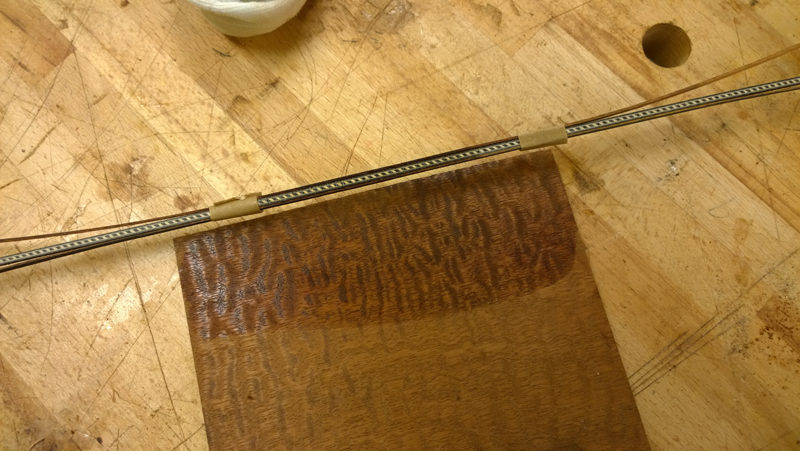
Instead of routing out the whole channel, I decided to make it on the sound board one section at a time. That way I can create tight channels for the rope binding and the EIR\B strips
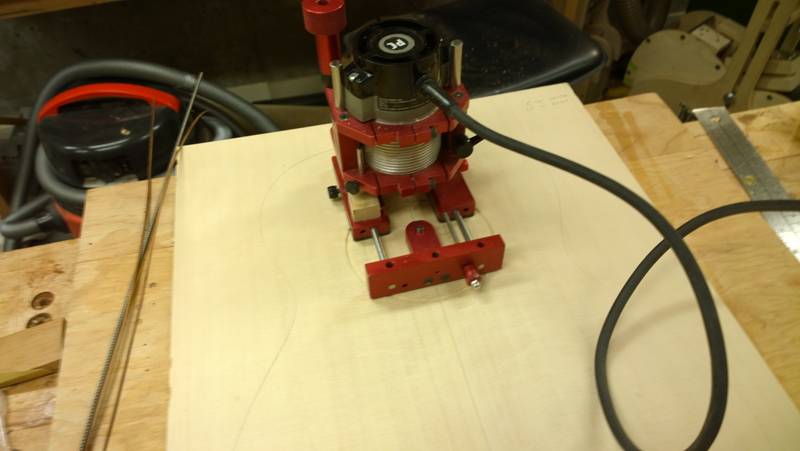
I tried to put in the stack without prebending. I was using a heat gun as I worked put I got so far and the roap binding started to come apart.
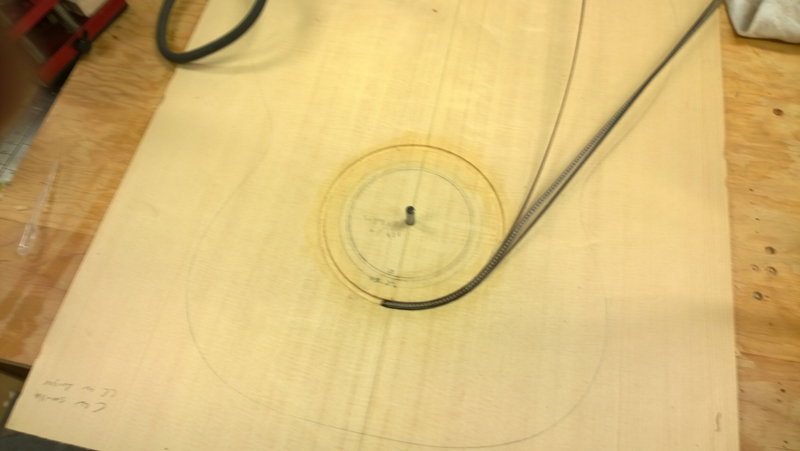
Ultimately I pulled out my bending pipe, bent everything close to the correct shape and found it easy to inlay the stack. I sealed the channel with shellac and I pushed the stack in place and flooded it with thin CA.
