Dave, I love that guitar. I could see how the lack of bindings in the back works. I have worked on old Martin Guitars without bindings. I wonder if they are a bit more work as the top and back joint needs to be really good. Generally I am happy if they are glued on the linings and often there is a gap between the rims and the top or back. With bindings it get routed away.
More progress on the flamenco.
I used my Micro Mill to rough out a bridge.
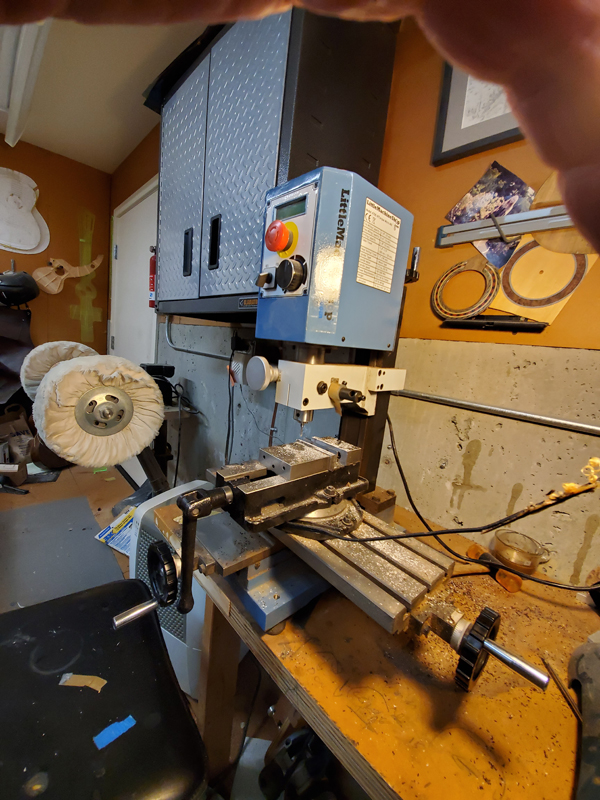
I have been working with a 1/8" end mill. Here are some pictures of me making the bridge with some descriptions
