Re: Third Flamenco Guitar
Posted: Tue Feb 04, 2020 8:04 pm
The first step going forward is to glue the endblock to the rims. I am sorry I do not have pictures, but I use my guitar template to draw the profile or the guitar onto the tail block, I then planed off close to the lines and used sand paper right in the rims to finish the profile. When finished the endblock fit perfectly. I also measured and cut the sides so that they would fit in the neck.
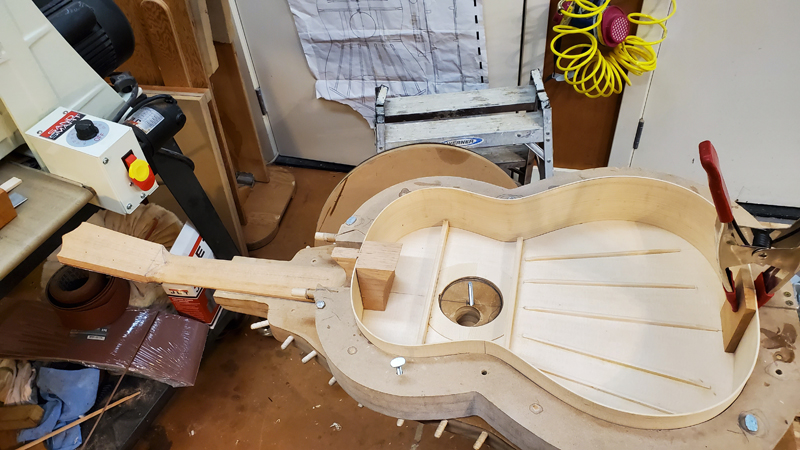
Because I am building on a solera and I will use individual tentallones to glue the sides to the top I have a couple of options for the end block. One way is to position and glue it on to the top making sure it is square to the top. As the neck is also glued to the top the rims can be installed on to the top assembly that includes the neck and the tail block. I did not do that this time rather I glued the sides to the end block. I started the glue up in the mold so that I could make sure everything was square. With the back side tightly clamped I removed the assembly from the mold and clamped the top side.
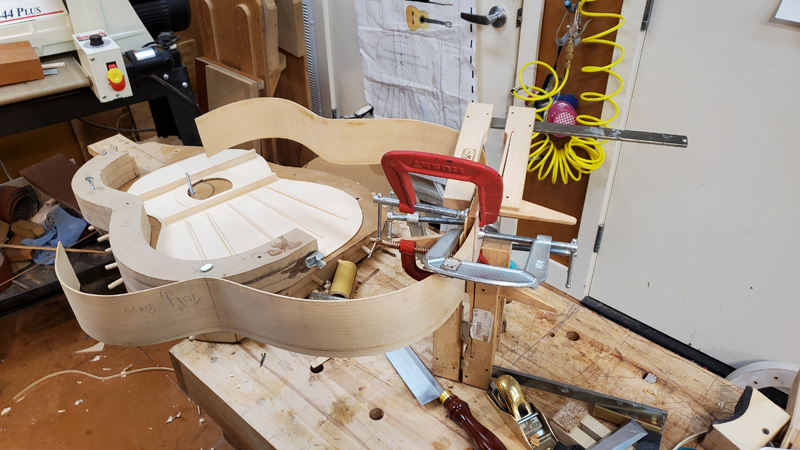
I make everything close to the right size, getting away from rough cut and sand and plane to shape.
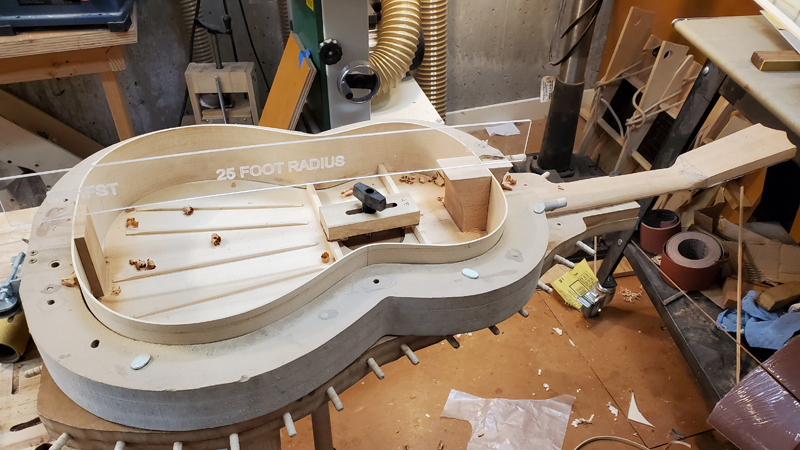
The neck step is to glue the neck to the top. Note if I were using linings instead of tentallones, I would glue the neck to the rims and install the linings. The top would be glued to the rims and neck and the same time. But building in this traditional style I need to glue the neck to the top making sure I am square to the center line everywhere. My solera has a neck angle built in. This operation is better with the top and the neck flat, so I have a seperate board to do this operation.

