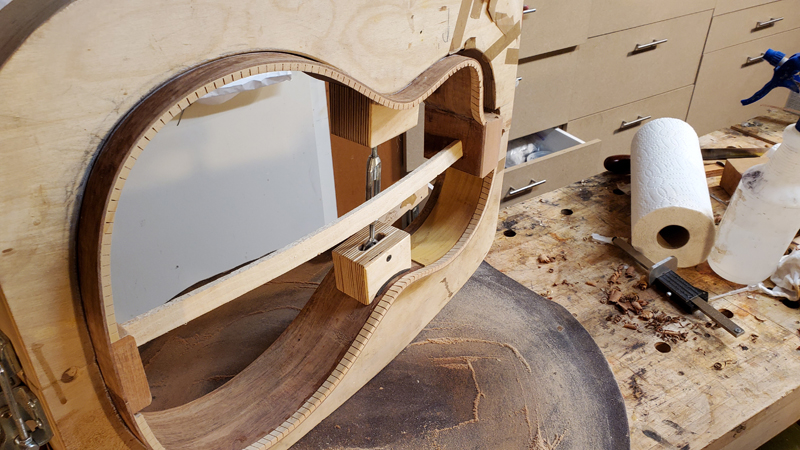
On to the top and back tomorrow.
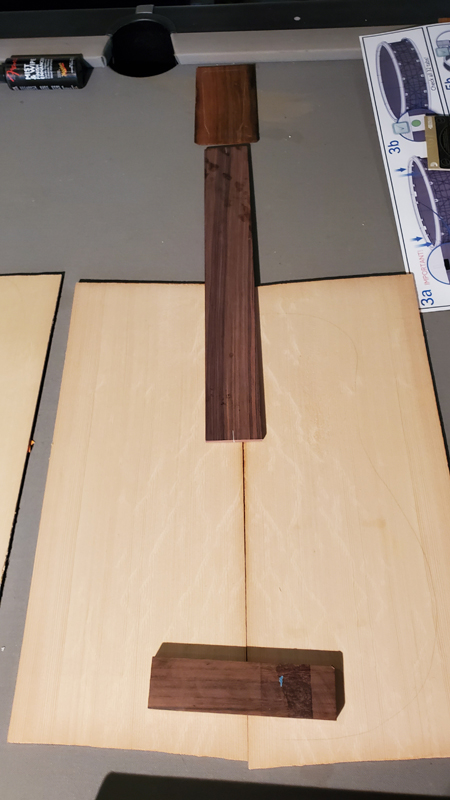
With some really figured and flamed Hawaiian Koa. I felt really guilty about the Koa as it was an auction item in the Seattle Lutherie Group auction that went way below cost.
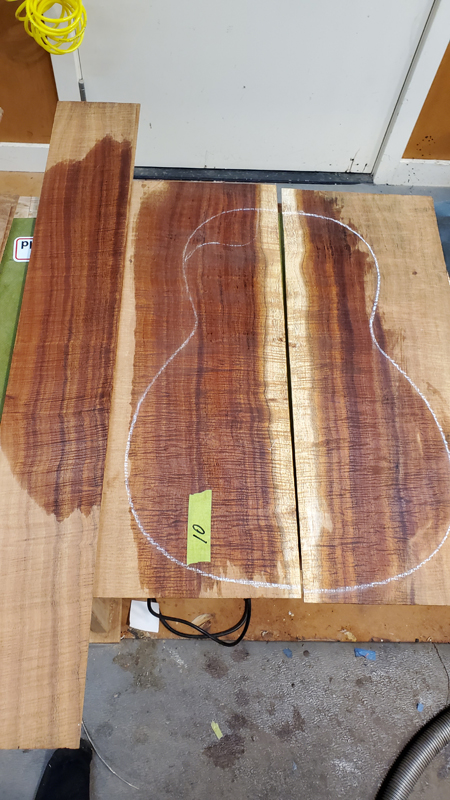
Unfortunately the sides were a bit too wild and their was a flaw in a dark figure line on a side that seperated when bending. Amazingly not on the venetian cutaway side but in the wide curve on the non cutaway side.
