I am not sure why I waited before making an acoustic bridge.
I have been slowly preparing this guitar for finishing. My main concern right now is keeping the maple clean while preparing the rosewood. I have scraped the entire the back and sides and sealed the binding, purfling, back center strip with shellac. I rounded the bindings edges and re applied the shellac. I plan pore fill with z-poxy. To seal the rosewood before I really get going I plan to carefully pad on alcohol thinned Z-poxy. I should be able to create a thin enough coat that I can follow with normal pore filling coats without the need to sand off the seal coat. It might be a nutty idea, but it mimics what I do when I French Polish with shellac and I want to avoid spreading rosewood stained shellac all over.
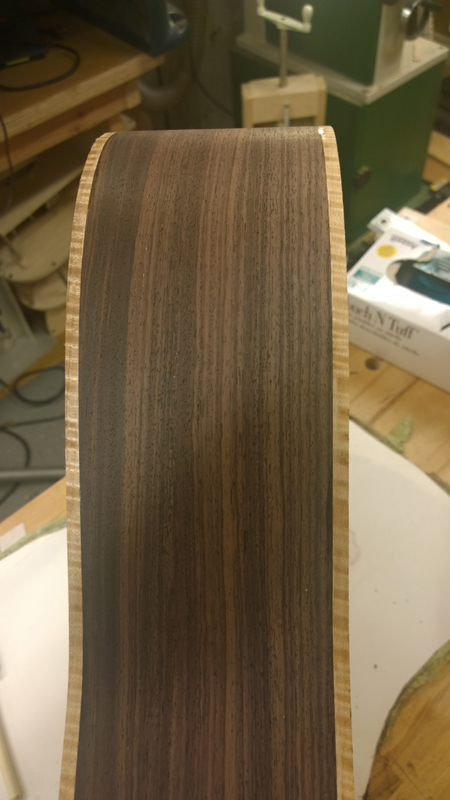
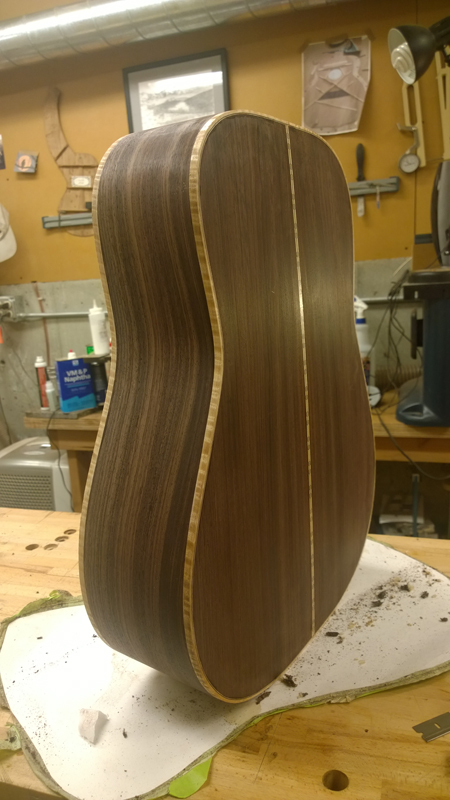