I work the tie block starting with the bottom of the bridge and work forward into the bridge. That way I can keep going in the same y direction without having to come back and zero. The tool is accurate to .001" if you deal with the backlash. So my first cut is a 2 mm deep cut 2 mm in for the tie block bone strip.
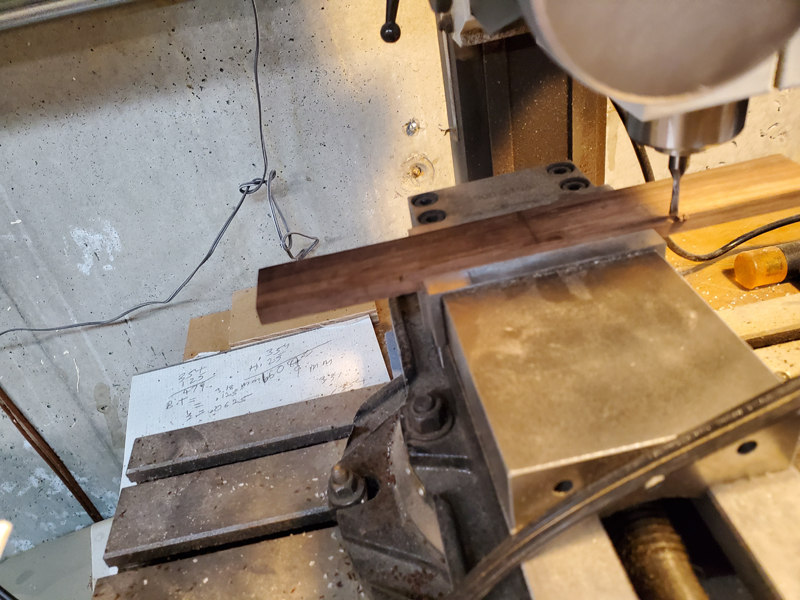
Testing the size
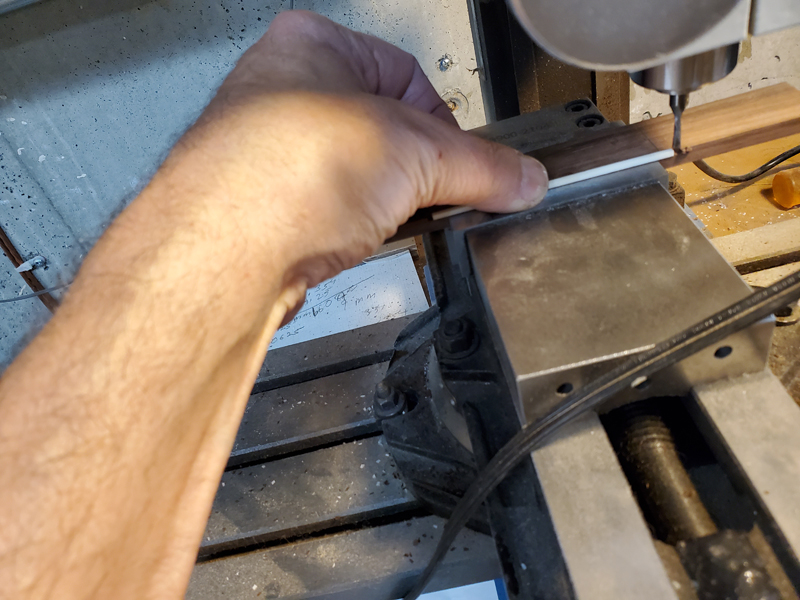
The next cut is the for the inside tie block strip. I am constantly converting mm to mils. So to move forward I wanted the back of the end mill to end up at 8 mm in. Once I calculated the distance I crank it in 50 