Martin 00 cutaway with arm bevel #12 so close
Posted: Sun Sep 08, 2013 11:17 pm
I am starting a Western Red Cedar and Koa Martin sized 00. This guitar is for me so there is no stress and the option to take risks. Fort this project I will do my first cutaway and install an arm bevel using Kent Everett's method of building it in from the start. The guitar will also have a sound hole. The other thing I will be doing through this build is to measure and document the characteristics of the tone wood and using the techniques in the Trevor Gore with Gerard Gilet Contemporary Acoustic Guitar Design and Build books.
This Koa is pretty figured. The back and sides should be wild.
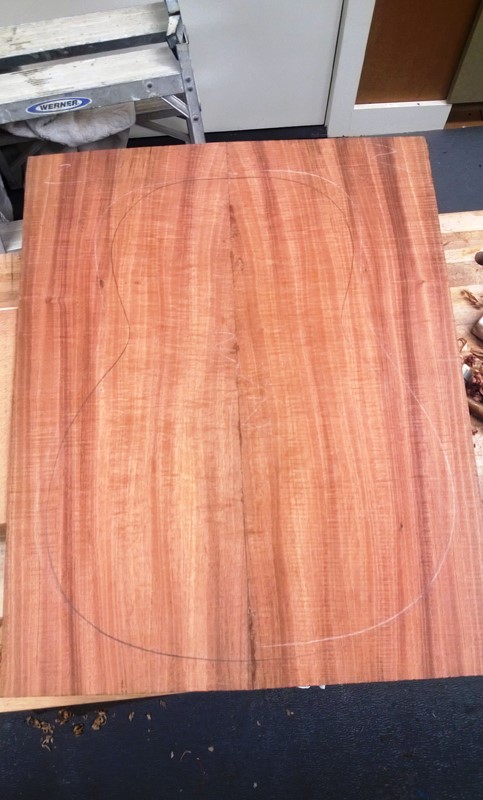
I found a couple of scrap of some sort of wood at the wood working store to use for the head stock and the rosette and other area.
I think the small plank that I resawed was amboyna burl. These faces do not look like it but the side figure did. The color looks right.
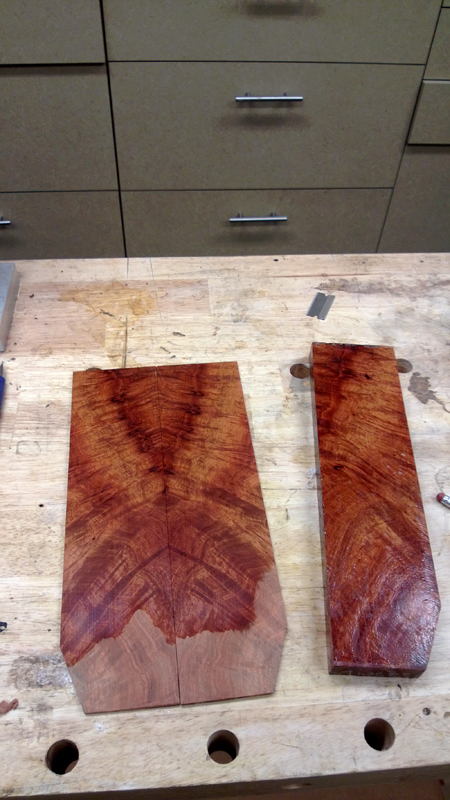
I had another small piece of burl with sap wood that I also resawed and joined for a rosette. I had three choices for rosettes, so I cut them all out the same
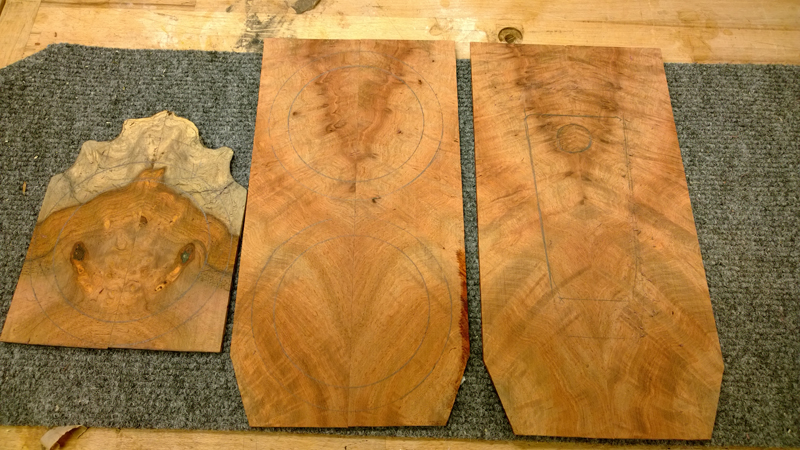
I plan for this rosette to have either bwb or all b bbb purfling inside and out.