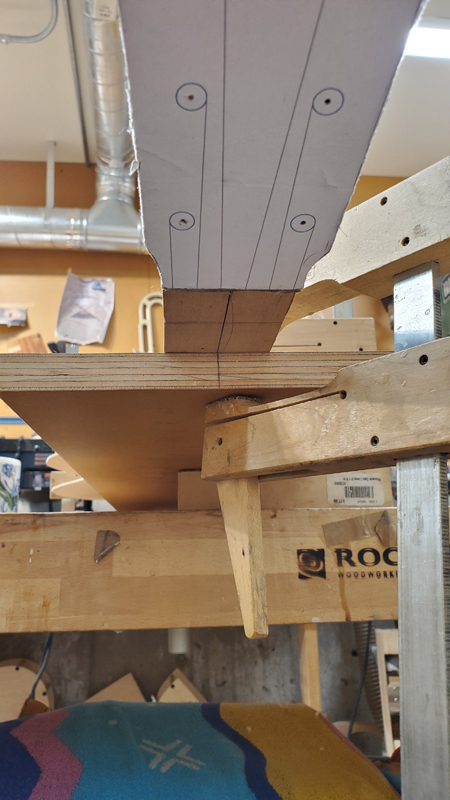
The neck and top are in line. I can not wait until the fretboard is glued on and I do not have to look at that router mishap.
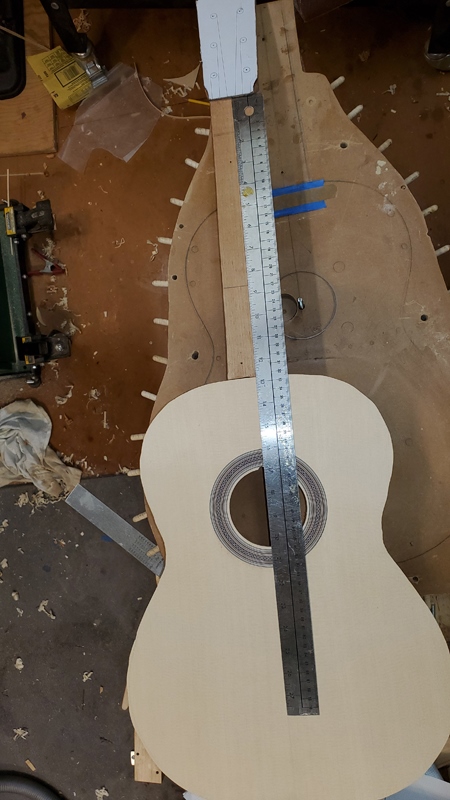
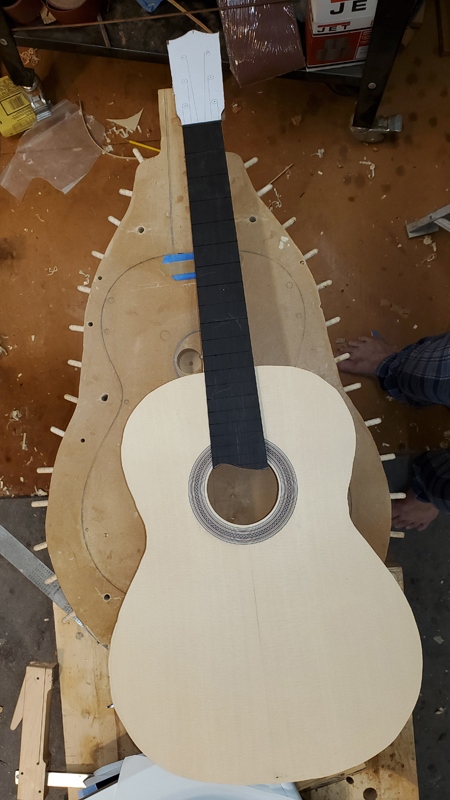
I like to install the end graph at this time. I just find it easier and safer with the top and back off. I can finally see my binding scheme of mahogany and black purfling lines.
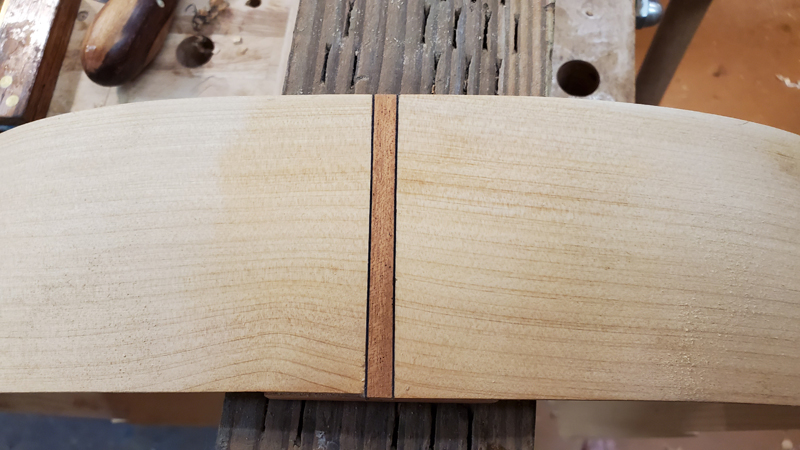
Next operation is to attach the rims to the top starting with the end block. I used a spatula to put glue on the block and I clamped it down.