mils per turn. I have a very accurate vertical adjustment that I bought extra with this machine. With it I can easily get 2 mills accuracy.
I move in another 2 mm, and did a 2 pass 3 mm cut for the separation between the saddle block and tie block. I made this all the way across the bridge as this left 4 mm, the thickness I wanted the wings.
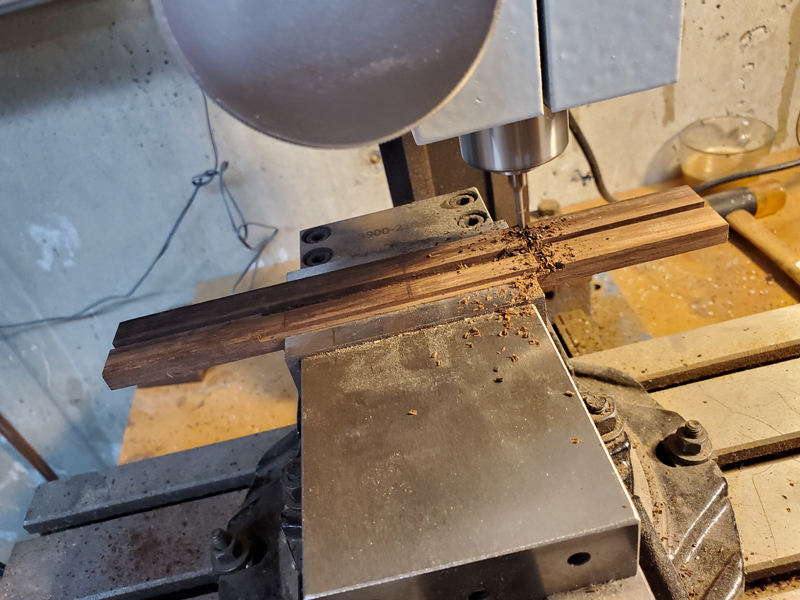
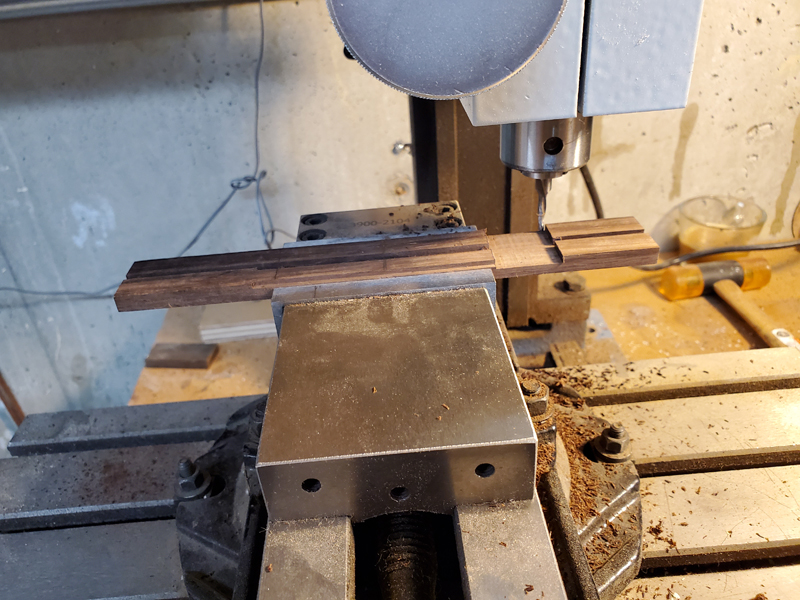
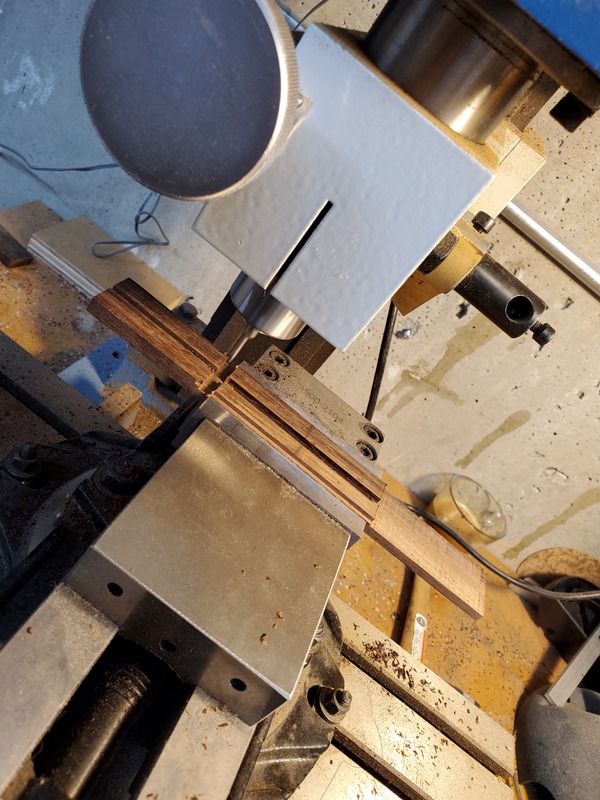
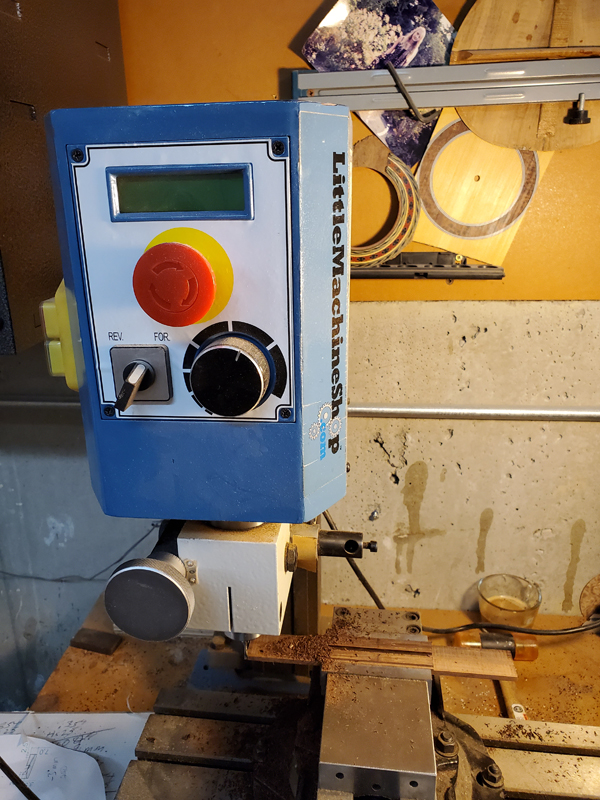
I used a file to round off the wings, also not shown chisels to angle back the saddle block on eanc side.
