My plan right now besides the EIR and Sitka is to have curly maple bindings, herringbone prufling on the top, a zippered back strip. The Rosette will harken to Martin with a ring design the outside rings will be a bwbbwb pattern the inner ring will be a thin ring of walnut with black purflings inside and out. I have BRW for the fretboard, headstock veneer and the bridge.
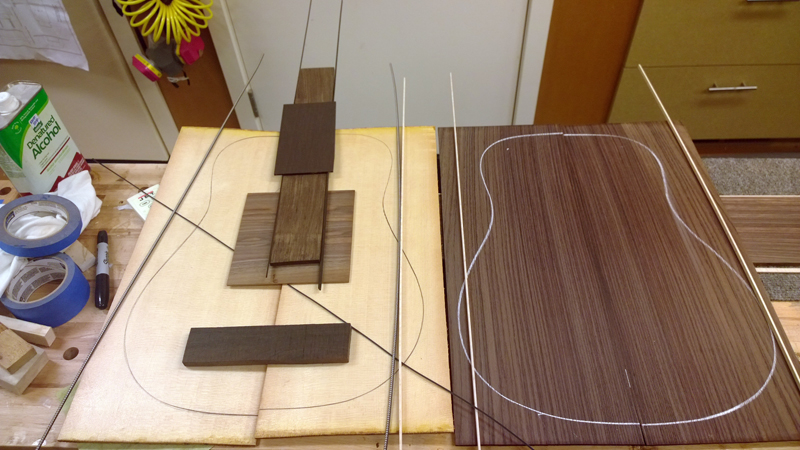
This is the third guitar that I will be documenting the wood's measured characteristics and building influenced on those measurements. John Link asked in a previous post so I will provide the information as I go along. I am hesitant to include this information as it mostly has meaning with in the context of Gore\Gilet Contemporary Acoustic Guitar Design book. The authors spent a bunch of time and effort describing the theory and methodology; I am not sure I can do the work justice. But here goes ...
My purpose for doing this is two fold:
1 - Documentation of the characteristics of the plates before I build
2 - A deterministic way to determine a target final thickness for the top and back. Basically a methodical and repeatable way to do tap tuning.
The method used is to combine a bunch of measurements of the wood and the guitar to be built with a user input of a target vibrational stiffness (really a target frequency). The book states that they found a set of values that they use for target vibrational stiffness by taking the information from a set of representative sounding guitars and back calculating a target frequency. This is important to note that they are not saying that there is a magical target frequency, rather they are saying that if you build to a consistent target frequency you will get more consistent results. A higher target will give a thicker plate and lower target will give a thinner plate. I started with their numbers. As I build more guitars and I want to change my sound I may deviate from where I started.
Before doing anything I used my thickness sander to take them to 4 mm. At this time both sets of plates had even thickness as I sanded past the saw cuts. The 4 mm is not important it was a thickness where I ended up with clean plates.
My first set of measurements were to record the height, width, thickness and weight of the top and back plates and to use that information first to calculate the woods density. ( just the weight divided by the product of the height, width and thickness.
With each of the plates I use a set of measurements to determine the long, cross and diagonal stiffness of the plates. I used a free product Visual Analyzer to sample and display a spectrum graph of the tap tones obtained by holding the plates at three different nodes and tapping on corresponding anti nodes of the plate. This gave 3 charts like the one I have below.
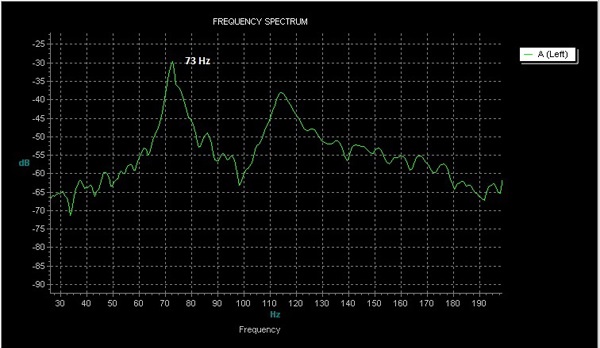
This graph is for the long grain vibrational mode of the top. The first peak 73Hz is a clear indication of the long grain frequency. One can also see the cross grain frequency with the peak around 113. I have another graph I used to determine the cross grain mode where I held and tapped in locations that suppressed the long grain vibrational mode.
I entered all of the above mentioned measurement and my target vibrational stiffness into a spread sheets that I made from the information in the book and ended up with a target thickness of 3 mm for the top and 2.7 for the back. You can see the two examples I have for the Sitka top and the EIR back.
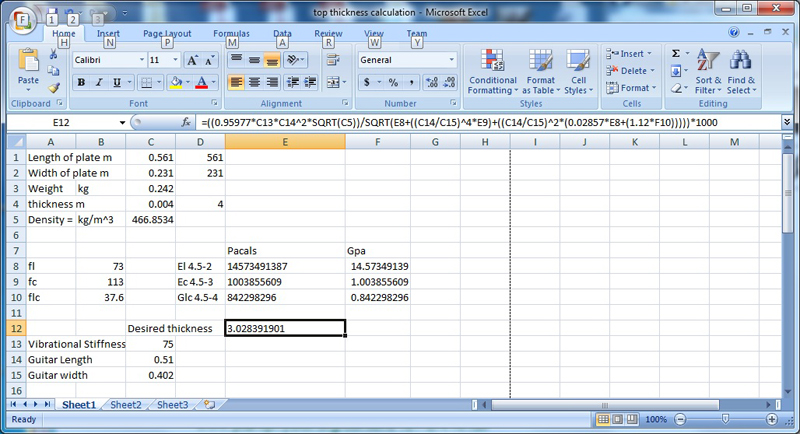
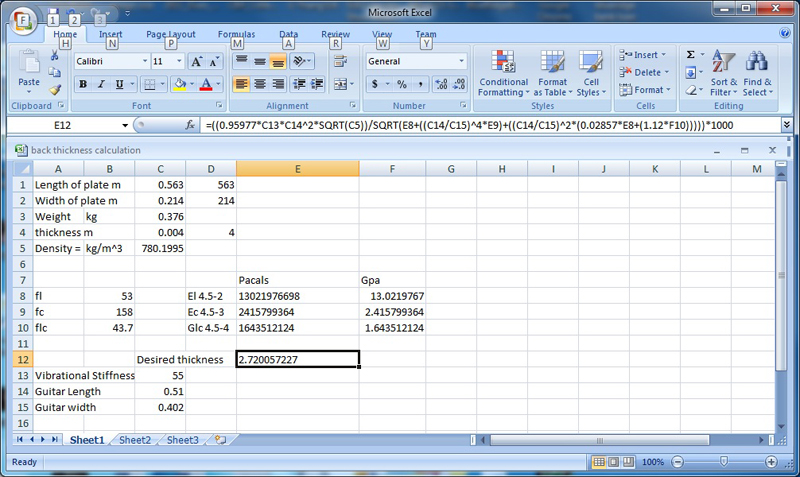