Page 2 of 7
Re: Antes Plan Martin O sized Koa guitar
Posted: Thu Dec 29, 2011 3:07 pm
by TonyinNYC
I have major shop envy! Building for others when money is involved definitely raises the stress level. However, I think it pushed me to build better guitars. So far everyone thinks they got a bargain and I am happy with that. You are doing great work John. Keep the pics and posts coming!
Re: Rick Micheletti Plan Martin O sized Koa guitar
Posted: Thu Dec 29, 2011 8:48 pm
by John Parchem
I was only able to spend a little time this morning on the guitar, but I did get the fingerboard inlays installed. It went pretty well; on some of them I would be ready for inlays on lighter wood. But luckily enough for me I am doing it in ebony.
To keep documenting how I do things, First I use LMI white glue just a dab to hold the inlays down to trace the pattern with a .05 mm lead pencil. I only let it set up for ten minutes before I trace. Then I carefully pop them off with an exacto knife blade.
When I routed for the inlays I tried two different procedures. One some of the holes first I traced out the pattern with a very small end mill, and then went after the bulk of the material a larger mill. On the rest of the holes I took out most of the material with a larger end mill and cleaned up the details with the very small mill. I still am not sure which I like best.
I am leaning on bulk removal first followed by detail.
I used thin CA at the bottom to hold them down, filled the small (and not so small gaps) with ebony dust from the routing and then wicked thin CA into the ebony filled gaps.
Here are the pictures.
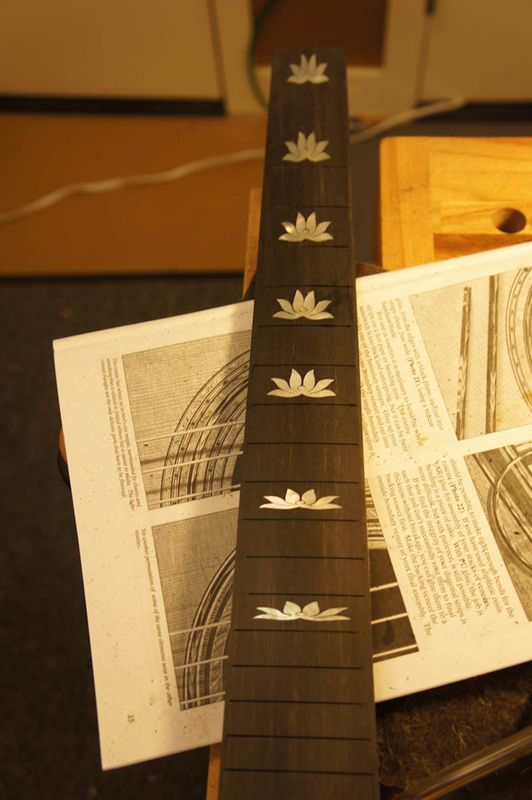
For tomorrow I am still trying to figure out which veneer to use from the two I cut. Then it is one to profiling the headstock and possibly carving the neck.
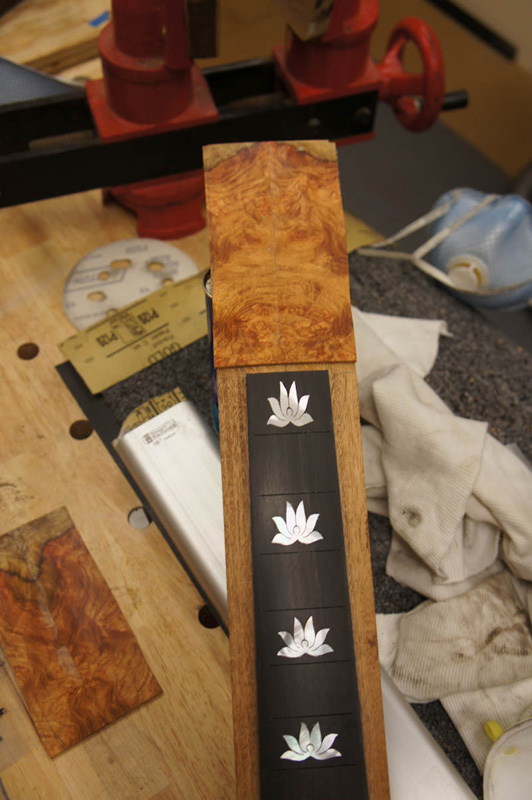
Re: Antes Plan Martin O sized Koa guitar
Posted: Fri Dec 30, 2011 10:50 am
by TonyinNYC
Nice work on the inlays!