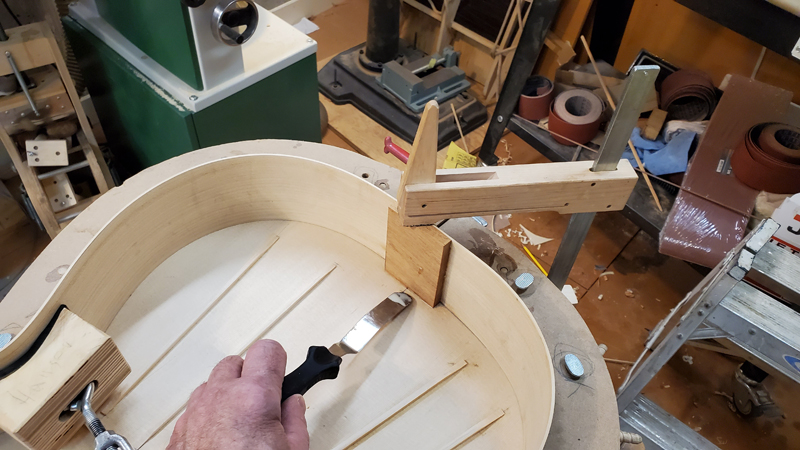
No one sells tentallones in the states so I had to make my own. I saw a youtube video by Pablo Requena https://www.youtube.com/watch?v=6KupYrzeVag&t=549s for a simple jig to cut a length of wood at an angle for the tentallones. He likes his blocks to be 10 mm by 14 which requires a 30° degree angle. For his jig he glued a couple of blocks of 3/4" plywood together and cut the face at 20 degrees. On to that face he glued a the square side of an off cut to the 30° face making a channel to guide a length of 10 mm by 30 stock into a bandsaw blade. A picture makes all of those words go away
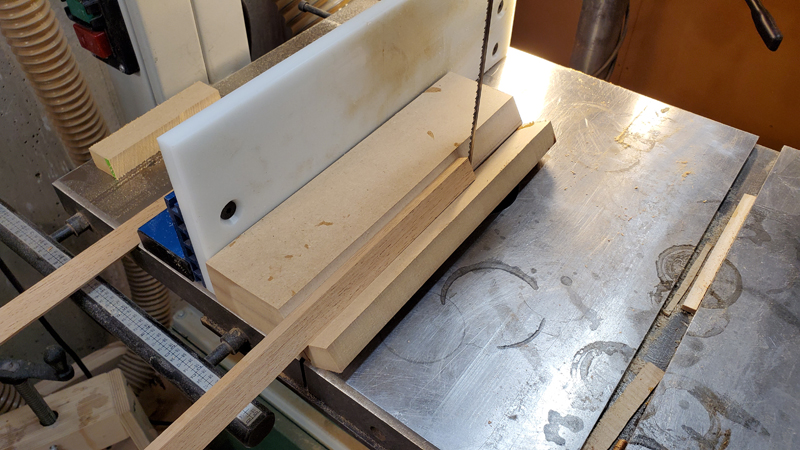
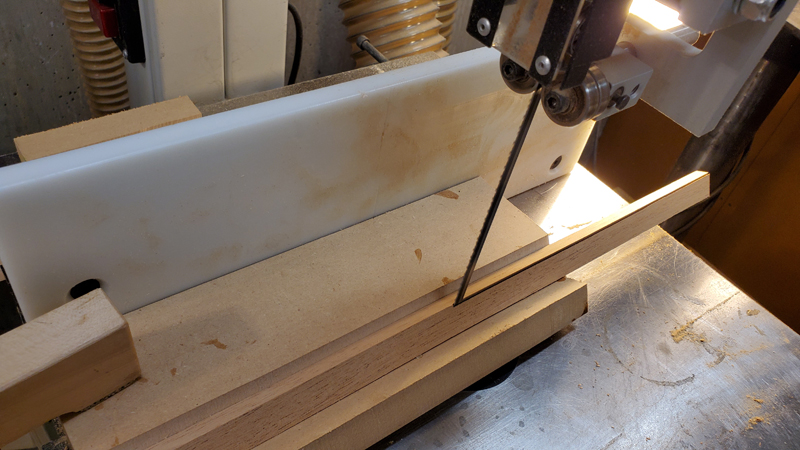
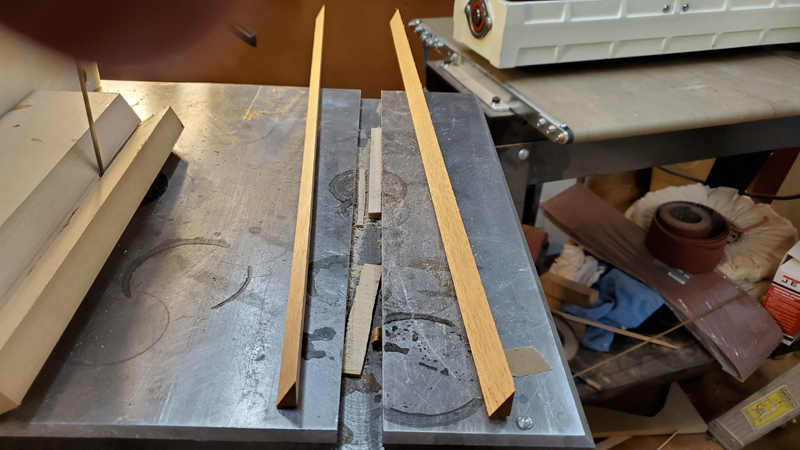
Then I just set a fence and had fed the stock to finish the tentallones.
