Amazingly it was not in "that" bad of shape. The major crack on the top is repairable. There was a small section of the x-brace that lifted cleanly over the crack. The tone bar has completely popped off. Just a thin shim of brace remains. With the large access port the repair to the top should not be difficult to do well.
I wanted to do a visible repair of the missing and cracked parts of the treble side. That is I wanted to mostly replace just the missing wood with new wood. My plan going in was to fit a 1 mm thick piece of bent mahogany (1 mm) backing the cracked but existing side extending to the endblock. Then inlay in piece of mahogany shaped to match the crack pattern. The patch would end up glued to the end bock, new kerfling and the backing patch.
I I did most of work with hot hide glue.
Here is where started:
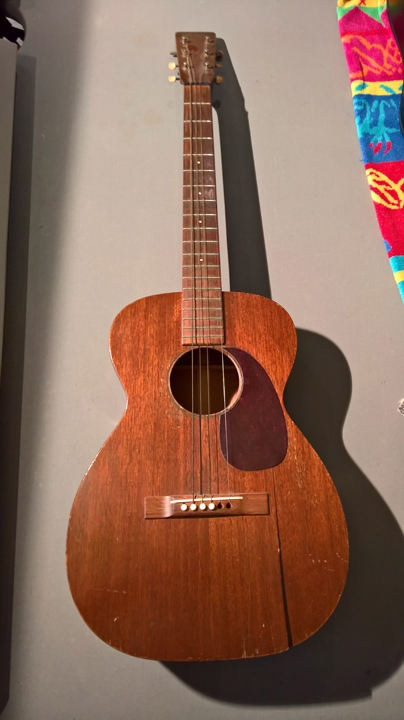
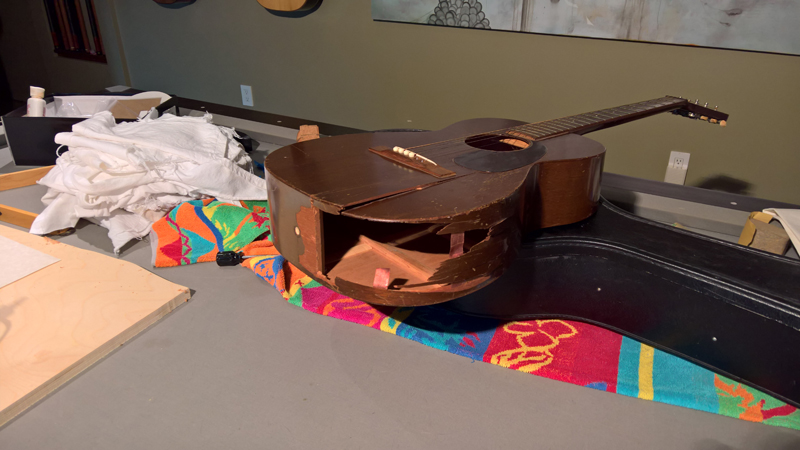
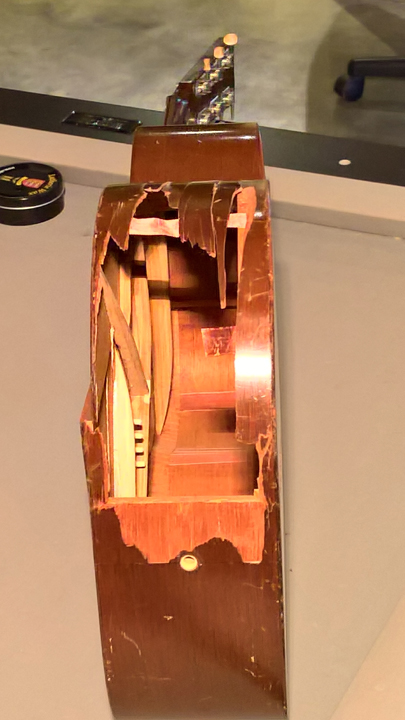
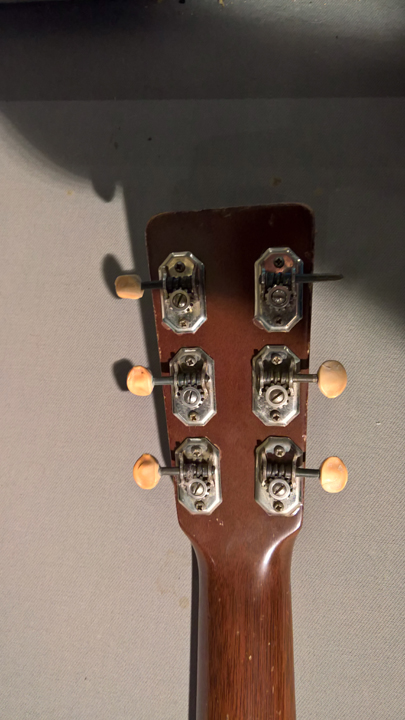
The inside was really clean
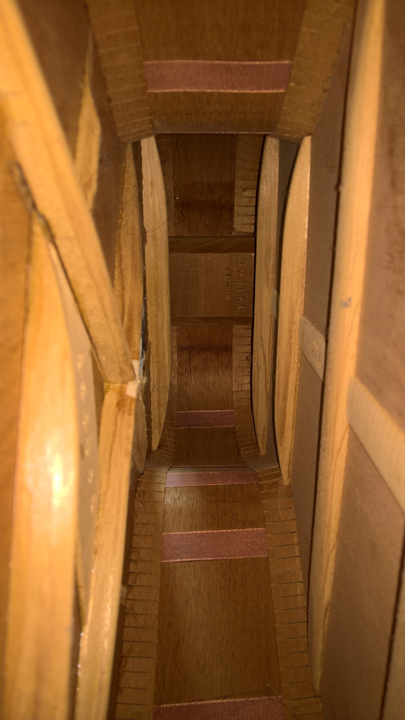
