Classical guitar Finished FP on body.
Posted: Sun Apr 07, 2013 11:10 pm
While I was joining the plates and installing the rosette for my Martin 00 I also joined the plates and put a rosette into an Adi top and jointed Afreica Rosewood back. I was going to build the two at the same time, but no I am not that good, so after many months I pulled the wood down this weekend and started the classical guitar for real.
In between I had a two day course with Jeffery Elliott about voicing a classical guitar top. It was a watch only course, but I learned a ton. Luckily I took good noted and pictures so I can put it into place today.
One of the interesting ideas I saw, from him is that he indexed all of the components that mattered up front. He has index holes in his solera for the saddle location, matching template to index the bridge, Index holes near the heel block and a complete story board with matching index holes for the saddle, rosette center 12 fret, nut ... What I like is that he actually places his bridge before he even makes the body.
Jeff made his story board, but on the Waldren Instrument site, I saw that one can buy a whole package of neck templates for any instrument. This package includes a full length story board.
As you can see in the pictures below. I located the proper saddle location on the story board and drilled index holes in the story board, the bridge and my solera. I used the story board to drill index holes in the top as well (second try, need to remember inside and outside.) I will also drill matching index holes in a neck template to use on the neck and fret board and a bridge template that I have to mark the saddle location. With all of these templates I should be able to achieve some constancy. But I have also already set the location of the top, saddle, and the neck on the top. I made the rough top braces before Jeff Elliott's class. The neck is an LMI neck I had for a couple of years.

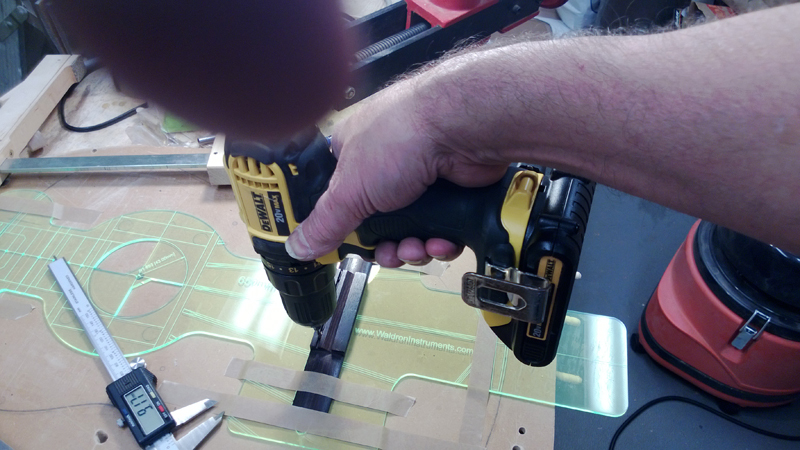
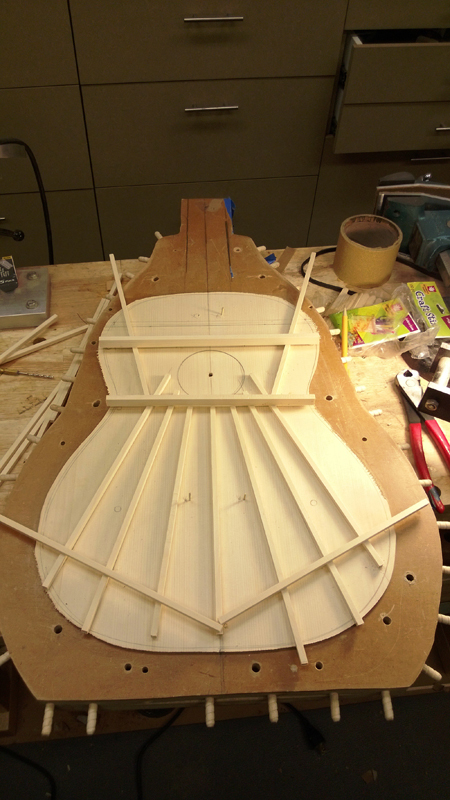
To finish the evening I thicknessed the back and thicknessed and profiled the sides. I could have probably bent the sides but I turned in for the evening.