When cutting out the rosette I learned the technique, maybe from Kevin of using a router bit the right diameter for the purfling I want to use. The result is a matching rosette and channel cut in the guitar the correct size for the rosette and the purfling.
First cut a channel where you want the inside or outside purfling on the guitar, leave the router set up exactly and cut the same channel on the rosette stock. I do not cut through the rosette rather I make the rosette the same thickness as the channel is deep. I then cut a channel on the other side on the guitar and again leave the router set up to make the same cut on the rosette stock.
I changed bits on the router and hogged out the center of the channel. I then run the rosettes through the thickness sander back side being sanded till the rosettes drop out (learned this from Rick Davis).
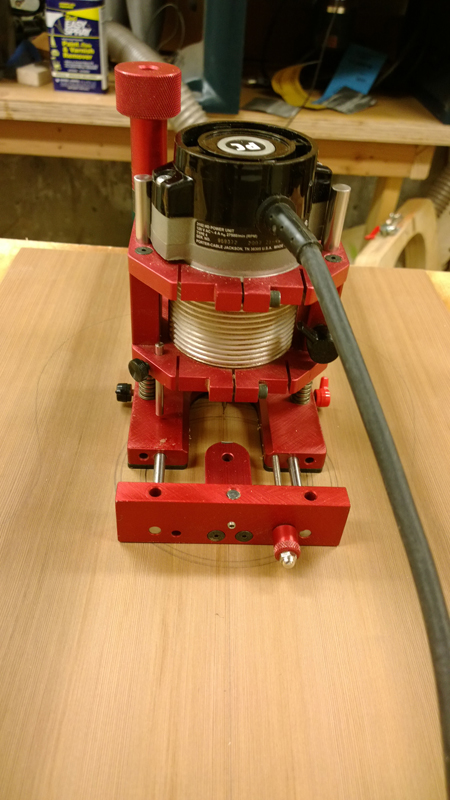
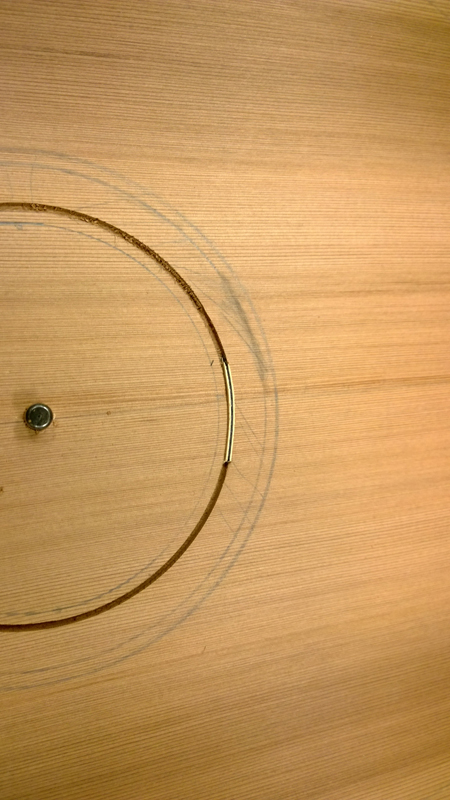
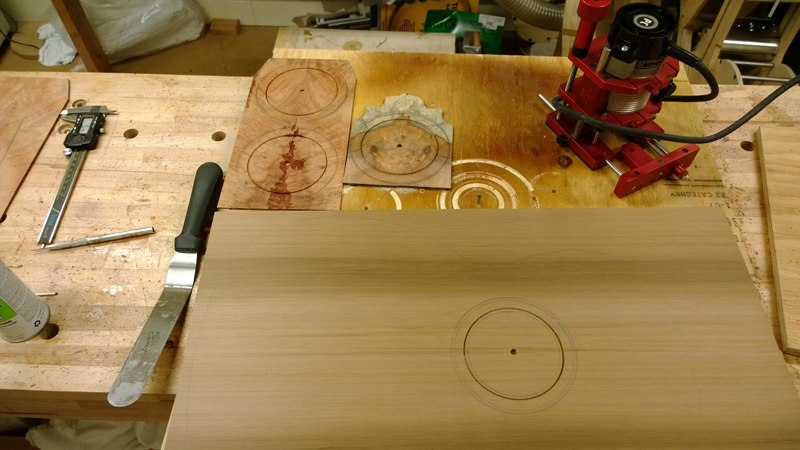
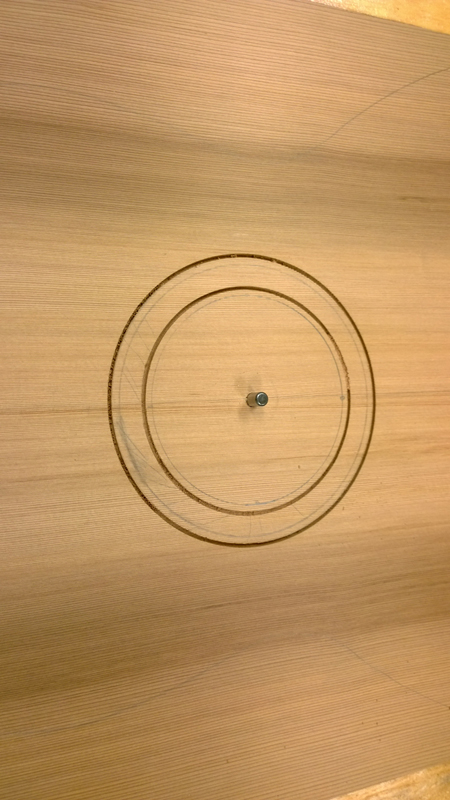
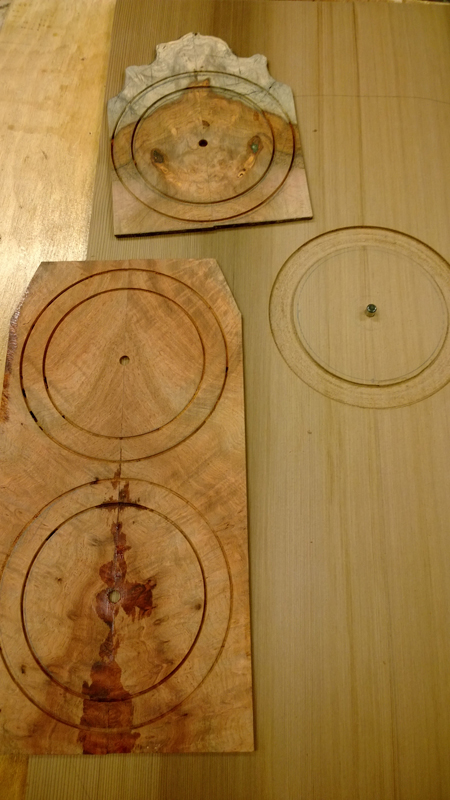
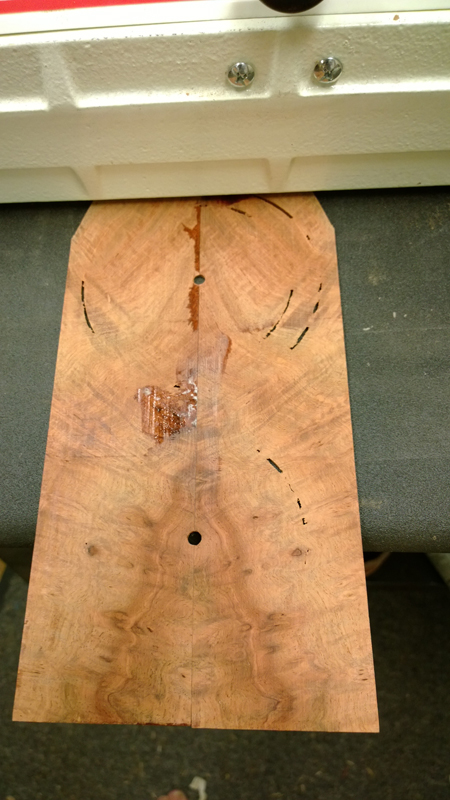
I went with the all black purfling.
