continuing build thread for Gore Medium body SS
-
- Posts: 2754
- Joined: Fri Dec 23, 2011 8:33 pm
- Location: Seattle
- Contact:
Re: continuing build thread for Gore Medium body SS
The pucker or crease he mentions in the book is between the end block and the lining. The example he showed had mahogany end block and and kerfed linings. He has not seen it on backs. I never have seen this but the book and his procedures cover both classical and SS. A lot of the classical tops are pretty thin on the edges, sub 2 mm. He thinks using plywood for the tail block helps. He also straps the linings to the end block. I am not finished with the strap yet. Ultimately it will be sanded to flow into the linings.
- Attachments
-
- straping.jpg (154.5 KiB) Viewed 790 times
-
- Posts: 2754
- Joined: Fri Dec 23, 2011 8:33 pm
- Location: Seattle
- Contact:
Re: continuing build thread for Gore Medium body SS
I am getting close to finishing the rims. I still need to put the back in the radius dish again to clean up the kerfed linings and generally spend some quality time clean up the inside of the rims.
Today I added the kerfed linings for the back, installed the side splints and manufactured and glued on the mass support block. Somehow I did not take pictures making the mass support blocks but you will see them in the photos below. The mass support blocks will allowed me to add mass to sides to tune them a bit. More mass on the sides allows one to drop the top resonance frequency without little change to resonances. It is just a mahogany block with a nut in it. The book called out a t-nut, I used a brass insert (mainly cause I had them and did not have a t-nut. ), You can see it in the second picture.
As recommended I installed the kerfed linings in small strips and as you can see in the first and second picture I left room for the side splint. The side spint is inlet into the top linings and runs to the back. Ultimately they will be sanded with the back kerfed linings
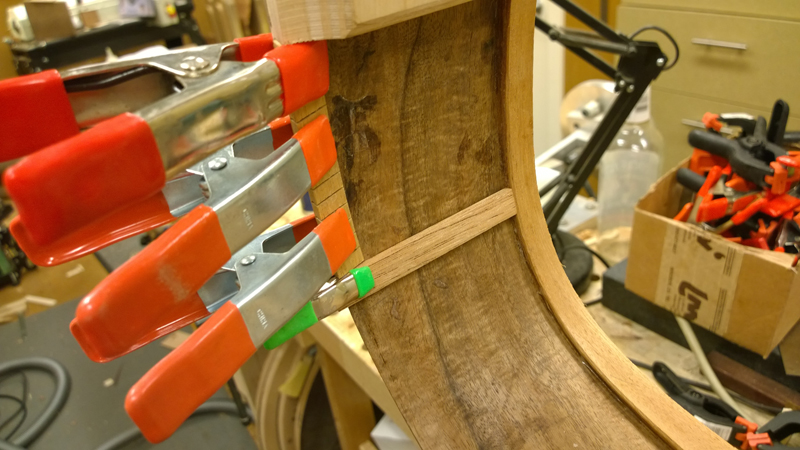
In the next few pictures you can see a mass support block. I have one on both sides.
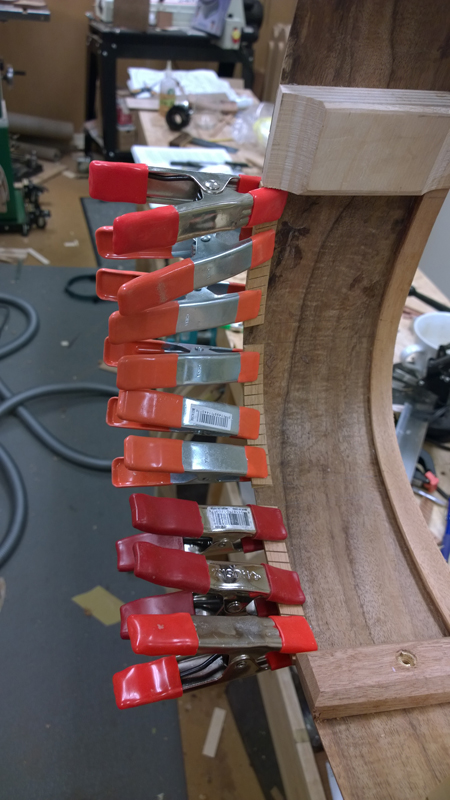
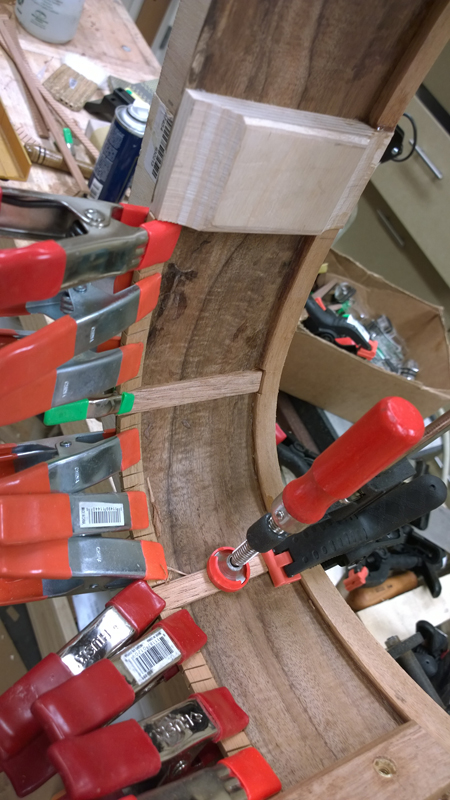
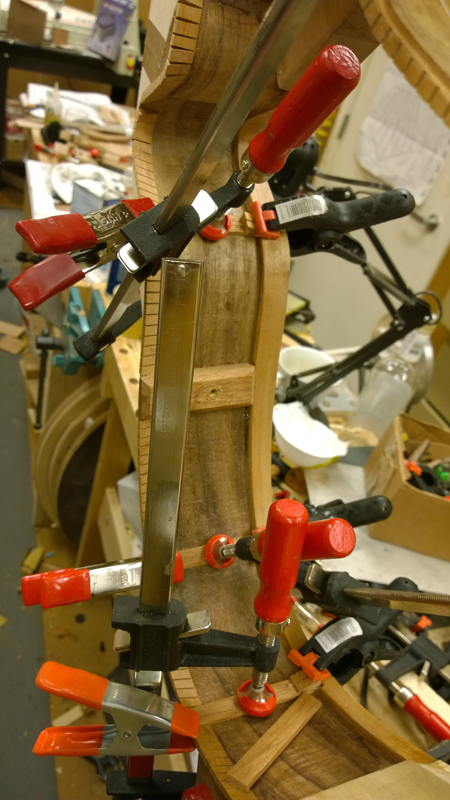
In this picture I am preparing to glue (following picture) a strap tying the kerfed top lining to the end block. It is used to avoid a ripple that sometimes shows on a top where the linings join the end block. I will blend the strap into the linings, once the glue sets.
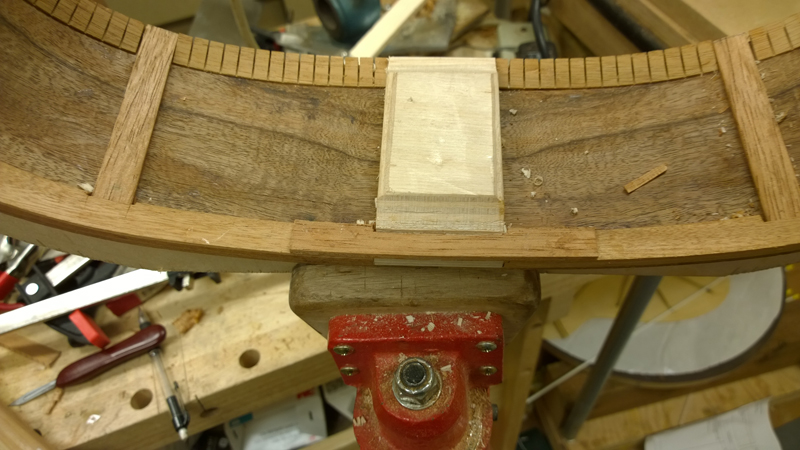
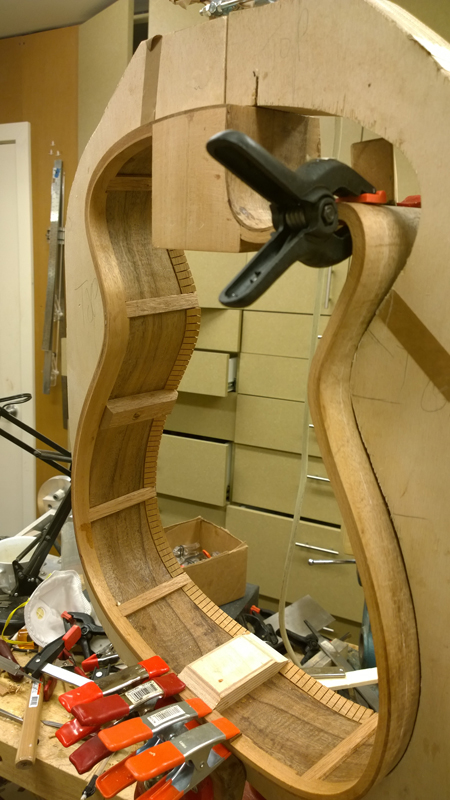
Today I added the kerfed linings for the back, installed the side splints and manufactured and glued on the mass support block. Somehow I did not take pictures making the mass support blocks but you will see them in the photos below. The mass support blocks will allowed me to add mass to sides to tune them a bit. More mass on the sides allows one to drop the top resonance frequency without little change to resonances. It is just a mahogany block with a nut in it. The book called out a t-nut, I used a brass insert (mainly cause I had them and did not have a t-nut. ), You can see it in the second picture.
As recommended I installed the kerfed linings in small strips and as you can see in the first and second picture I left room for the side splint. The side spint is inlet into the top linings and runs to the back. Ultimately they will be sanded with the back kerfed linings
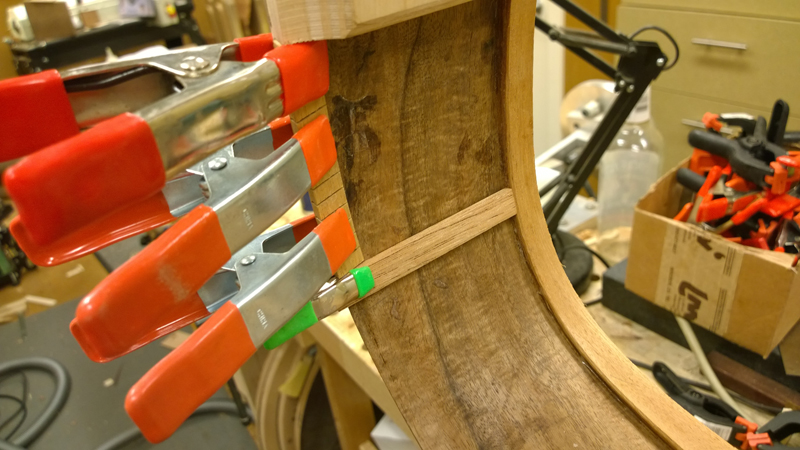
In the next few pictures you can see a mass support block. I have one on both sides.