Re:Rick Micheletti Plan Martin O sized Koa guitar
Posted: Mon Jan 02, 2012 3:20 pm
by John Parchem
This amounts to a couple of days of work and includes a bunch of pictures, maybe too many, but you all get to see how I went about nearly finishing this neck. As part of this work one could see the advantaged of a nicely indexed fingerboard. I like to glue on the fingerboard very late because once glued the neck angle set gets harder. But I do want to know exactly where the fingerboard is on the neck when gluing on the headstock veneer and carving the neck. I will glue on the fingerboard for the sanding of the neck so that I will sand the neck and the fingerboard edge together.
For this guitar I made a headstock template out of plexiglass with holes for the tuner and my logo.
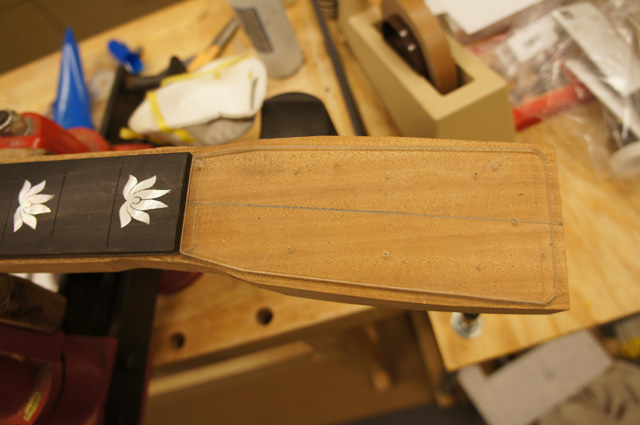
I used the template to decide where to cut the nut end of the headstock veneer, marked it and used my belt sander to sand in the headstock angle.
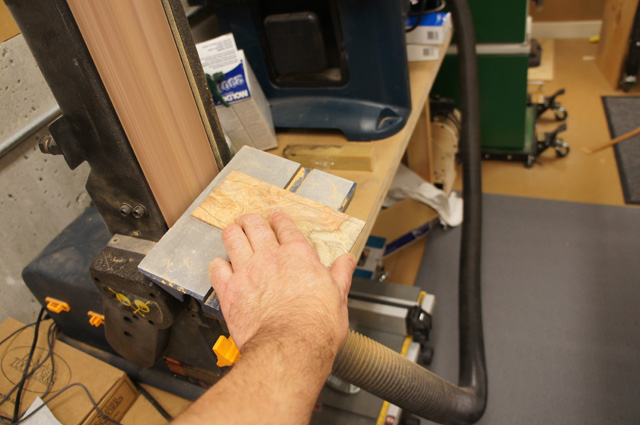
I have a properly sized nut blank, that I cut too short on one guitar, which I use to properly space the headstock veneer.
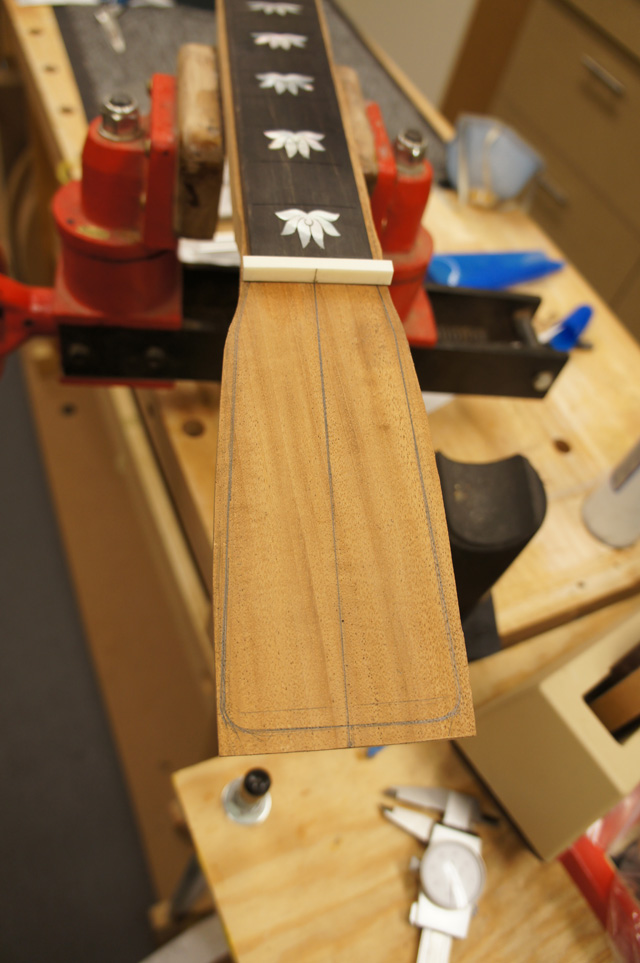
I laid out the headstock veneer double checking everything and proceeded to glue it on to the headstock with LMI white glue.