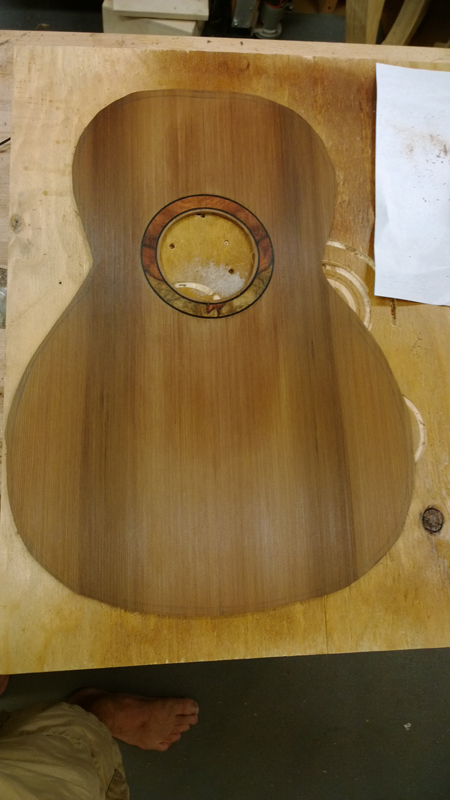
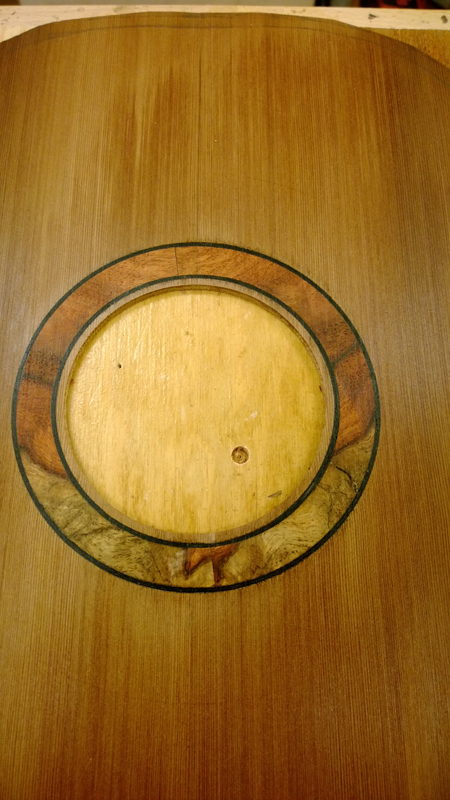
This Koa is pretty figured. The back and sides should be wild.
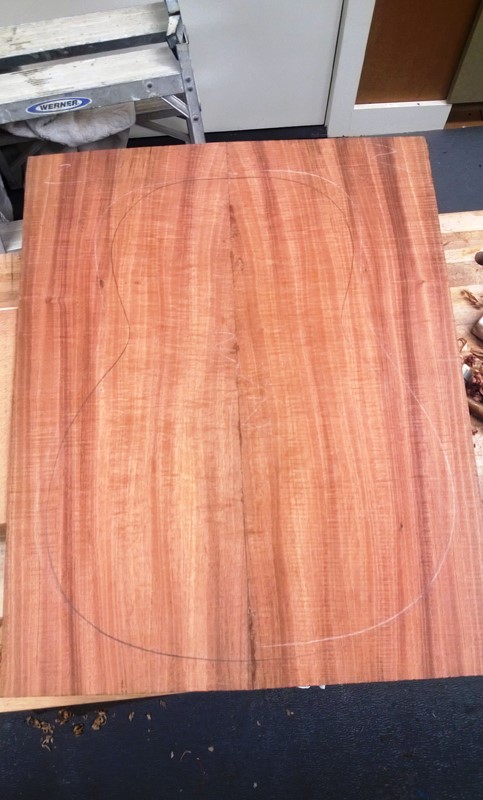
I found a couple of scrap of some sort of wood at the wood working store to use for the head stock and the rosette and other area.
I think the small plank that I resawed was amboyna burl. These faces do not look like it but the side figure did. The color looks right.