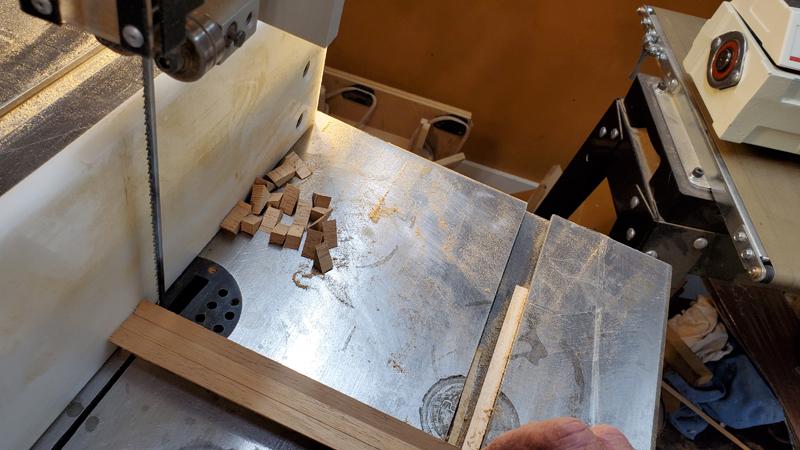
I used original titebond to glue these in place. I only need to hold them a moment and they seem to stick. On my first flamenco I used hot hide glue. I set the upper bout rather close for structural reasons. I space the lower bout to loosen the top a bit. I want the top to be able to drain its energy to get the flamenco sound. On a classical guitar I do just the opposite using solid lining to keep the sound in the top. This is not the most exciting operation building a guitar. I had spotify play a bunch of Paco De Lucia songs.
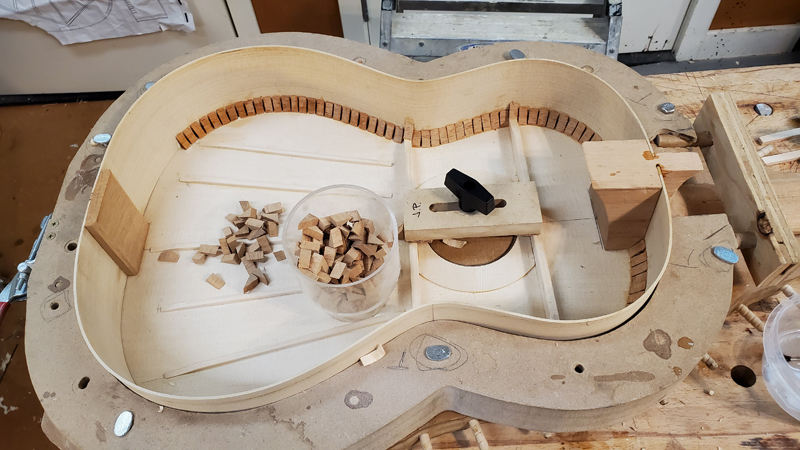
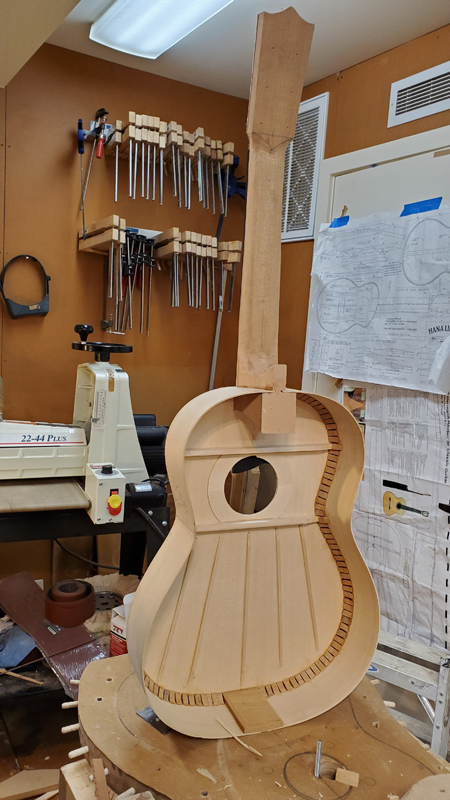
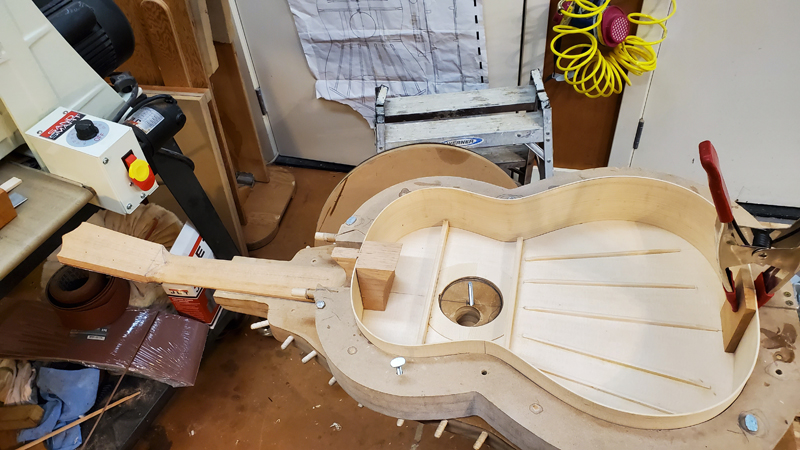
Because I am building on a solera and I will use individual tentallones to glue the sides to the top I have a couple of options for the end block. One way is to position and glue it on to the top making sure it is square to the top. As the neck is also glued to the top the rims can be installed