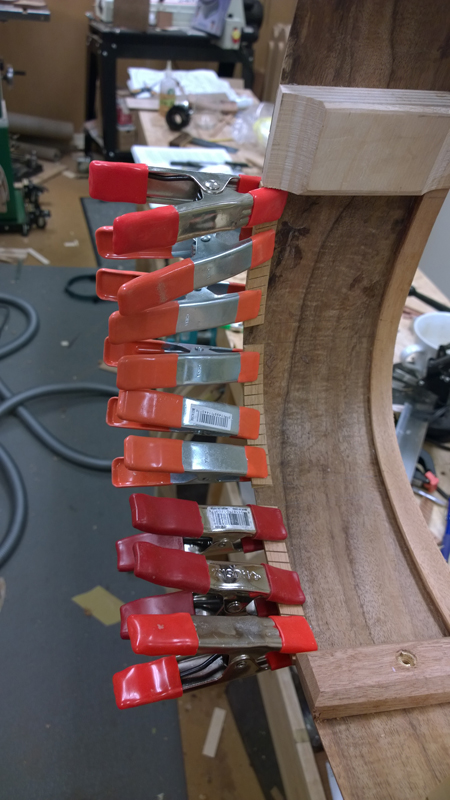
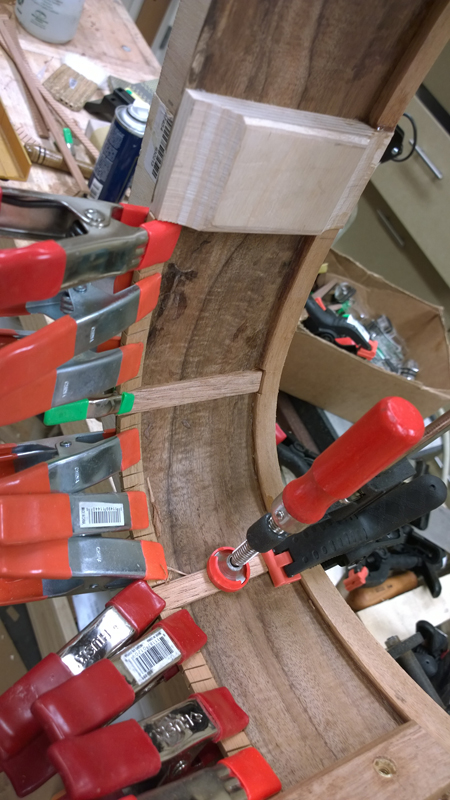
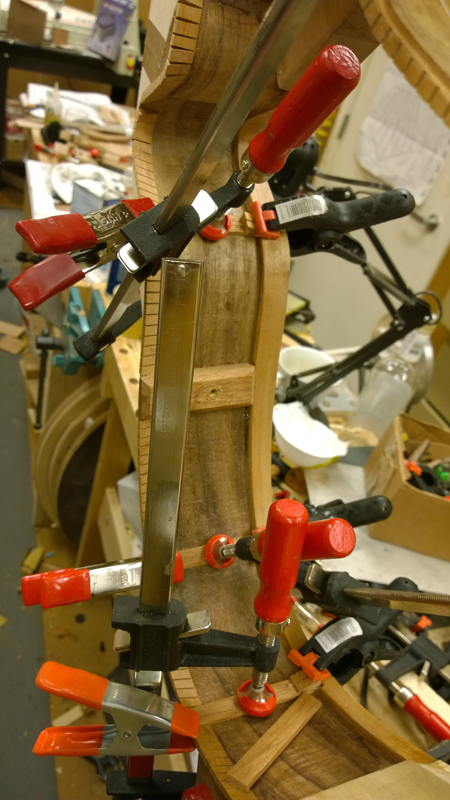
In this picture I am preparing to glue (following picture) a strap tying the kerfed top lining to the end block. It is used to avoid a ripple that sometimes shows on a top where the linings join the end block. I will blend the strap into the linings, once the glue sets.
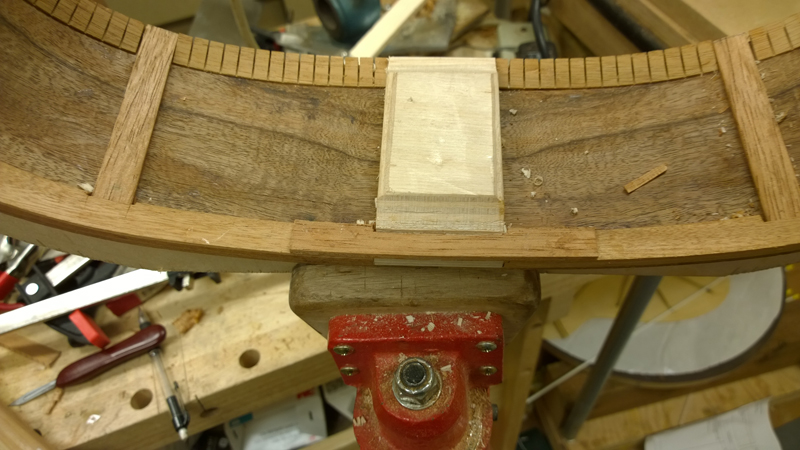
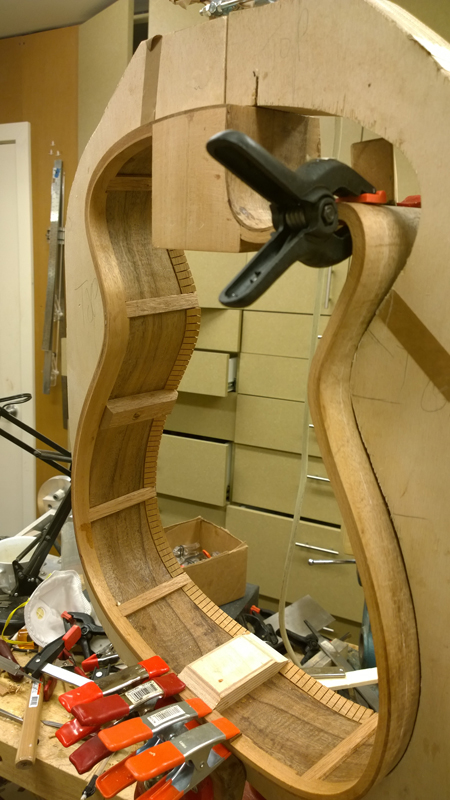
Re: continuing build thread for Gore Medium body SS
ken cierp
http://www.kennethmichaelguitars.com/
Store Front
http://www.cncguitarproducts.com/
KMG Guitar Kit Information
http://www.kennethmichaelguitars.com/ki ... ckage.html
http://www.kennethmichaelguitars.com/
Store Front
http://www.cncguitarproducts.com/
KMG Guitar Kit Information
http://www.kennethmichaelguitars.com/ki ... ckage.html
-
- Posts: 2754
- Joined: Fri Dec 23, 2011 8:33 pm
- Location: Seattle
- Contact:
Re: continuing build thread for Gore Medium body SS
It could be, I know he builds or has built boats.
-
- Posts: 2754
- Joined: Fri Dec 23, 2011 8:33 pm
- Location: Seattle
- Contact:
Re: continuing build thread for Gore Medium body SS
I have the body components finished and am in the process of cleaning things up and fitting the top and back on to the rims. This guitar is designed to have an active back so I thinned the back down a bit more than I normally would, used the plans 3 meter radius (well I used 10 feet) and used the plans active bracing pattern.
Bracing the back was pretty straight forward, the one change in my procedures was I could not use the 10 foot radius dish to radius the braces. I found it too had to not roll over the sides a bit. Instead I used the 10 foot radius board I made to first mark the radius for using a plane and I finished up the braces in the other side of the radius board.
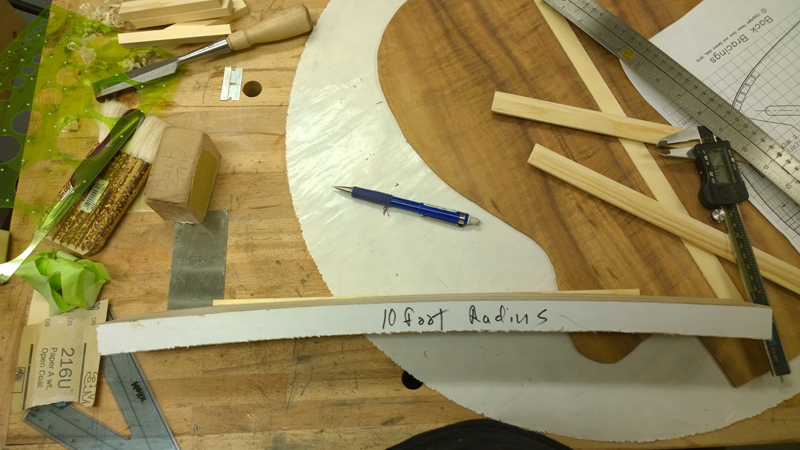
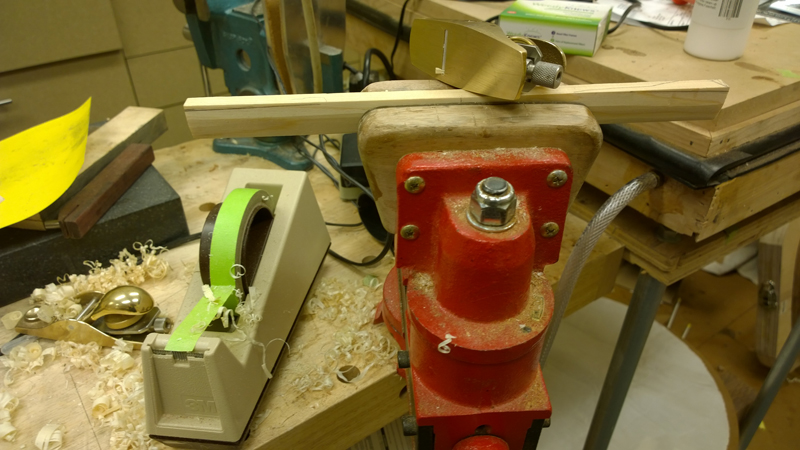
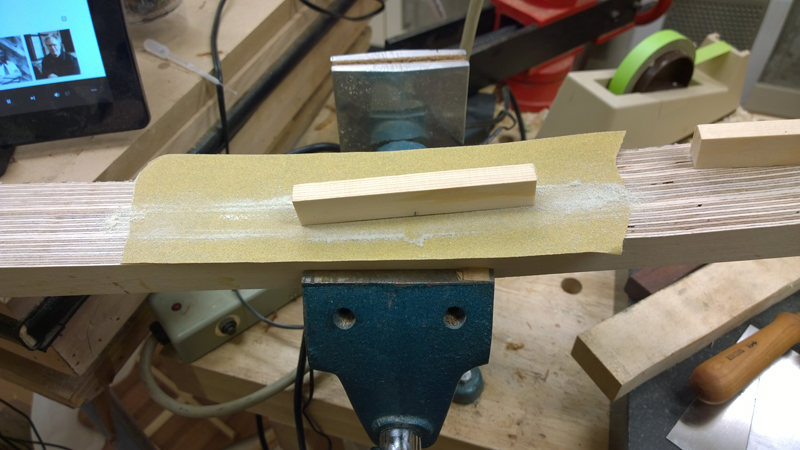
The braces are all house shaped in their in profile. The book had a method of using a 22.5 degree router bit to shape the brace stock. I bought the bit but I found the process a little scary, so I used a chisel and a small plane to shape the braces.