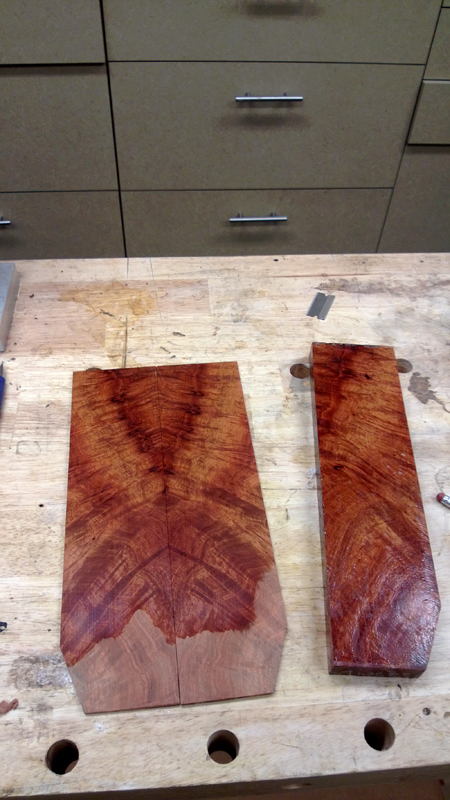
I had another small piece of burl with sap wood that I also resawed and joined for a rosette. I had three choices for rosettes, so I cut them all out the same
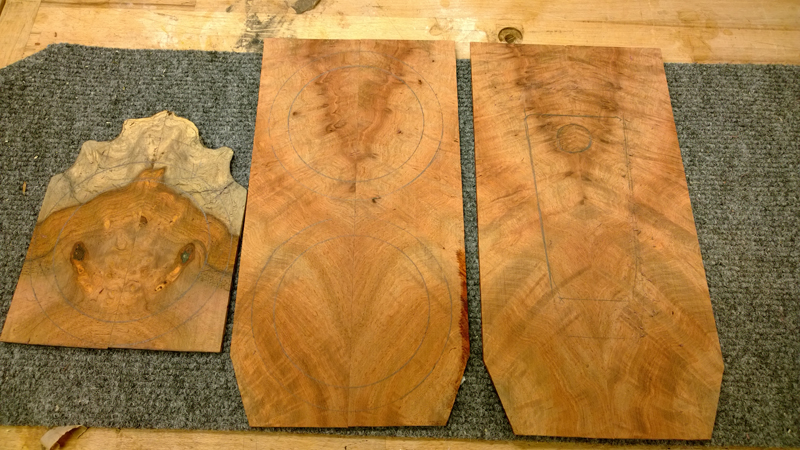
I plan for this rosette to have either bwb or all b bbb purfling inside and out.
When cutting out the rosette I learned the technique, maybe from Kevin of using a router bit the right diameter for the purfling I want to use. The result is a matching rosette and channel cut in the guitar the correct size for the rosette and the purfling.