I did have a lot of Koa so I grabbed another set of sides that were a good color match. Still figured but not as much flame. Same back as the previous picture just different lighting.
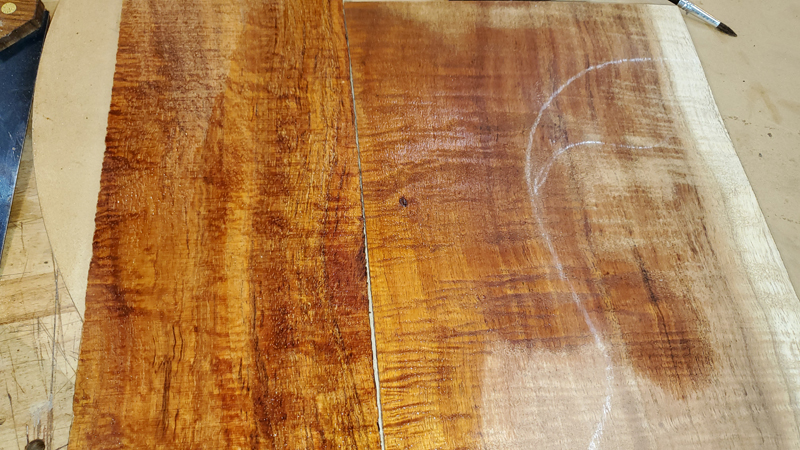
So the second set of sides I thinned to just under .080" and I scraped the inside of the cut away to .070" from just past the waist through the cutaway bends to the end.
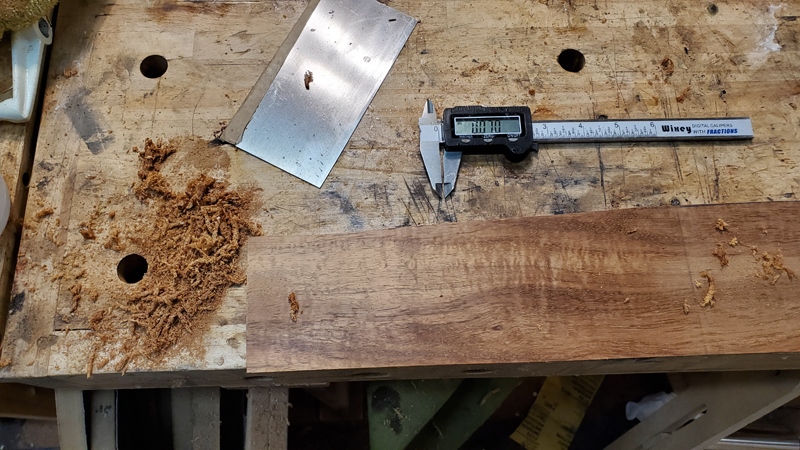
I sprayed them both with supersoft II, wrapped them and let them set under some weight (a big piece of ebony) overnight.
