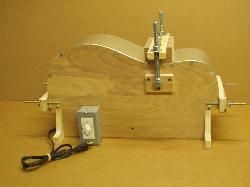
My new bender (so far)
Re: My new bender (so far)
Also its important to have the bulbs in close proximity to the form profile -- but not touching a support or the skin.
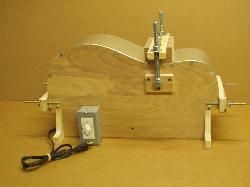
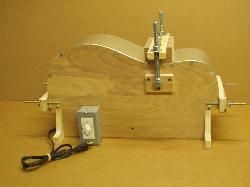
ken cierp
http://www.kennethmichaelguitars.com/
Store Front
http://www.cncguitarproducts.com/
KMG Guitar Kit Information
http://www.kennethmichaelguitars.com/ki ... ckage.html
http://www.kennethmichaelguitars.com/
Store Front
http://www.cncguitarproducts.com/
KMG Guitar Kit Information
http://www.kennethmichaelguitars.com/ki ... ckage.html
Re: My new bender (so far)
I have reflective material on the bottom below the ceramic bulb bases. I can put some above as well. I am thinking the bulbs are still too far away from the form. I will get them closer tomorrow and switch to a 300 w bulb for the lower bout. I am planning on prebending the waist as you recommend. I have not built the pipe bender yet. That comes after I finish this one.
- johnnyg
-
- Posts: 2824
- Joined: Mon Dec 19, 2011 4:19 pm
Re: My new bender (so far)
Johnny, some pics of my bender, note the aluminum taped cover that the bulbs screw through.
- Attachments
-
- benderreflector2.JPG (36.71 KiB) Viewed 3423 times
-
- tempprobe.JPG (35.44 KiB) Viewed 3423 times
-
- 339.JPG (36.38 KiB) Viewed 3423 times
Re: My new bender (so far)
Thanks to everyone for the tips and help. I reworked it again incorporating many of the suggestions. I added a base that is now even with the bottom of the bulbs. I relined everything on the inside with reflective insulated tape to reduce dissipation through the sides and back. Added a 300W bulb on the lower bout side. I believe I have overcome the heat problem as this thing heats to 250F in about 15 minutes. And that is with nothing on it but the aluminum skin.
I decide it was time to test it out. I have not yet build the pipe bender, although that is still my intention. This was just a test of the bending capabilities at this point in the venture. I have some test sides from the big Ohio vendor so that is what I used. I gave them a good soaking of water from a spray bottle and folded them into parchment paper. I then laid it directly on the skin on the mold and place my 6 x 6 heating blanket at the waist location. The I put a 6 x 36 piece of aluminum flashing on top of that to complete the sandwich. Fired up the light bulbs and plugged in the heating blanket and waited about 10 minutes. Tightening down the waist caul seemed to have little resistance so I slowly brought it down over about 10 minutes. Then I applied hand pressure to the lower bout and let them kind of work itself down. Same with the upper bout. After the bend operation I let it cook for about 15 minutes and shut everything down. it took about an hour to cool down to room temperature and i took the test side out.
i would call it partial success and partial fail. The fail part is the waist was cracked, even though it went down easy and I heard no tell tale noise. The inside of the lower bout area was scorched. Not badly, but it would take some good sanding to clean it up. The success part is the upper and lower bout bends actually looked pretty good except for some rippling and unevenness.
The skin on the bender also had some warpage and misshaping.
I attribute the fail parts to my lack of skill and knowledge. I would appreciate any critical reviews of my procedures and how to do it better. I know the pipe bender is recommended for the waist bend. Is the aluminum flashing from the box store too flimsy for this? Should I try to find something else? Should I add more aluminum rods to help it keep its shape? I am using 12 rods now and they seem close enough together.
Thanks for all input!
I decide it was time to test it out. I have not yet build the pipe bender, although that is still my intention. This was just a test of the bending capabilities at this point in the venture. I have some test sides from the big Ohio vendor so that is what I used. I gave them a good soaking of water from a spray bottle and folded them into parchment paper. I then laid it directly on the skin on the mold and place my 6 x 6 heating blanket at the waist location. The I put a 6 x 36 piece of aluminum flashing on top of that to complete the sandwich. Fired up the light bulbs and plugged in the heating blanket and waited about 10 minutes. Tightening down the waist caul seemed to have little resistance so I slowly brought it down over about 10 minutes. Then I applied hand pressure to the lower bout and let them kind of work itself down. Same with the upper bout. After the bend operation I let it cook for about 15 minutes and shut everything down. it took about an hour to cool down to room temperature and i took the test side out.
i would call it partial success and partial fail. The fail part is the waist was cracked, even though it went down easy and I heard no tell tale noise. The inside of the lower bout area was scorched. Not badly, but it would take some good sanding to clean it up. The success part is the upper and lower bout bends actually looked pretty good except for some rippling and unevenness.
The skin on the bender also had some warpage and misshaping.
I attribute the fail parts to my lack of skill and knowledge. I would appreciate any critical reviews of my procedures and how to do it better. I know the pipe bender is recommended for the waist bend. Is the aluminum flashing from the box store too flimsy for this? Should I try to find something else? Should I add more aluminum rods to help it keep its shape? I am using 12 rods now and they seem close enough together.
Thanks for all input!
- johnnyg
Re: My new bender (so far)
So far I've always bent the waist first. When you do that first you learn about that particular wood and get a feel for how it bends and temp/ moisture details. Definitely make the pipe bender. Ken's design works very well.
JJ
Learning every day. And having fun doing it.
Learning every day. And having fun doing it.
Re: My new bender (so far)
Heat should applied to the compression side of a bend -- inside the curve. I don't recommend that process none the less the heater was on the wrong surface.I then laid it directly on the skin on the mold and place my 6 x 6 heating blanket at the waist location.
Pre-bend the waist -- nough said.The fail part is the waist was cracked, even though it went down easy and I heard no tell tale noise.
Too much water and likely not enough support or form covering too thinupper and lower bout bends actually looked pretty good except for some rippling and unevenness.
We have about a dozen supports on all our forms --- they also have to be exactly on the curve tangent. Plain aluminum flashing material is too thin I made one form with it and plan to re-cover with .023" materialThe skin on the bender also had some warpage and misshaping.
ken cierp
http://www.kennethmichaelguitars.com/
Store Front
http://www.cncguitarproducts.com/
KMG Guitar Kit Information
http://www.kennethmichaelguitars.com/ki ... ckage.html
http://www.kennethmichaelguitars.com/
Store Front
http://www.cncguitarproducts.com/
KMG Guitar Kit Information
http://www.kennethmichaelguitars.com/ki ... ckage.html
Re: My new bender (so far)
So the luthier I am working with talked me into trying out using a steam box he had just built. I have to say it went very well. I thinned the sides to .075 and then steamed them for 30 minutes each and then put them straight into the preheated light bulb bender. I used a sandwich of parchment paper, the side, another layer of paper and then the .020 sheet metal flashing. I bent the waist first, then the upper bout, then the lower. I had them all done in 5 minutes. This was longer than my goal of 2 minutes but I am still a little gun shy about bending too fast. I let them cook in the bend for about 15 minutes and then shut it off and let it cool to room temp. The sides came out great. Beautiful bends with very little spring back and went into the form very well. There were a few water spots on the wood, but they will sand out easily.
let me know what you think.
let me know what you think.
- johnnyg