For this process I needed two good representative rectangular samples of the back plates for a long grain stiffness value and a cross grain stiffness measurement. As you could see in the first photo. I was able to create a square section on one of the plates. Also after taking a long grain deflection I will have enough length to cut off a rectangular section of the same plate.
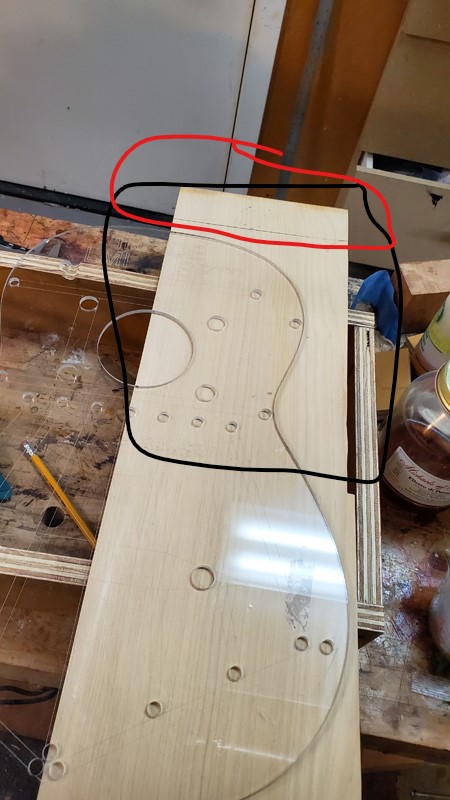
Previously I have built a deflection jig that allows me to take deflection measurements on a variety of span lengths. So first off I measured the long grain deflection under a measured load.
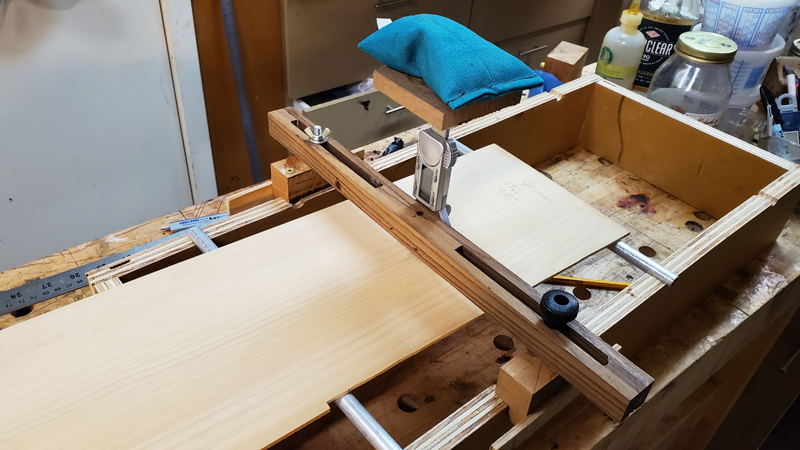
Next I cut off a 50 mm or so rectangular section off of the plate, set up the deflection jig and measured the cross grain deflection
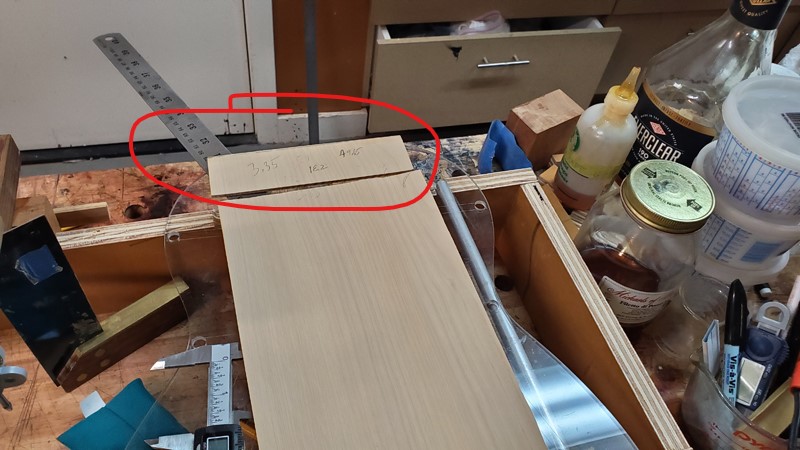
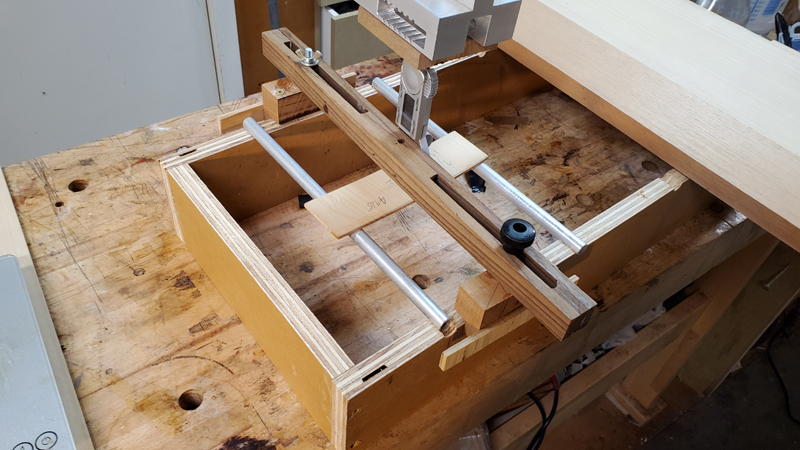
The last additional bit of information I needed was the density of the wood. To determine the density of the wood I needed the mass of the cross grain sample.