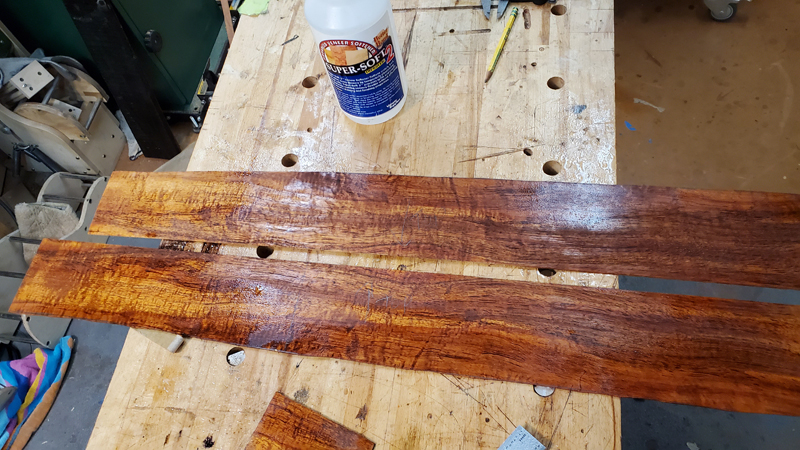
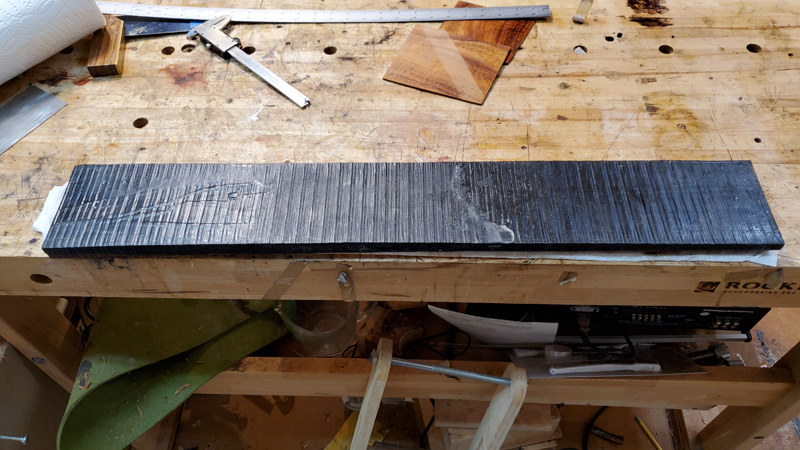
No problem with these bends in my fox style bender. While bending the cutaway I heat the bottom side of the cutaway area with a heat gun. I really took my time screwing in that last tight bend. I also used my stainless spring steel slats as my soft steel ones seem to ebonise koa. I learned that on my set of broken sides. It can be sanded out but I could also avoid it using stainless. I really need to take care removing the cutaway side as the spring steel can blow it up. (happened to a friend of mine once).
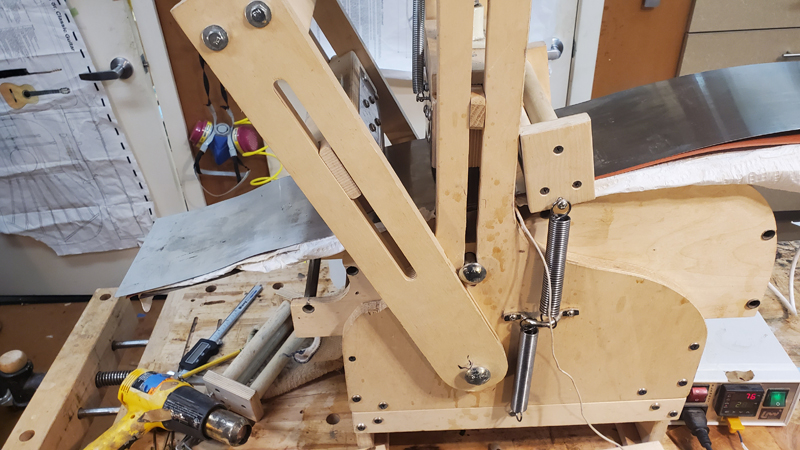
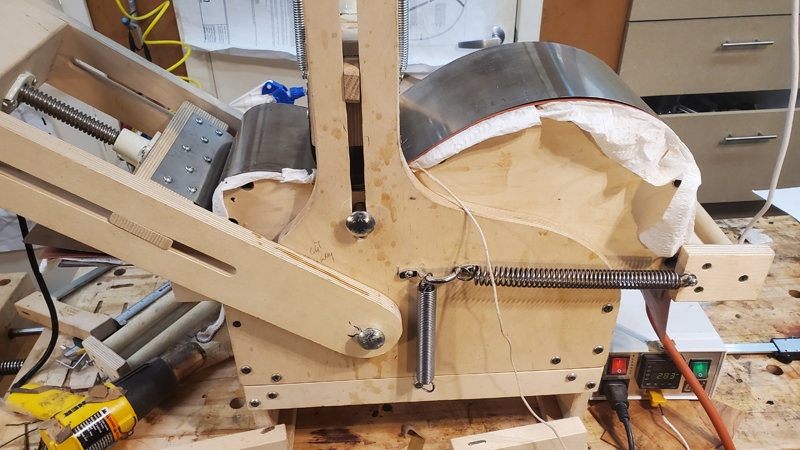