Also the live back plan has a set of radial braces in the lower bout. I made a 30 degree square to set the brace location.
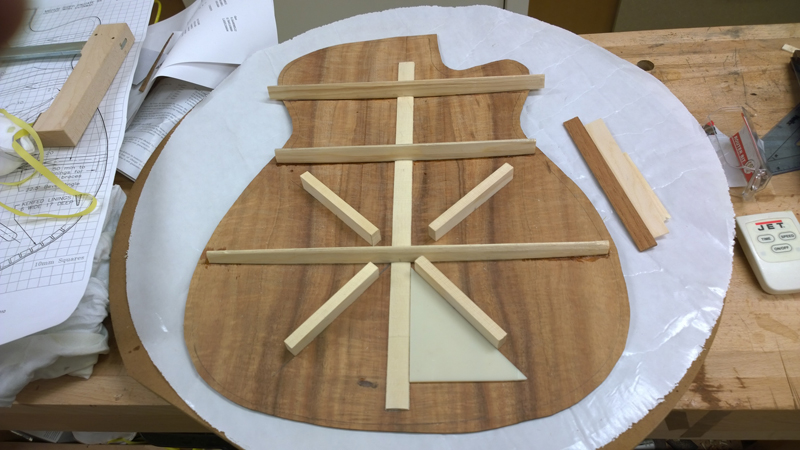
A bit of chisel work shaped the braces
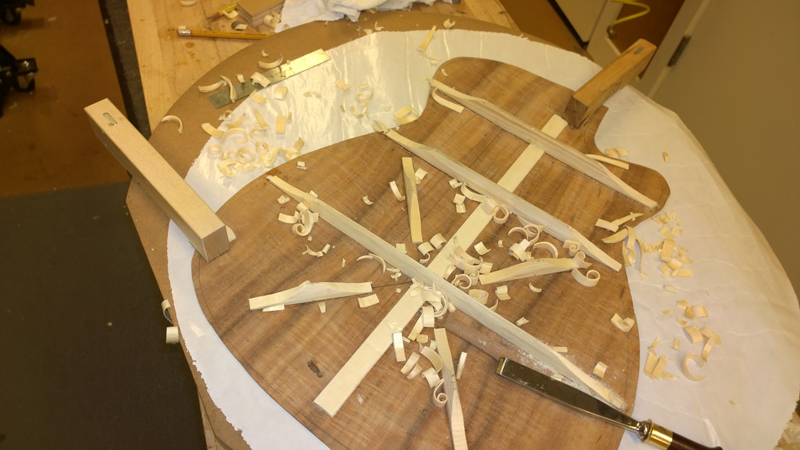
After a little bit of clean up I had the completed rims, top and back.
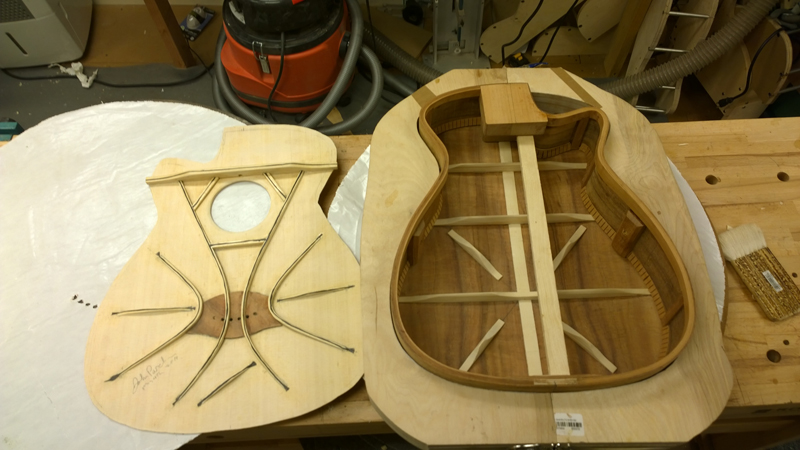
The carbon fiber on the top kept the top in the prefect shape. Absolutely no spring back. There was even a bit of vacuum when I put the top on the radius board that the top was glued up in. A straight edge on the fret board extension area of the top gave me the perfect 2.5 mm at the saddle that I am looking for.
When I fit the top to the rims it was easy to see that I made a little bit more longitudinal radius than I wanted. as the top needed to be pushed down about a mm at the blocks. It was hard to see this with the rims in the radius board as the neck block extension block the view. No big deal though. I carefully used a combination of a block plane and the radius board to take more off of the middle of the rims, until the top fit perfectly. It now sits on the rims requiring no pressure to hold it down. I also still have the correct body angle to match the required neck angle.
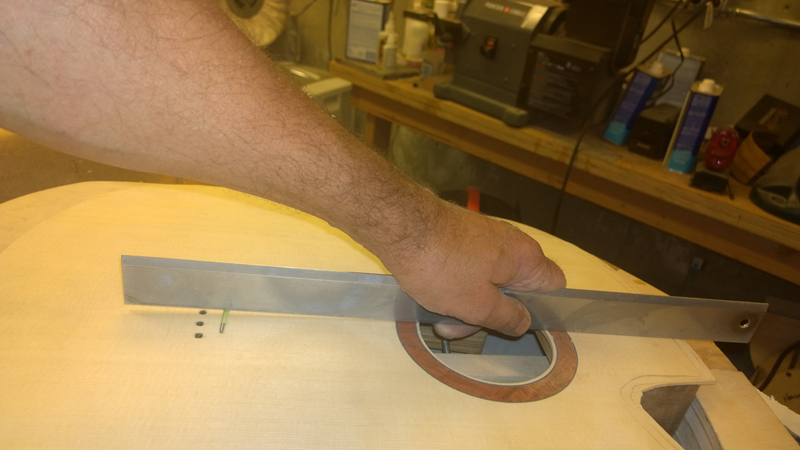
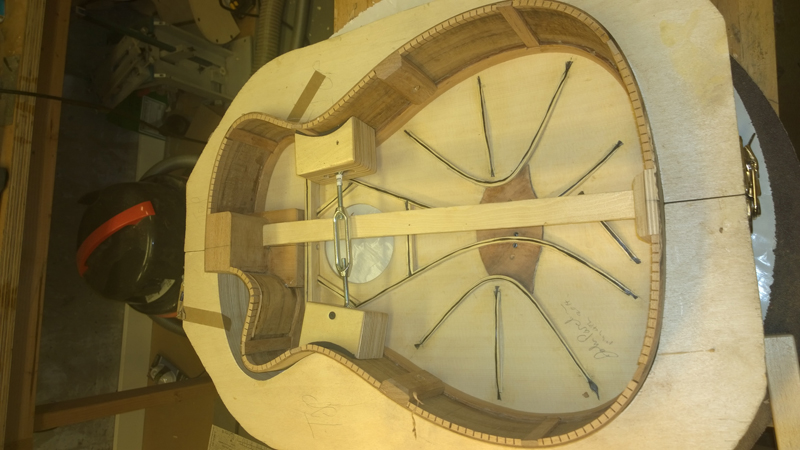
I need to route the rims for the back braces, a bit more cleanup and I can close the box.
Bracing the back was pretty straight forward, the one change in my procedures was I could not use the 10 foot radius dish to radius the braces. I found it too had to not roll over the sides a bit. Instead I used the 10 foot radius board I made to first mark the radius for using a plane and I finished up the braces in the other side of the radius board.
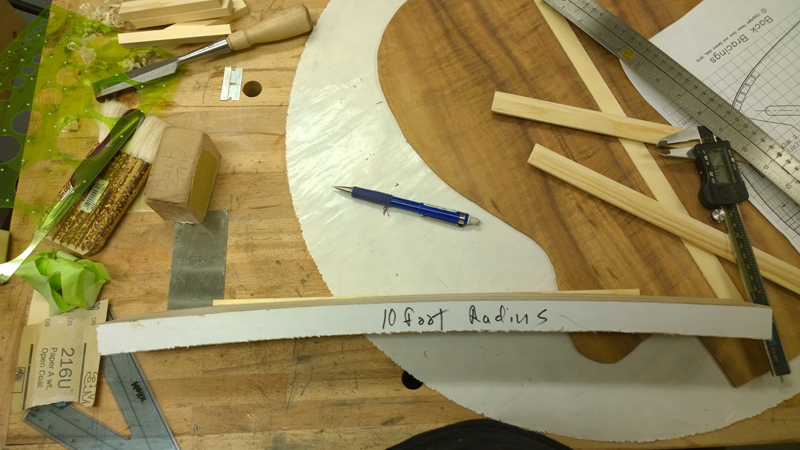
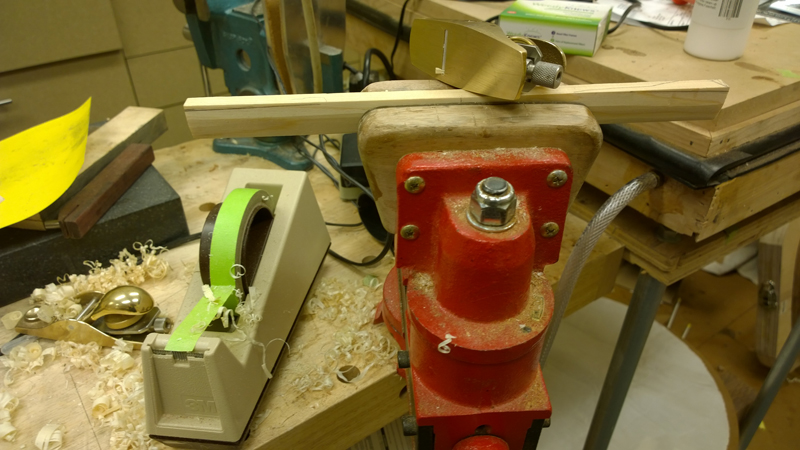
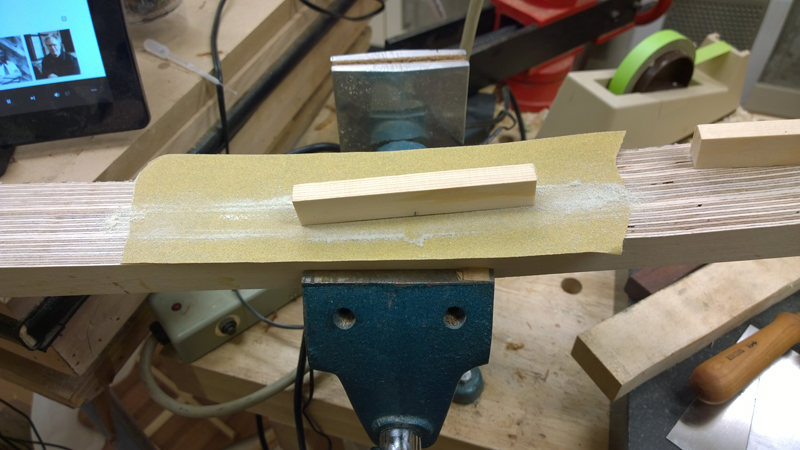
The braces are all house shaped in their in profile. The book had a method of using a 22.5 degree router bit to shape the brace stock. I bought the bit but I found the process a little scary, so I used a chisel and a small plane to shape the braces.