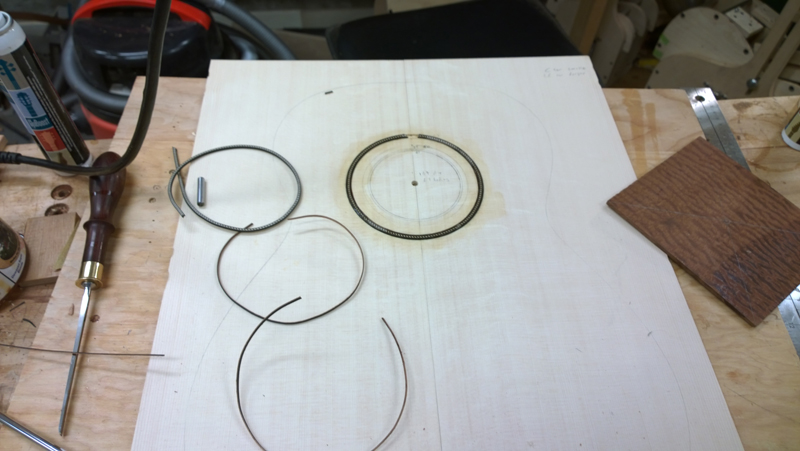
Before moving on to the next channel, the router base is set up perfectly to cut the outside of the wood rosette. I only take it to the depth that matches the thickness of the rosette I want. So without changing anything I cut to the outside line of the wood rosette. No measuring just negative space.
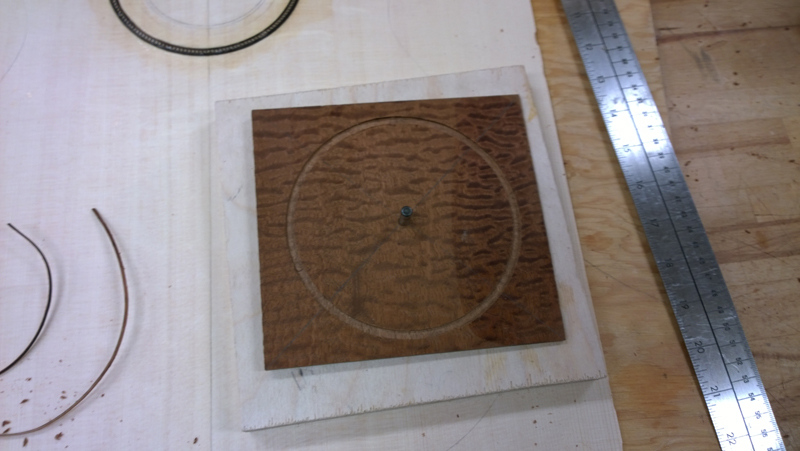
After first trying to cat the second ring I noticed that I needed to scraped the ring level so that the router will cut the next channel at the correct depth.
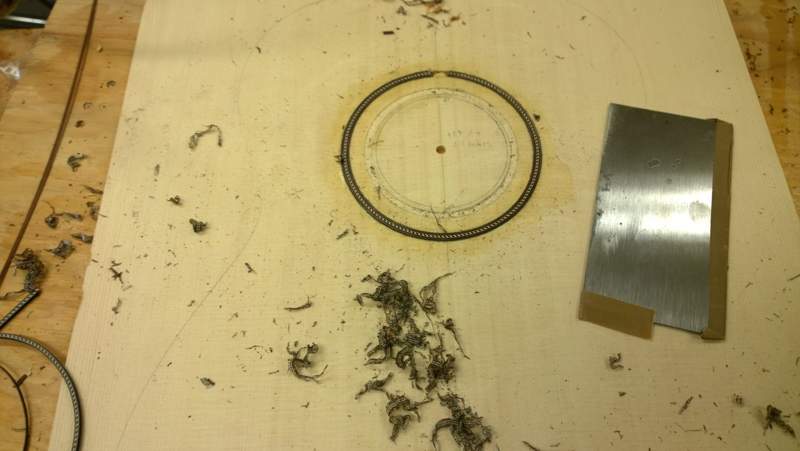
My stack is just a touch wider than my bit so I take a few passes and sneak up on the correct width. I make sure that any needed passes are going into the wood rosette area so that the router base is set to cut the inside of the wood rosette. Later when I run the back of the rosette blank though the drum sander a perfect sized ring should drop out.