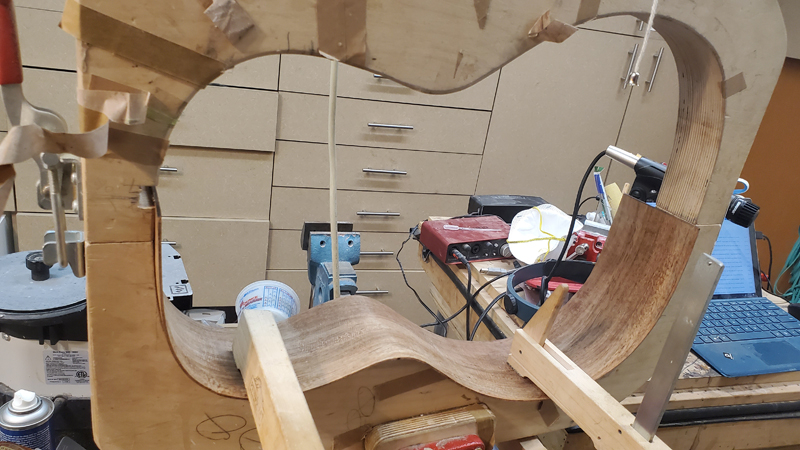
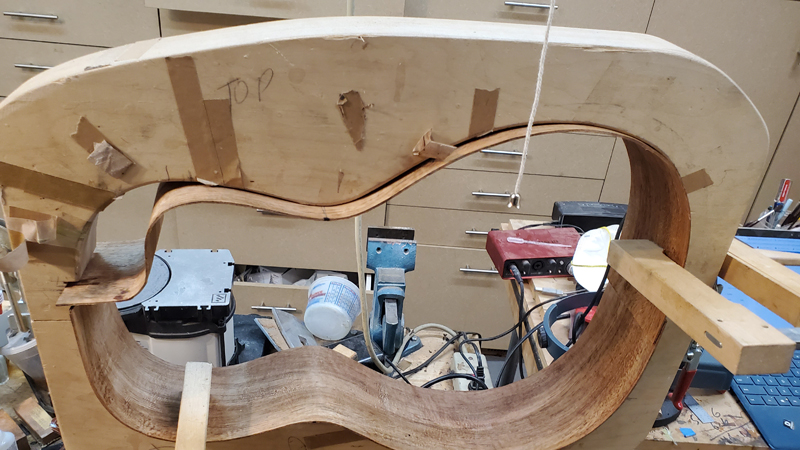
To get the heel block just right I put poster board under the guitar sides in the mold (not shown) and I traced out the pattern for the heel block. I glued that to chunk of mahogany and cut it out on the bandsaw.
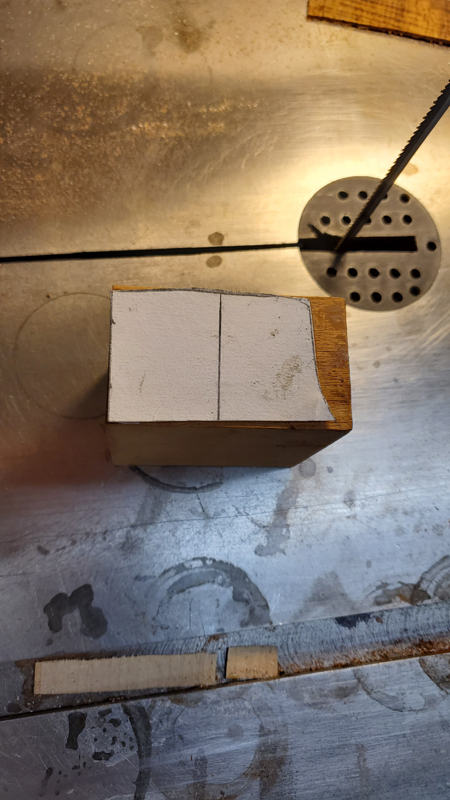
I used to try and glue in the heel block in one go. Now I glue first to the non cutaway side and then glue the cutaway side to the block. To assure alignment I set a couple of clamps while the sides are in the mold to hold it in position. I then remove the clamped block and side from the mold to make sure I can really clamp it.