I closed the cracks on the top and back and installed cleats to keep them closed. With the unintentional access hole it was easy to close the cracks.
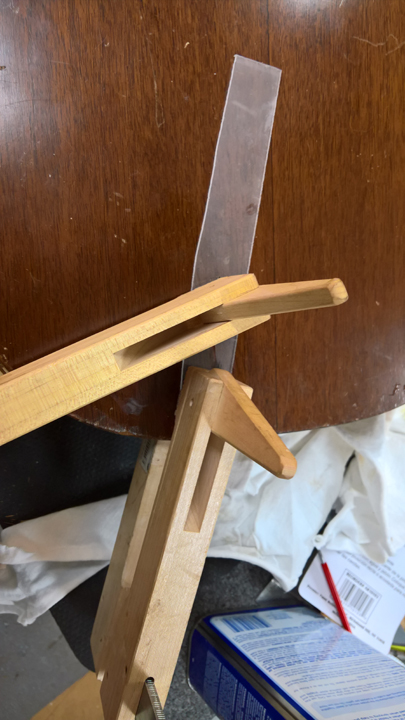
I thought of replacing the side as it would have been easier, but I really wanted to maintain the history of the guitar.
I made an insert that included a tongue to reinforced the intact but cracked area in the sides and kerfed linings to replace the missing linings and assure a good glue joint to the top and back. I was going to use a 1 mm cross grain strip, but could not find one long enough. Instead I thinned an orphaned side to 1 mm, bent it to shape, installed the kerfed linings then I fitted and glued it into the guitar. It is recessed in about 1.5-2.0 mm to allow me to inlay a mahogany veneer.
I had a couple of orphaned sides to work with. I pick these up in the sale bins on the various tonewood sites. Often they sell a batch of unlabeled sides cheap
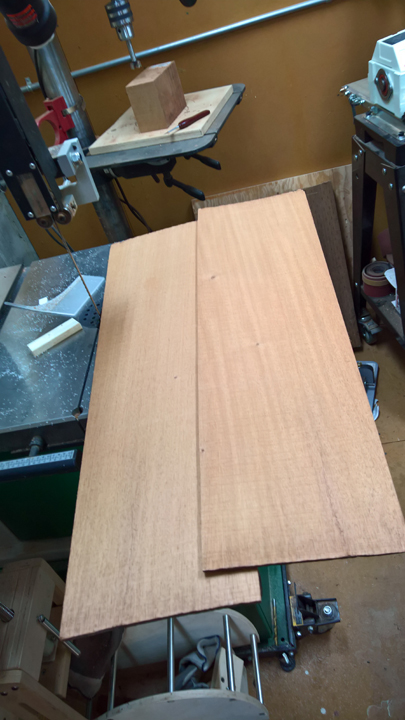
I made a cardboard template for the insert.