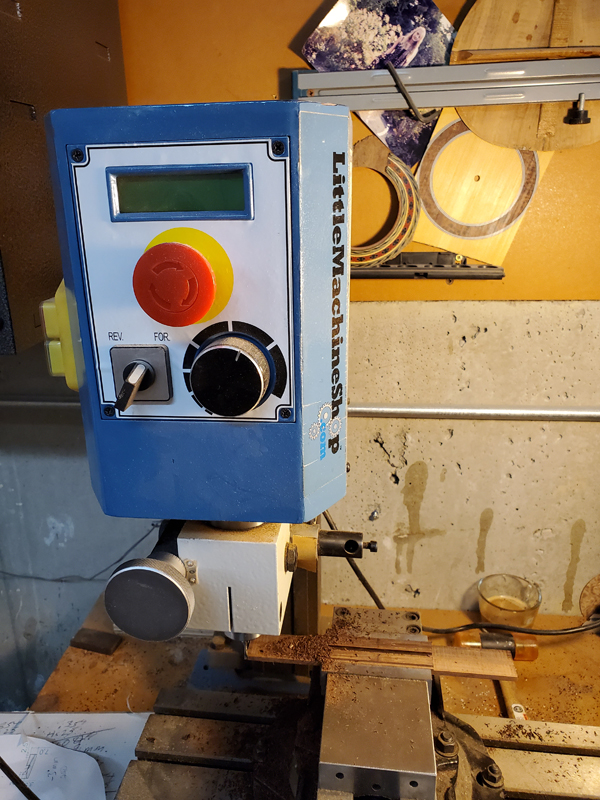
Scraper to put the 20 ' radius on the bridge
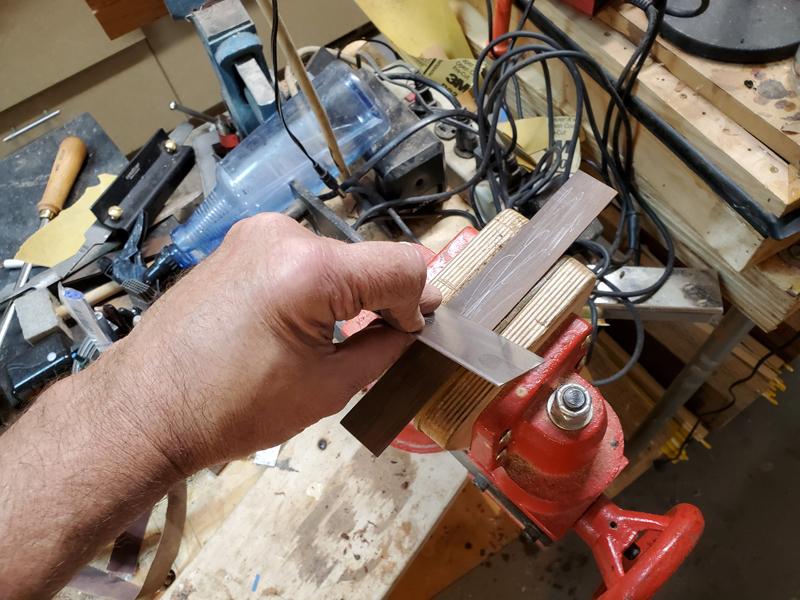
I used a chisel sharpening jig to put an even bevel on each side.