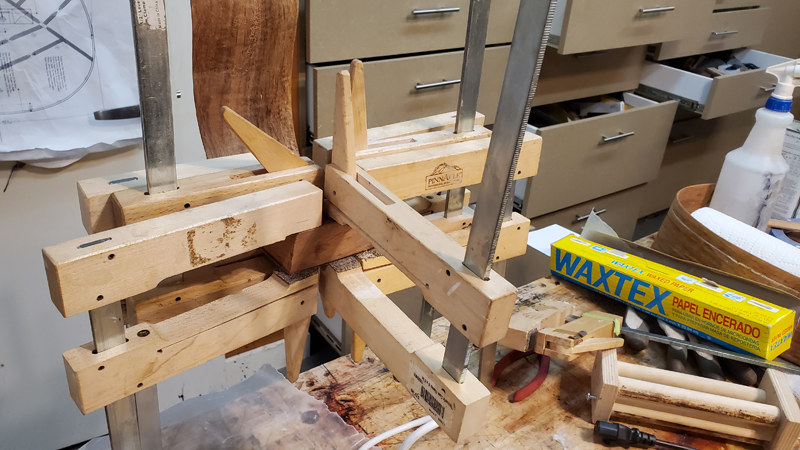
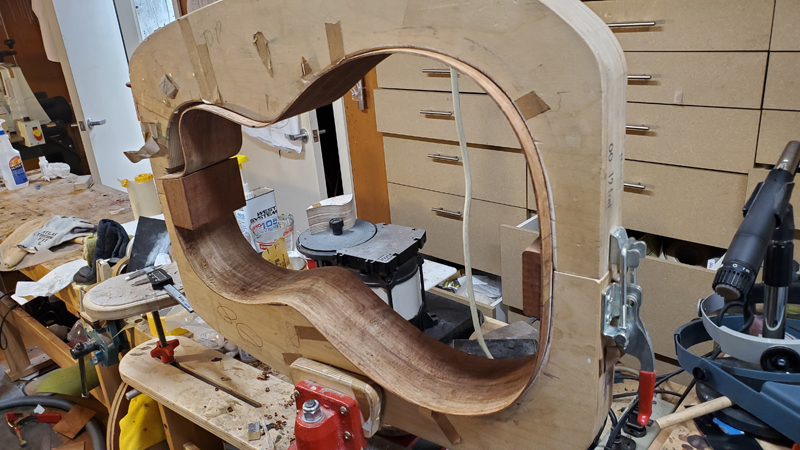
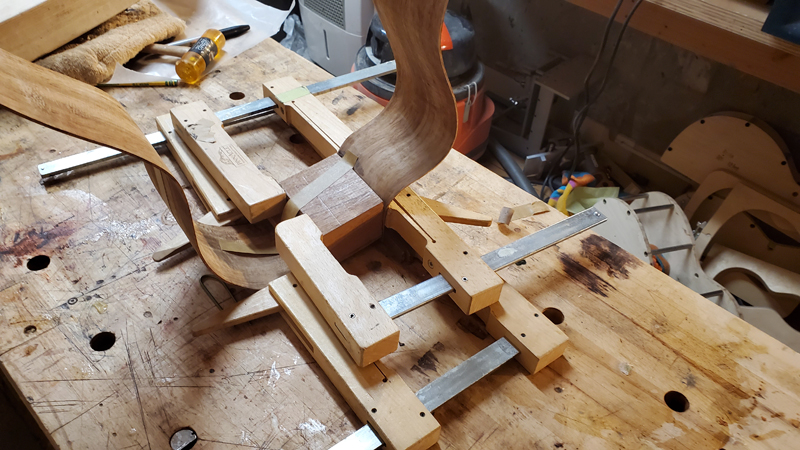
I also glued on the tail block, a cut and slight shaped piece of mahogany.