Also the live back plan has a set of radial braces in the lower bout. I made a 30 degree square to set the brace location.
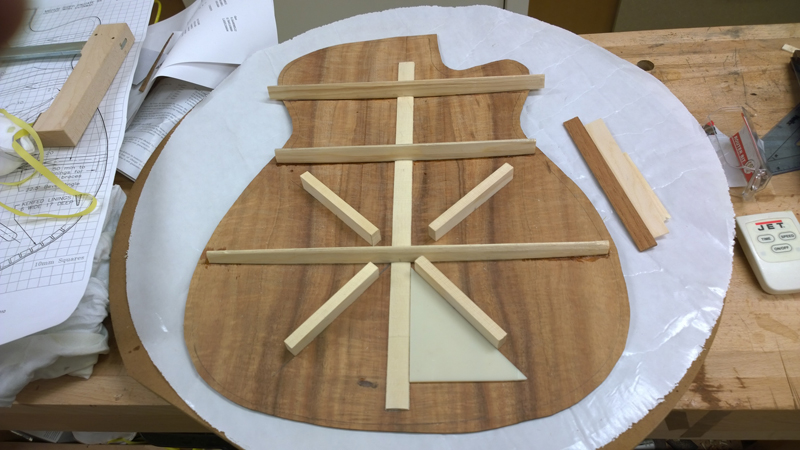
A bit of chisel work shaped the braces
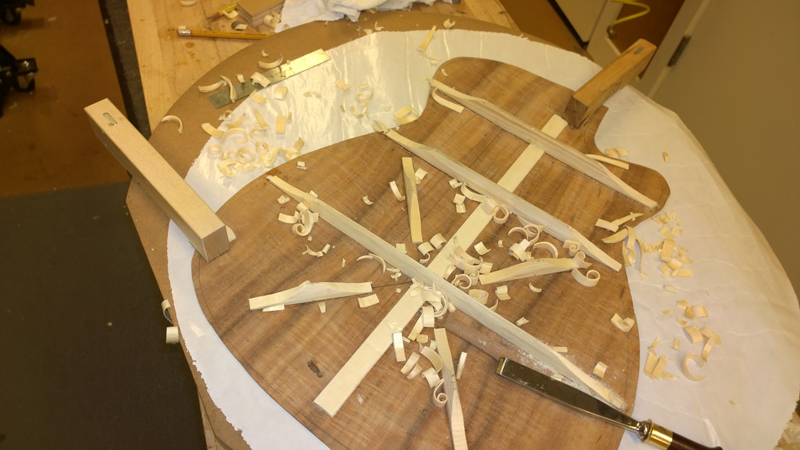
After a little bit of clean up I had the completed rims, top and back.
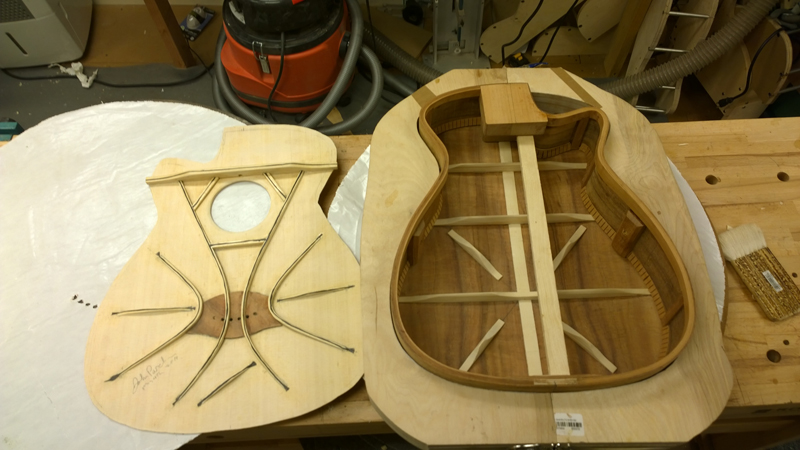
The carbon fiber on the top kept the top in the prefect shape. Absolutely no spring back. There was even a bit of vacuum when I put the top on the radius board that the top was glued up in. A straight edge on the fret board extension area of the top gave me the perfect 2.5 mm at the saddle that I am looking for.
When I fit the top to the rims it was easy to see that I made a little bit more longitudinal radius than I wanted. as the top needed to be pushed down about a mm at the blocks. It was hard to see this with the rims in the radius board as the neck block extension block the view. No big deal though. I carefully used a combination of a block plane and the radius board to take more off of the middle of the rims, until the top fit perfectly. It now sits on the rims requiring no pressure to hold it down. I also still have the correct body angle to match the required neck angle.
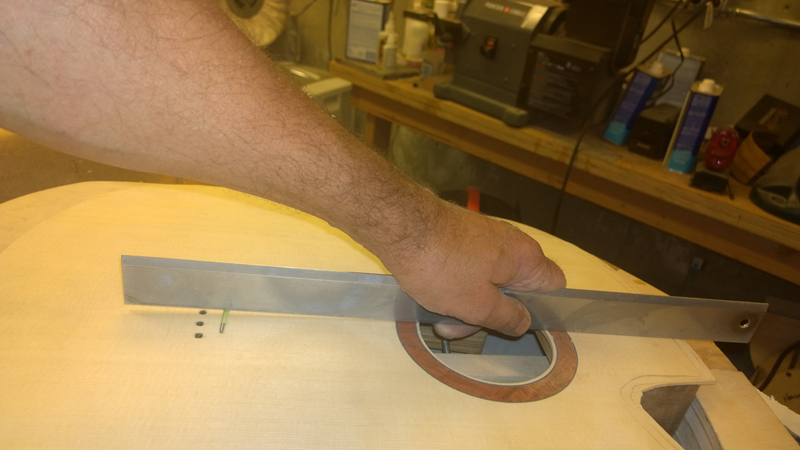
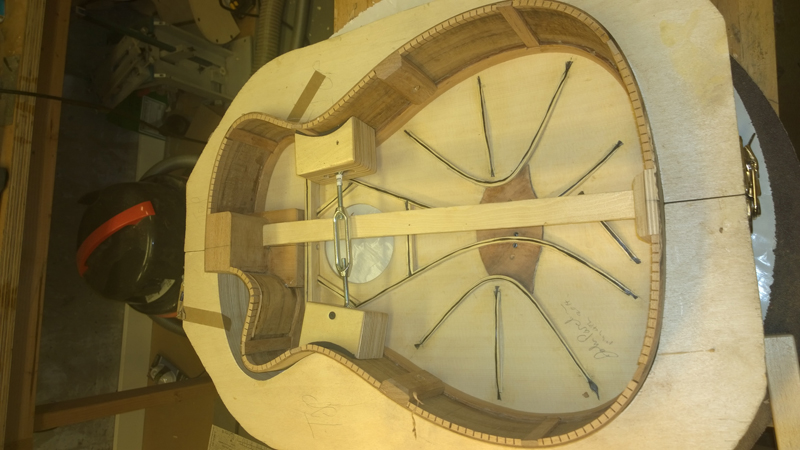
I need to route the rims for the back braces, a bit more cleanup and I can close the box.
-
- Posts: 2754
- Joined: Fri Dec 23, 2011 8:33 pm
- Location: Seattle
- Contact:
Re: continuing build thread for Gore Medium body SS
I closed the box yesterday and today. I did the back first and the top today. In each case I used my radius dish as a gluing caul and cam clamps. I do not have the picture gluing on the back but the guitar was in the mold with spreaders holding the guitar square to the mold. One the back was on the rims with the solid linings for the top no longer need a mold.