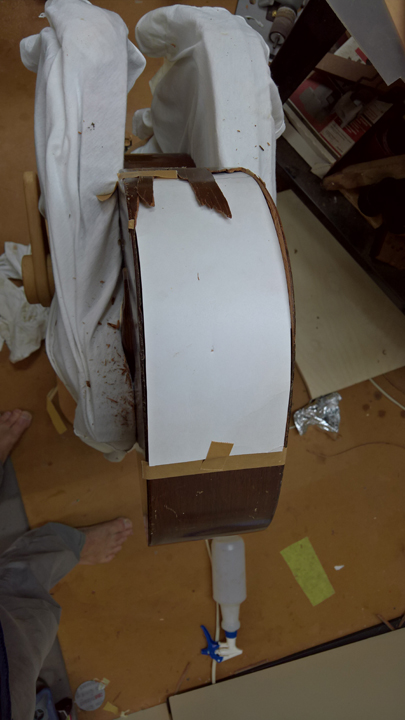
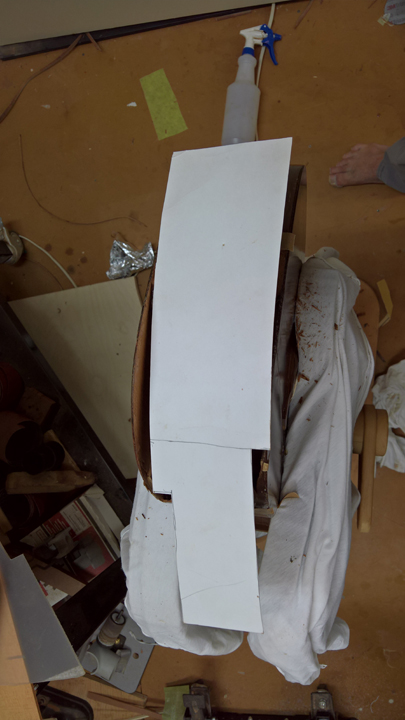
I bent the insert to the correct shape. It took a bit to get it to fit in the guitar. Once fitted I installed the linings and some reinforcement strips.
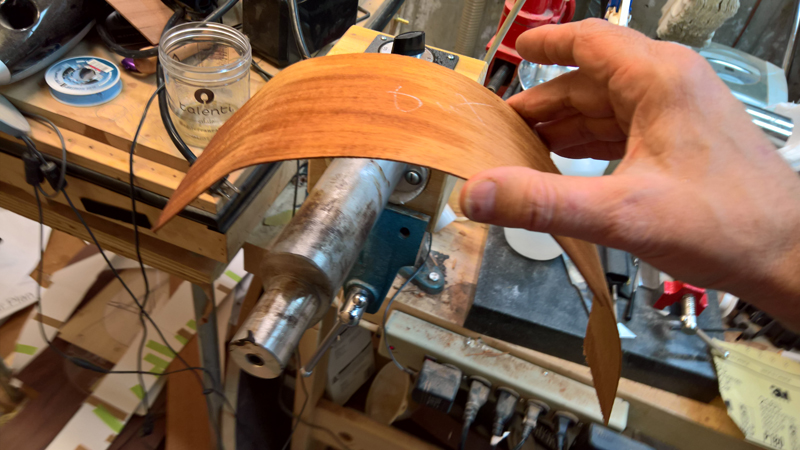
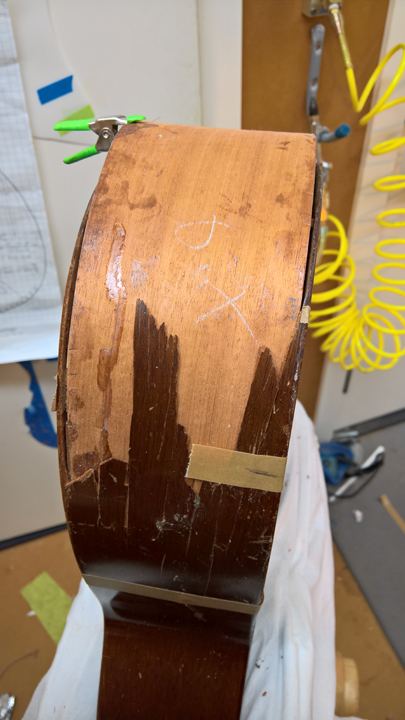
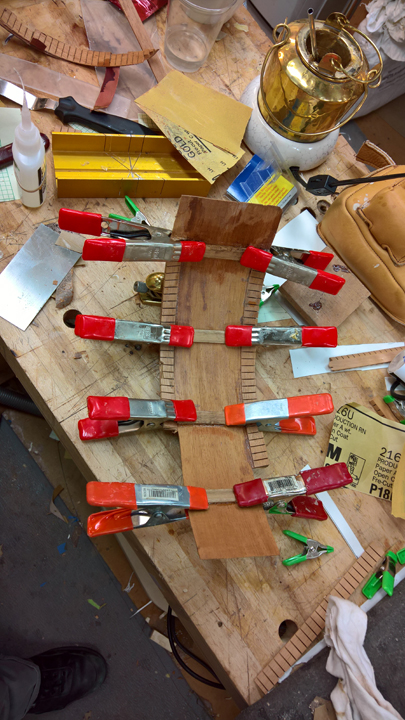
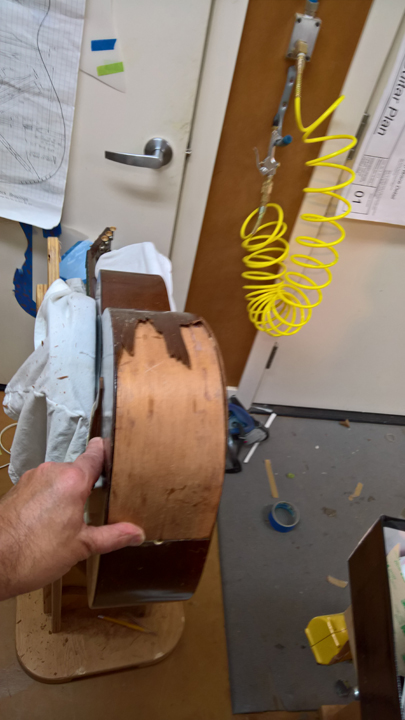
Instead of gluing all at once. I used hot hide glue to glue the tongue inside the cracked area. I made special shaped cauls attached to a spreader