on to the top assembly that includes the neck and the tail block. I did not do that this time rather I glued the sides to the end block. I started the glue up in the mold so that I could make sure everything was square. With the back side tightly clamped I removed the assembly from the mold and clamped the top side.
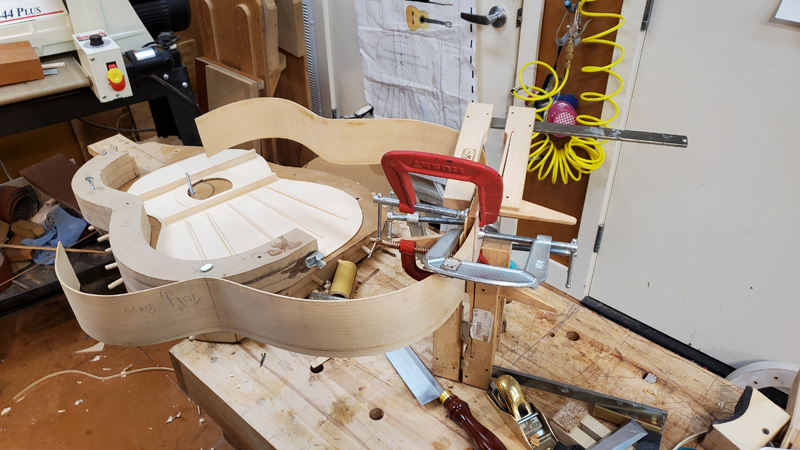
I make everything close to the right size, getting away from rough cut and sand and plane to shape.
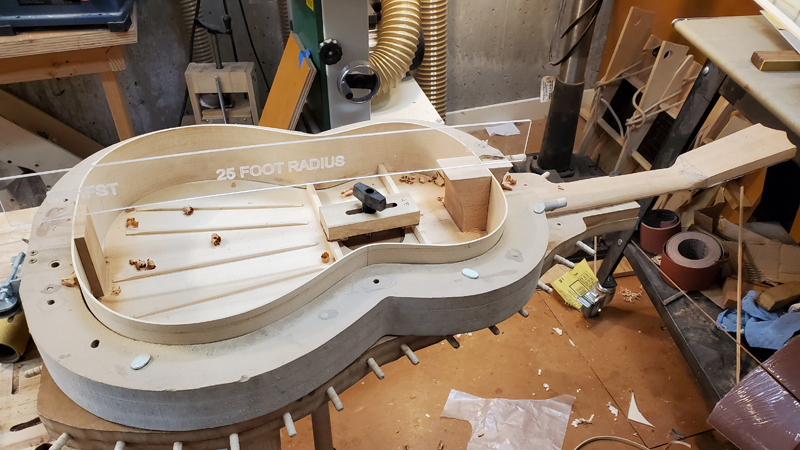
The neck step is to glue the neck to the top. Note if I were using linings instead of tentallones, I would glue the neck to the rims and install the linings. The top would be glued to the rims and neck and the same time. But building in this traditional style I need to glue the neck to the top making sure I am square to the center line everywhere. My solera has a neck angle built in. This operation is better with the top and the neck flat, so I have a seperate board to do this operation.