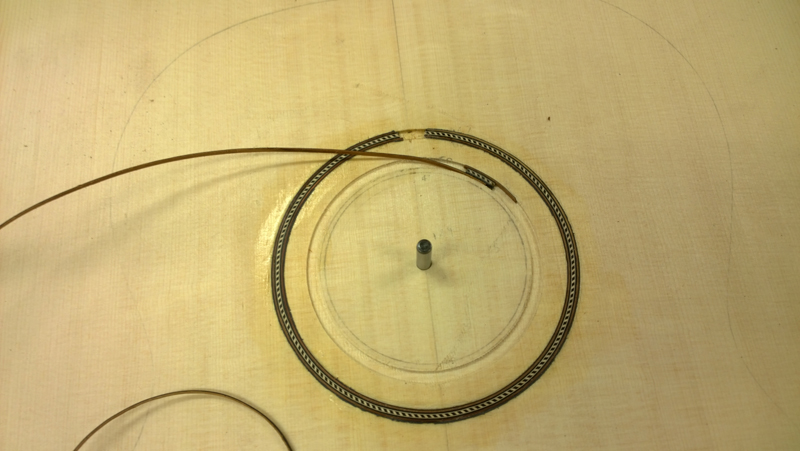
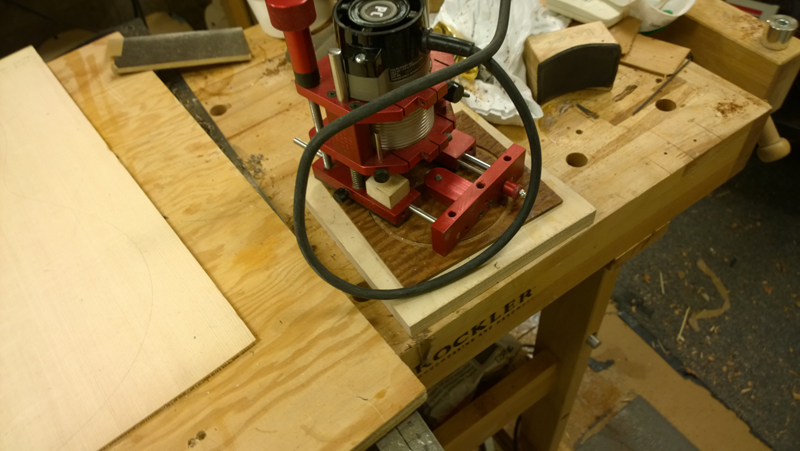
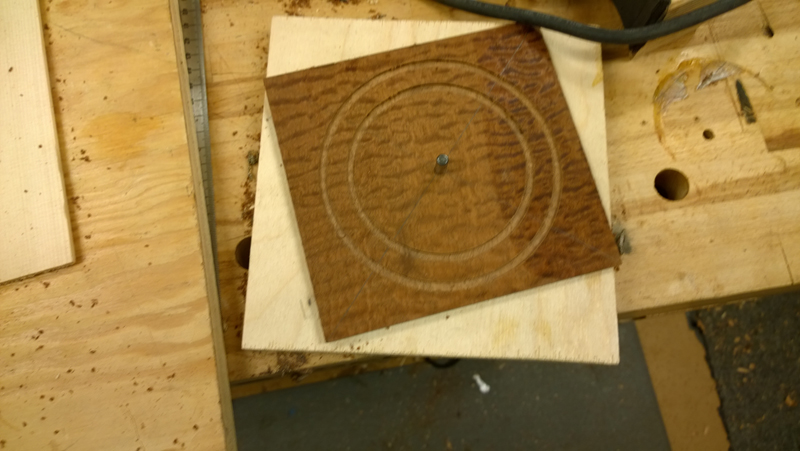
I pushed in the second purfling stack and ran the rosette blank through the drum sander until my ring dropped out.