clamp to some what gently provide an internal backing. (sorry no pictures). I installed a few small cleats on the top and back to help me set the depth on the insert.
With all of the in place I was able to use hot hide glue to glue the insert onto place.
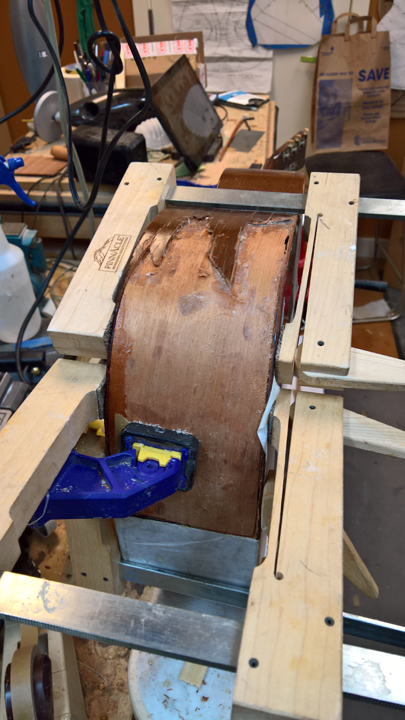
The small gap is where the back brace comes in. The kerfing was inset to the accommodate the brace.
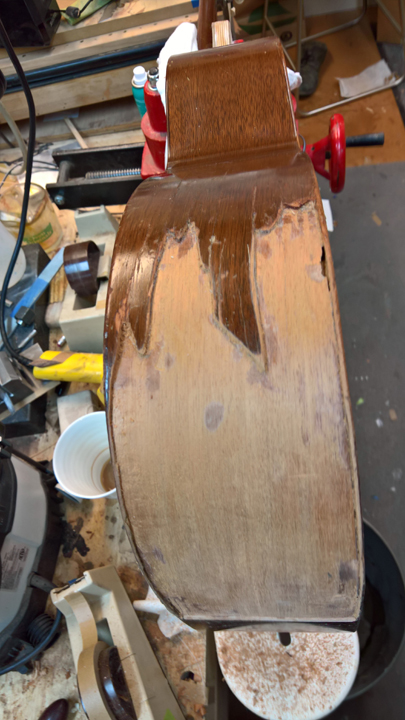
The next step was to make the veneer. I traced the shape onto some paper using a pencil to highlight the edge.