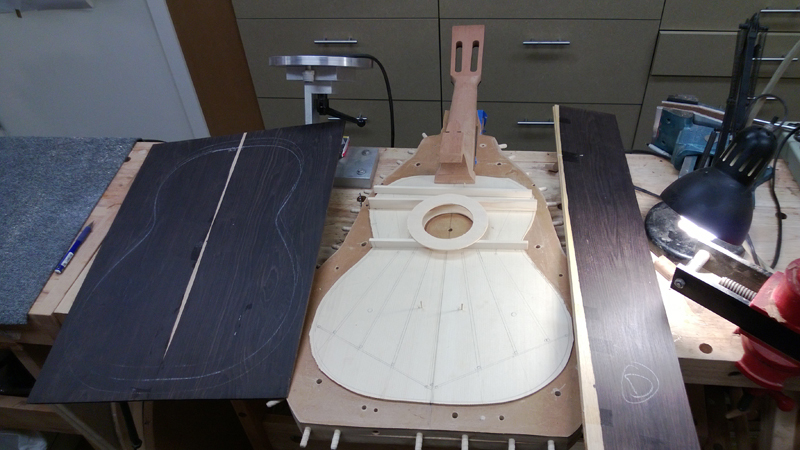
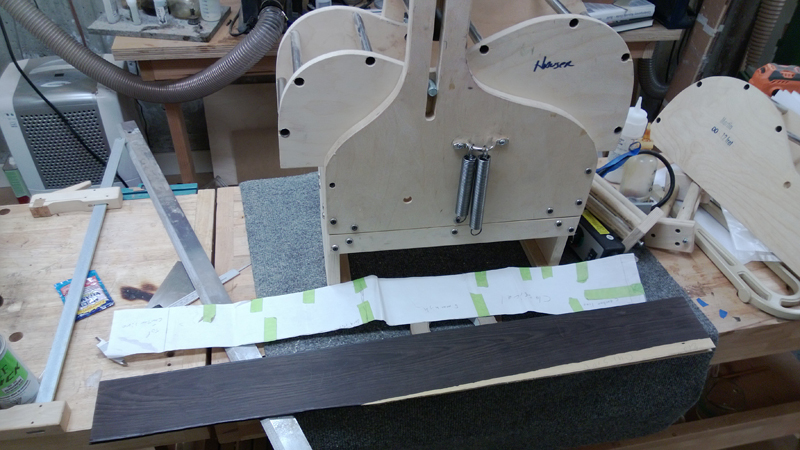
In between I had a two day course with Jeffery Elliott about voicing a classical guitar top. It was a watch only course, but I learned a ton. Luckily I took good noted and pictures so I can put it into place today.
One of the interesting ideas I saw, from him is that he indexed all of the components that mattered up front. He has index holes in his solera for the saddle location, matching template to index the bridge, Index holes near the heel block and a complete story board with matching index holes for the saddle, rosette center 12 fret, nut ... What I like is that he actually places his bridge before he even makes the body.
Jeff made his story board, but on the Waldren Instrument site, I saw that one can buy a whole package of neck templates for any instrument. This package includes a full length story board.
As you can see in the pictures below. I located the proper saddle location on the story board and drilled index holes in the story board, the bridge and my solera. I used the story board to drill index holes in the top as well (second try, need to remember inside and outside.) I will also drill matching index holes in a neck template to use on the neck and fret board and a bridge template that I have to mark the saddle location. With all of these templates I should be able to achieve some constancy. But I have also already set the location of the top, saddle, and the neck on the top. I made the rough top braces before Jeff Elliott's class. The neck is an LMI neck I had for a couple of years.

