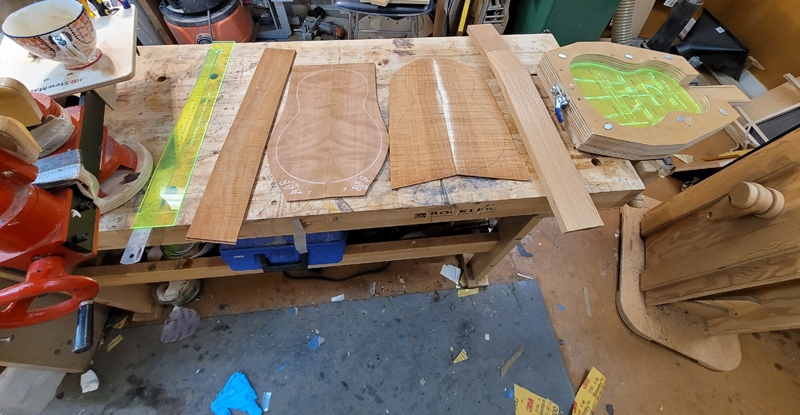
I started on the neck blank. I am sorry I did not take a lot of pictures. I started with scarfed jointed blank I had in my stash and using a plane thicknessed the head stock from the top and then tapered and thicknesses the fretboard face of the blank. These two complementary actions kept the scarf joint end right under the nut location. I had a small block of mahogany that I am using for a built up heel.