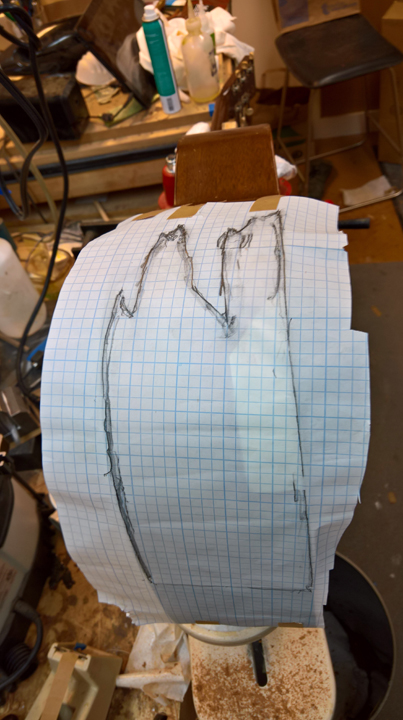
I cut out the pattern and spend a bit of time getting it to fit by fitting it to the guitar. When ready, I taped the pattern to the inside of the side patch and cut close with a band saw.
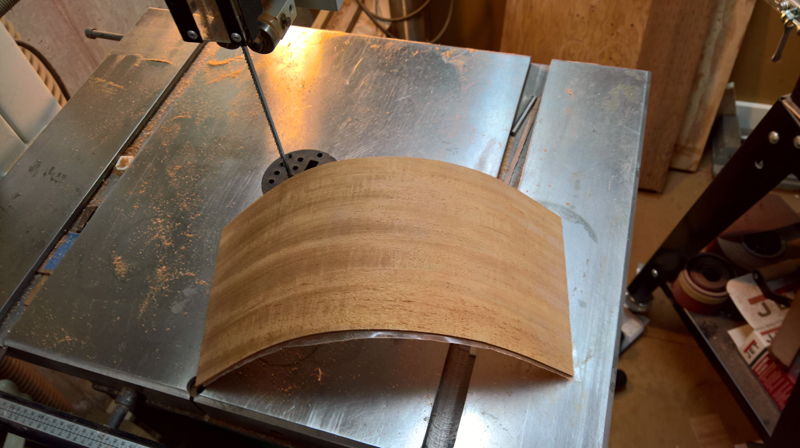
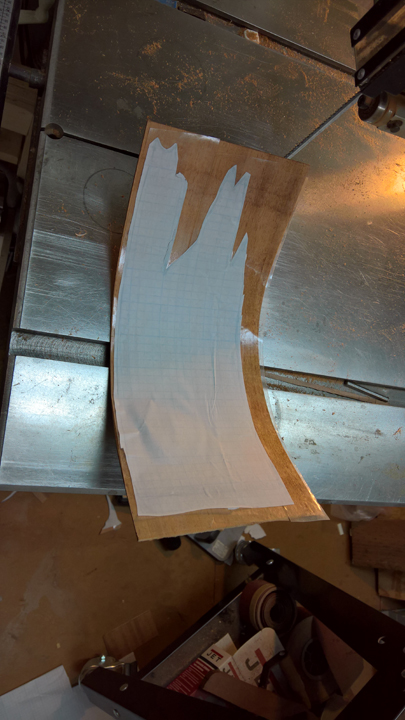
It did take a combination of a plane for the top and back edges, chalk, chisels, files and sanding sticks to fit the inlay
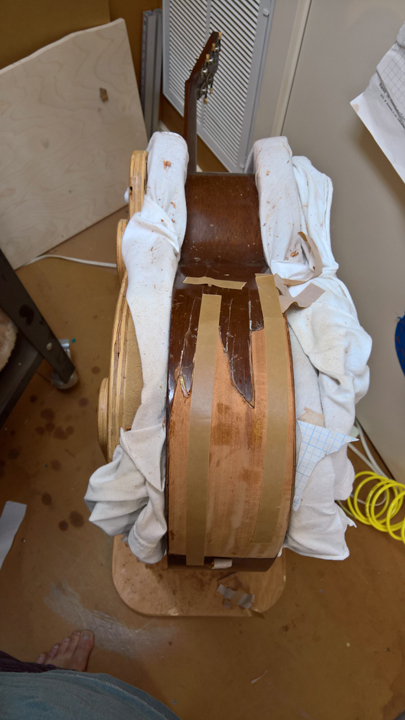
I spend a few moments to decide how to clamp it, after a trial run I decided on the belt clamp. I used fish glue to give me a bit more time to fuss around. Yes I do work bare foot and in my pajamas, retirement is great!