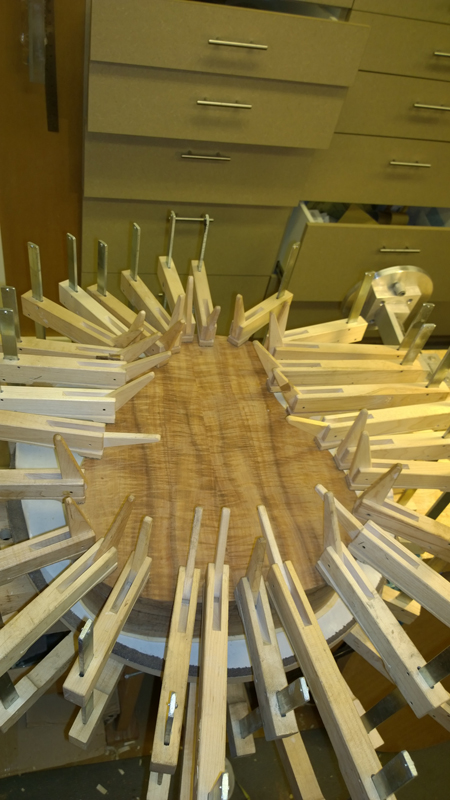
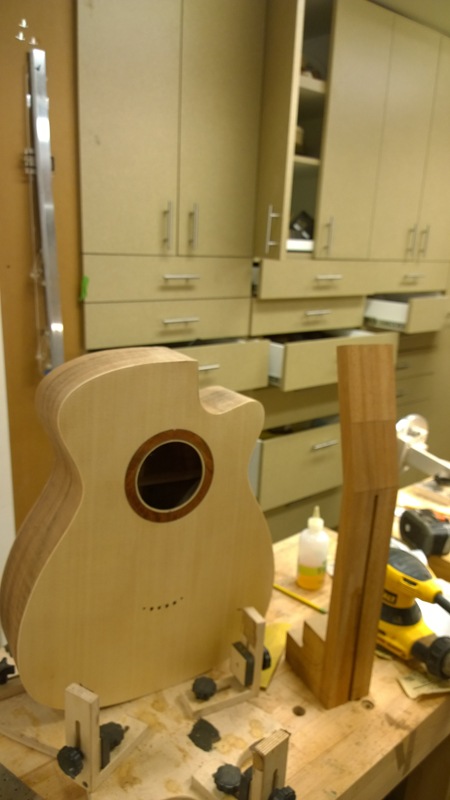
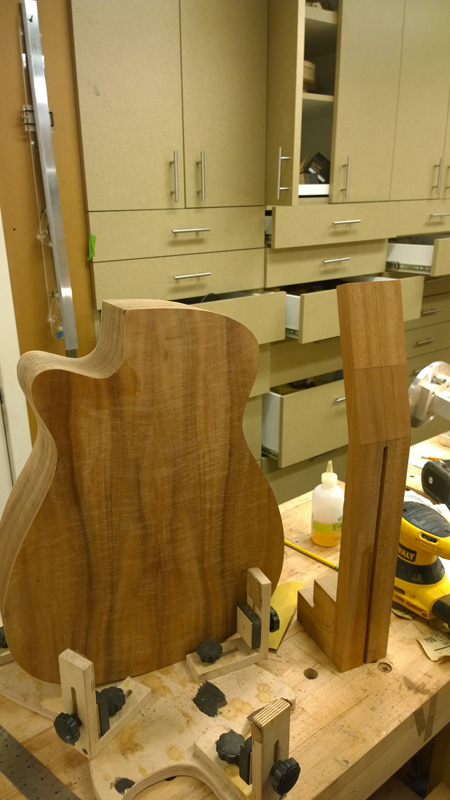
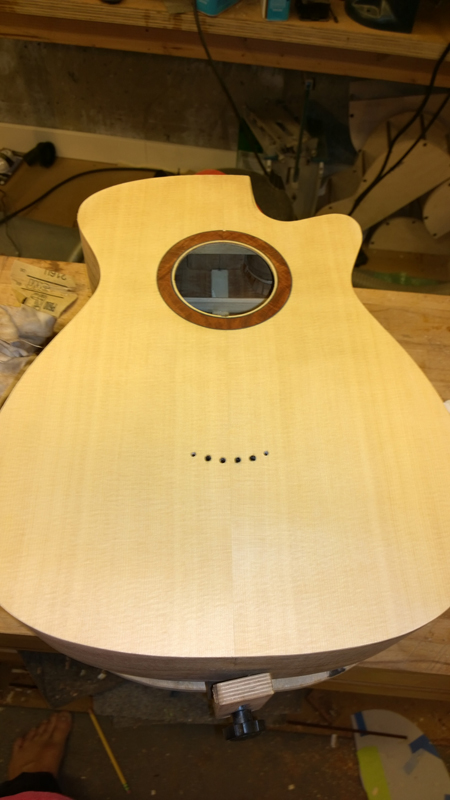
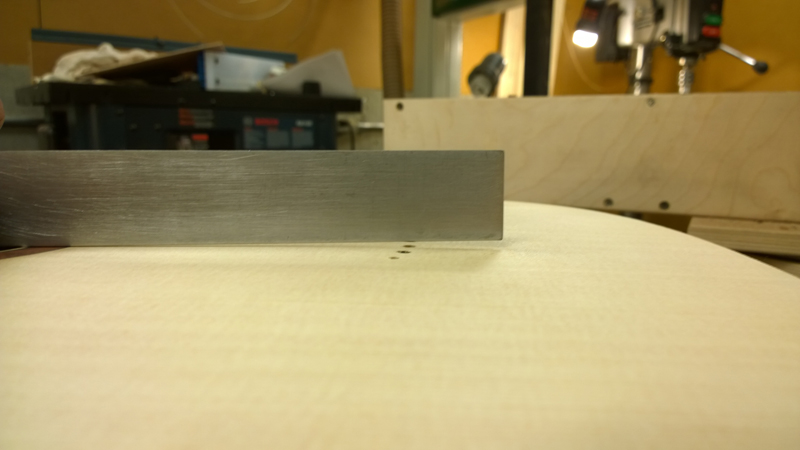
On to the bolt on bolt off neck ...
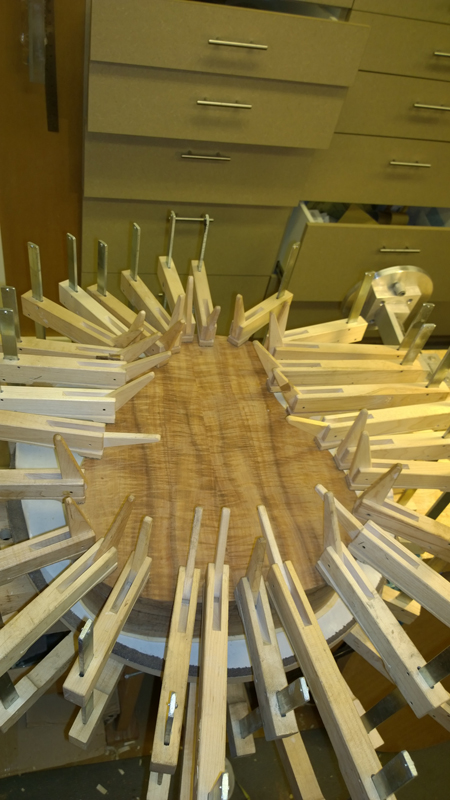
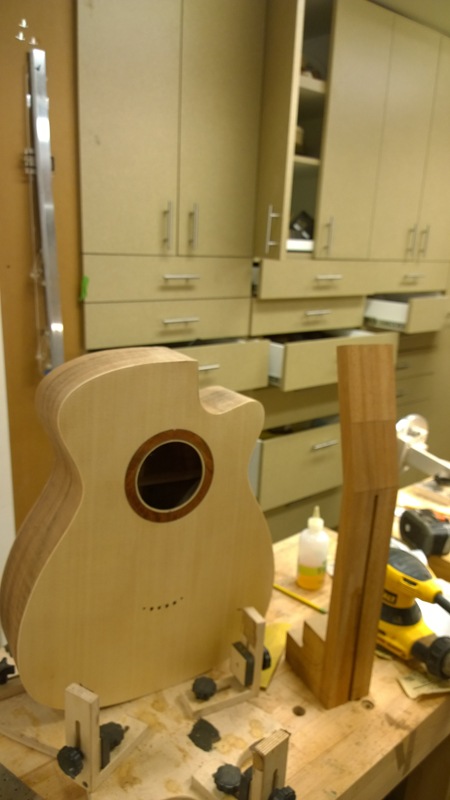
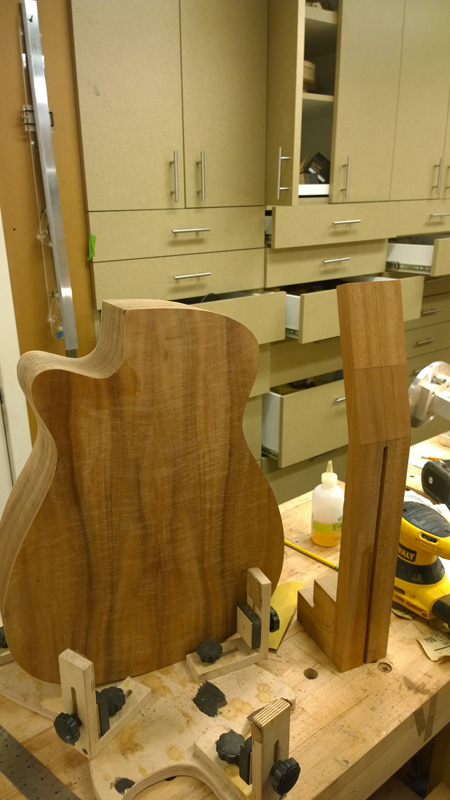
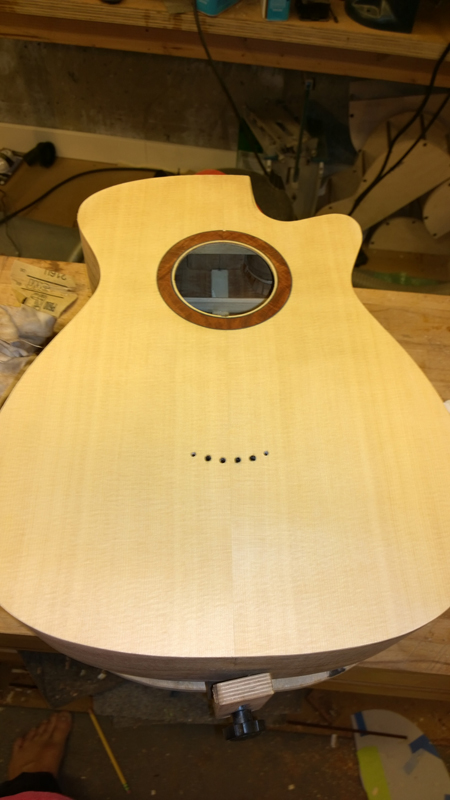
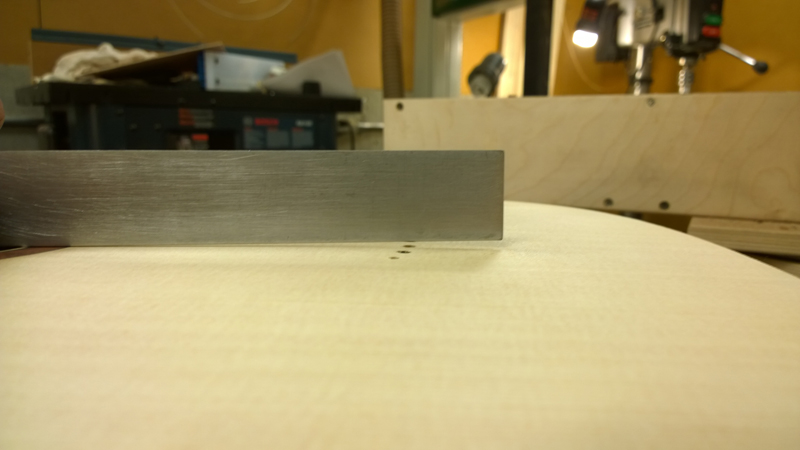
On to the bolt on bolt off neck ...
-
- Posts: 2754
- Joined: Fri Dec 23, 2011 8:33 pm
- Location: Seattle
- Contact:
Re: continuing build thread for Gore Medium body SS
Before I can really start working on the neck I needed to get the body bound and the tail wedge installed. The binding, head stock veneer and tail wedge are all cocobola. I have a thin BWB fiber purfling that matches the rosette that I am using for purfling.