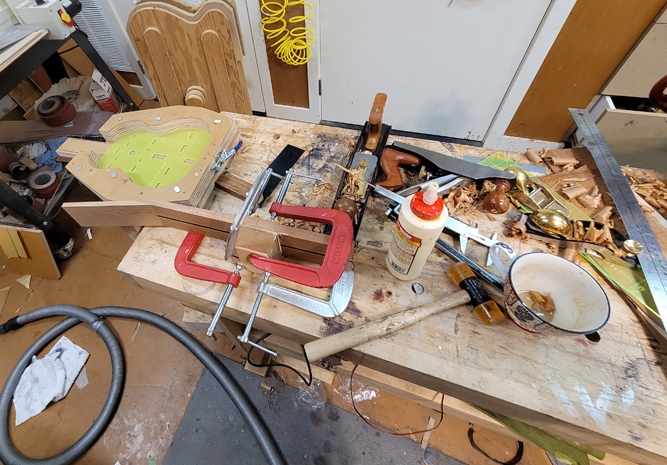
The ukulele plates are a bit small to work well in my LMI jointer jig, so I used a tensioned tape jointing method.
I used a plane and a shooting board to clean up the edges for gluing and then with the plates tilted relative to each other taped, glued and flattened them. Then tension from stretching the tape holds the plates together until the glue cures.