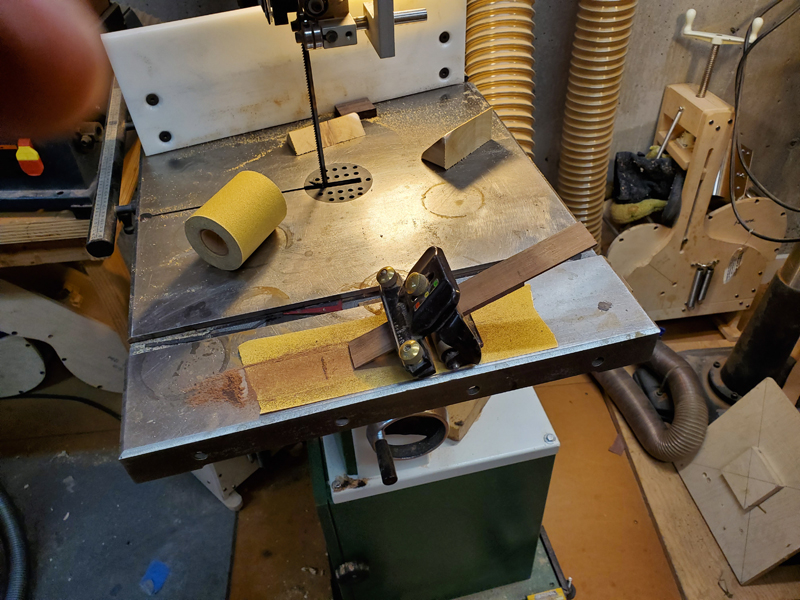
I drilled the holes on my pillar drill angling the bridge 3 degrees to make the string path work.
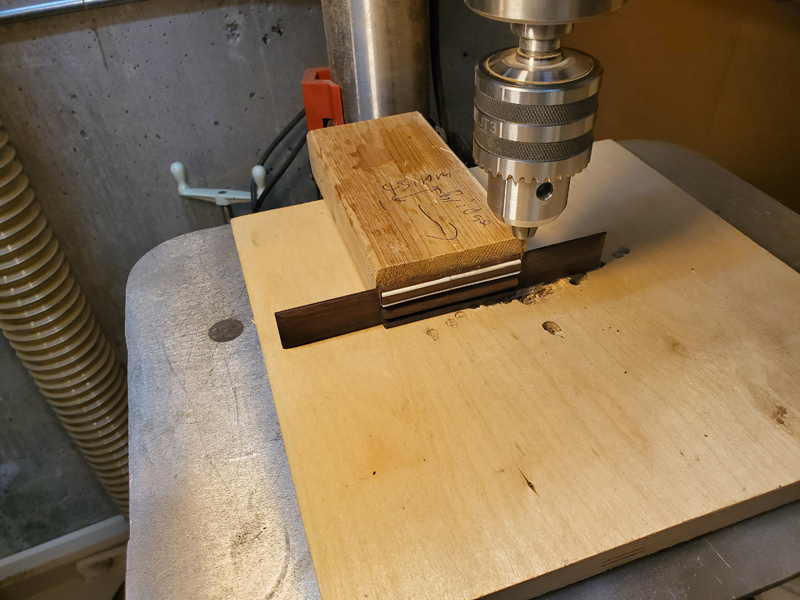
A little clean up with sand paper and scrapers and a 15 gram bridge.
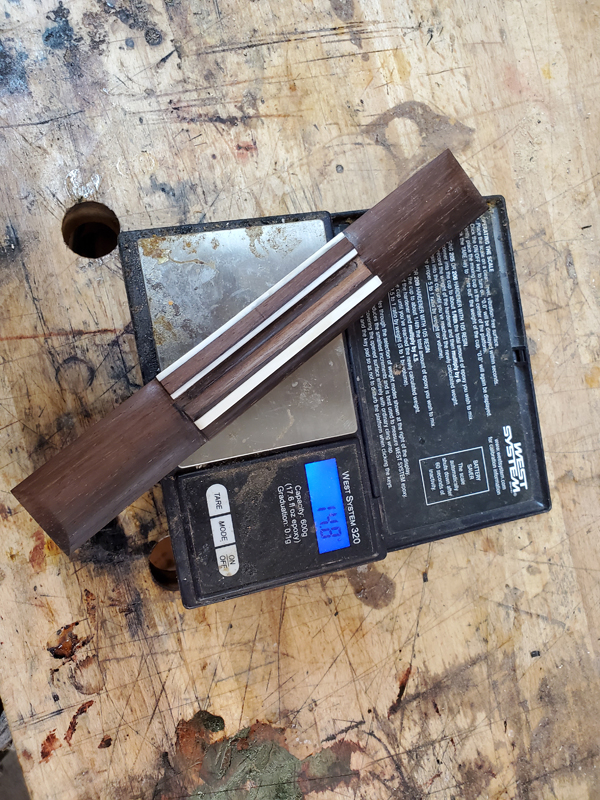
I used my center finder and a ruler to place the bridge and make a mask.