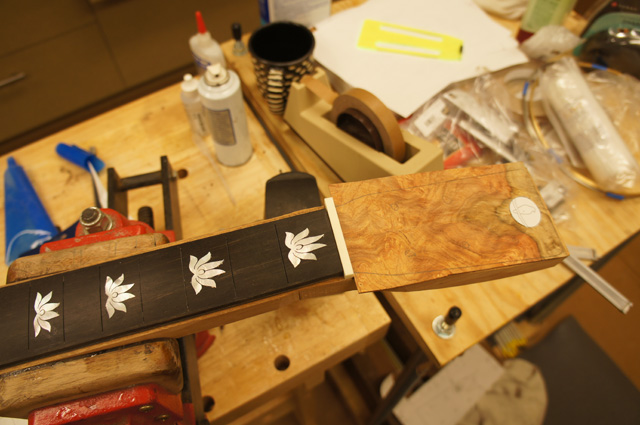
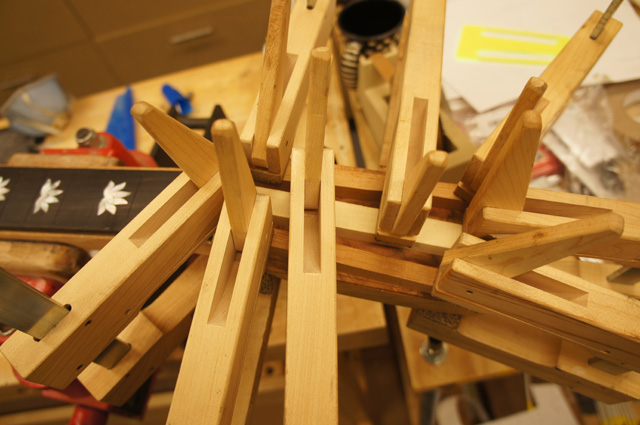
I used good double stick-um tape to glue the template on to the headstock and used the template as an index for the Luthier friend sanding drum.
I think next time I will use a router. With a router I could have profiled this in one pass, with less opportunity of error.
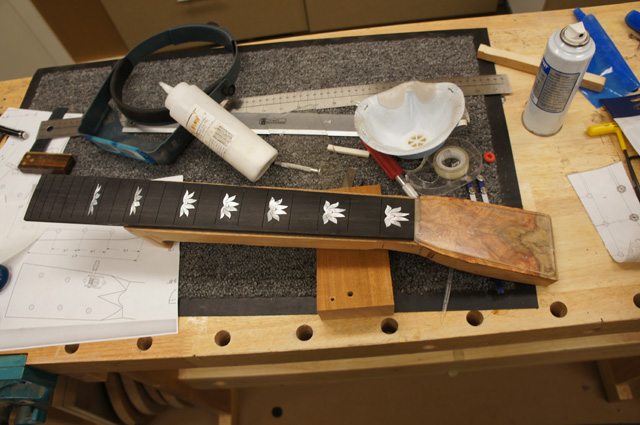
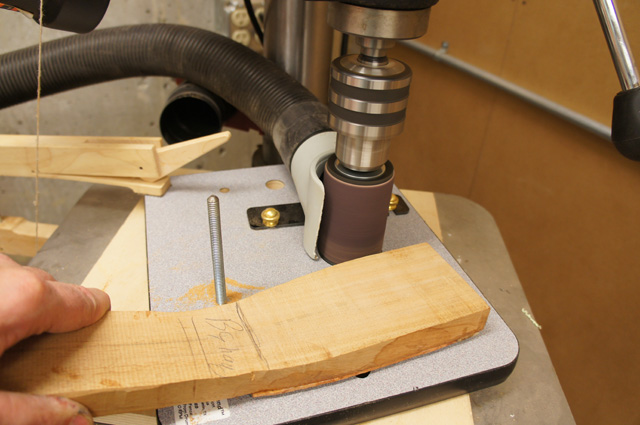
I used my favorite tool the safe-t planer (how can it be any safer!), wheel of spinning blades, to take the headstock to the right depth. I take very little off each pass. Basically I bump height wheel with the drill press locked. Toward the end, I carefully dial it in using the depth stop on the drill press.