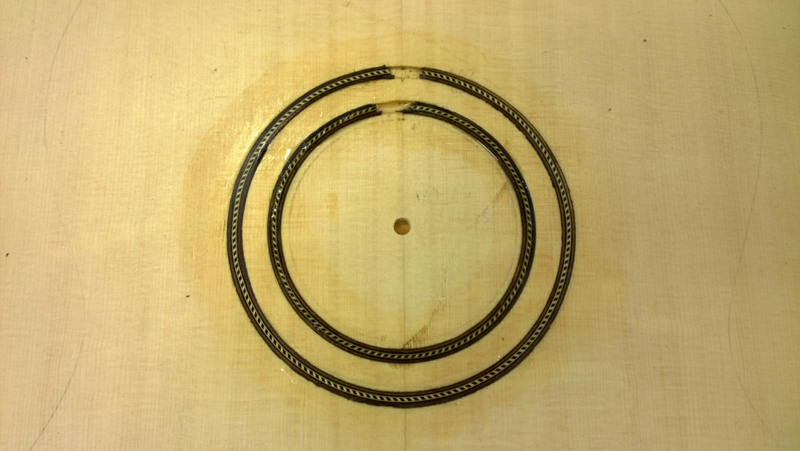
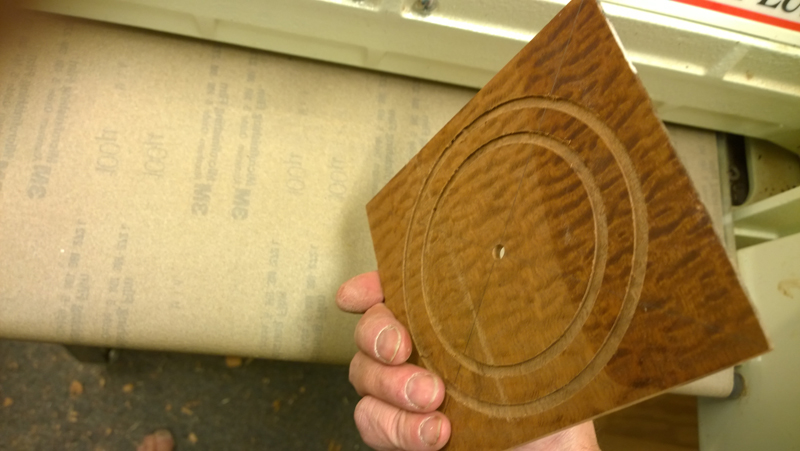
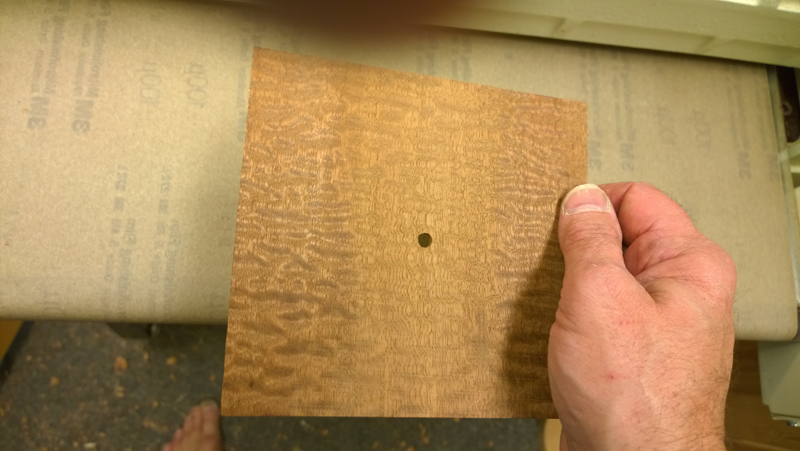
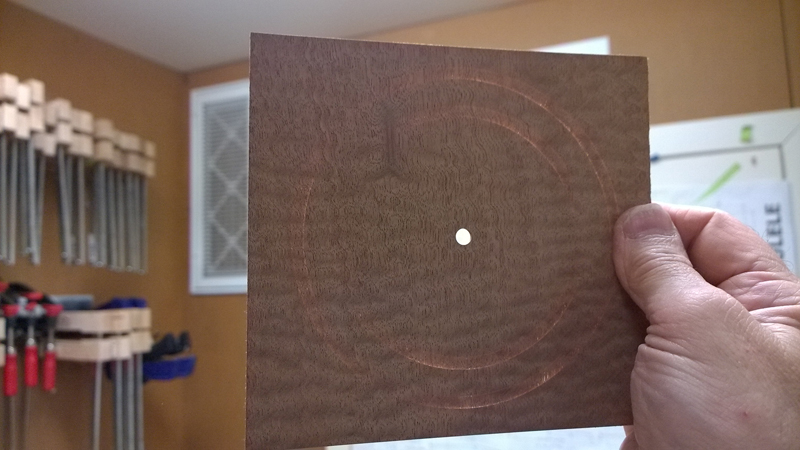
Looks like it will be a perfect fit
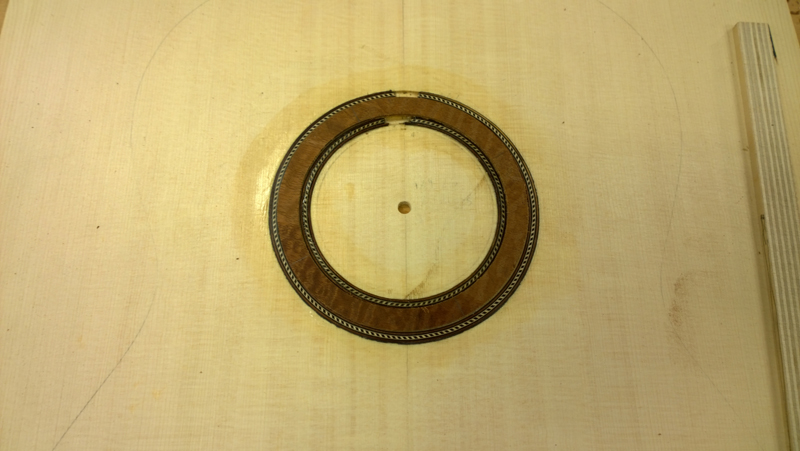
I routed the inside of the rosette channel sneaking up on the black fiber. This is where the Bishop Cochran base shines. I have gotten where I can move the bit in .01 mm increments.