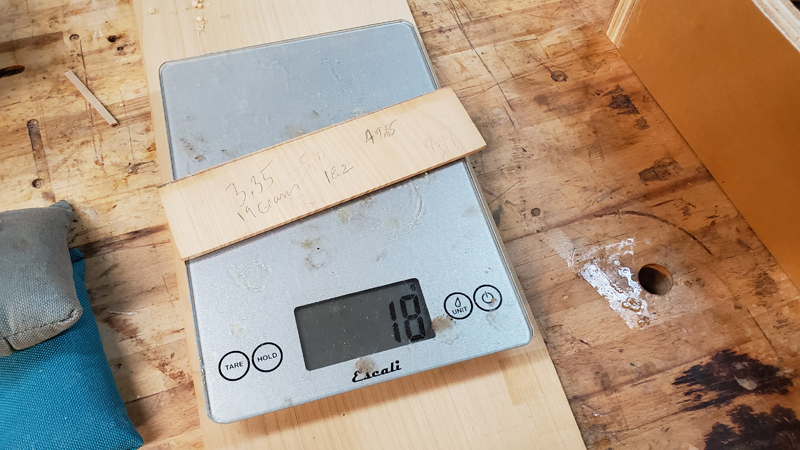
The last step was to modify my previously spreadsheet for calculating target thickness using tap frequencies to use deflection based young's modulus calculations. Luckily I had a handy spreadsheet from the Modal Tuning with Trevor Gore class I took at Robbie's place to calculate the long and cross grain young's modulus for the plate. The book also has the information needed to make these calculations. I substituted the deflection based El and Ec calculations for the frequency calculations in my original spreadsheet and set the Elc to an average value. This term has little effect in the overall calculation. With all the required inputs I got what looks like a good thickness target for the plate. This target is very close to my frequency based target from my first flamenco guitar using spanish cypress. So it seems like the method worked well.

Just for reference here is the spreadsheet for my tap baised thickness calculation for the top plates on this guitar.
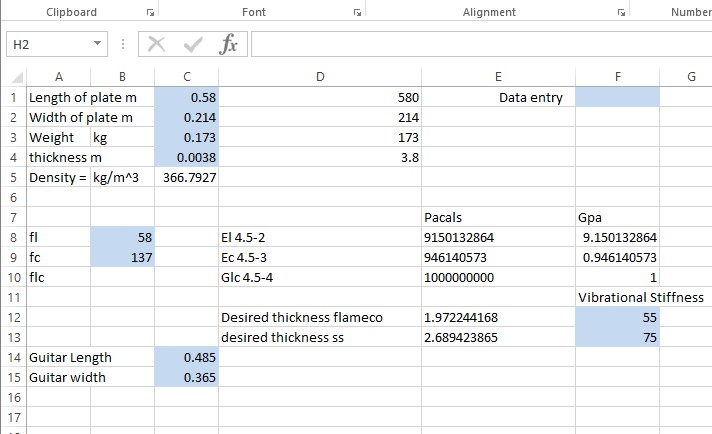
With the properties of the tone wood I was in a position to joint both plates.