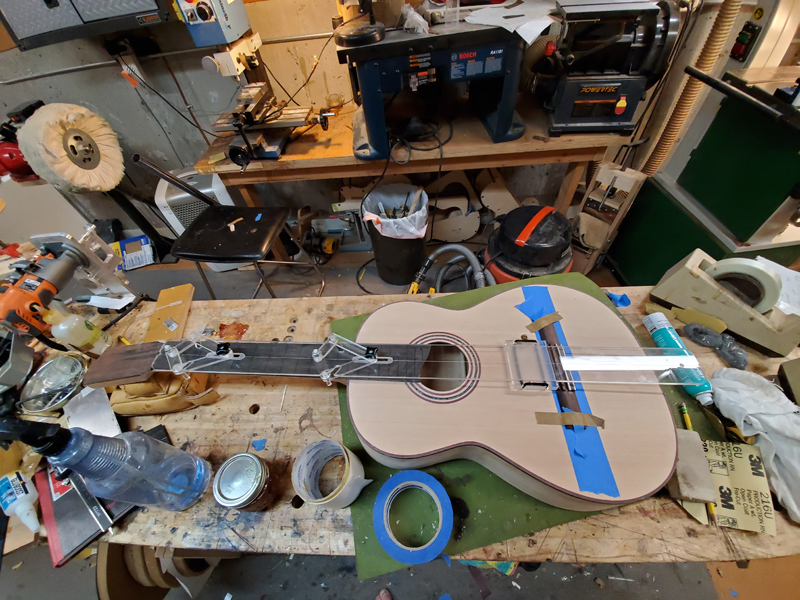
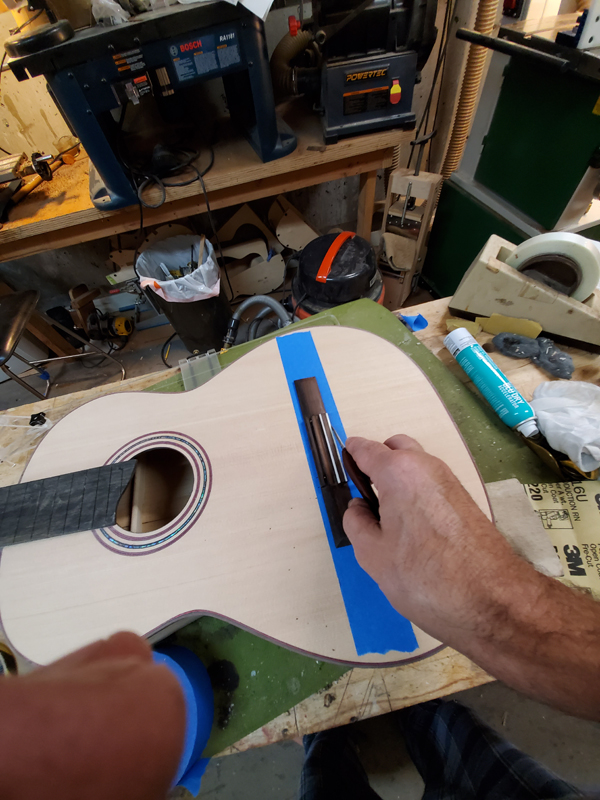
It looking OK. I am away for a few days but will come back and french polish the instrument next week.