First cut a channel where you want the inside or outside purfling on the guitar, leave the router set up exactly and cut the same channel on the rosette stock. I do not cut through the rosette rather I make the rosette the same thickness as the channel is deep. I then cut a channel on the other side on the guitar and again leave the router set up to make the same cut on the rosette stock.
I changed bits on the router and hogged out the center of the channel. I then run the rosettes through the thickness sander back side being sanded till the rosettes drop out (learned this from Rick Davis).
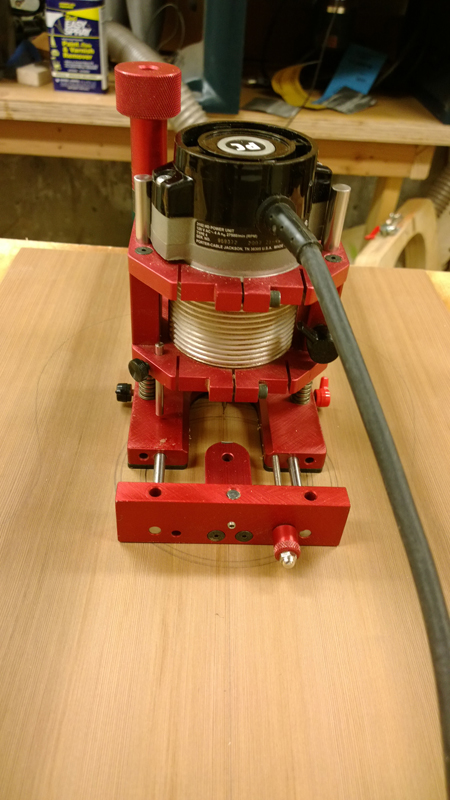
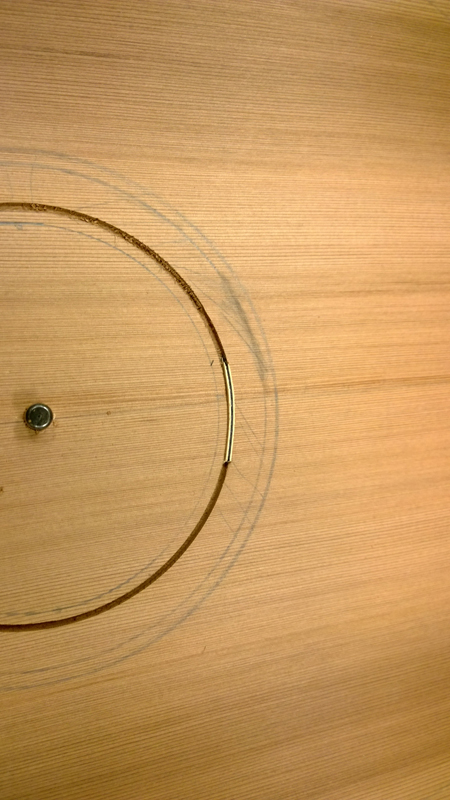
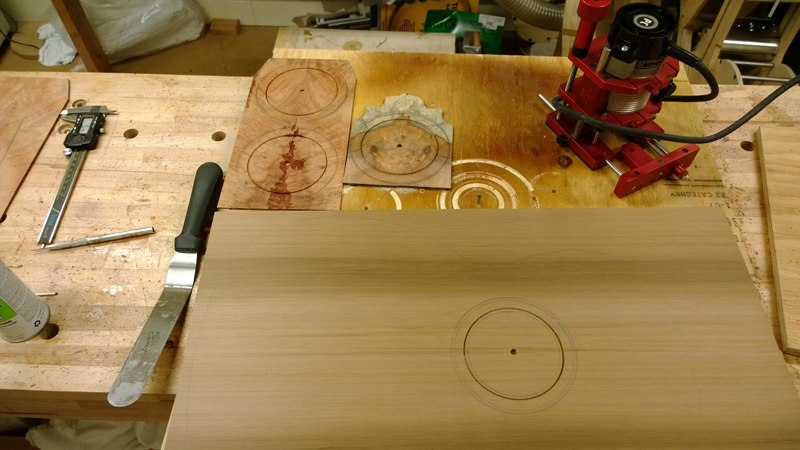
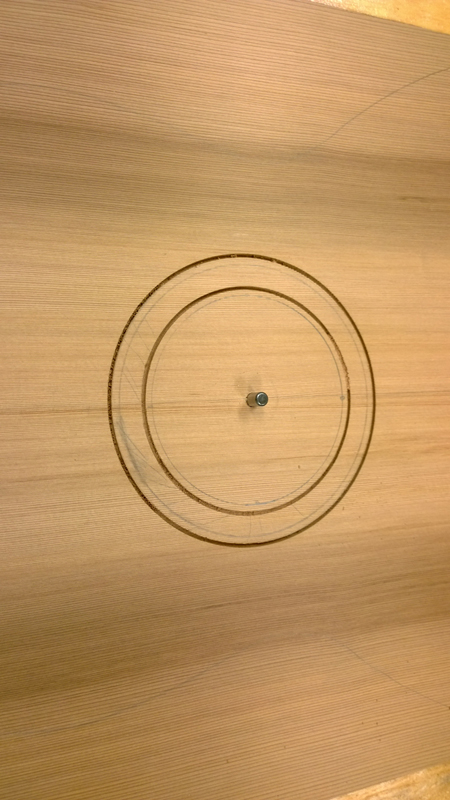
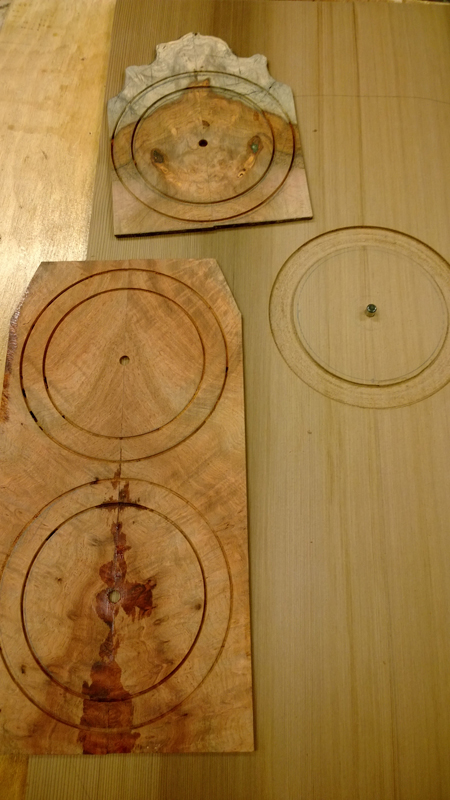
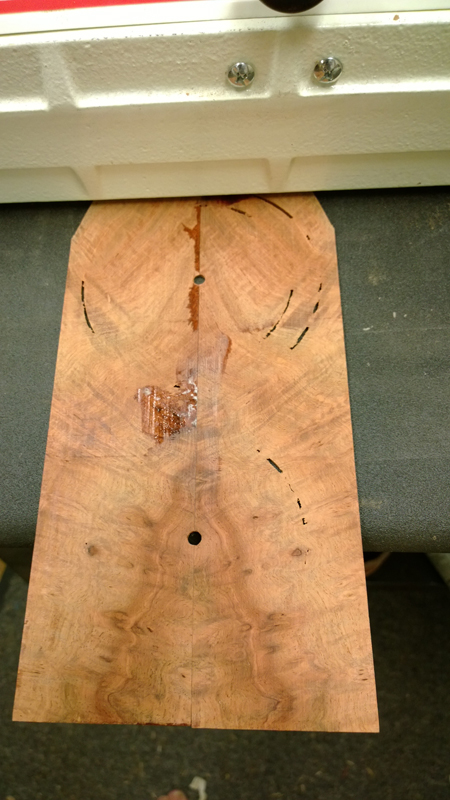
I went with the all black purfling.
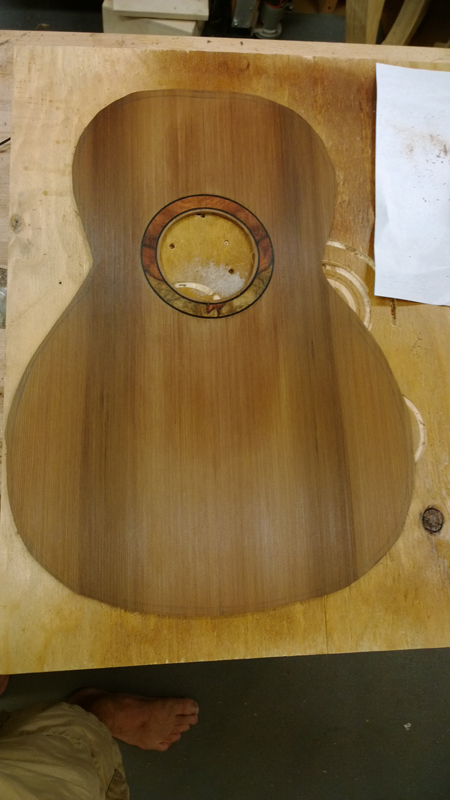
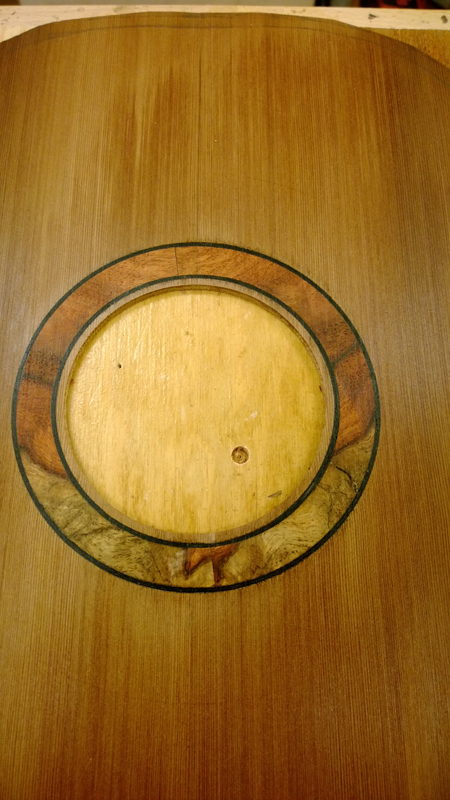