Normally I install the end wedge before I close the box. This time I did not; I started to mark out the wedge before I routed for bindings but stopped when I realized that it would be hard to judge the depth and with no purfling on the back it would be easy to cut into the back. The book has it cut out after binding the guitar, using a set of steel rulers, a marking knife and a chisel to chisel out the waste and to miter the side purflings. I decided that I am not the good with cutting and ultimately I cut and chiseled out the wedge after I cut the binding rebate but before the bindings were glued in. (sorry not a full set of photos.)
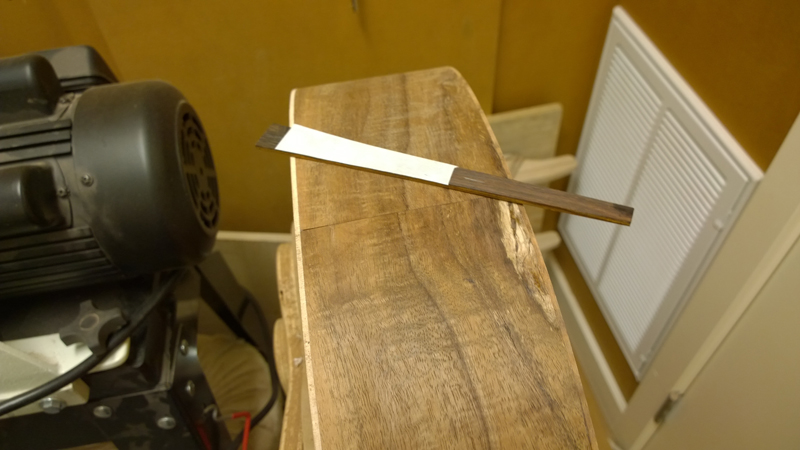
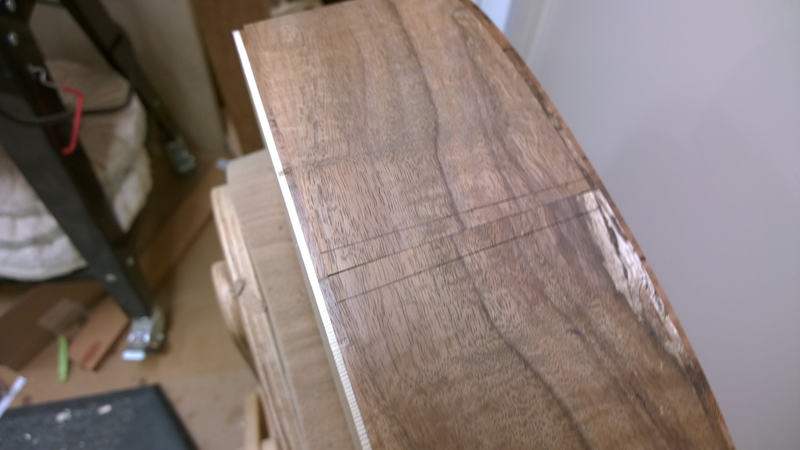
I had to slow down my shop work to build a pretty substantial corrugated steel fence for the hidden sculpture garden my wife designed, 40' by 21' by 7'; mounted on 2" sqr steel posts. The fence is bolted on 24 10" round by 2.5' concrete filled post holes. She offered to hire someone, but I imagined the estimate. The steel will be left to rust and for the most part in short order there will be a lot of clematis and other plants. I had the steel posts custom fabricated. I think I am finished for this season!
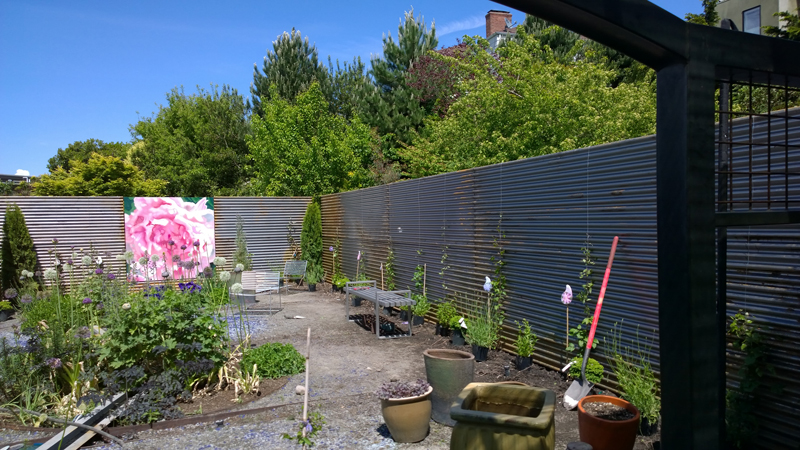
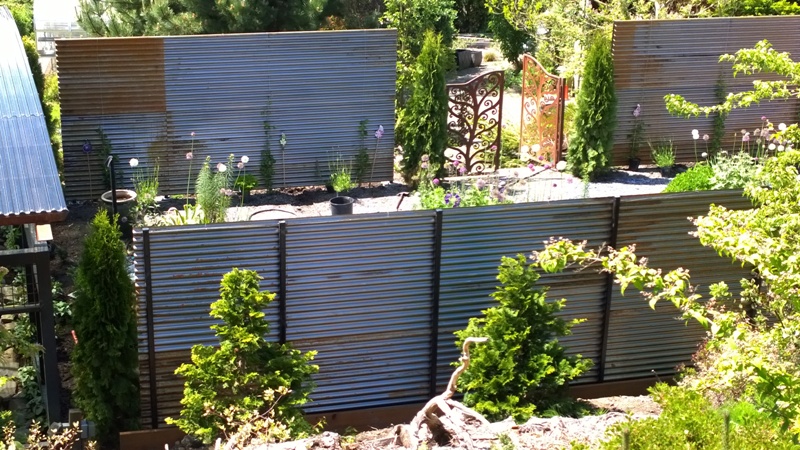
I finally got to bending the bindings for the cutaway one of the tasks that I have been nervous about. I did not have much luck my first try, so I sprayed the bindings with supersoft and waited a day. The super soft really helped, this cut away is really tight. On my previous cut away I softened the curves. Ultimately I did alright and got both bindings bent.
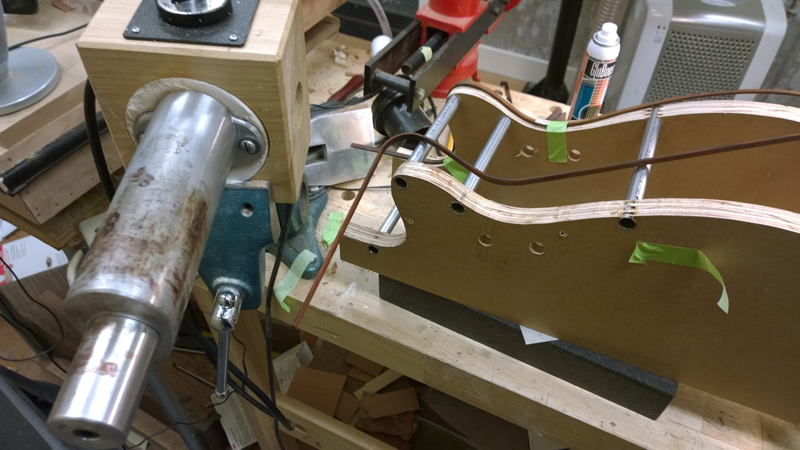
I used high tack fish glue to bind the guitar. I like the slow cure time as it allowed me to bind, first the entire top, following it with a tight wrap. I used a continuous strip for the entire top purfling. I waited a few hours fit and then glued on the back bindings followed with a complete wrap of the guitar with the long rubber strip.