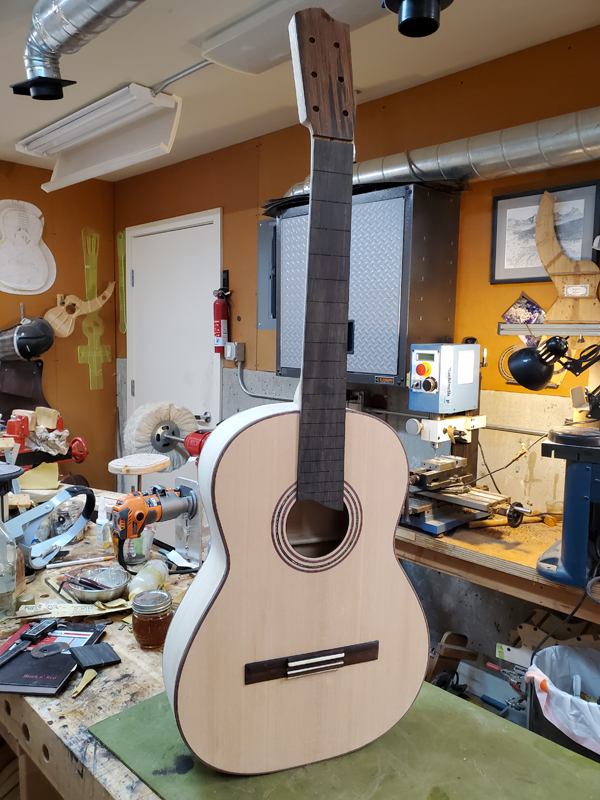
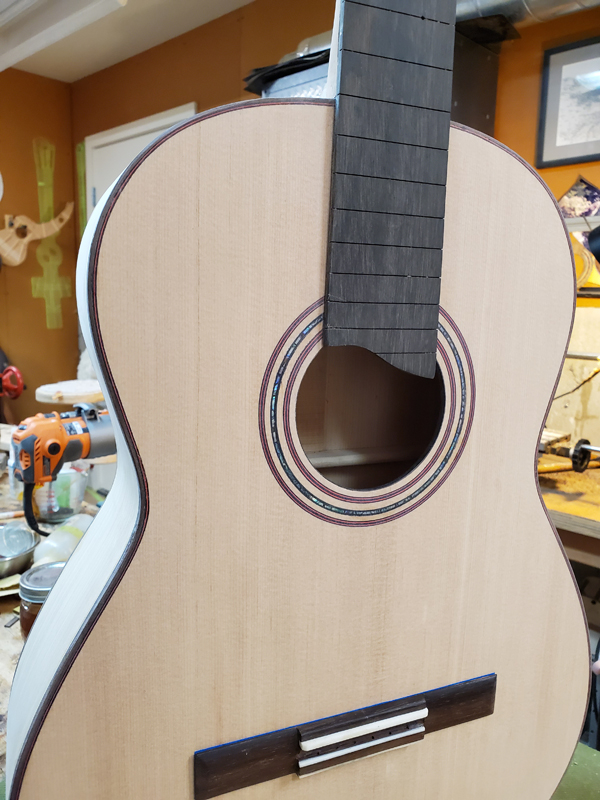