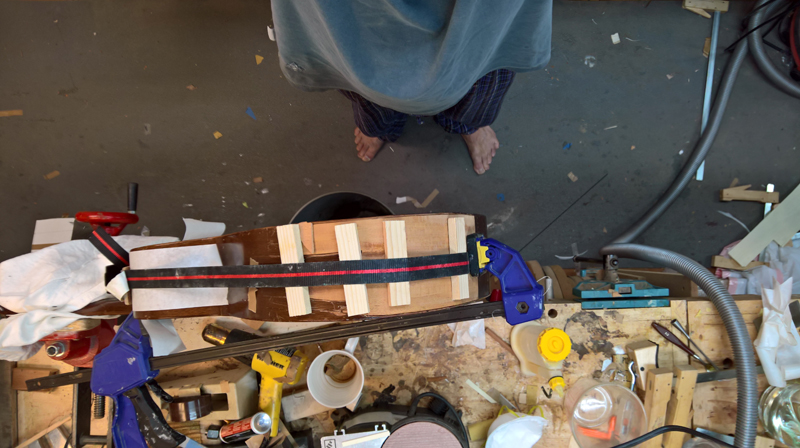
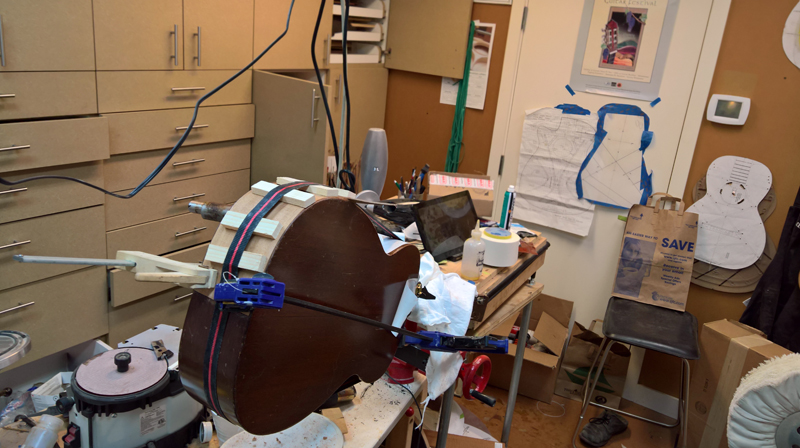
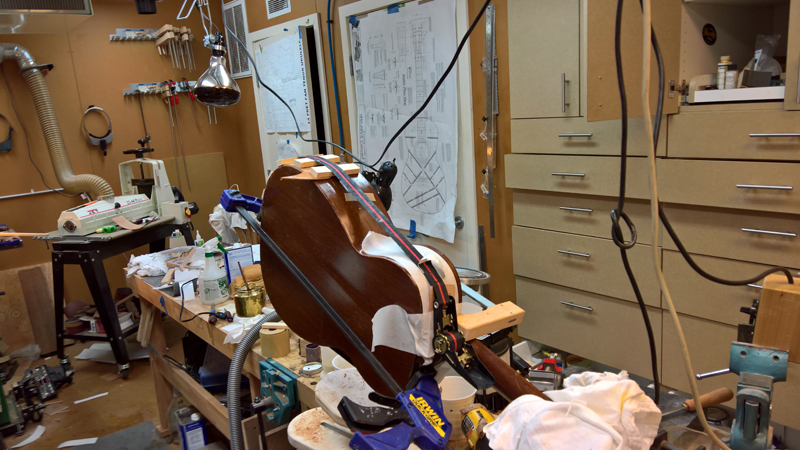
I was not really happy with my first color match. Maybe needed a little bit of yellow, or less red. This with done with Red Mahogany, tobacco brown and a touch of black.