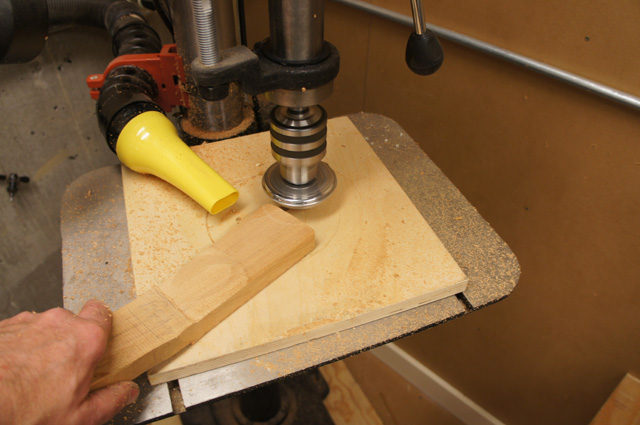
I took the desired width at the fingerboard and at the tail of the heel and made a half pattern that I transferred first to a piece of plexiglass and then to the bottom of the neck heal. I also free hand drew a heal cap shape and glued it on to the heel with CA.
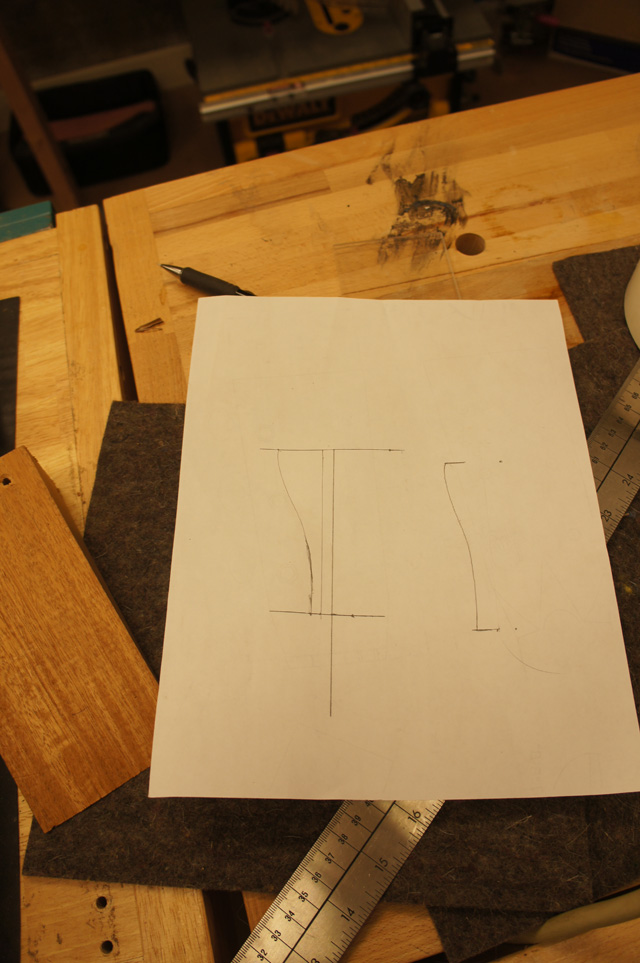
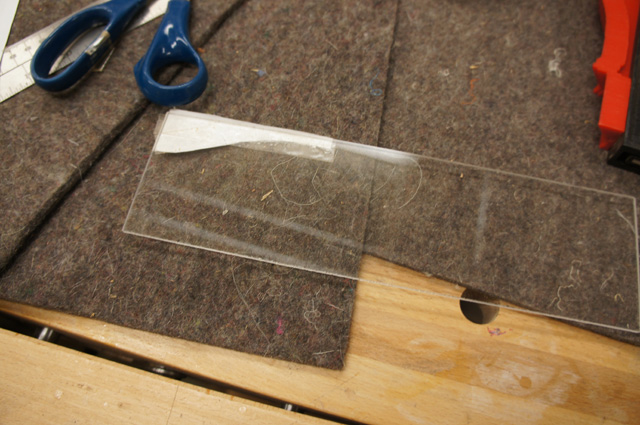
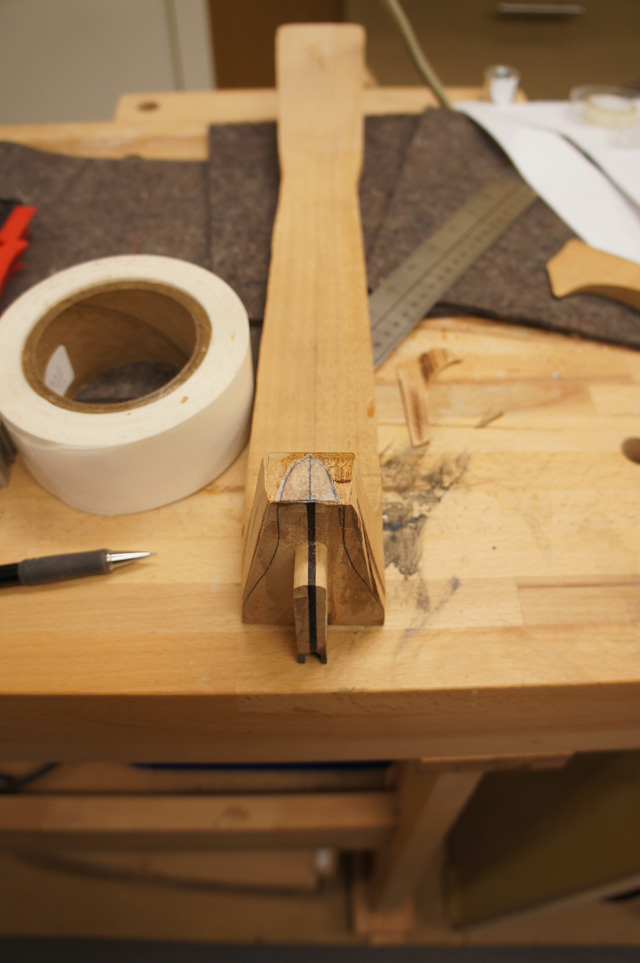