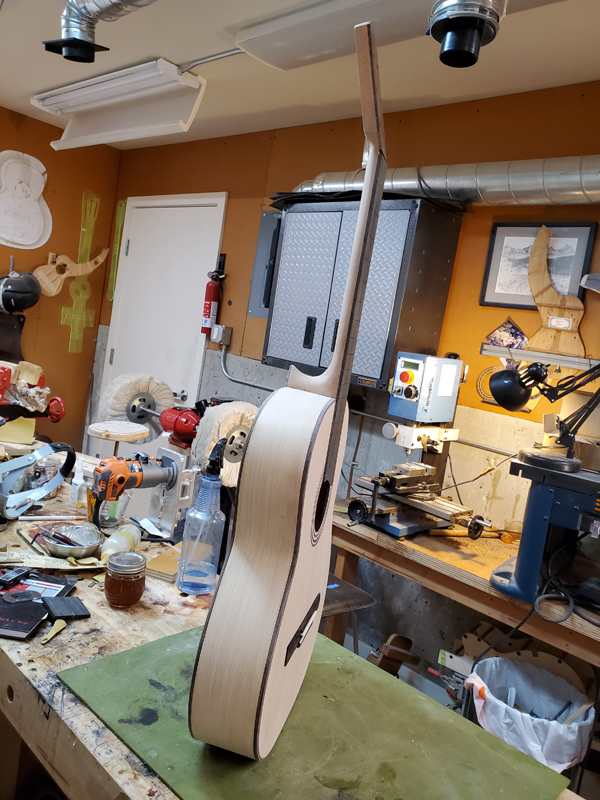
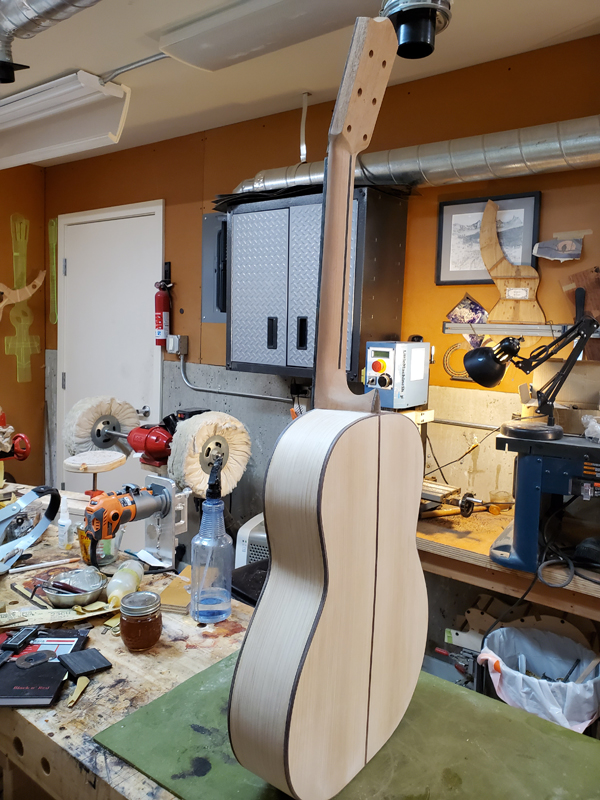
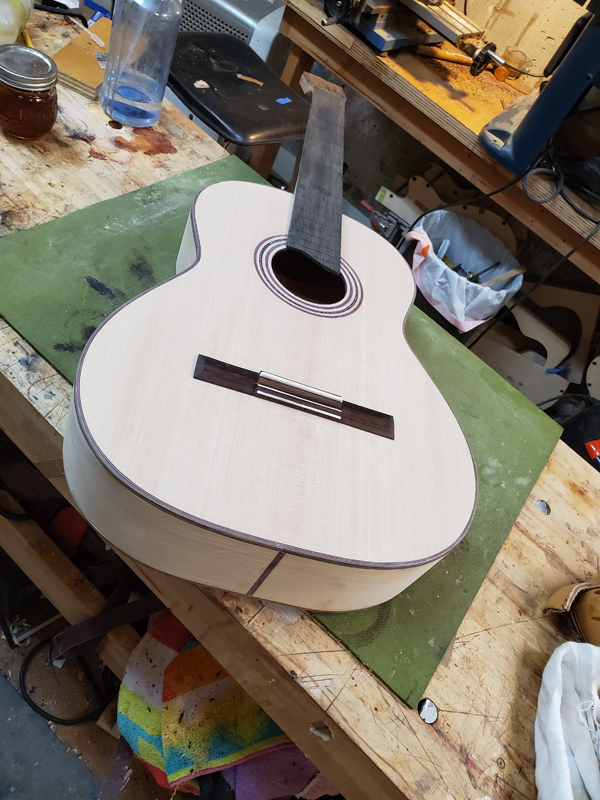