DIY drum sander
-
- Posts: 230
- Joined: Fri Dec 23, 2011 10:37 pm
- Location: Glen Burnie Md
Re: DIY drum sander
I'm not so sure about using pvc. Seems to me the heat from sanding would cause the pvc to easily warp. I made mine out of mdf. It was easy to true up using a peice of mdf covered with 80 grit. As far as holding the paper on, the duct tape I wrapped around each end to try the test run is still holding fine. I have done the back, sides and top on one guitar and various other items. The 3/4 hp motor has been sufficient so far ( it was free ). Cost me about $75 to make and couldn't be happier with it. Of course I've never used a "real" sander so I wouldn't know any better.
Kyle
-
- Posts: 249
- Joined: Wed Jan 04, 2012 12:18 pm
- Location: Chicago Area
- Contact:
Re: DIY drum sander
You know, I never thought of just fixing the ends....thanks! Good idea.
So, my big brother was playing guitar and I figured I'd try it too.
- Stevie Ray Vaughan
http://www.nocturnalguitars.com
- Stevie Ray Vaughan
http://www.nocturnalguitars.com
Re: DIY drum sander
One drum sander that I actually constructed using PVC , and that I actually used "professionally" for a couple of years had no problems at all with the drum warping. As a mentioned don't over think the thing -- The PVC is not hanging in free space like a drain pipe -- its a supported drum attached to several round disks and a shaft. Being sorta of hollow I believe it does somewhat self cool.
I will say that the heavy multi-disk MDF roller is good as well. If we (KMG) do decide to offer some drum sander parts or a complete kit like the drum will likely be made of MDF.
A DIY sander should have a rather long in/out table -- this makes it easier to manually feed the
material.
As I mentioned previously above -- the 3/4" or 1" filament reinforced packaging tape is what "Grizzly" instructs it buyers to use to secure the abrasive to the drum on each end.
I will say that the heavy multi-disk MDF roller is good as well. If we (KMG) do decide to offer some drum sander parts or a complete kit like the drum will likely be made of MDF.
A DIY sander should have a rather long in/out table -- this makes it easier to manually feed the
material.
As I mentioned previously above -- the 3/4" or 1" filament reinforced packaging tape is what "Grizzly" instructs it buyers to use to secure the abrasive to the drum on each end.
ken cierp
http://www.kennethmichaelguitars.com/
Store Front
http://www.cncguitarproducts.com/
KMG Guitar Kit Information
http://www.kennethmichaelguitars.com/ki ... ckage.html
http://www.kennethmichaelguitars.com/
Store Front
http://www.cncguitarproducts.com/
KMG Guitar Kit Information
http://www.kennethmichaelguitars.com/ki ... ckage.html
Re: DIY drum sander
The clamps are actually snug against the disk -- mine had only the center disk secured to the shaft in this manner, I had zero problems but two might be better
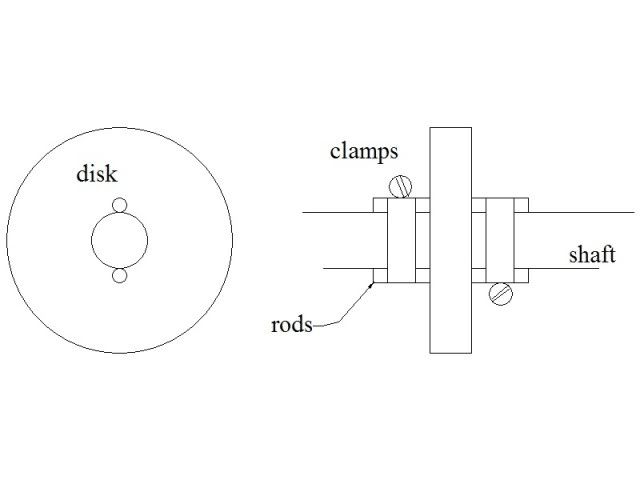
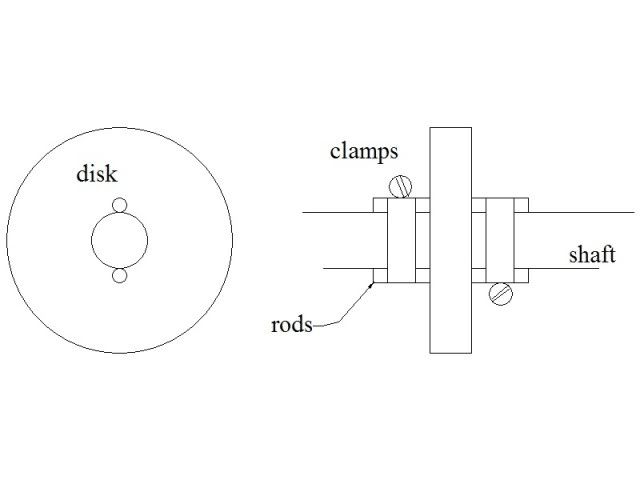
ken cierp
http://www.kennethmichaelguitars.com/