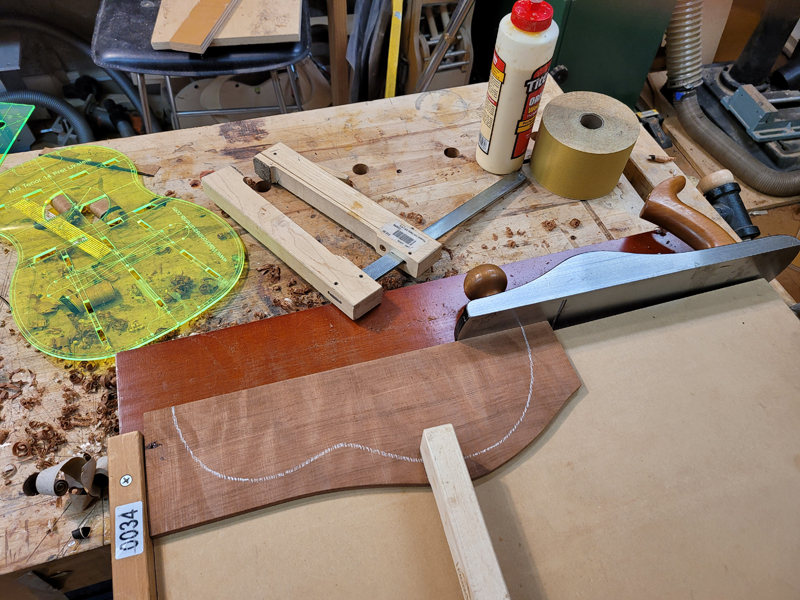
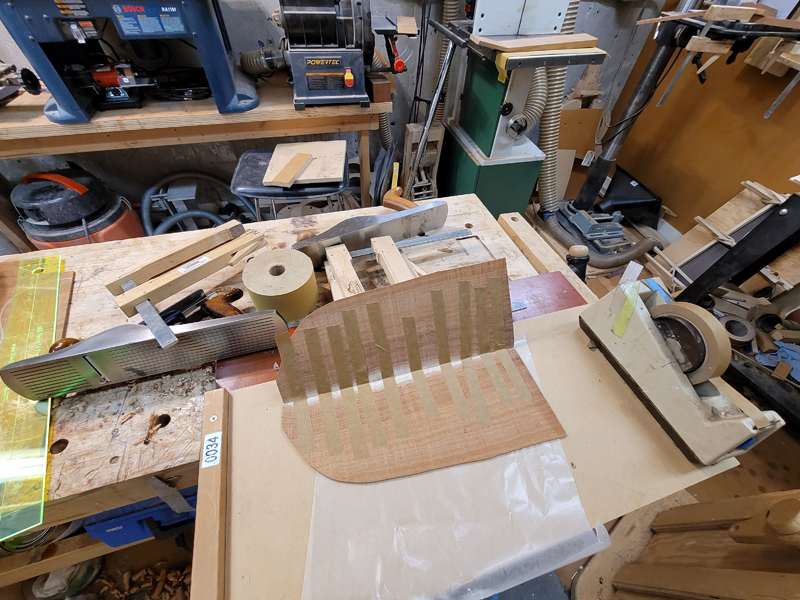
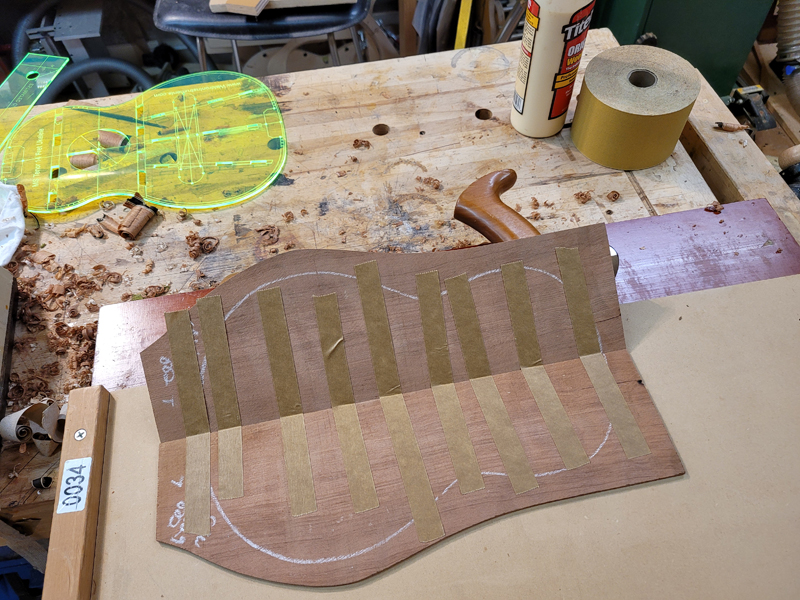
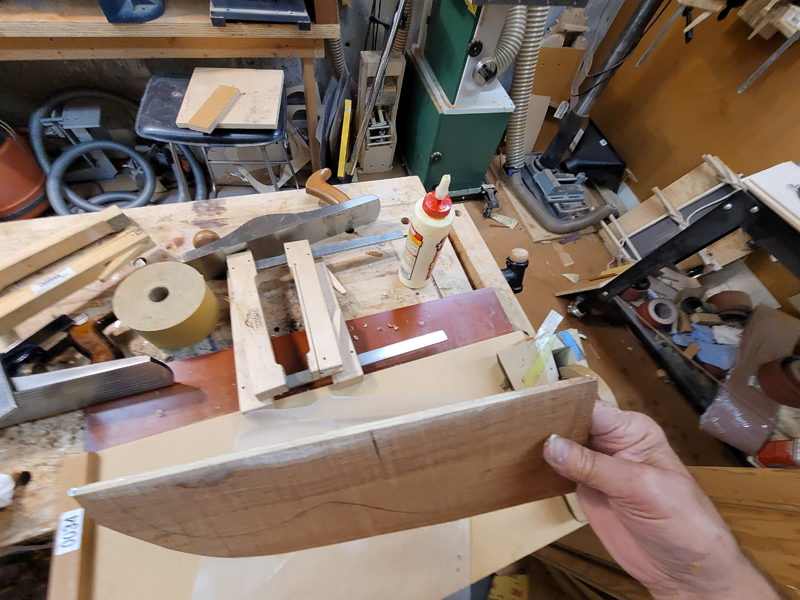
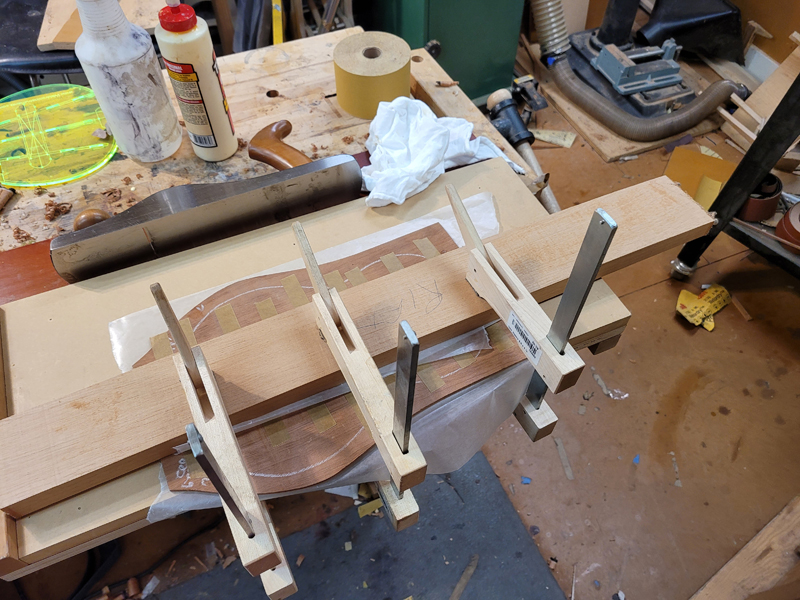
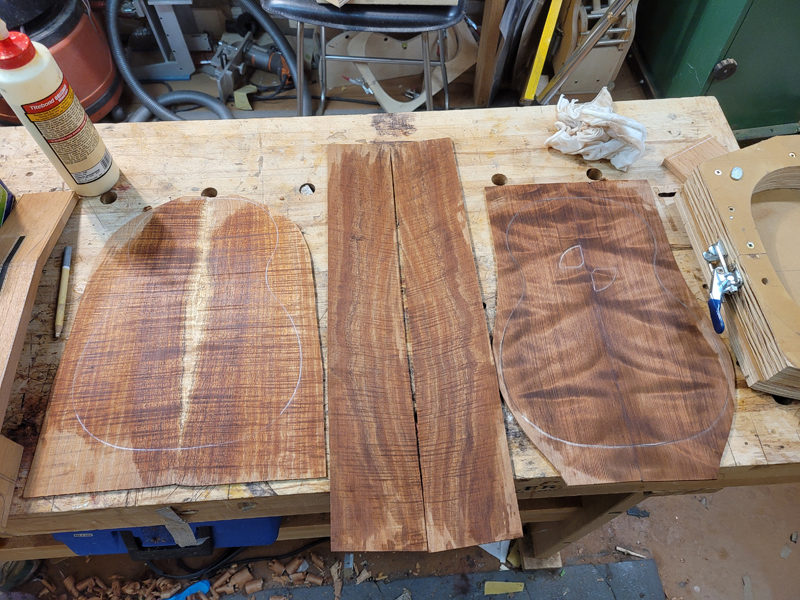
I started to lay out the neck but had to stop there.
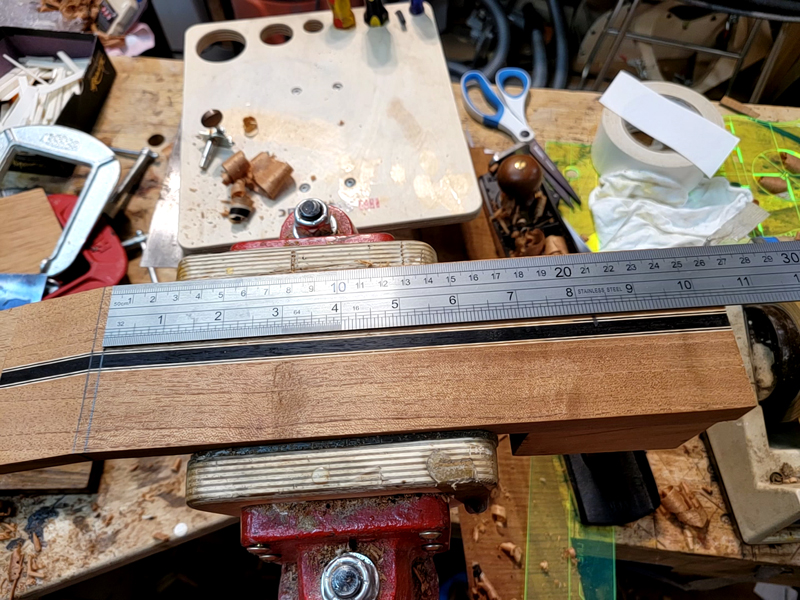