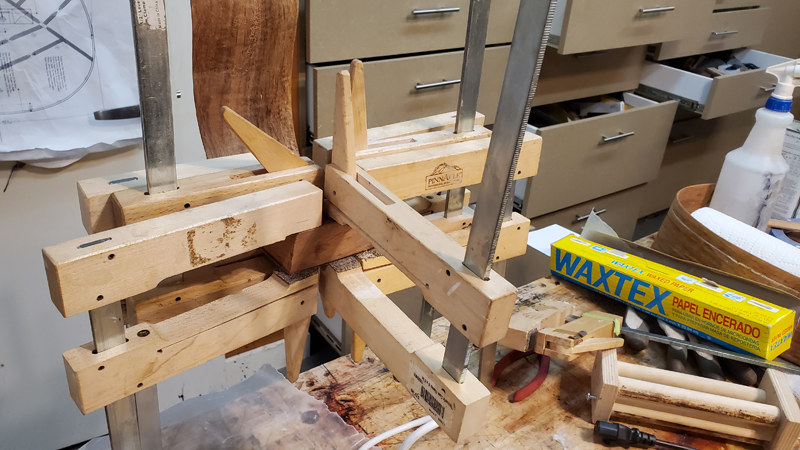
I radiused the back to 15' and the lower bout of the top to 30'. First the back. My side templates are really close to the correct shape for both sides. They are close enough that I cut the sides pretty close, leaving just enough extra to safely put the radius on the heel block without making the guitar too thin.
You can see in the first picture before doing any sanding the rims fit tightly on the radius dish
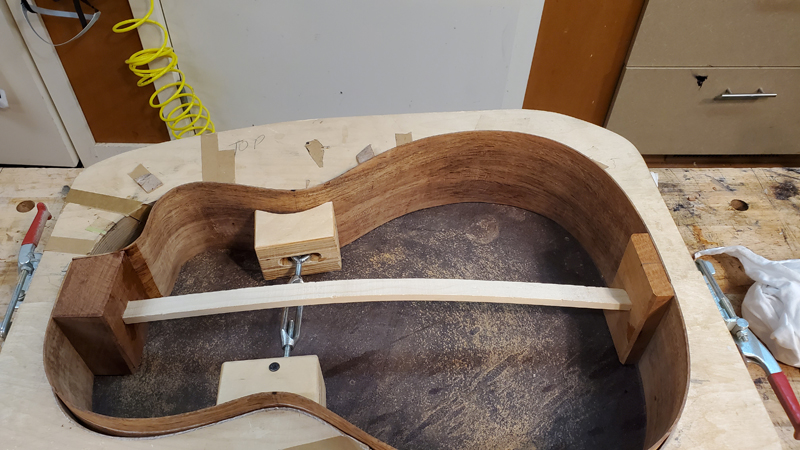
I do a combination of sanding and planing. I mark the top of the rims and the blocks with pencil. I sand for a bit, turn the sides over and plane where the pencil mark was sanded off. I repeat this unto the heel block is completely sanded\ planed to the correct radius.
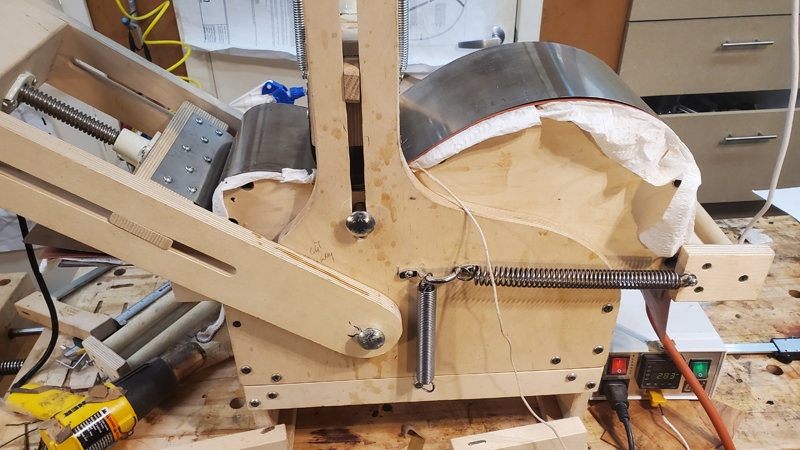

When the back was radiused I turned it over and put tape on the blocks. The tape is to stop me from sanding the back on the top's radius dish. This was a procedure I had to learn multiple times.