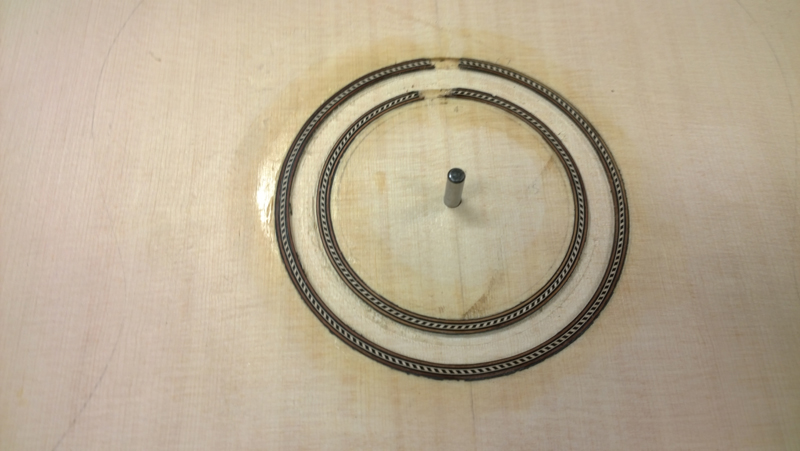
The ring snapped right in place. Not wanting to break it by pulling it out, and having previously sealed the inside of the channel with shellac, I flooded the rosette with thin CA.
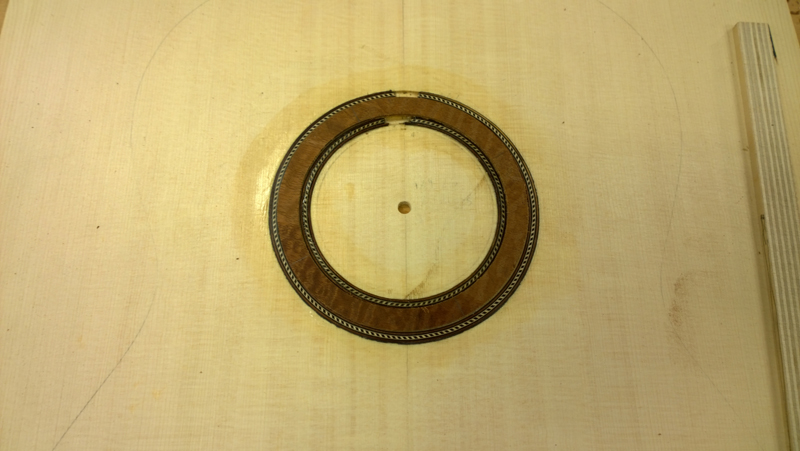
All cleaned up
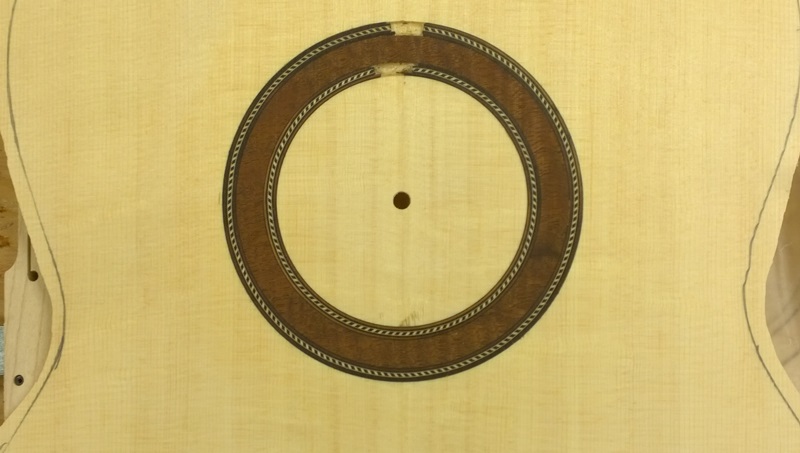