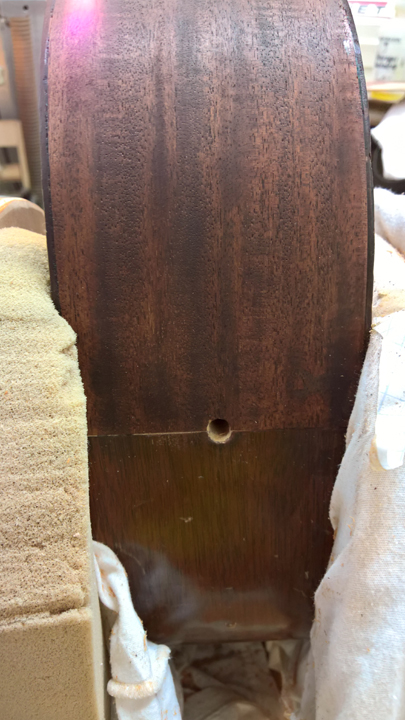
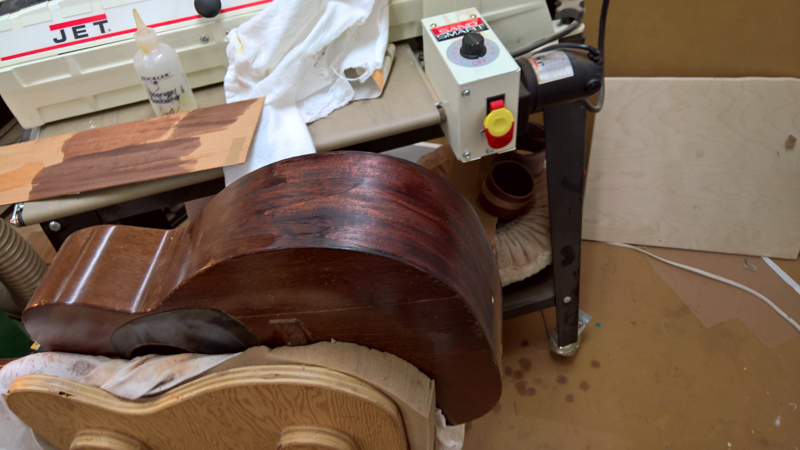
Here is what I had before the stain (just some naptha)
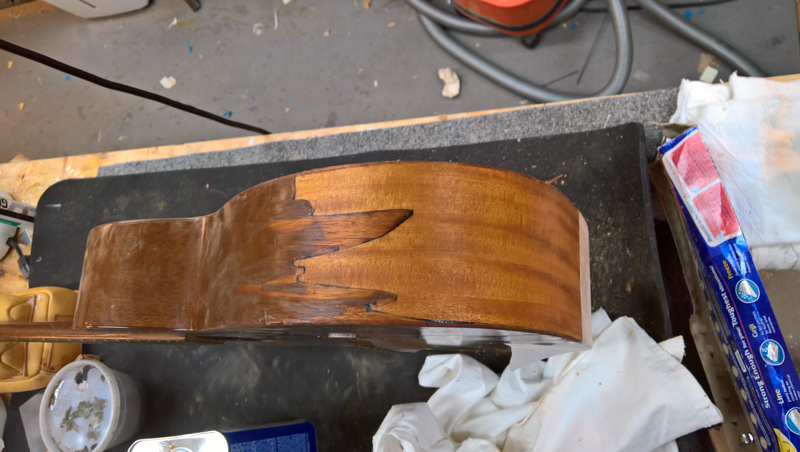
So I sanded off all of what I put on yesterday and sanded into the original a bit more. I remixed the dye with less red a and a bit more amber. It is not perfect, but looks ok unless looking right at it. The repair is very solid. The guitar has a clean drum like tap sound.
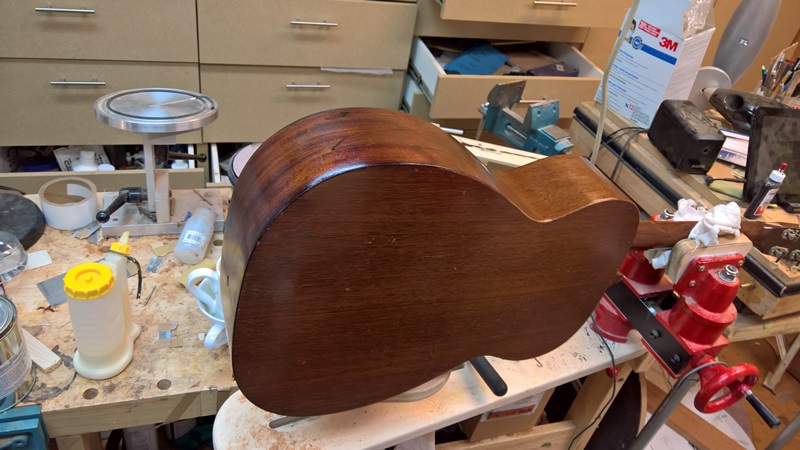
I really should have let the finish cure for another week or so, but I am not the most patient guy. Here is the 51 all strung up. It is a real instrument again.