I also made and installed two version of my hawk in moon logo. The first I made with mother of pearl and ebony. I thought that I had installed OK but, when I had it installed there was a hair line crack in the pearl going straight up from the hawks head. Also I wanted to try a black African rosewood hawk instead of the ebony to look better with the Brazilian Rosewood.
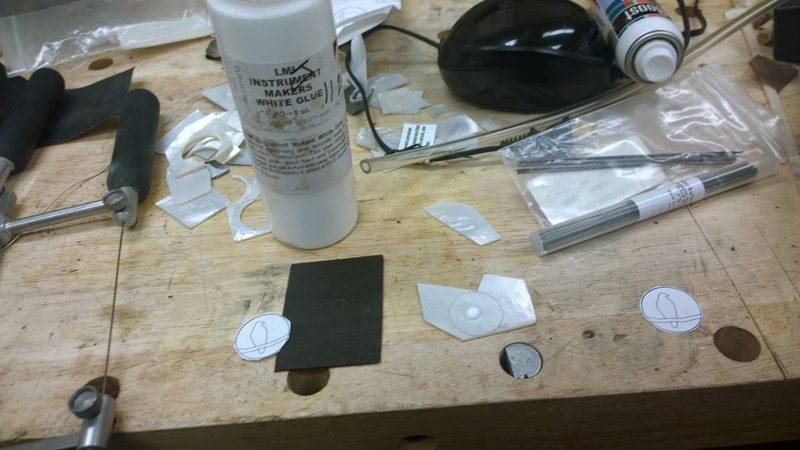
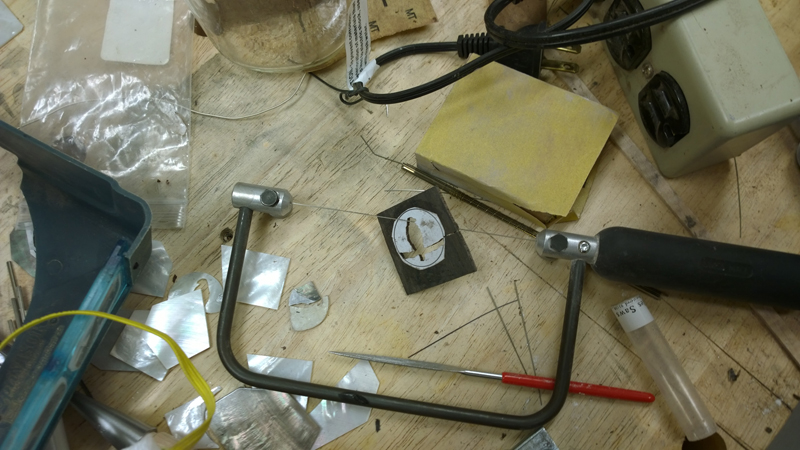
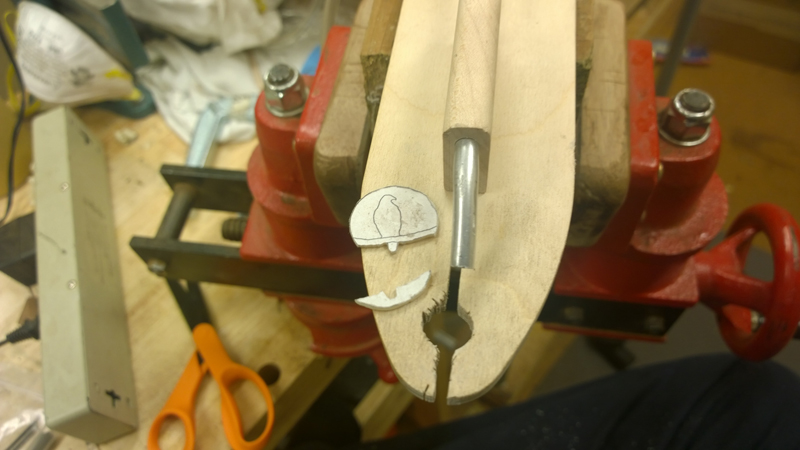
Logo one with ebony would have been Ok except for the crack. It is too small to see in the picture.
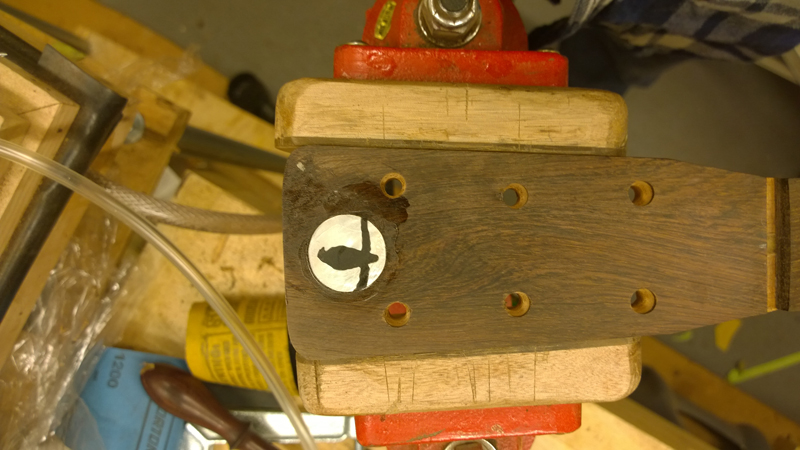
Logo two with a Black African Rosewood hawk. Still is very dark under finish but a nice match with the headstock veneer.
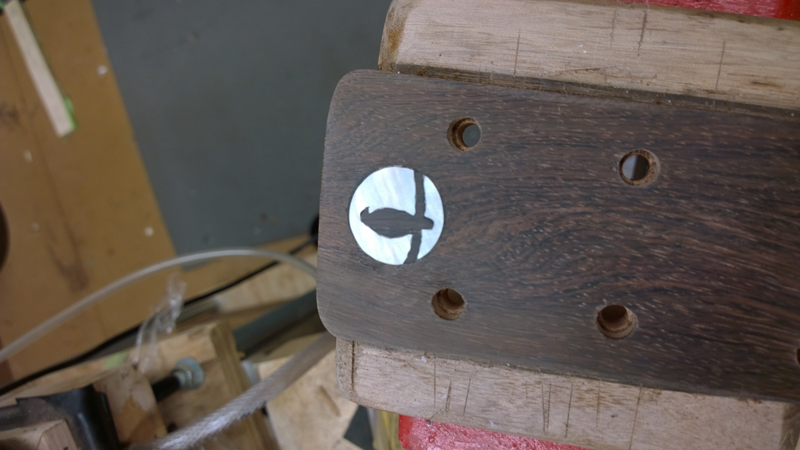
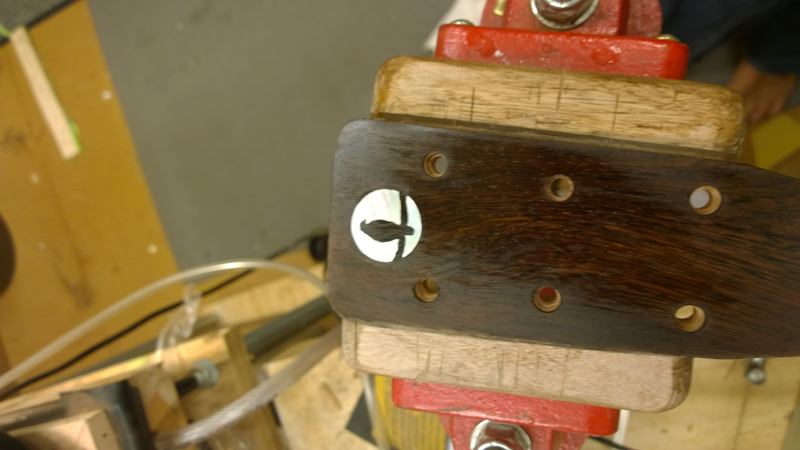