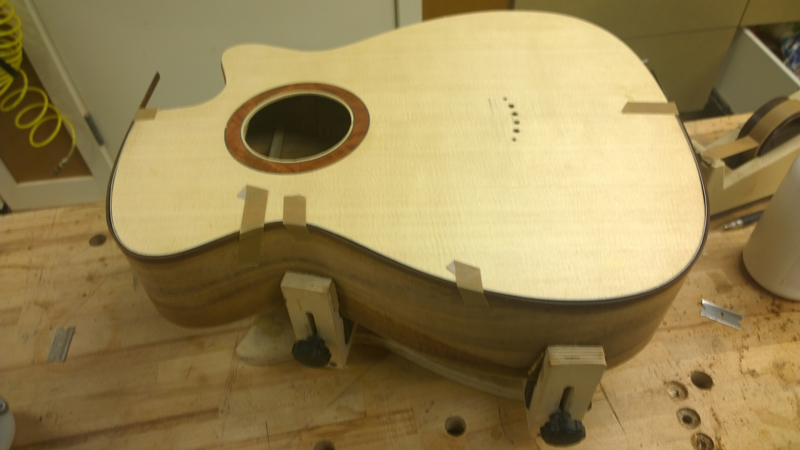
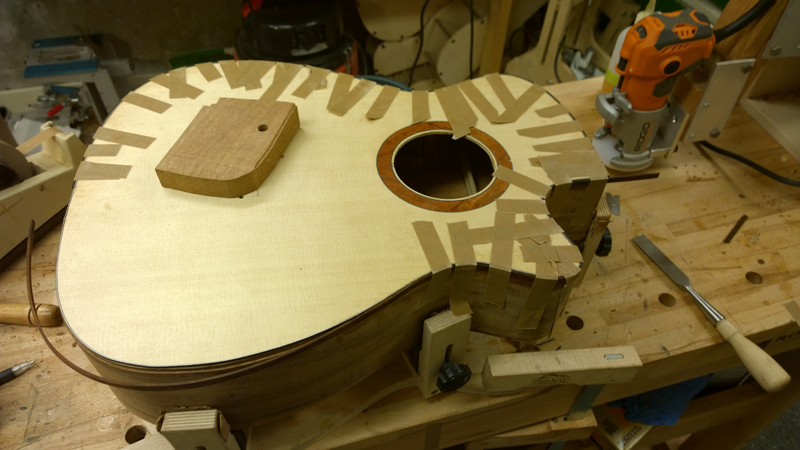
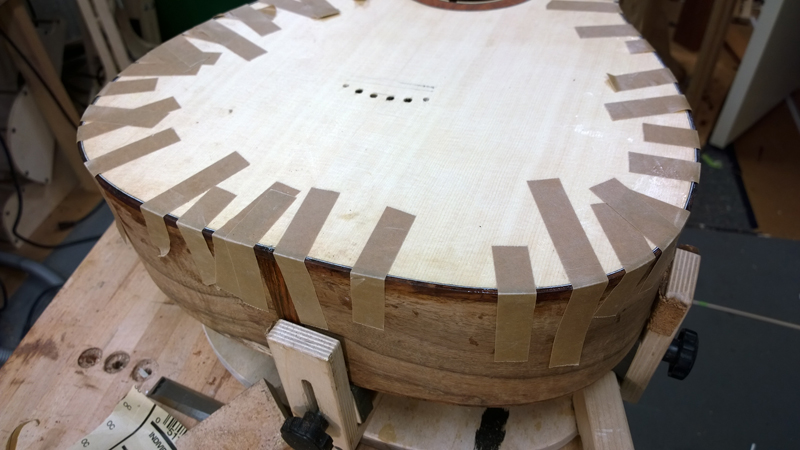
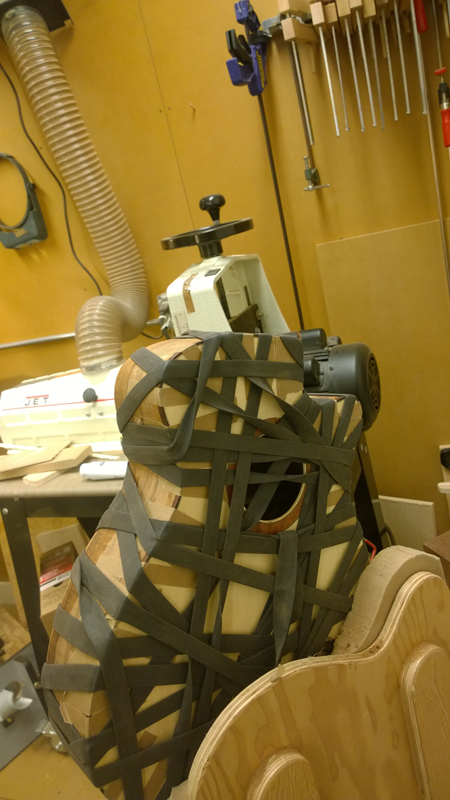
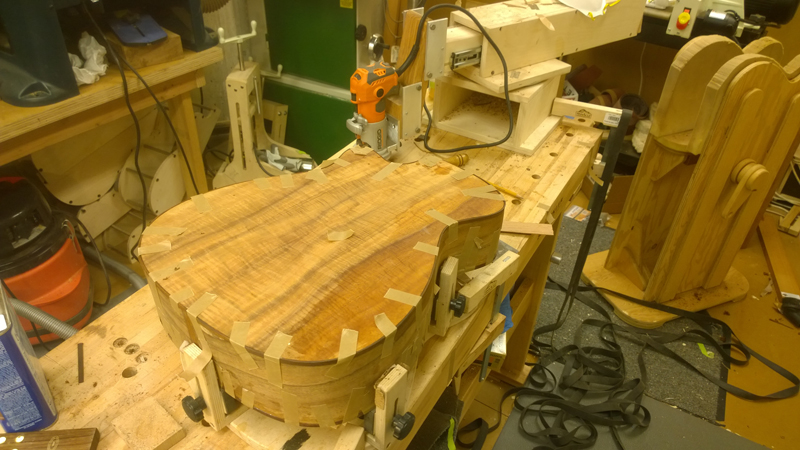
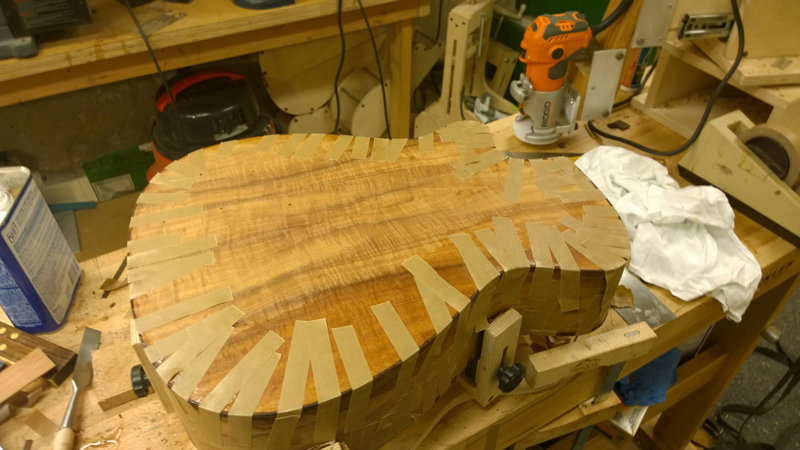
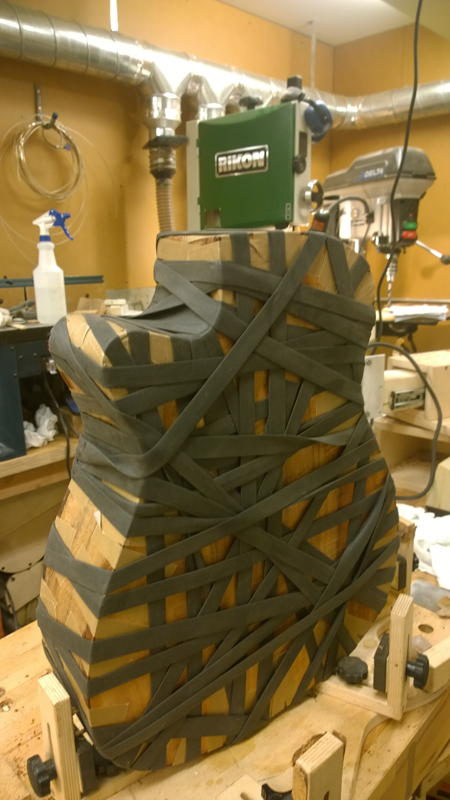
Normally I install the end wedge before I close the box. This time I did not; I started to mark out the wedge before I routed for bindings but stopped when I realized that it would be hard to judge the depth and with no purfling on the back it would be easy to cut into the back. The book has it cut out after binding the guitar, using a set of steel rulers, a marking knife and a chisel to chisel out the waste and to miter the side purflings. I decided that I am not the good with cutting and ultimately I cut and chiseled out the wedge after I cut the binding rebate but before the bindings were glued in. (sorry not a full set of photos.)
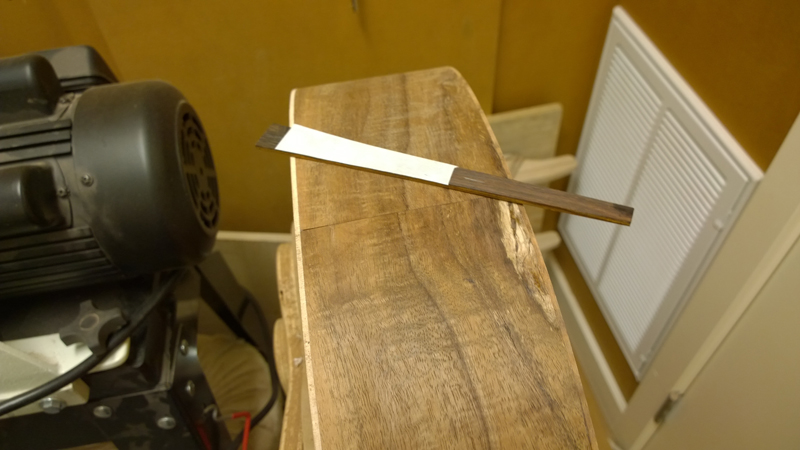
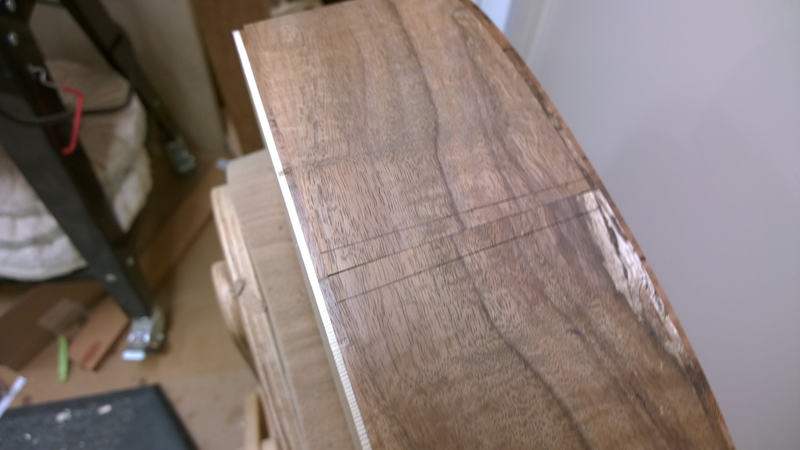
I had to slow down my shop work to build a pretty substantial corrugated steel fence for the hidden sculpture garden my wife designed, 40' by 21' by 7'; mounted on 2" sqr steel posts. The fence is bolted on 24 10" round by 2.5' concrete filled post holes. She offered to hire someone, but I imagined the estimate. The steel will be left to rust and for the most part in short order there will be a lot of clematis and other plants. I had the steel posts custom fabricated. I think I am finished for this season!
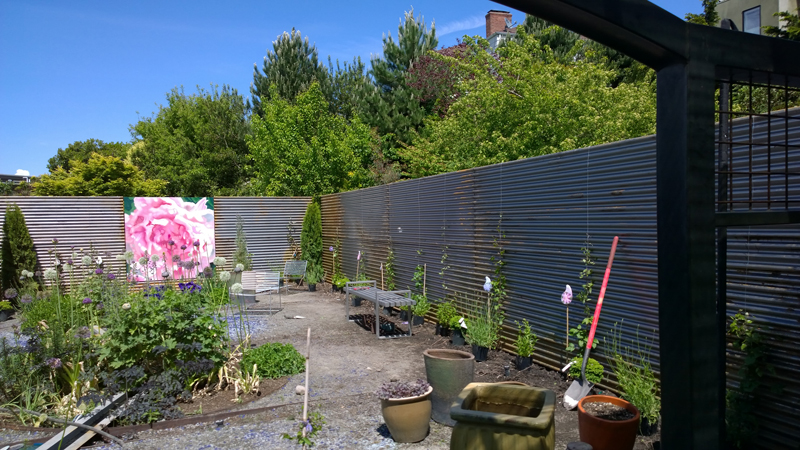
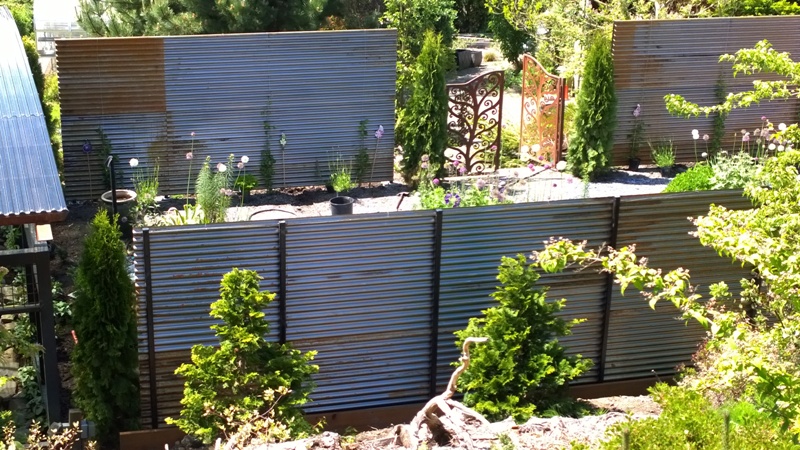
I finally got to bending the bindings for the cutaway one of the tasks that I have been nervous about. I did not have much luck my first try, so I sprayed the bindings with supersoft and waited a day. The super soft really helped, this cut away is really tight. On my previous cut away I softened the curves. Ultimately I did alright and got both bindings bent.