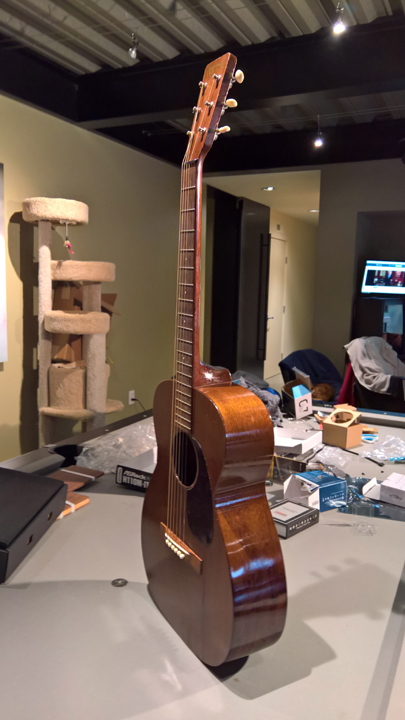
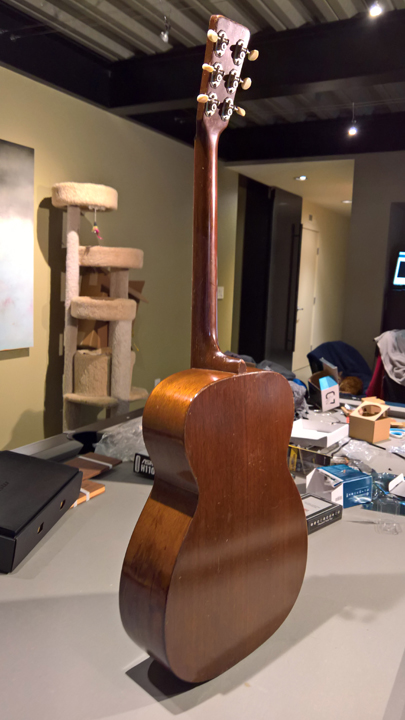
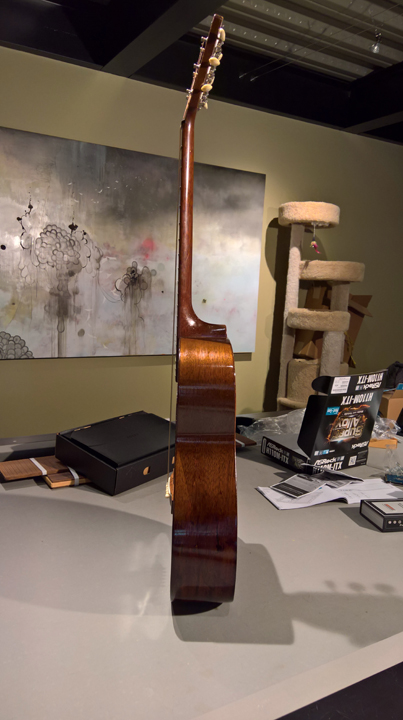

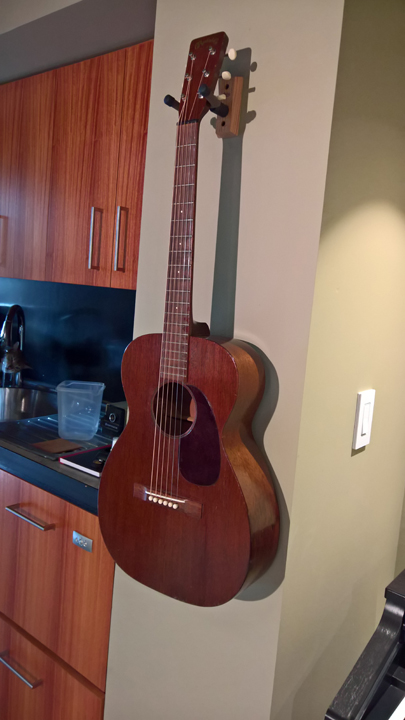