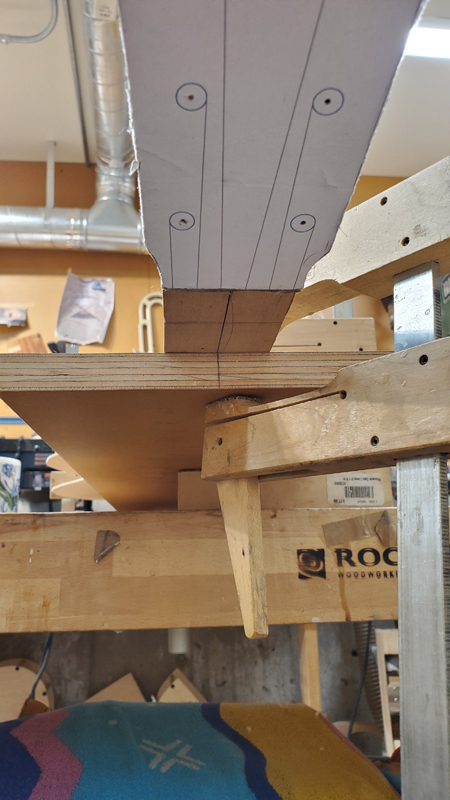
The neck and top are in line. I can not wait until the fretboard is glued on and I do not have to look at that router mishap.
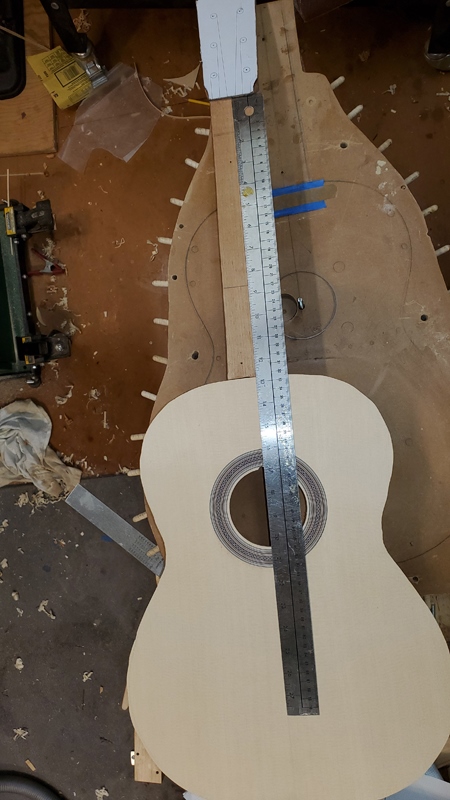
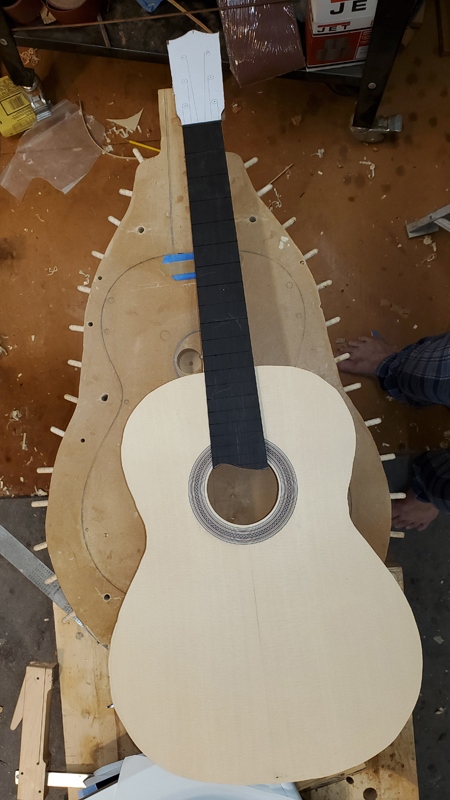
I like to install the end graph at this time. I just find it easier and safer with the top and back off. I can finally see my binding scheme of mahogany and black purfling lines.
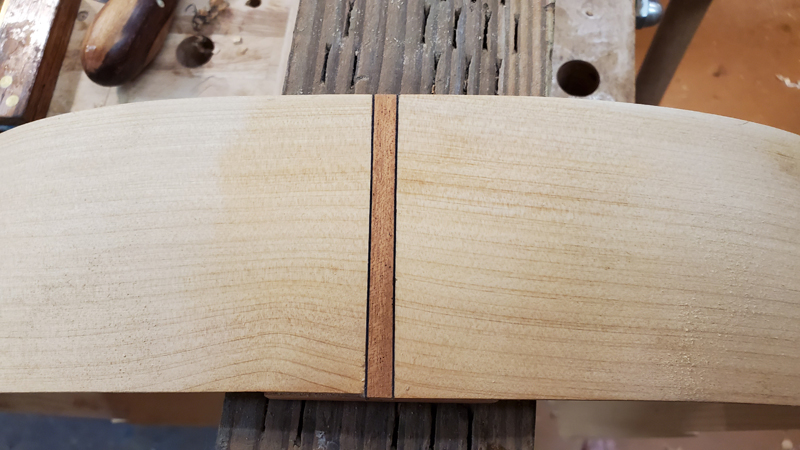
Next operation is to attach the rims to the top starting with the end block. I used a spatula to put glue on the block and I clamped it down.