I use long sweeping strokes with the rasp or micro plane to follow the profile and approach the center line on the top of the heel. I find that if I keep the approach to the center line and the approach to the profile somewhat even and use long sweeping strokes the heel carves to a natural (based on the profile) curve.
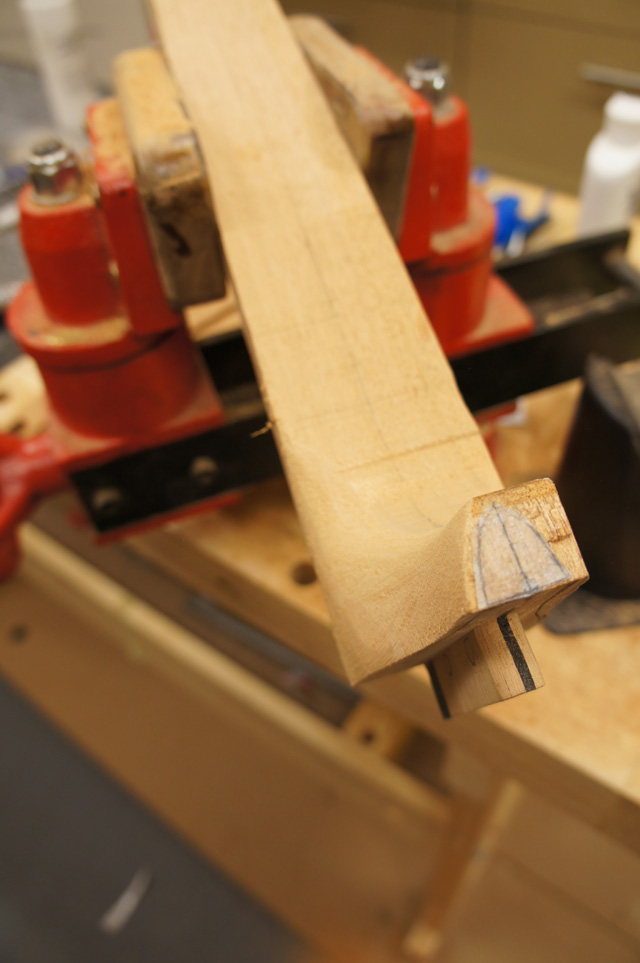
When first starting I use a micro plane to take off some of the bulk. I mostly use course and fine carpenter rasps from LMI as I like the feel in my hand.