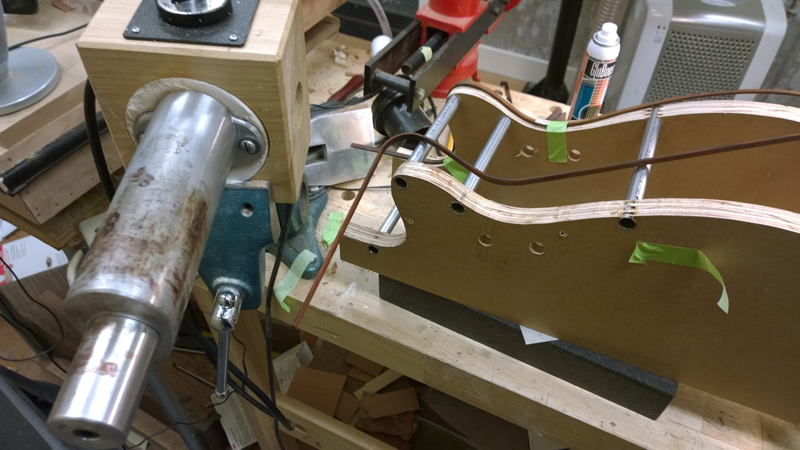
I used high tack fish glue to bind the guitar. I like the slow cure time as it allowed me to bind, first the entire top, following it with a tight wrap. I used a continuous strip for the entire top purfling. I waited a few hours fit and then glued on the back bindings followed with a complete wrap of the guitar with the long rubber strip.
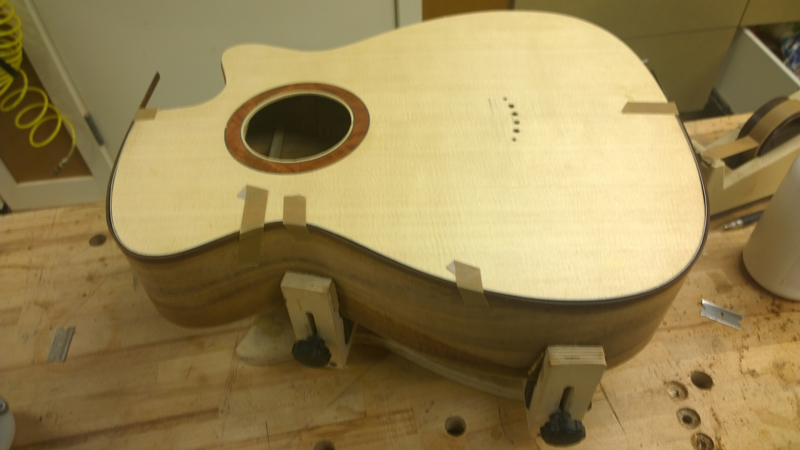
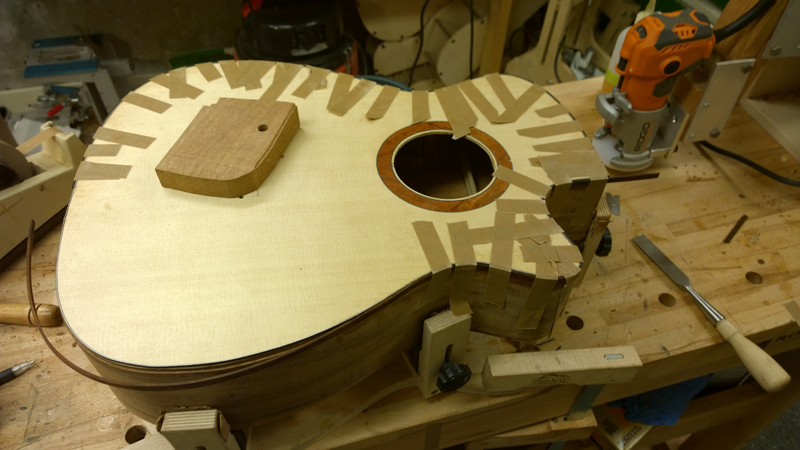
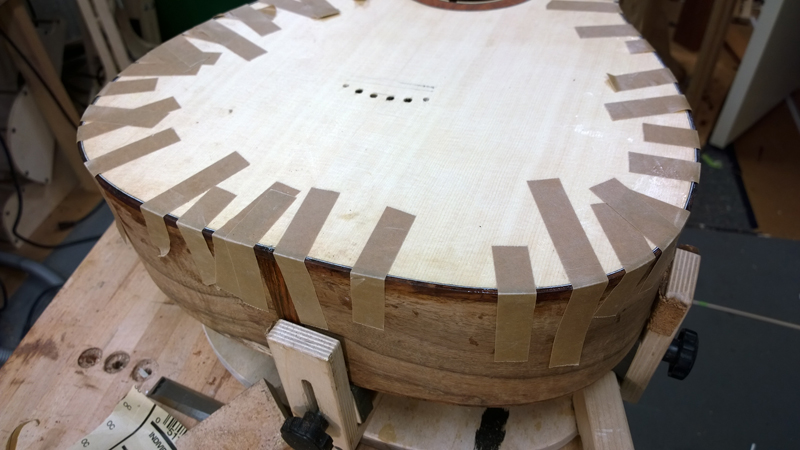
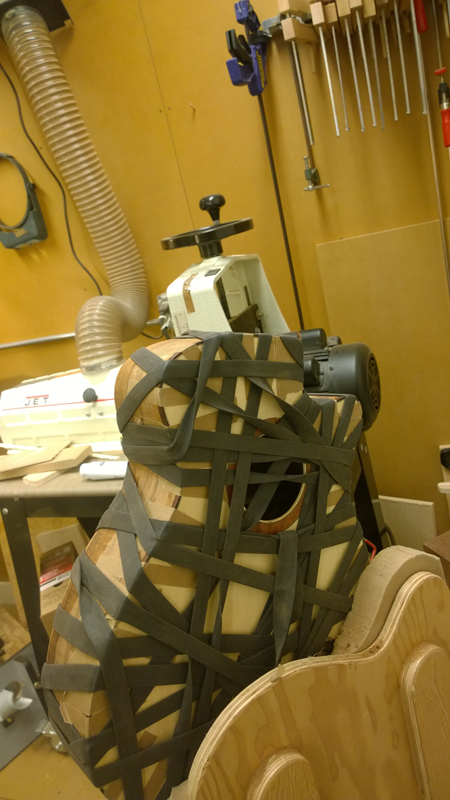
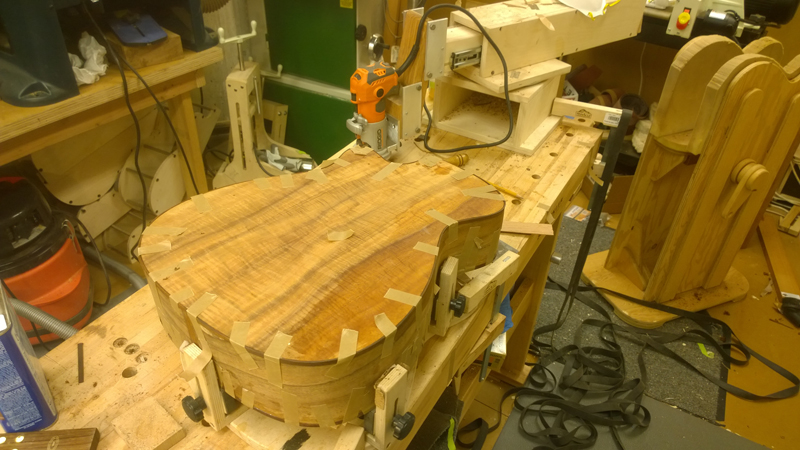
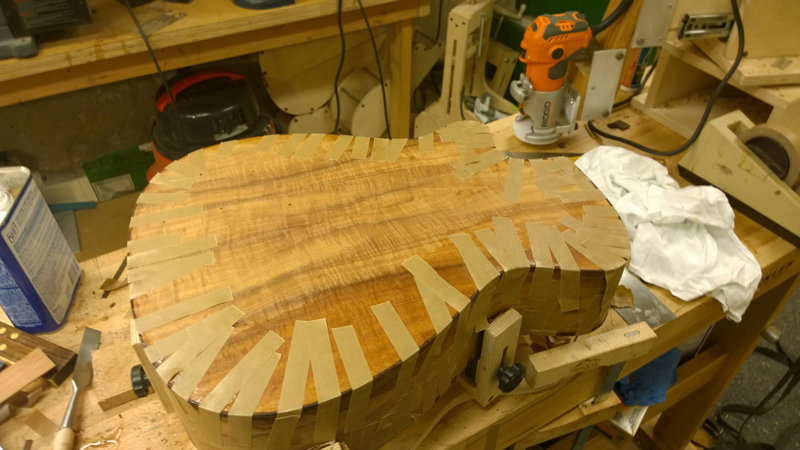
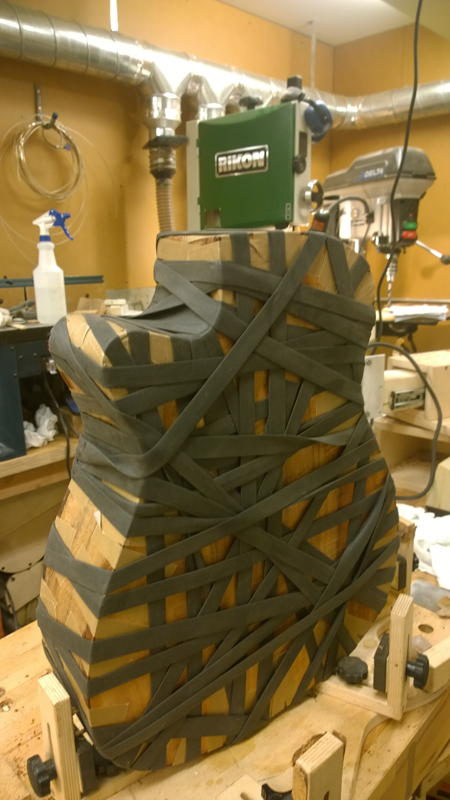