Store Front
http://www.cncguitarproducts.com/
KMG Guitar Kit Information
http://www.kennethmichaelguitars.com/ki ... ckage.html
http://www.kennethmichaelguitars.com/
Store Front
http://www.cncguitarproducts.com/
KMG Guitar Kit Information
http://www.kennethmichaelguitars.com/ki ... ckage.html
-
- Posts: 5952
- Joined: Tue Dec 13, 2011 7:44 pm
-
- Posts: 5952
- Joined: Tue Dec 13, 2011 7:44 pm
Re: DIY drum sander
Here's a pic of the general idea of the tablesaw - driven sander.
- Attachments
-
- IMG_1257.jpg (65.51 KiB) Viewed 1081 times
-Under permanent construction
-
- Posts: 167
- Joined: Tue May 08, 2012 7:30 pm
- Location: Southern IN
Re: DIY drum sander
Thank you for this thread; it already contains a lot of good info.
A drum width of 24" seems to be suitable for a variety of needs.
Hopefully a 1.5 HP motor would be adequate- I have extras of those, eliminating the expense of a different motor. Perhaps that's wishful thinking there, as the completed drum will probably weigh 25-30 pounds, and the proposed span is a good bit of surface area. But we'll see. I plan on upgrading one of the saws with a 5 HP motor in the future, so that would free up the 3 HP currently on it.
At the risk of sounding like I'm overthinking the drum construction, I am pondering the importance of central internal drum support should the drum material be aluminum or steel.
The goal is to produce a drum of reasonable quality with presently available material while reducing the need for outside machine shop services ($$). I may end up having to pay for the outer diameter of the drum to be trued; will have to check that after assembly.
The tubing checks good for roundness; if I can minimize eccentricity I should be OK.
For the shaft, I have about 3 feet of 1.5" stressproof 1144. Also have the bearings to fit this.
To affix the drum to the shaft, I was considering the use of interchangeable-bore sheaves (pulleys). I have extras of these in various diameters that would fit inside the tubing with a minor amount of work. I have compared outside diameter of the sheaves (endcaps?) to inside diameter of my available tubing, and I think I can get it to fit with minor grinding of the sheaves instead of paying for the service of turning down diameter in a lathe. It's very close.
Or I could make the endcaps out of MDF. Simple enough, but I think it would be about the same amount of effort. The use of MDF would present the same problem of clamping to the shaft as disk-type construction, whereas the sheaves offer the option of both setscrews and keys. I think it's "six of one, half a dozen of the other".
After achieving a good fit, a variety of methods could be used to lock the drum onto the endcaps. I considered the use of small screws.
For the drum itself, I have aluminum in 5" OD, 4.25" ID (3/8" wall).
I also have a piece of steel tubing in 4" OD, 3.75" ID (1/8" wall).
Considering the desired span (24"), would either of these suffice without need for additional support in the center of the drum?