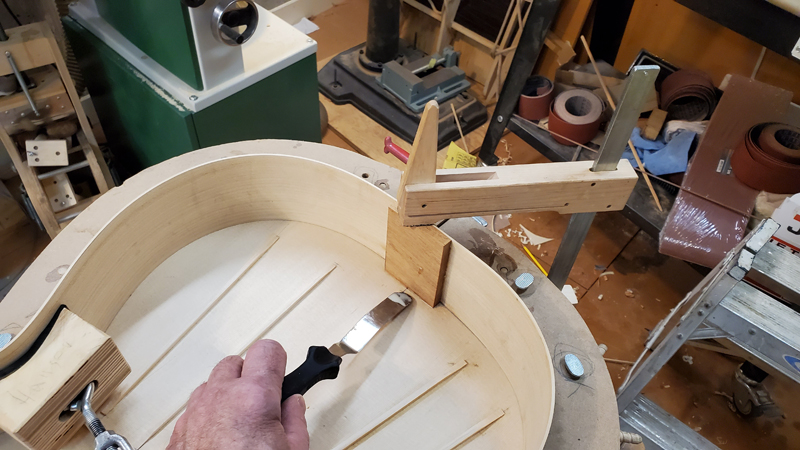
No one sells tentallones in the states so I had to make my own. I saw a youtube video by Pablo Requena https://www.youtube.com/watch?v=6KupYrzeVag&t=549s for a simple jig to cut a length of wood at an angle for the tentallones. He likes his blocks to be 10 mm by 14 which requires a 30° degree angle. For his jig he glued a couple of blocks of 3/4" plywood together and cut the face at 20 degrees. On to that face he glued a the square side of an off cut to the 30° face making a channel to guide a length of 10 mm by 30 stock into a bandsaw blade. A picture makes all of those words go away
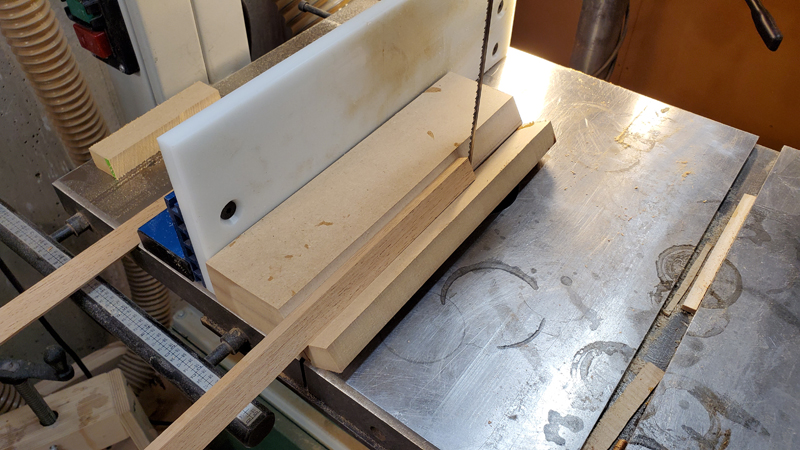
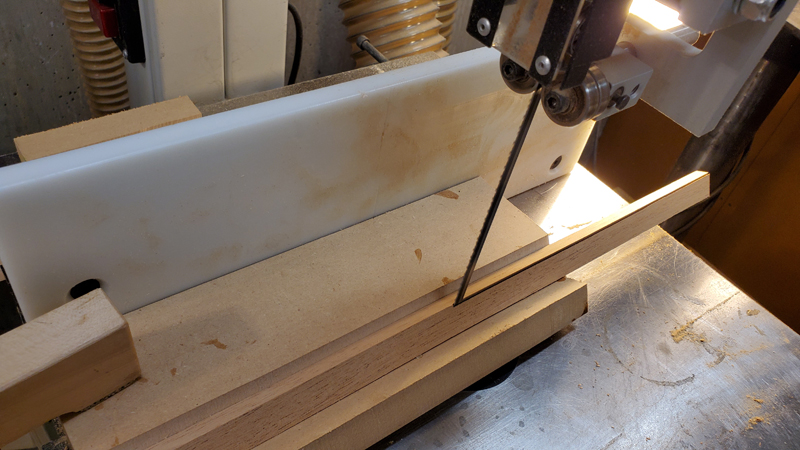
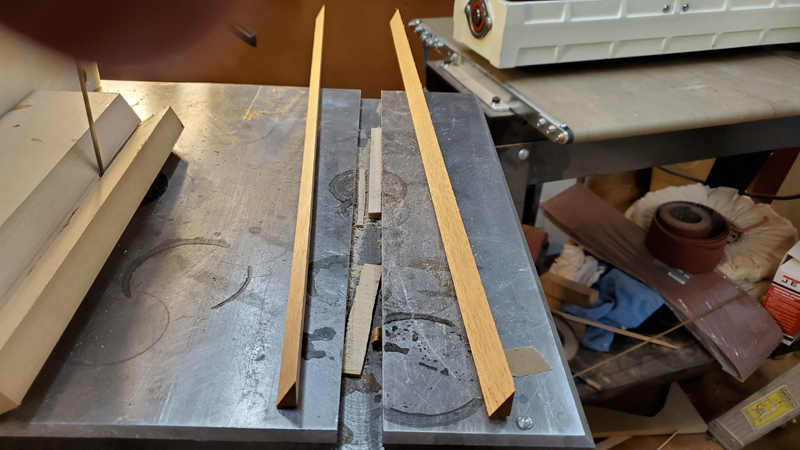
Then I just set a fence and had fed the stock to finish the tentallones.