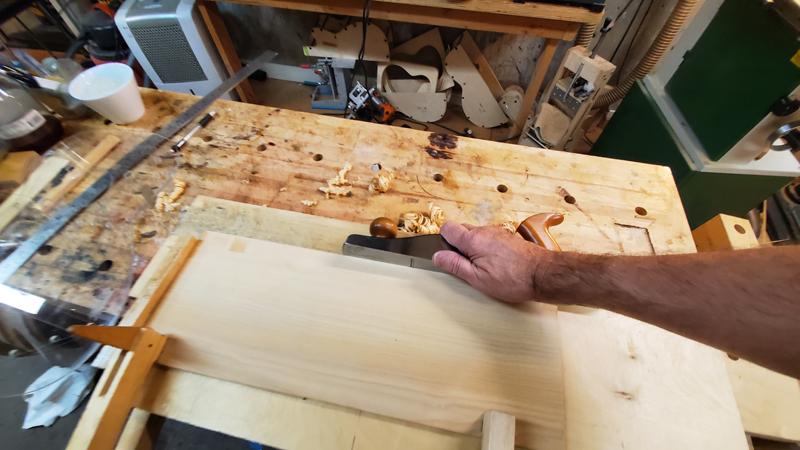
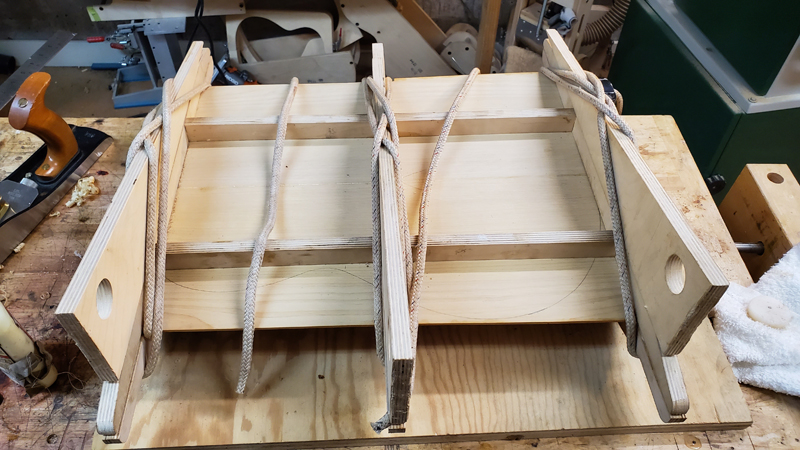
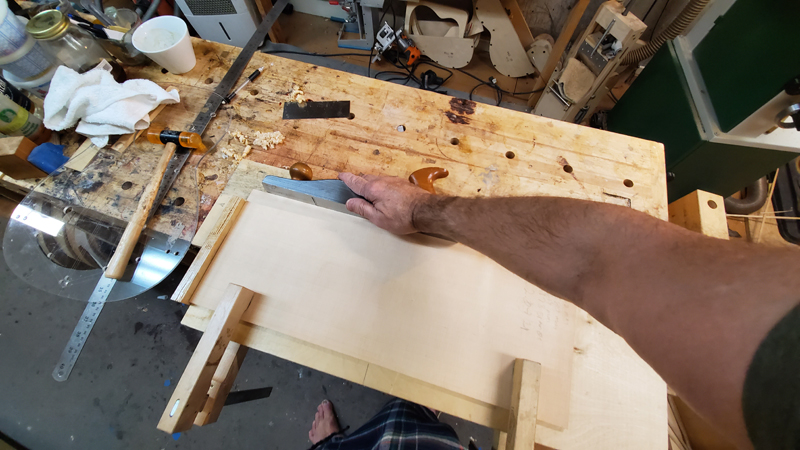
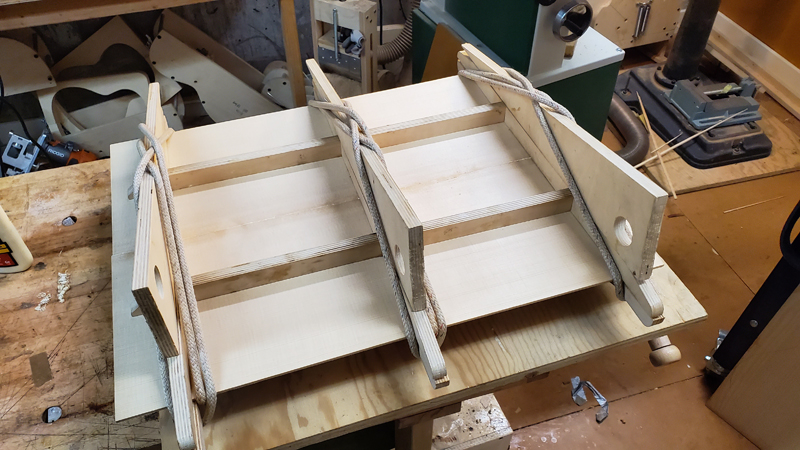