If the aluminum tube is used and central support is needed, that means a trip to the machine shop ($$) to get the inside diameter bored/honed in order to remove the weld flash. Whereas if no center support is needed, I could clean up the seams at the outer ends of the tube at home, then slip in the endcaps.
The steel is DOM tubing (drawn over mandrel), so no internal weld flash. Still, it would be nice to avoid the need of "fitting" a third piece for the center.
I have no actual experience with this. Obviously the goal is to minimize flex. The main shaft is probably more than enough, maybe even overkill, but it's what I have. Dealing with the issue of center support for the tubing is what has me overthinking.
Any thoughts on this, both good and bad?
By the way, these are items I already have from past projects. It would be nice to find good use for them, plus have a drum that minimizes (or even eliminates) need for periodic retruing. It would also eliminate the labor to cut and glue disks for drum construction.
But if I didn't already have this stuff, I would definitely be using MDF disks. Today's prices for my proposed materials are simply unbelievable!
Thanks,
Rob
A drum width of 24" seems to be suitable for a variety of needs.
Hopefully a 1.5 HP motor would be adequate- I have extras of those, eliminating the expense of a different motor. Perhaps that's wishful thinking there, as the completed drum will probably weigh 25-30 pounds, and the proposed span is a good bit of surface area. But we'll see. I plan on upgrading one of the saws with a 5 HP motor in the future, so that would free up the 3 HP currently on it.
At the risk of sounding like I'm overthinking the drum construction, I am pondering the importance of central internal drum support should the drum material be aluminum or steel.
The goal is to produce a drum of reasonable quality with presently available material while reducing the need for outside machine shop services ($$). I may end up having to pay for the outer diameter of the drum to be trued; will have to check that after assembly.
The tubing checks good for roundness; if I can minimize eccentricity I should be OK.
For the shaft, I have about 3 feet of 1.5" stressproof 1144. Also have the bearings to fit this.
To affix the drum to the shaft, I was considering the use of interchangeable-bore sheaves (pulleys). I have extras of these in various diameters that would fit inside the tubing with a minor amount of work. I have compared outside diameter of the sheaves (endcaps?) to inside diameter of my available tubing, and I think I can get it to fit with minor grinding of the sheaves instead of paying for the service of turning down diameter in a lathe. It's very close.
Or I could make the endcaps out of MDF. Simple enough, but I think it would be about the same amount of effort. The use of MDF would present the same problem of clamping to the shaft as disk-type construction, whereas the sheaves offer the option of both setscrews and keys. I think it's "six of one, half a dozen of the other".
After achieving a good fit, a variety of methods could be used to lock the drum onto the endcaps. I considered the use of small screws.
For the drum itself, I have aluminum in 5" OD, 4.25" ID (3/8" wall).
I also have a piece of steel tubing in 4" OD, 3.75" ID (1/8" wall).
Considering the desired span (24"), would either of these suffice without need for additional support in the center of the drum?
If the aluminum tube is used and central support is needed, that means a trip to the machine shop ($$) to get the inside diameter bored/honed in order to remove the weld flash. Whereas if no center support is needed, I could clean up the seams at the outer ends of the tube at home, then slip in the endcaps.
The steel is DOM tubing (drawn over mandrel), so no internal weld flash. Still, it would be nice to avoid the need of "fitting" a third piece for the center.
I have no actual experience with this. Obviously the goal is to minimize flex. The main shaft is probably more than enough, maybe even overkill, but it's what I have. Dealing with the issue of center support for the tubing is what has me overthinking.
Any thoughts on this, both good and bad?
By the way, these are items I already have from past projects. It would be nice to find good use for them, plus have a drum that minimizes (or even eliminates) need for periodic retruing. It would also eliminate the labor to cut and glue disks for drum construction.
But if I didn't already have this stuff, I would definitely be using MDF disks. Today's prices for my proposed materials are simply unbelievable!
Thanks,
Rob
Always have plenty of sandpaper; it's rough out there!