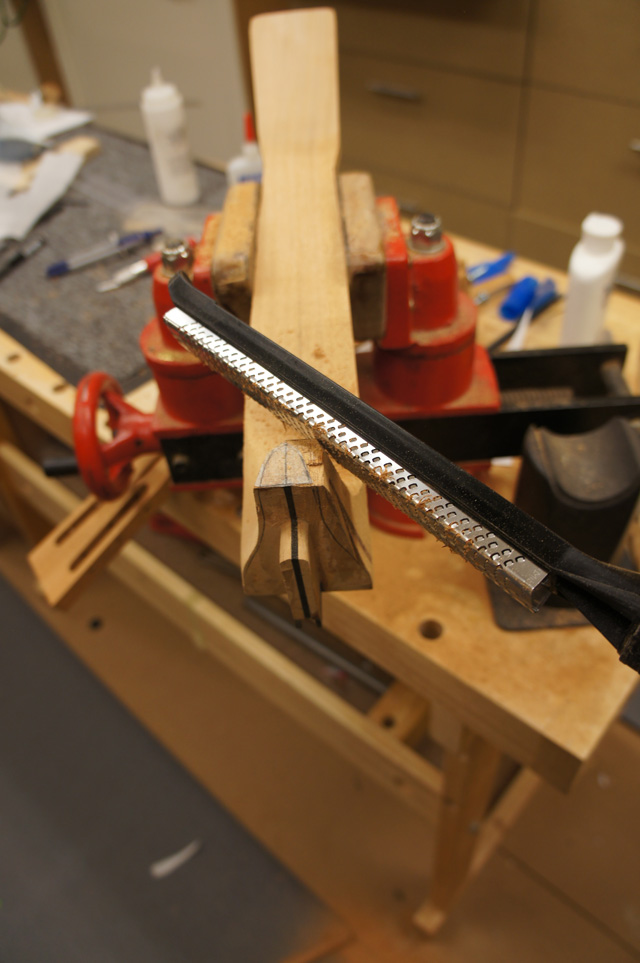
This is good enough for now. It is close to symmetrical. I still have a little to go but I will save it until after the rest of the neck is carved.
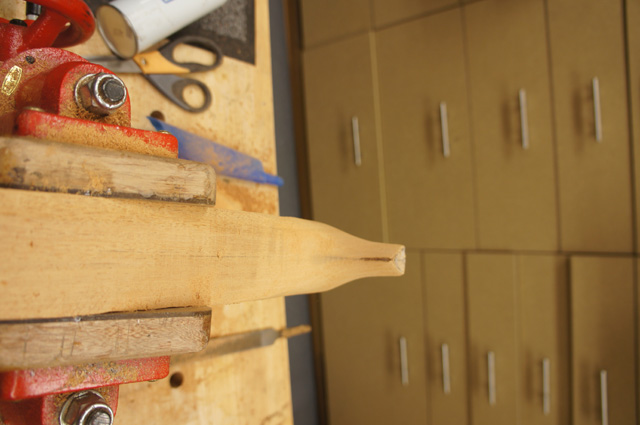
Although the use of fast power tools often gets me in trouble I used the belt sander to profile the thickness I wanted for the final neck. With it I can be sure that I have a plane along the centerline instead of a curve. I am making the neck about .85” at the first fret and .95” at the eighth fret.
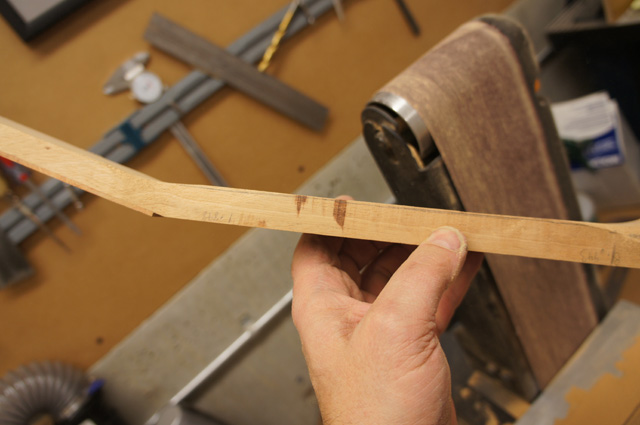
I general just freehand the carve; working toward the edge and the centerline somewhat evenly (as a percent) using nice sweeping stokes. I did carve one side making a 45 degree facet and using a 22 degree angle to take the edges off of the first facet. I could see this method would allow me to better match a desired template with the proper use of layout lines.