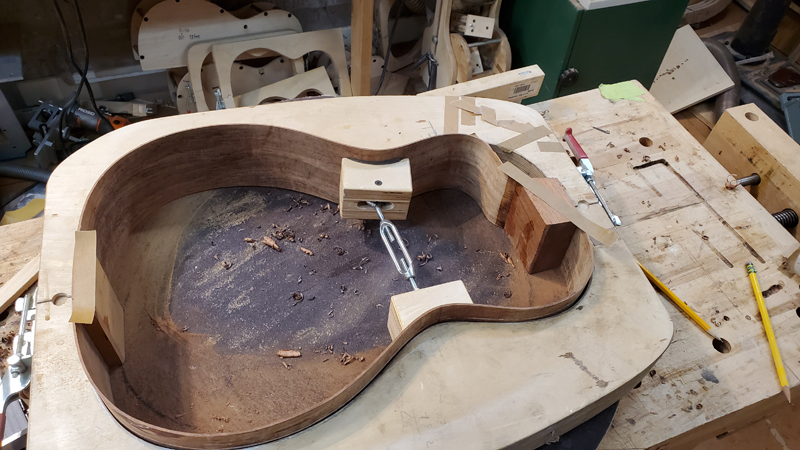
I leave the dish back side down in the 15' radius dish and radius the top firstI radius the lower bout to just past the middle of the waist with a 30' and then use a flat disk to clean up the upper bout.
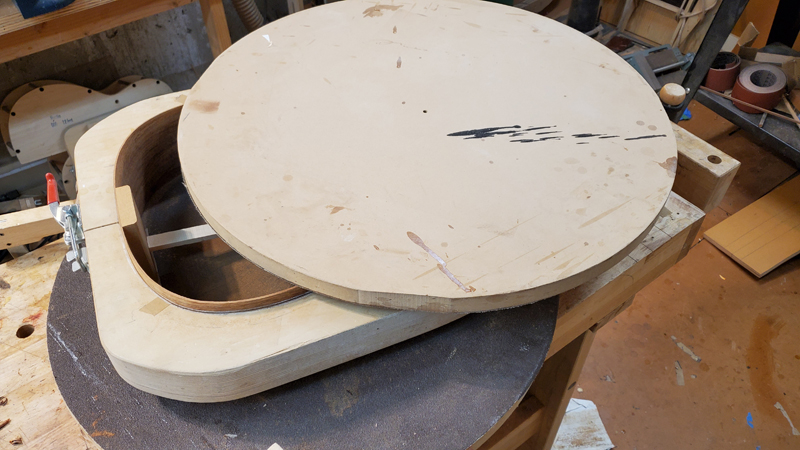
I went ahead and installed some kerfed linings on the back side. Pretty straight forward. I do remove a bit from each of the kerfed blocks around the cutaway so that they do not run into each other on the tight bends.