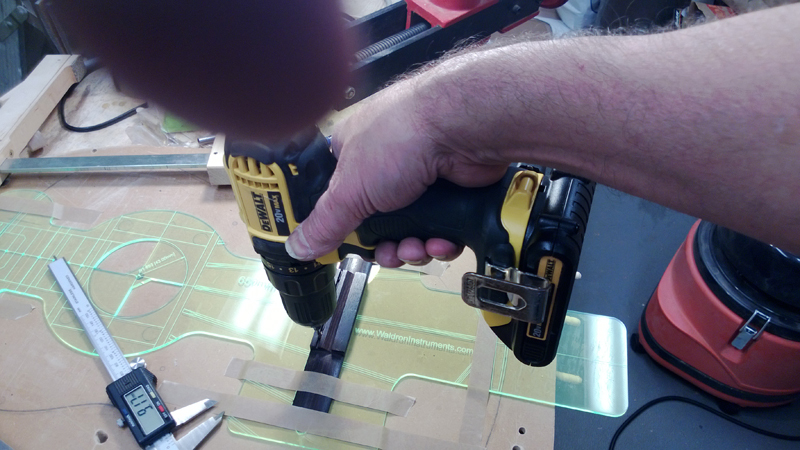
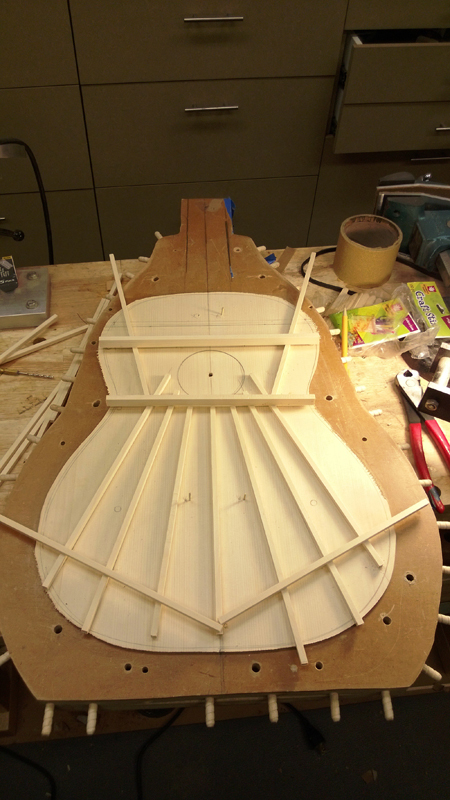
To finish the evening I thicknessed the back and thicknessed and profiled the sides. I could have probably bent the sides but I turned in for the evening.
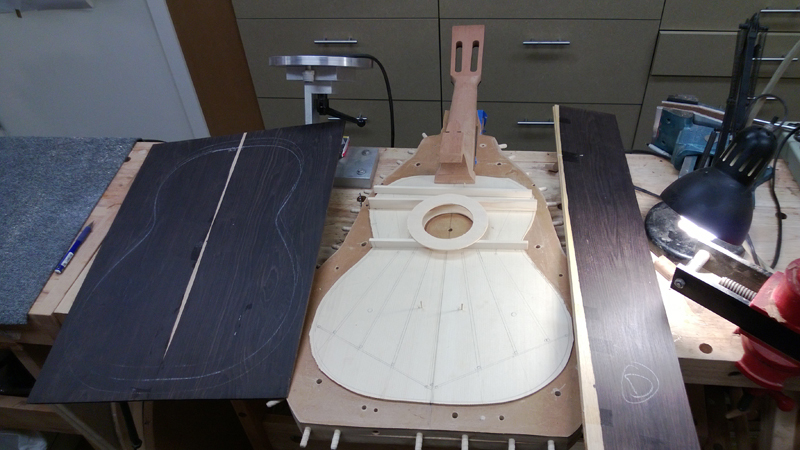
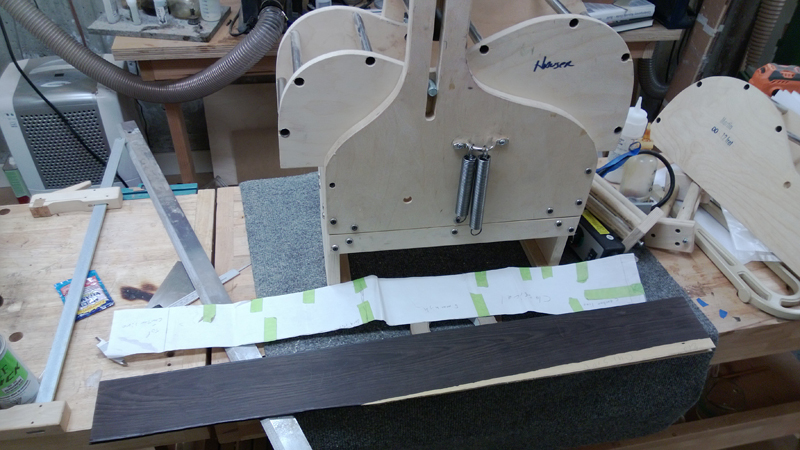