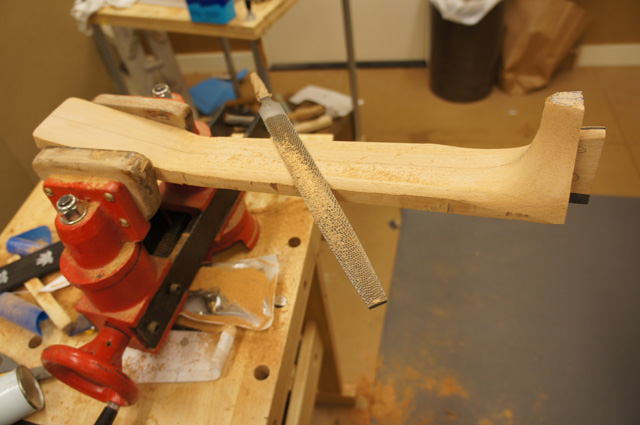
Here are a few photos of where I am at. The neck angle is still right on and over all the neck looks good on the guitar. After a break to get out of the push mode I am in I will glue on the finger board, work out the transition between the headstock and the neck and final sand the neck. Also note in the pictures the smoothness of the carving from the fine rasp. I have not yet used any sandpaper on the carved parts of the of the heel.
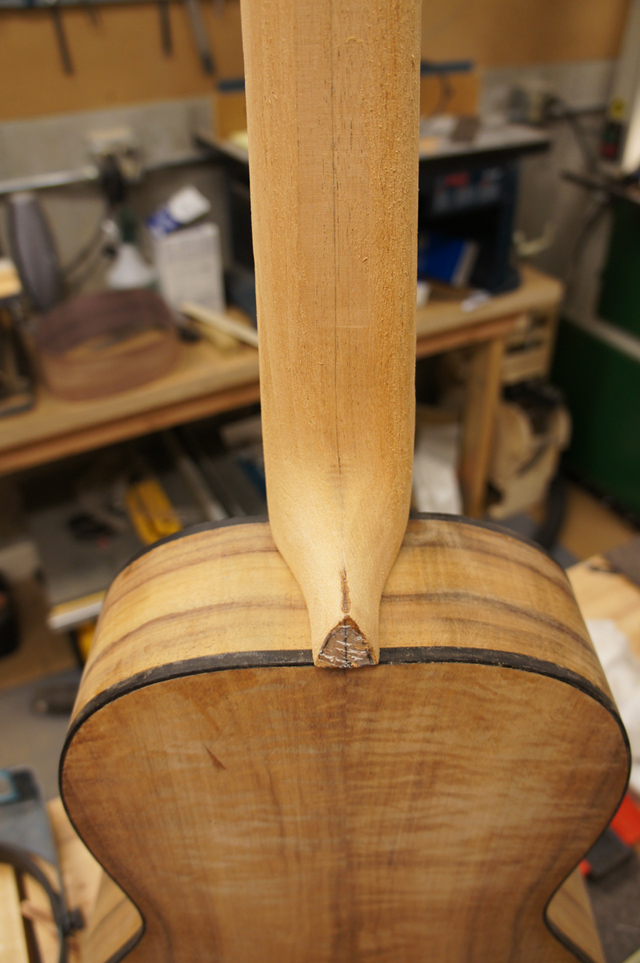
Re: Rick Micheletti Plan Martin O sized Koa guitar
Posted: Tue Jan 17, 2012 11:22 pm
by John Parchem
Re: Antes Plan Martin O sized Koa guitar
Posted: Tue Jan 17, 2012 11:39 pm
by Dave Bagwill
Very nice work, John, as we've come to expect from you, and always enjoy seeing it and hearing about it.
Re: Antes Plan Martin O sized Koa guitar
Posted: Wed Jan 18, 2012 8:41 am
by David L
Great work and documentation too, typical JP style.
David L