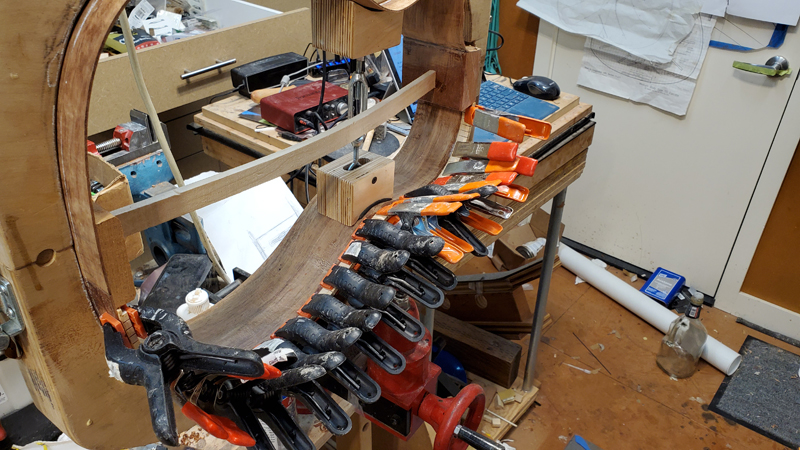
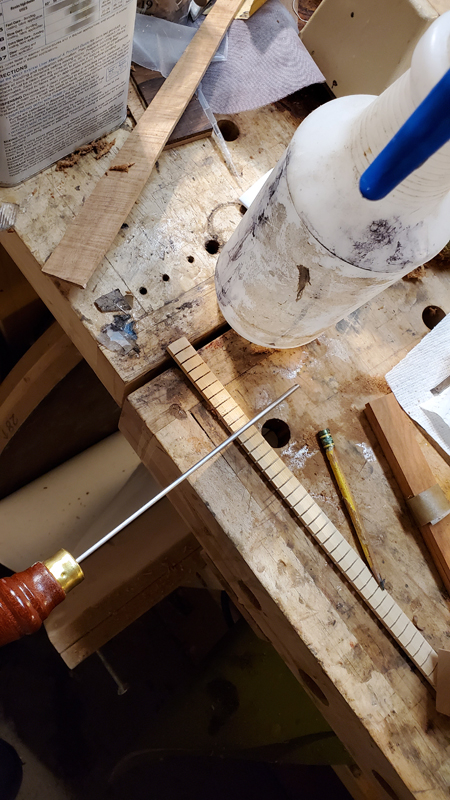
I took it back to the 15' dish and cleaned the kerfed linings up. I will do the top linings after I have a top and I can make sure the rims are profiled for the correct neck angle.
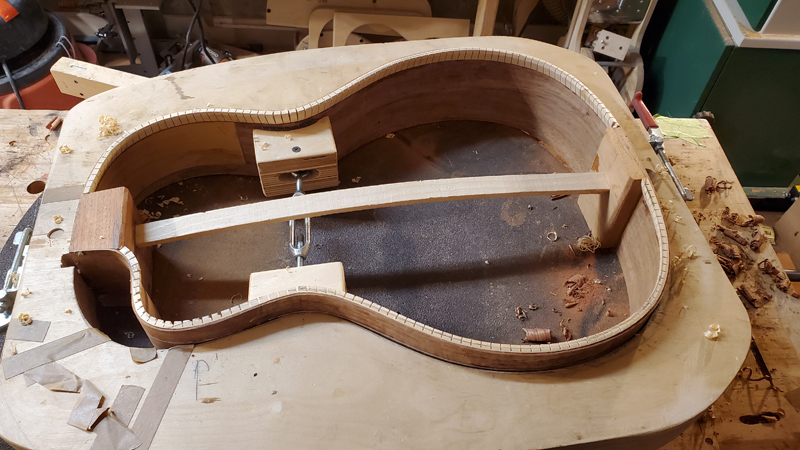
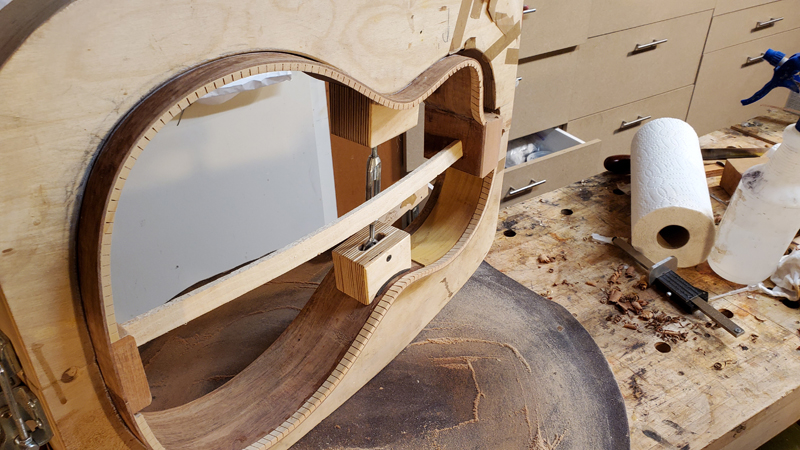
On to the top and back tomorrow.