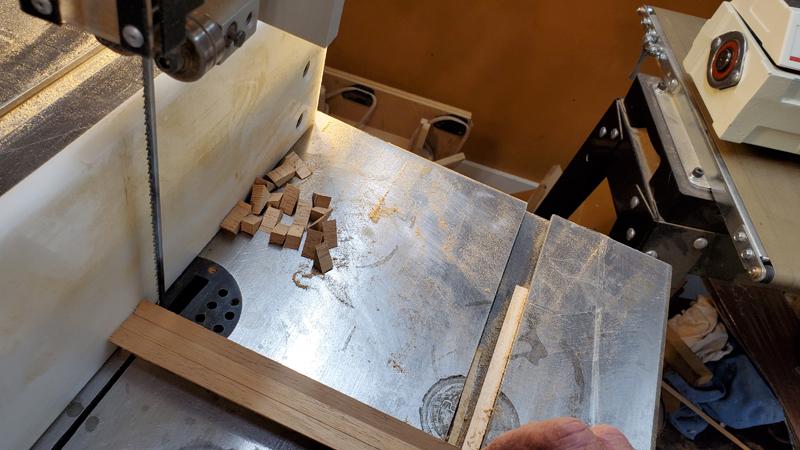
I used original titebond to glue these in place. I only need to hold them a moment and they seem to stick. On my first flamenco I used hot hide glue. I set the upper bout rather close for structural reasons. I space the lower bout to loosen the top a bit. I want the top to be able to drain its energy to get the flamenco sound. On a classical guitar I do just the opposite using solid lining to keep the sound in the top. This is not the most exciting operation building a guitar. I had spotify play a bunch of Paco De Lucia songs.
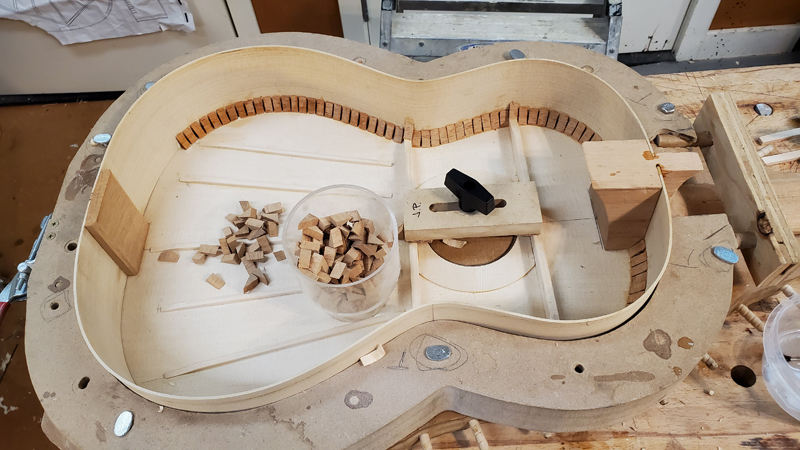
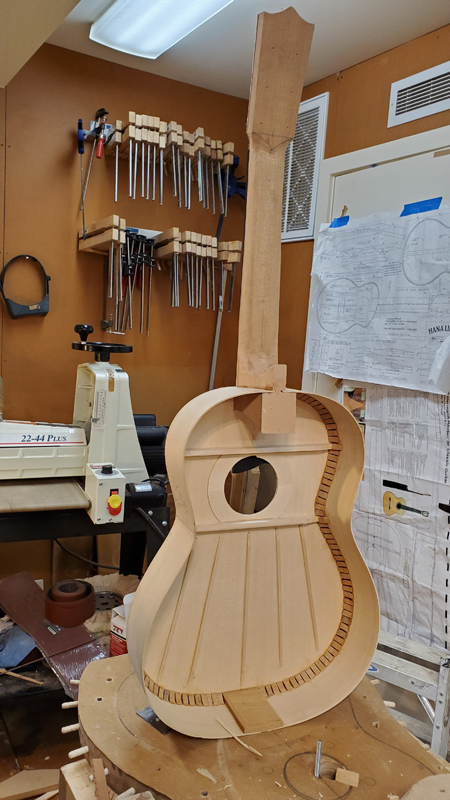